What is CNC turning?
Turning is CNC machining on a lathe, and lathe machining is a part of mechanical processing.
CNC lathe processing mainly uses a turning tool to turn a rotating workpiece. Drills, reamers, taps, dies and knurling tools can also be used on the lathe for corresponding processing. Lathes are mainly used to machine shafts, pins, discs, sleeves and other workpieces with a rotating surface. It is the most widely used turning part in industry.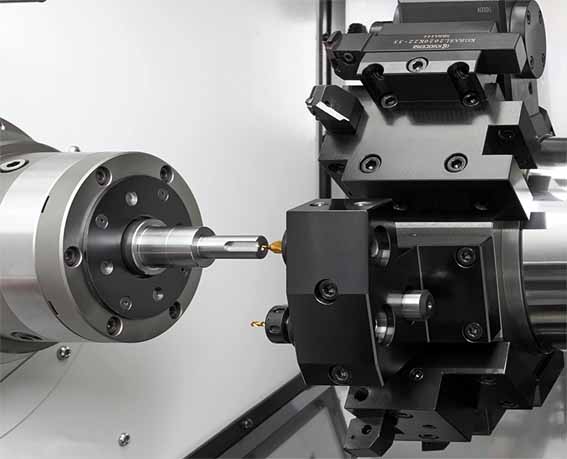
Working principle of turning
The rotation of the workpiece, the turning tool performs cutting processing in a straight line or a curve movement in the plane. Turning is generally performed on a lathe to process the inner and outer cylindrical surfaces, end surfaces, conical surfaces, forming surfaces and threads of the workpiece. When turning the inner and outer cylindrical surfaces, the turning tool moves in a direction parallel to the axis of rotation of the workpiece. When turning the end face or cutting the workpiece, the turning tool moves horizontally in the direction perpendicular to the axis of rotation of the workpiece. If the moving track of the turning tool is at an oblique angle to the axis of rotation of the workpiece, a conical surface can be machined. The surface of the turning body formed by turning can adopt the forming tool method or the tool tip trajectory method. When turning, the workpiece is driven by the main shaft of the machine tool to rotate as the main movement; The turning tool clamped on the tool holder makes a feed movement. Turning speed v: is the linear speed (m/min) at the contact point between the machined surface of the rotating workpiece and the turning tool; The depth of cut is the vertical distance (mm) between the workpiece surface to be machined and the machined surface during each cutting stroke. In turning cutting and forming turning, it is the contact length (mm) between the turning tool and the workpiece perpendicular to the feed direction. The feed rate represents the displacement (mm/rev) of the turning tool in the feed direction per revolution of the workpiece, and it can also be expressed as the feed per minute (mm/min) of the turning tool. When turning ordinary steel with high-speed steel turning tools, the cutting speed is generally 25-60 m/min; cemented carbide turning tools can reach 80-200 m/min; The maximum cutting speed can reach more than 300 m/min when using coated carbide turning tools.Turning is generally divided into rough turning and fine turning (including semi-finish turning).
Rough turning strives to use large turning depth and large feed rate to improve turning efficiency without reducing the cutting speed, but the machining accuracy can only reach IT11, and the surface roughness is Rα20-10 microns; Semi-finishing turning and finishing turning try to use high-speed and small feed and cutting depth. The machining accuracy can reach IT10~7, and the surface roughness is Rα10~0.16 microns. The high-speed precision turning of non-ferrous metal parts with the fine-refined diamond turning tool on the high-precision lathe can make the machining accuracy reach IT7~5. The surface roughness is Rα0.04~0.01 micron, this kind of turning is called "mirror turning". If the concave and convex shapes of 0.1 to 0.2 microns are ground on the cutting edge of a diamond turning tool, the surface of the turning will produce very fine and neatly arranged stripes, which will show a brocade-like luster under the action of light diffraction. It can be used as a decorative turning surface. This kind of turning is called "CD pattern turning parts".
During turning, if the turning tool rotates in the same direction with the workpiece at the corresponding speed ratio (the tool speed is generally several times the workpiece speed) while the workpiece is rotating, the relative motion trajectory of the turning tool and the workpiece can be changed. In this way, turning can process workpieces with polygonal cross-sections (triangular, square, prismatic, hexagonal, etc.). If you add a periodic radial reciprocating motion to the tool holder for each revolution of the workpiece while the turning tool is longitudinally feeding, you can machine cams or other surface parts with non-circular cross-sections. On a shovel lathe, the flank face of certain multi-tooth tools (such as forming milling cutters, gear hobs) can be machined according to a similar working principle, which is called "hobbing".
Process characteristics of turning
1. It is easy to ensure the position accuracy of each processing surface of the workpiecea, for example, it is easy to ensure the coaxiality requirements
Use the chuck to install the workpiece, the rotation axis is the rotation axis of the lathe spindle
Use the front and rear centers to clamp the workpiece, the axis of rotation is the centerline of the two centers
b, It is easy to ensure the verticality requirements of the end face and the axis, and the verticality of the slide guide rail and the rotation axis of the workpiece
2. The cutting process is relatively stable, avoiding inertial force and impact force, allowing the use of larger cutting parameters, high-speed cutting, and improving productivity.
3. Suitable for finishing of non-ferrous metal parts
When the surface roughness of non-ferrous metal parts is large and the Ra value is small, grinding is not suitable, and turning or milling is required. High quality can be achieved when using diamond turning tools for fine turning.
4. The tool is simple
It is convenient to manufacture, sharpen and install turning tools.
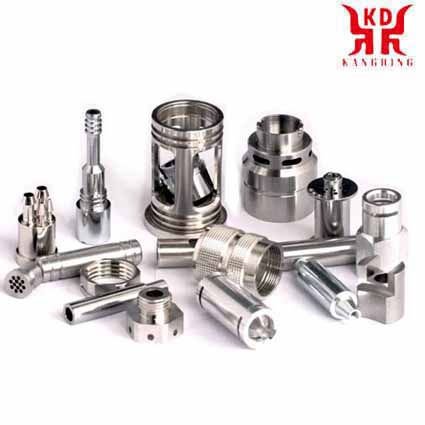
Practical application of turning
Using different turning tools on the lathe can process various rotating surfaces, such as inner and outer cylindrical surfaces, inner and outer conical surfaces, threads, grooves, end surfaces and forming surfaces. The machining accuracy can reach IT8-IT7, and the surface roughness Ra value is 1.6~0.8. Turning is often used to process parts with a single axis, such as straight shafts, general disks, and sleeve parts. If the installation position of the workpiece is changed or the lathe is appropriately modified, multi-axis parts (such as crankshafts, eccentric wheels, etc.) or disc-shaped cams can also be processed. In single-piece small batch production, various shafts, discs, sleeves and other parts are mostly processed by horizontal lathes or CNC lathes with wide adaptability; Large parts with large diameters and short lengths (length-to-diameter ratio 0.3~0.8) are mostly processed by vertical lathes. When mass production of small and medium-sized shafts and sleeve parts with internal holes and threads is more complicated, the turret lathe should be used for processing. When mass production of small parts with less complex shapes, such as screws, nuts, pipe joints, shaft sleeves, etc., semi-automatic and automatic lathes are mostly used for processing. It has high productivity but low accuracy.Turning processing method
1. Rough turning is the most economical and effective method for external roughing. Since the main purpose of roughing is to quickly remove excess metal from the blank, improving productivity is its main task.Rough turning usually uses the largest possible backfeed and feed to improve productivity. In order to ensure the necessary tool life, the turning speed is usually low. When rough turning, the turning tool should choose a larger entering angle to reduce the reverse force and prevent the bending deformation and vibration of the workpiece; Select smaller rake angles, clearance angles and negative edge inclination angles to enhance the strength of the cutting part of the turning tool. The machining accuracy that can be achieved by rough turning is IT12~IT11, and the surface roughness Ra is 50~12.5μm.
2. Fine turning
The main task of precision turning is to ensure the required machining accuracy and surface quality of the parts. The outer surface of the finish turning is generally processed with a smaller back-cutting amount and feed rate and a higher cutting speed. When machining the outer circle of large shaft parts, low-speed precision turning with a wide blade turning tool is often used. When finishing turning, the turning tool should use larger rake angle, back angle and positive tool inclination to improve the surface quality of processing. Finish turning can be used as the final machining of a higher precision outer circle or as a pre-machining for fine machining. The machining accuracy of fine turning can reach IT8~IT6, and the surface roughness Ra can reach 1.6~0.8μm.
3. The characteristics of fine turning are:
The amount of back-cutting and the amount of feed are extremely small, and the turning speed is as high as 150-2000m/min. Fine turning generally uses tools made of superhard materials such as cubic boron amide (CBN) and diamond. The machine tool used must also be a high-precision machine tool with a spindle capable of high-speed rotation and high rigidity. The machining accuracy and surface roughness of fine turning are roughly equivalent to those of ordinary cylindrical grinding. The machining accuracy can reach over IT6, and the surface roughness Ra can reach 0.4 to 0.005 μm. It is mostly used for precision machining of metal workpieces with poor grinding workability. Fine turning is more effective for workpieces such as aluminum and aluminum alloys that are likely to block the pores of the grinding wheel. In the precision outer surface machining of large parts, fine turning can replace grinding.
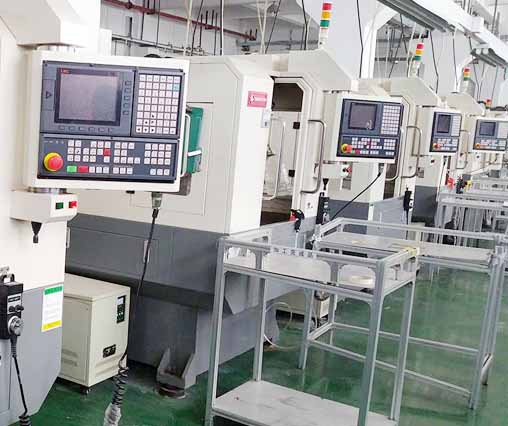
Operational safety of CNC lathe
(1) Before work, lubricate the machine tool according to the regulations, check whether the handles are in place, and start a slow turning test run for five minutes, and confirm that everything is normal before operation.(2) The chuck chuck should be fastened firmly, and the wrench cannot be left on the chuck when the machine is turned on.
(3) The workpiece and the tool should be clamped firmly, and the tool bar should not extend too long (except for boring);
Turn the small tool post to stop turning to prevent the tool from colliding with the chuck, workpiece or scratching your hands.
(4) When the workpiece is running, the operator cannot stand facing the workpiece, not lean on the lathe, or step on the oil pan.
(5) When turning at high speed, chip breaker and shield should be used.
(6) High-speed anti-brake lathes are prohibited, and the lathe should exit and stop turning smoothly.
(7) To remove iron filings, use a brush or special hook.
(8) Grinding the workpiece with a file, the right hand must be in front and the left hand in the back;
(9) All work, measurement, and cutting tools should be placed in a safe place, so that they are neat and orderly.
(10) When the lathe is not stopped, it is forbidden to take the workpiece or measure the workpiece on the lathe.
(11) When the lathe is working, it is forbidden to open or remove the protective device.
(12) Near the end of get off work, the lathe should be cleaned and wiped, and the tailstock and carriage box should be retracted to the far right end of the bed.
turning tool
What is a turning tool?The turning tool is the most widely used single-edged tool. It is also the basis for learning and analyzing various types of tools. Turning tools are used on all kinds of lathes to turn the outer circle, inner hole, end face, thread, groove, etc.
2. Classification of turning tools
According to the structure, turning tools can be divided into integral turning tools, welding turning tools, machine clamp turning tools, indexable turning tools and forming turning tools. Among them, the application of indexable turning tools is becoming more and more widespread, and the proportion of indexable turning tools is gradually increasing.
(1) Carbide welding turning tool
The so-called welded turning tool is a tool slot made on the carbon steel toolholder according to the geometrical angle of the tool. Weld the cemented carbide blade in the slot with solder, and sharpen the used turning tool according to the selected geometric parameters.
(2) Turning tool clamped by machine
The machine clamp turning tool is a turning tool that uses ordinary blades and clamps the blade on the tool bar by mechanical clamping.
(3) Indexable turning tool
The indexable turning tool is a machine clamp turning tool that uses indexable inserts. After a cutting edge is blunt, it can be quickly indexed and replaced with a new adjacent cutting edge, and the work can be continued. Until all the cutting edges on the blade are blunt, the blade is scrapped and recycled. After replacing the new blade, the turning tool can continue to work.
Compared with welding turning tools, indexable turning tools have the following advantages:
A. Long tool life
Because the blade avoids the defects caused by high temperature of welding and sharpening, the geometric parameters of the tool are completely guaranteed by the blade and the shank groove, and the cutting performance is stable, thereby increasing the tool life.
B. High production efficiency
Since the machine operator no longer sharpens the knife, the auxiliary time such as shutting down and changing the tool can be greatly reduced.
C. Conducive to the promotion of new technologies and processes
Indexable knives are conducive to popularizing the use of coatings, ceramics and other new tool materials.
D. Conducive to reducing tool costs
Due to the long service life of the tool holder, the consumption and inventory of the tool holder are greatly reduced, the management of the tool is simplified, and the cost of the tool is reduced.
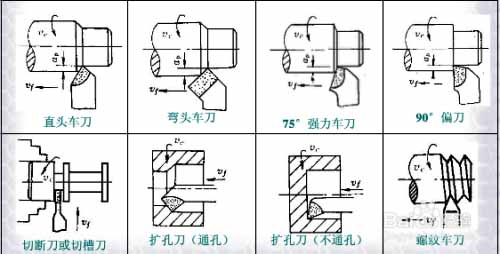
A. High positioning accuracy
After the blade is indexed or replaced with a new blade, the change in the position of the tool tip should be within the allowable range of the accuracy of the workpiece.
B. Reliable clamping of the blade
It should be ensured that the contact surfaces of the blade, shim, and shank fit tightly and can withstand shock and vibration, but the clamping force should not be too large, and the stress distribution should be uniform to avoid crushing the blade.
C. Smooth chip removal
It is best to have no obstacles on the front of the blade to ensure smooth chip discharge and easy observation.
D. Easy to use
It is convenient and quick to change the blade and replace the new blade. For small-sized tools, the structure should be compact. When meeting the above requirements, the structure should be as simple as possible, and the manufacture and use should be convenient.
(4) Forming turning tool
The forming turning tool is a special tool for processing the forming surface of the rotating body. The blade shape is designed according to the profile of the workpiece, and can be used on various lathes to process the forming surface of the inner and outer rotating bodies. The surface of the part can be formed at one time when the part is processed by the forming turning tool, which is easy to operate and high in productivity. After processing, it can reach the tolerance level IT8~IT10, the roughness is 10~5μm, and can guarantee high interchangeability. However, the manufacturing of forming turning tools is more complicated, the cost is higher, and the working length of the blade is wider, so it is easy to cause vibration. Forming turning tools are mainly used for processing batches of small and medium-sized parts with forming surfaces.
Turning tools are classified by purpose
(1) The turning tool can be divided according to its purpose
(A) 90° turning tool (partial tool);
(B) 45° turning tool (elbow turning tool);
(C) Cutting tool;
(D) Boring tool;
(E) Forming turning tool;
(F) Thread turning tool;
(G) Carbide turning tools without heavy grinding
(2) The basic use of various turning tools
(A) 90° turning tool: It is used to turn the outer circle, step table and end face of the workpiece.
(B) 45° turning tool: Used to turn the outer circle, end face and chamfer of the workpiece.
(C) Cutting knife: Used to cut off the workpiece or the groove cut out on the workpiece.
(D) Boring tool: Used to turn the inner hole of the workpiece.
(E) Forming turning tool: It is used for turning round corners, round grooves or turning special-shaped workpieces at the step table.
(F) Pattern turning tool: Used for turning thread.