Formulate CNC Turning Process
3.1 Reasonable selection of machine tools
CNC machine tools are usually best suited for machining parts with the following characteristics:
(1) Parts for multi-variety, low-volume production, or trial production of new products.
(2) Parts with complex contours or high requirements on machining accuracy.
(3) Parts that require expensive process equipment (tools, fixtures, and dies) are used when machining with ordinary machine tools.
(4) Parts that need to be modified many times.
(5) the value of expensive, can not go wrong when machining key parts.
(6) Urgently needed parts with the shortest production cycle.
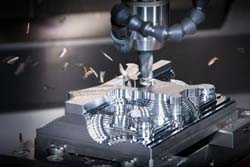
3.2 Process Analysis of CNC Machining Parts
(1) The size data on the parts drawing should be given in accordance with the principle of convenient programming
(2) The structural process of each part of the part should be in accordance with the characteristics of numerical control processing
3.3 Selection of processing methods and determination of processing plans
(1) Selection of processing methods
The principle of selection of processing methods is: At the same time, the requirements for processing accuracy and surface roughness are ensured. In addition, productivity and economic requirements should also be considered. and the actual situation of existing production equipment.
(2) The principle of determining the processing plan
Surface machining with high precision on parts is often achieved through roughing, semi-finishing and finishing. For these surfaces, the final machining plan is determined based on quality requirements, machine conditions, and billet conditions.
When determining the processing plan, first of all, according to the requirements of the accuracy and surface roughness of the main surface, the processing methods needed to achieve these requirements should be initially determined. At this point we must consider the rationality and economy of the use of CNC machine tools, and give full play to the functions of CNC machine tools. In principle, CNC machine tools only perform more complicated parts processing and important reference part finishing.
3.4 Division of processes and work steps
(a) Division of processes
(1) The process is divided by the clamping positioning of the parts, due to the different shapes of each part, the technical requirements of each surface are also different. Therefore, the positioning methods will be different in the processing. When the part is generally machined, the inner shape is positioned; when the inner structure of the part is processed, the outer shape is positioned. The process can be divided according to the different positioning methods.
(2) by the rough and fine machining step division
When the process is divided according to factors such as the machining accuracy, stiffness, and deformation of the part, the process can be divided according to the principle of rough and fine processing separation, that is, roughing is performed first, and then finishing is performed. Different machines or different tools can be used for machining. Usually in one installation, it is not allowed to machine the surface of a part of a part and then machine the other surface of the part.
In order to reduce the number of tool changes, shorten the idle travel time and reduce unnecessary positioning errors. According to the method of using the same tool and concentrating the machining process, the machining process of the parts can be divided. Whenever possible, use the same tool to machine all positions that can be machined, then replace the other tool and machine the rest of the part. This method is often used in special CNC machine tools and machining centers.
(b) The division of work steps
The division of work steps is mainly considered in terms of processing accuracy and production efficiency.In a process it is often necessary to use different cutting tools and cutting amounts to process different surfaces. In order to facilitate analysis and description of complex parts, it is subdivided into steps within the process.
The principle of division of work steps is:
(1) The same surface is finished by roughing, semi-finishing and finishing. Or all of the machined surfaces are roughed first and then finished separately.
(2) For a part that has both a milling plane and a boring surface, it can be machined by boring first after milling the plane. Because the method is divided into steps, the machining accuracy of the hole can be improved. Because of the large cutting forces when milling planes, parts are prone to deformation. After the first plane is milled and the hole is bored, it is possible to restore the deformation for a period of time and reduce the influence of the deformation on the accuracy of the hole.
(3) Press the tool to divide the step.
The rotation time of some machine tool tables is shorter than the time of tool change. It can be divided into steps according to the use of tools to reduce the number of tool changes and improve machining efficiency.
3.5 Parts Installation and Fixture Selection
(A) The basic principle of positioning and installation
(1) Strive to unify design criteria, process benchmarks, and programming calculation benchmarks.
(2) Minimize the number of clampings. After the positioning clamping is performed as much as possible, all the surfaces to be machined are machined.
(3) Avoid occupation of machines and manually adjust processing plans. In order to give full play to the effectiveness of CNC machine tools.
(B) Basic principles of selecting fixtures The characteristics of numerical control processing put forward two requirements for fixtures:
The first is to ensure that the coordinate direction of the fixture and the coordinate direction of the machine tool are relatively constant;
The second is to coordinate the dimensional relationship between the part and the machine coordinate system.
In addition, the following points should also be considered:
(B) Basic principles for selecting fixtures
The characteristics of CNC machining put forward two requirements for fixtures:
The first is to ensure that the coordinate direction of the fixture and the coordinate direction of the machine tool are relatively constant;
The second is to coordinate the dimensional relationship between the part and the machine coordinate system. In addition, the following points should also be considered:
(1) When the parts processing volume is not large, it should try to use combination fixtures, adjustable fixtures or other universal fixtures to shorten the production preparation time and save production costs.
(2) Consider using special fixtures only in batch production.
(3) The loading and unloading of parts should be quick, convenient and reliable to shorten the pause time of CNC machine tools.
(4) The components on the fixture should not interfere with the machining of the parts on the surface of the part. The clamps should be open, and their positioning of the components of the clamping mechanism must not affect the running of the tool during machining.
3.6 Tool Selection and Cutting Rate Determination
(a) the choice of tool
CNC machining tool materials require the use of new high-quality materials. The general principle is to use carbide as much as possible. For precision machining, ceramics, CBN and diamond tools with better performance and wear resistance can also be selected, and tool parameters should be optimized.
(II) Determination of cutting amount
The principle of reasonable choice of cutting amount is: When roughing, generally it is mainly to increase productivity, but the processing cost should also be considered. In the semi-finishing and finishing processes, the cutting efficiency, economy, and processing cost should be taken into consideration in the premise of guaranteeing the processing quality.
(1) Determine the cutting depth t (mm). In the case of machine tools, workpieces and tool rigidity, where permitted, The margin to be machined should be removed with the minimum number of feeds. It is best to remove the remaining allowance at one time to increase the production efficiency.
(2) Determine the cutting speed V (m/min). Increasing the cutting speed can also increase production efficiency. But the most effective measures to improve productivity or should as far as possible using a large cutting depth t.
(3) Determine the feed speed f (mm/min or mm/r)
The feed rate is an important parameter in the cutting amount of CNC machine tools.
Mainly based on the parts of the processing accuracy and surface roughness requirements and the material properties of the tool and parts to choose. When the machining accuracy and surface roughness requirements are high, the feed rate f should be chosen smaller. The maximum feed rate is determined by the stiffness of the machine tool and the performance of the feed system, and is related to the magnitude of the pulse equivalent of the numerical control system.
3.7 Determination of cutter points and tool change points
The principle of choosing a cutter point is:
(1) The selected cutter point is related to mathematical processing and simplified programming.
(2) The cutter point is easily calibrated on the machine.
(3) Easy inspection during processing.
(4) The processing error caused is small.
3.8 Determination of processing route
The principle of determining the processing route is:
(1) Ensure the machining accuracy and surface roughness of the parts.
(2) Convenient numerical calculations, reducing programming workload.
(3) Shorten the processing operation route and reduce the idle operation schedule.
When determining the processing route, we also need to consider the machining allowance of the parts and the stiffness of the machine tools and cutting tools. Need to determine if it is a single pass or multiple passes to complete the cutting process. And to determine in the CNC milling processing, is the use of reverse milling or milling and so on.
CNC machine tools are usually best suited for machining parts with the following characteristics:
(1) Parts for multi-variety, low-volume production, or trial production of new products.
(2) Parts with complex contours or high requirements on machining accuracy.
(3) Parts that require expensive process equipment (tools, fixtures, and dies) are used when machining with ordinary machine tools.
(4) Parts that need to be modified many times.
(5) the value of expensive, can not go wrong when machining key parts.
(6) Urgently needed parts with the shortest production cycle.
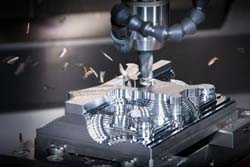
3.2 Process Analysis of CNC Machining Parts
(1) The size data on the parts drawing should be given in accordance with the principle of convenient programming
(2) The structural process of each part of the part should be in accordance with the characteristics of numerical control processing
3.3 Selection of processing methods and determination of processing plans
(1) Selection of processing methods
The principle of selection of processing methods is: At the same time, the requirements for processing accuracy and surface roughness are ensured. In addition, productivity and economic requirements should also be considered. and the actual situation of existing production equipment.
(2) The principle of determining the processing plan
Surface machining with high precision on parts is often achieved through roughing, semi-finishing and finishing. For these surfaces, the final machining plan is determined based on quality requirements, machine conditions, and billet conditions.
When determining the processing plan, first of all, according to the requirements of the accuracy and surface roughness of the main surface, the processing methods needed to achieve these requirements should be initially determined. At this point we must consider the rationality and economy of the use of CNC machine tools, and give full play to the functions of CNC machine tools. In principle, CNC machine tools only perform more complicated parts processing and important reference part finishing.
3.4 Division of processes and work steps
(a) Division of processes
(1) The process is divided by the clamping positioning of the parts, due to the different shapes of each part, the technical requirements of each surface are also different. Therefore, the positioning methods will be different in the processing. When the part is generally machined, the inner shape is positioned; when the inner structure of the part is processed, the outer shape is positioned. The process can be divided according to the different positioning methods.
(2) by the rough and fine machining step division
When the process is divided according to factors such as the machining accuracy, stiffness, and deformation of the part, the process can be divided according to the principle of rough and fine processing separation, that is, roughing is performed first, and then finishing is performed. Different machines or different tools can be used for machining. Usually in one installation, it is not allowed to machine the surface of a part of a part and then machine the other surface of the part.
In order to reduce the number of tool changes, shorten the idle travel time and reduce unnecessary positioning errors. According to the method of using the same tool and concentrating the machining process, the machining process of the parts can be divided. Whenever possible, use the same tool to machine all positions that can be machined, then replace the other tool and machine the rest of the part. This method is often used in special CNC machine tools and machining centers.
(b) The division of work steps
The division of work steps is mainly considered in terms of processing accuracy and production efficiency.In a process it is often necessary to use different cutting tools and cutting amounts to process different surfaces. In order to facilitate analysis and description of complex parts, it is subdivided into steps within the process.
The principle of division of work steps is:
(1) The same surface is finished by roughing, semi-finishing and finishing. Or all of the machined surfaces are roughed first and then finished separately.
(2) For a part that has both a milling plane and a boring surface, it can be machined by boring first after milling the plane. Because the method is divided into steps, the machining accuracy of the hole can be improved. Because of the large cutting forces when milling planes, parts are prone to deformation. After the first plane is milled and the hole is bored, it is possible to restore the deformation for a period of time and reduce the influence of the deformation on the accuracy of the hole.
(3) Press the tool to divide the step.
The rotation time of some machine tool tables is shorter than the time of tool change. It can be divided into steps according to the use of tools to reduce the number of tool changes and improve machining efficiency.
3.5 Parts Installation and Fixture Selection
(A) The basic principle of positioning and installation
(1) Strive to unify design criteria, process benchmarks, and programming calculation benchmarks.
(2) Minimize the number of clampings. After the positioning clamping is performed as much as possible, all the surfaces to be machined are machined.
(3) Avoid occupation of machines and manually adjust processing plans. In order to give full play to the effectiveness of CNC machine tools.
(B) Basic principles of selecting fixtures The characteristics of numerical control processing put forward two requirements for fixtures:
The first is to ensure that the coordinate direction of the fixture and the coordinate direction of the machine tool are relatively constant;
The second is to coordinate the dimensional relationship between the part and the machine coordinate system.
In addition, the following points should also be considered:
(B) Basic principles for selecting fixtures
The characteristics of CNC machining put forward two requirements for fixtures:
The first is to ensure that the coordinate direction of the fixture and the coordinate direction of the machine tool are relatively constant;
The second is to coordinate the dimensional relationship between the part and the machine coordinate system. In addition, the following points should also be considered:
(1) When the parts processing volume is not large, it should try to use combination fixtures, adjustable fixtures or other universal fixtures to shorten the production preparation time and save production costs.
(2) Consider using special fixtures only in batch production.
(3) The loading and unloading of parts should be quick, convenient and reliable to shorten the pause time of CNC machine tools.
(4) The components on the fixture should not interfere with the machining of the parts on the surface of the part. The clamps should be open, and their positioning of the components of the clamping mechanism must not affect the running of the tool during machining.
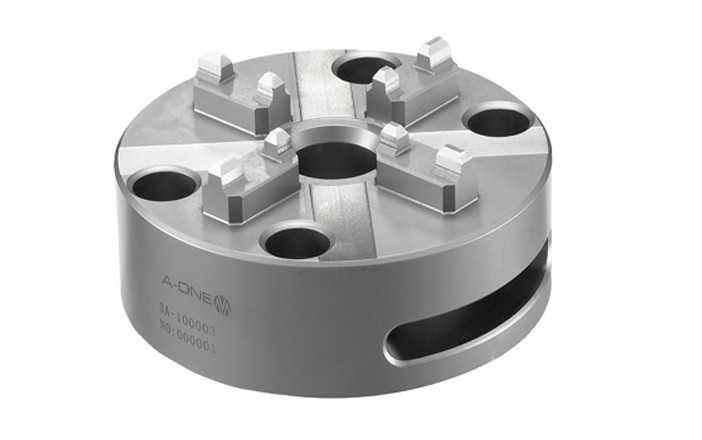
3.6 Tool Selection and Cutting Rate Determination
(a) the choice of tool
CNC machining tool materials require the use of new high-quality materials. The general principle is to use carbide as much as possible. For precision machining, ceramics, CBN and diamond tools with better performance and wear resistance can also be selected, and tool parameters should be optimized.
(II) Determination of cutting amount
The principle of reasonable choice of cutting amount is: When roughing, generally it is mainly to increase productivity, but the processing cost should also be considered. In the semi-finishing and finishing processes, the cutting efficiency, economy, and processing cost should be taken into consideration in the premise of guaranteeing the processing quality.
(1) Determine the cutting depth t (mm). In the case of machine tools, workpieces and tool rigidity, where permitted, The margin to be machined should be removed with the minimum number of feeds. It is best to remove the remaining allowance at one time to increase the production efficiency.
(2) Determine the cutting speed V (m/min). Increasing the cutting speed can also increase production efficiency. But the most effective measures to improve productivity or should as far as possible using a large cutting depth t.
(3) Determine the feed speed f (mm/min or mm/r)
The feed rate is an important parameter in the cutting amount of CNC machine tools.
Mainly based on the parts of the processing accuracy and surface roughness requirements and the material properties of the tool and parts to choose. When the machining accuracy and surface roughness requirements are high, the feed rate f should be chosen smaller. The maximum feed rate is determined by the stiffness of the machine tool and the performance of the feed system, and is related to the magnitude of the pulse equivalent of the numerical control system.
3.7 Determination of cutter points and tool change points
The principle of choosing a cutter point is:
(1) The selected cutter point is related to mathematical processing and simplified programming.
(2) The cutter point is easily calibrated on the machine.
(3) Easy inspection during processing.
(4) The processing error caused is small.
3.8 Determination of processing route
The principle of determining the processing route is:
(1) Ensure the machining accuracy and surface roughness of the parts.
(2) Convenient numerical calculations, reducing programming workload.
(3) Shorten the processing operation route and reduce the idle operation schedule.
When determining the processing route, we also need to consider the machining allowance of the parts and the stiffness of the machine tools and cutting tools. Need to determine if it is a single pass or multiple passes to complete the cutting process. And to determine in the CNC milling processing, is the use of reverse milling or milling and so on.
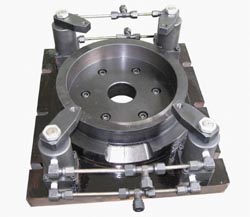