Stamping Die Material Types And Characteristics
Stamping Die manufacturing materials are steel, carbide, steel cemented carbide, zinc-based alloys, low melting point alloys, aluminum bronze, polymer materials and so on. At present, most of the materials used to make Stamping Die are steel-based. The types of commonly used mold working part materials include: carbon tool steel, low alloy tool steel, high carbon high chromium or medium chromium tool steel, medium carbon alloy steel, high speed steel, matrix steel, hard alloy, steel cemented carbide etc.
1. Carbon tool steel: The carbon tool steel used in the mold is T8A, T10A, etc. The advantages are good processing performance and low price. However, the hardenability and red hardness are poor, heat treatment deformation is large, and the bearing capacity is low.
2. Low-alloy tool steels: Low-alloy tool steels incorporate appropriate amounts of alloying elements on the basis of carbon tool steels. Compared with the carbon tool steel, the tendency of quenching deformation and cracking is reduced, the hardenability of the steel is improved, and the wear resistance is also better. Low-alloy steels used to make molds include CrWMn, 9Mn2V, 7CrSiMnMoV (code CH-1), and 6CrNiSiMnMoV (code GD).
3. High-carbon high-chromium tool steel: Commonly used high-carbon high-chromium tool steels are Cr12 and Cr12MoV, Cr12Mo1V1 (code D2), they have good hardenability, hardenability and wear resistance, heat treatment deformation is very small. High wear-resistant micro-deformation die steel, bearing capacity second only to high-speed steel. However, serious segregation of carbides must be carried out by repeatedly forging (axial boring, radial plunging). To reduce the inhomogeneity of carbides, improve the use of performance.
4. High carbon medium chromium tool steel: The high-carbon medium-chromium tool steels used in the molds include Cr4W2MoV, Cr6WV, Cr5MoV, etc., which have lower chromium content, less eutectic carbides, uniform carbide distribution, and small heat treatment distortion. Has good hardenability and dimensional stability. The performance is improved compared to high carbon high chromium steels where carbide segregation is relatively severe.
5. High speed steel: High-speed steel has the highest hardness, wear resistance and compressive strength in die steels, and has a high load carrying capacity. Commonly used in the mold is W18Cr4V (code 8-4-1) and W6Mo5 Cr4V2 containing less tungste
(Code 6-5-4-2, U.S. Grade M2) and 6W6Mo5 Cr4V (code 6W6 or low carbon M2), a carbon reduction vanadium high speed steel developed to improve toughness. High-speed steel also needs to be upgraded to improve its carbide distribution.
6. Base steel: Add a small amount of other elements to the basic ingredients of high-speed steel, and increase or decrease the carbon content to improve the performance of the steel. Such steels are collectively referred to as base steels. They not only have the characteristics of high-speed steel, have a certain degree of wear resistance and hardness, and fatigue strength and toughness are better than high-speed steel, high strength and toughness cold work die steel, material cost is lower than high-speed steel. The matrix steels commonly used in molds include 6Cr4W3Mo2VNb (code 65Nb), 7Cr7Mo2V2Si (code LD), and 5Cr4Mo3SiMnVAL (code 012AL).
7. Carbide and steel cemented carbide:
Hard alloys have higher hardness and wear resistance than any other type of die steel, but have poor bending strength and toughness. The cemented carbide used as a mold is a tungsten-cobalt type, and a mold with a low impact and a high wear resistance is required, and a hard alloy containing a relatively low amount of cobalt may be used. For high impact molds, carbides with high cobalt content can be used.
Steel cemented carbide is made by adding a small amount of alloying element powder (such as chromium, molybdenum, tungsten, vanadium, etc.) as binder to iron powder, and using titanium carbide or tungsten carbide as hard phase, which is sintered by powder metallurgy. The steel cemented carbide substrate is steel, which overcomes the disadvantages of poor toughness and processing difficulties of the cemented carbide, and can be cut, welded, forged and heat-treated. Steel-bonded carbides contain a large amount of carbides. Although the hardness and wear resistance are lower than those of cemented carbides, they are still higher than those of other steels. After quenching and tempering, the hardness can reach 68 to 73HRC.
Blanking die material selection and heat treatment requirements
Selection of punching die materials should consider the workpiece production batch, if the batch is not large, there is no need to choose a high-life die material; Should be considered to be punched workpiece material, different materials of suitable mold materials are also different. For the punching die, wear resistance is an important factor in determining die life. The wear resistance of steel depends on the condition of carbides and hard spots and the hardness of the substrate. The higher the hardness of the two, the greater the number of carbides, the better the wear resistance. Commonly used Stamping Die steel wear resistance, excellent performance, followed by: Carbon tool steel - alloy tool steel - matrix steel - high carbon high chromium steel - high speed steel - steel cemented carbide - carbide.
In addition, the influence of the thickness, shape, size, and precision requirements of the workpiece on the choice of mold materials must also be considered.
1. Traditional mold steel: For a long time, the steel used in domestic thin blanking die has been T10A, CrWMn, 9Mn2V, Cr12 and Cr12MoV.
Among them, T10A is a carbon tool steel with certain strength and toughness. However, the wear resistance is not high, the quenching is easy to be deformed and cracked, and the hardenability is poor, and it is only applicable to a blanking die with a simple workpiece shape, a small size, and a small number.
T10A carbon tool steel heat treatment process is: 760 ~ 810 °C water or oil quenching, 160 ~ 180 °C tempering, hardness 59 ~ 62HRC.
CrWMn and 9Mn2V are high carbon low alloy steels: Quenching operation is simple, hardenability is better than carbon tool steel, deformation is easy to control. However, the wear resistance and toughness are still low, and they are used in blanking molds with medium-sized batches and complicated workpiece shapes.
CrWMn steel heat treatment process: quenching temperature 820 ~ 840 °C oil cooling, tempering temperature 200 °C, hardness 60 ~ 62HRC.
9Mn2V steel heat treatment process: quenching temperature 780 ~ 820 °C oil cooling, tempering temperature 150 ~ 200 °C, air cooling, hardness 60 ~ 62HRC.
Note tempering brittleness and significant volume expansion in the tempering temperature range of 200-300 °C should be avoided.
Cr12 and Cr12MoV: high carbon high chromium steel, high wear resistance, small deformation during quenching, good hardenability, can be used for mass production of molds, such as silicon steel blanking die. However, carbides of this type have non-uniformity of carbides and are liable to cause segregation of carbides, and are easily chipped or fractured during blanking. Among them, Cr12 has a high carbon content, and the distribution of carbides is more severe than that of Cr12MoV, and the brittleness is greater.
The choice of heat treatment process for Cr12 steel depends on the requirements of the mold. When the mold requires relatively small deformation and certain toughness, it can be quenched and tempered at low temperature (Cr12 is 950~980 °C quenching, 150~200 °C tempering; Cr12MoV is quenched at 1020-1050 °C and tempered at 180-200 °C ). To improve the use of the mold temperature, improve its hardenability and red hardness, high temperature quenching, tempering (Cr12 is 1000 ~ 1100 °C quenching, 480 ~ 500 °C tempering; Cr12MoV is quenched at 1110~1140 °C and tempered at 500~520 °C ). High-chromium steels have temper brittleness in the 275-375 °C zone and should be avoided.
2. New mold steel
In order to compensate for the lack of traditional mold steel performance, domestic development or introduction of better performance Stamping Die steel of the following:
(1) Cr12Mo1V1 (Code D2) steel is a type of steel imported from D2 steel in the United States ASTM standard and belongs to Cr12 steel. As the content of Mo and V in D2 steel increases, the grain is refined, and the distribution of carbides is improved. Therefore, the toughness (impact toughness, bending strength, and deflection) of D2 steel is higher than that of Cr12MoV steel. Sex and anti-tempering stability are also higher than Cr12MoV. Cryogenic treatment can be used to increase hardness and improve dimensional stability. The life of the punching die made of D2 steel is higher than that of the Cr12MoV steel die. The forgeability and thermoformability of D2 steel are slightly worse than that of Cr12MoV steel, and the machining performance and heat treatment process are similar to those of Cr12 steel.
(2) Cr6WV steel is a highly wear resistant micro-deformed high-carbon medium-chromium steel with lower content of carbon and chromium than Cr12 steel. The distribution of carbides is evener than that of Cr12MoV and has good hardenability. Heat treatment deformation is small, better machining performance. The flexural strength and impact toughness are better than Cr12MoV, but the wear resistance is slightly lower than Cr12 steel. The high hardness, high wear-resistance blanking die used to withstand large impacts is better than Cr12 steel.
The commonly used heat treatment process of steel is: the quenching temperature is 9701 ~ 000 °C, generally it can be cooled and quenched by hot oil or nitrate salts, and the parts with small size can adopt air cooling. After quenching, it should be tempered immediately. The tempering temperature is 160210 ~ °C and the hardness is 58 ~ 62HRC.
(3) Cr4W2MoV steel is also a high wear-resistant micro-deformation high-carbon medium-chromium steel. It is developed as a substitute for Cr12 steel. It has good carbide uniformity and wear resistance higher than Cr12MoV. It is suitable for producing complex shapes and high dimensional accuracy. Stamping Die, can be used for silicon steel die.
The heat treatment process of Cr4W2MoV steel: When high strength and toughness are required, low temperature quenching is used.
Low temperature tempering process: Quenching temperature 960 ~ 980 °C, tempering temperature 280 ~ 320 °C, hardness 60 ~ 62HRC. When high thermal and wear resistance are required, high-temperature quenching and high-temperature tempering processes are used: the quenching temperature is 1020 to 1040 °C, the tempering temperature is 50 to 540 °C, and the hardness is 60 to 62HRC.
(4) 7CrSiMnMoV (Code CH-1) Steel: For air quenched micro-deformation low-alloy steel, flame-hardened steel, can be used to partially quench the flame, harden the die edge. Quenching temperature (800 ~ 1000 °C), with good hardenability and hardenability (up to 60 HRC or more), high strength and toughness, after the collapse can repair welding. Instead of CrWMn and Cr12MoV steels, it is possible to produce punches with complex shapes. Recommended heat treatment process for CH-1 steel: Quenching temperature 900~920 °C, oil cooling, 190~200 °C tempering 1~3 hours, hardness 58~62 HRC.
(5) 6CrNiSiMnMoV (Code GD) Steel: High toughness low alloy steel, hardenability, air quenching deformation, high wear resistance. Its strength and toughness are significantly higher than those of CrWMn and Cr12MoV steels, and they are not easily chipped or broken. It is particularly suitable for slender, laminar punches and large, complex-shaped, thin-walled punches.
Recommended heat treatment process for GD steel: Quenching temperature 870 ~ 930 °C (best 900 °C), salt bath heating (45s/mm), oil or air cooling, air cooling, 175 ~ 230 °C tempering 2 hours, hardness 58 ~ 62 HRC. Since it can be hardened by air cooling, it can also be quenched by flame heating.
(6) 9Cr6W3Mo2V2 (code-named GM) Steel: It is a highly wear-resistant, high-strength and tough alloy steel with good process performance. Its wear resistance, toughness, and processing performance are superior to those of Cr12 steel. It can be used in high-speed press stamping. Multi-position progressive die and other precision molds are ideal wear-resistant, precision Stamping Die steels. GM steel heat treatment process: quenching temperature 1080 ~ 1120 °C, hardness 64 ~ 66HRC. Tempering temperature 540~560 °C, tempering twice.
(7) Cr8MoWV3Si (code ER5) Steel: It is a high wear-resistant, high-strength and tough alloy steel with good EDM performance. Its strength, toughness and wear resistance are superior to those of Cr12 steel. It is suitable for large-scale precision Stamping Die.
For silicon steel blanking die, the life of one-time sharpening is 21 million times, and the total life is as high as 3.6 million times. It is the current high life level of alloy steel punching silicon steel sheet.
Recommended Heat Treatment Process for ER5 Steel: For high wear resistance, high strength and toughness molds, use 1150 °C quenching, 520~530 °C tempering 3 times; for heavy duty service molds, use 1120~1130 °C quenching, 550 °C Tempered 3 times.
3, hard alloy and steel cemented carbide
When the mass of the workpiece is extremely large, it may be considered to select a harder alloy or a hard alloy steel with higher hardness and wear resistance than various types of die steel. The cemented carbide used as the mold material is tungsten-cobalt. As the cobalt content increases, the toughness and bending strength increase and the hardness decreases. For molds with lower impact forces, YG10X with lower cobalt content can be used. For molds with medium or large impact strength, YG15 or YG20 with high cobalt content can be selected. The disadvantage of cemented carbide is poor toughness and difficult to process. As a working part of a mold, it can be designed as a mosaic structure. The performance of steel-bonded carbide is between hard alloy and high-speed steel. It can be machined and heat treated and can be used to make complex high-life molds. The steel cemented carbides used as blanking dies include DT, GT35, TLMW50, GW50 and so on.
1. Carbon tool steel: The carbon tool steel used in the mold is T8A, T10A, etc. The advantages are good processing performance and low price. However, the hardenability and red hardness are poor, heat treatment deformation is large, and the bearing capacity is low.
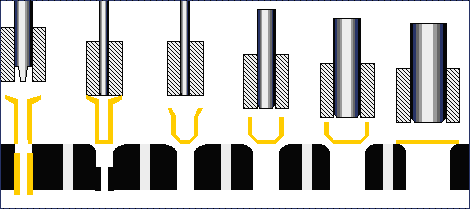
3. High-carbon high-chromium tool steel: Commonly used high-carbon high-chromium tool steels are Cr12 and Cr12MoV, Cr12Mo1V1 (code D2), they have good hardenability, hardenability and wear resistance, heat treatment deformation is very small. High wear-resistant micro-deformation die steel, bearing capacity second only to high-speed steel. However, serious segregation of carbides must be carried out by repeatedly forging (axial boring, radial plunging). To reduce the inhomogeneity of carbides, improve the use of performance.
4. High carbon medium chromium tool steel: The high-carbon medium-chromium tool steels used in the molds include Cr4W2MoV, Cr6WV, Cr5MoV, etc., which have lower chromium content, less eutectic carbides, uniform carbide distribution, and small heat treatment distortion. Has good hardenability and dimensional stability. The performance is improved compared to high carbon high chromium steels where carbide segregation is relatively severe.
5. High speed steel: High-speed steel has the highest hardness, wear resistance and compressive strength in die steels, and has a high load carrying capacity. Commonly used in the mold is W18Cr4V (code 8-4-1) and W6Mo5 Cr4V2 containing less tungste
(Code 6-5-4-2, U.S. Grade M2) and 6W6Mo5 Cr4V (code 6W6 or low carbon M2), a carbon reduction vanadium high speed steel developed to improve toughness. High-speed steel also needs to be upgraded to improve its carbide distribution.
6. Base steel: Add a small amount of other elements to the basic ingredients of high-speed steel, and increase or decrease the carbon content to improve the performance of the steel. Such steels are collectively referred to as base steels. They not only have the characteristics of high-speed steel, have a certain degree of wear resistance and hardness, and fatigue strength and toughness are better than high-speed steel, high strength and toughness cold work die steel, material cost is lower than high-speed steel. The matrix steels commonly used in molds include 6Cr4W3Mo2VNb (code 65Nb), 7Cr7Mo2V2Si (code LD), and 5Cr4Mo3SiMnVAL (code 012AL).
7. Carbide and steel cemented carbide:
Hard alloys have higher hardness and wear resistance than any other type of die steel, but have poor bending strength and toughness. The cemented carbide used as a mold is a tungsten-cobalt type, and a mold with a low impact and a high wear resistance is required, and a hard alloy containing a relatively low amount of cobalt may be used. For high impact molds, carbides with high cobalt content can be used.
Steel cemented carbide is made by adding a small amount of alloying element powder (such as chromium, molybdenum, tungsten, vanadium, etc.) as binder to iron powder, and using titanium carbide or tungsten carbide as hard phase, which is sintered by powder metallurgy. The steel cemented carbide substrate is steel, which overcomes the disadvantages of poor toughness and processing difficulties of the cemented carbide, and can be cut, welded, forged and heat-treated. Steel-bonded carbides contain a large amount of carbides. Although the hardness and wear resistance are lower than those of cemented carbides, they are still higher than those of other steels. After quenching and tempering, the hardness can reach 68 to 73HRC.
Blanking die material selection and heat treatment requirements
Selection of punching die materials should consider the workpiece production batch, if the batch is not large, there is no need to choose a high-life die material; Should be considered to be punched workpiece material, different materials of suitable mold materials are also different. For the punching die, wear resistance is an important factor in determining die life. The wear resistance of steel depends on the condition of carbides and hard spots and the hardness of the substrate. The higher the hardness of the two, the greater the number of carbides, the better the wear resistance. Commonly used Stamping Die steel wear resistance, excellent performance, followed by: Carbon tool steel - alloy tool steel - matrix steel - high carbon high chromium steel - high speed steel - steel cemented carbide - carbide.
In addition, the influence of the thickness, shape, size, and precision requirements of the workpiece on the choice of mold materials must also be considered.
1. Traditional mold steel: For a long time, the steel used in domestic thin blanking die has been T10A, CrWMn, 9Mn2V, Cr12 and Cr12MoV.
Among them, T10A is a carbon tool steel with certain strength and toughness. However, the wear resistance is not high, the quenching is easy to be deformed and cracked, and the hardenability is poor, and it is only applicable to a blanking die with a simple workpiece shape, a small size, and a small number.
T10A carbon tool steel heat treatment process is: 760 ~ 810 °C water or oil quenching, 160 ~ 180 °C tempering, hardness 59 ~ 62HRC.
CrWMn and 9Mn2V are high carbon low alloy steels: Quenching operation is simple, hardenability is better than carbon tool steel, deformation is easy to control. However, the wear resistance and toughness are still low, and they are used in blanking molds with medium-sized batches and complicated workpiece shapes.
CrWMn steel heat treatment process: quenching temperature 820 ~ 840 °C oil cooling, tempering temperature 200 °C, hardness 60 ~ 62HRC.
9Mn2V steel heat treatment process: quenching temperature 780 ~ 820 °C oil cooling, tempering temperature 150 ~ 200 °C, air cooling, hardness 60 ~ 62HRC.
Note tempering brittleness and significant volume expansion in the tempering temperature range of 200-300 °C should be avoided.
Cr12 and Cr12MoV: high carbon high chromium steel, high wear resistance, small deformation during quenching, good hardenability, can be used for mass production of molds, such as silicon steel blanking die. However, carbides of this type have non-uniformity of carbides and are liable to cause segregation of carbides, and are easily chipped or fractured during blanking. Among them, Cr12 has a high carbon content, and the distribution of carbides is more severe than that of Cr12MoV, and the brittleness is greater.
The choice of heat treatment process for Cr12 steel depends on the requirements of the mold. When the mold requires relatively small deformation and certain toughness, it can be quenched and tempered at low temperature (Cr12 is 950~980 °C quenching, 150~200 °C tempering; Cr12MoV is quenched at 1020-1050 °C and tempered at 180-200 °C ). To improve the use of the mold temperature, improve its hardenability and red hardness, high temperature quenching, tempering (Cr12 is 1000 ~ 1100 °C quenching, 480 ~ 500 °C tempering; Cr12MoV is quenched at 1110~1140 °C and tempered at 500~520 °C ). High-chromium steels have temper brittleness in the 275-375 °C zone and should be avoided.
2. New mold steel
In order to compensate for the lack of traditional mold steel performance, domestic development or introduction of better performance Stamping Die steel of the following:
(1) Cr12Mo1V1 (Code D2) steel is a type of steel imported from D2 steel in the United States ASTM standard and belongs to Cr12 steel. As the content of Mo and V in D2 steel increases, the grain is refined, and the distribution of carbides is improved. Therefore, the toughness (impact toughness, bending strength, and deflection) of D2 steel is higher than that of Cr12MoV steel. Sex and anti-tempering stability are also higher than Cr12MoV. Cryogenic treatment can be used to increase hardness and improve dimensional stability. The life of the punching die made of D2 steel is higher than that of the Cr12MoV steel die. The forgeability and thermoformability of D2 steel are slightly worse than that of Cr12MoV steel, and the machining performance and heat treatment process are similar to those of Cr12 steel.
(2) Cr6WV steel is a highly wear resistant micro-deformed high-carbon medium-chromium steel with lower content of carbon and chromium than Cr12 steel. The distribution of carbides is evener than that of Cr12MoV and has good hardenability. Heat treatment deformation is small, better machining performance. The flexural strength and impact toughness are better than Cr12MoV, but the wear resistance is slightly lower than Cr12 steel. The high hardness, high wear-resistance blanking die used to withstand large impacts is better than Cr12 steel.
The commonly used heat treatment process of steel is: the quenching temperature is 9701 ~ 000 °C, generally it can be cooled and quenched by hot oil or nitrate salts, and the parts with small size can adopt air cooling. After quenching, it should be tempered immediately. The tempering temperature is 160210 ~ °C and the hardness is 58 ~ 62HRC.
(3) Cr4W2MoV steel is also a high wear-resistant micro-deformation high-carbon medium-chromium steel. It is developed as a substitute for Cr12 steel. It has good carbide uniformity and wear resistance higher than Cr12MoV. It is suitable for producing complex shapes and high dimensional accuracy. Stamping Die, can be used for silicon steel die.
The heat treatment process of Cr4W2MoV steel: When high strength and toughness are required, low temperature quenching is used.
Low temperature tempering process: Quenching temperature 960 ~ 980 °C, tempering temperature 280 ~ 320 °C, hardness 60 ~ 62HRC. When high thermal and wear resistance are required, high-temperature quenching and high-temperature tempering processes are used: the quenching temperature is 1020 to 1040 °C, the tempering temperature is 50 to 540 °C, and the hardness is 60 to 62HRC.
(4) 7CrSiMnMoV (Code CH-1) Steel: For air quenched micro-deformation low-alloy steel, flame-hardened steel, can be used to partially quench the flame, harden the die edge. Quenching temperature (800 ~ 1000 °C), with good hardenability and hardenability (up to 60 HRC or more), high strength and toughness, after the collapse can repair welding. Instead of CrWMn and Cr12MoV steels, it is possible to produce punches with complex shapes. Recommended heat treatment process for CH-1 steel: Quenching temperature 900~920 °C, oil cooling, 190~200 °C tempering 1~3 hours, hardness 58~62 HRC.
(5) 6CrNiSiMnMoV (Code GD) Steel: High toughness low alloy steel, hardenability, air quenching deformation, high wear resistance. Its strength and toughness are significantly higher than those of CrWMn and Cr12MoV steels, and they are not easily chipped or broken. It is particularly suitable for slender, laminar punches and large, complex-shaped, thin-walled punches.
Recommended heat treatment process for GD steel: Quenching temperature 870 ~ 930 °C (best 900 °C), salt bath heating (45s/mm), oil or air cooling, air cooling, 175 ~ 230 °C tempering 2 hours, hardness 58 ~ 62 HRC. Since it can be hardened by air cooling, it can also be quenched by flame heating.
(6) 9Cr6W3Mo2V2 (code-named GM) Steel: It is a highly wear-resistant, high-strength and tough alloy steel with good process performance. Its wear resistance, toughness, and processing performance are superior to those of Cr12 steel. It can be used in high-speed press stamping. Multi-position progressive die and other precision molds are ideal wear-resistant, precision Stamping Die steels. GM steel heat treatment process: quenching temperature 1080 ~ 1120 °C, hardness 64 ~ 66HRC. Tempering temperature 540~560 °C, tempering twice.
(7) Cr8MoWV3Si (code ER5) Steel: It is a high wear-resistant, high-strength and tough alloy steel with good EDM performance. Its strength, toughness and wear resistance are superior to those of Cr12 steel. It is suitable for large-scale precision Stamping Die.
For silicon steel blanking die, the life of one-time sharpening is 21 million times, and the total life is as high as 3.6 million times. It is the current high life level of alloy steel punching silicon steel sheet.
Recommended Heat Treatment Process for ER5 Steel: For high wear resistance, high strength and toughness molds, use 1150 °C quenching, 520~530 °C tempering 3 times; for heavy duty service molds, use 1120~1130 °C quenching, 550 °C Tempered 3 times.
3, hard alloy and steel cemented carbide
When the mass of the workpiece is extremely large, it may be considered to select a harder alloy or a hard alloy steel with higher hardness and wear resistance than various types of die steel. The cemented carbide used as the mold material is tungsten-cobalt. As the cobalt content increases, the toughness and bending strength increase and the hardness decreases. For molds with lower impact forces, YG10X with lower cobalt content can be used. For molds with medium or large impact strength, YG15 or YG20 with high cobalt content can be selected. The disadvantage of cemented carbide is poor toughness and difficult to process. As a working part of a mold, it can be designed as a mosaic structure. The performance of steel-bonded carbide is between hard alloy and high-speed steel. It can be machined and heat treated and can be used to make complex high-life molds. The steel cemented carbides used as blanking dies include DT, GT35, TLMW50, GW50 and so on.
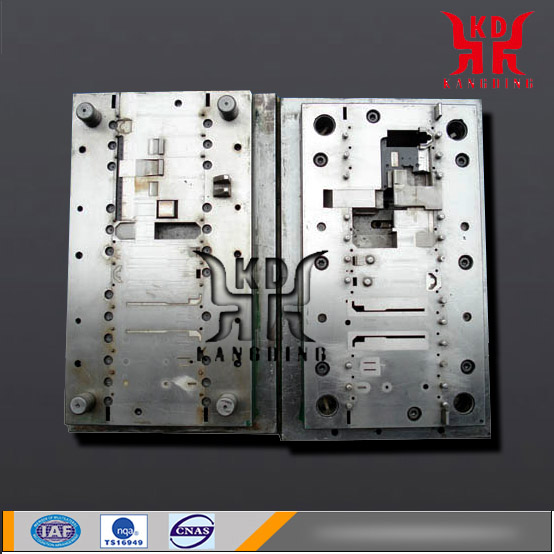