To Overcome the Difficulties in Processing Various Complex Titanium Alloy Parts, Professional Titanium Alloy Cutting Tools are Needed
The machining efficiency of complex titanium alloy aerospace components and the overall performance of the workpiece. Including common products: titanium alloy complex cavity, titanium alloy deep groove processing, titanium alloy rotation, such as titanium alloy circular interpolation and spiral interpolation slope milling, shoulder milling, milling groove, slot milling and slope milling. Among them, screening excellent tool suppliers in combination with their actual needs is one of the important measures.
Aviation parts generally have the characteristics of material and structure which are difficult to process. High tool costs, processing quality and processing efficiency are difficult to guarantee, which is a common challenge in production, especially for titanium alloy structural parts. The development of modern aircraft design technology provides a broad space for the development of titanium alloys with superior overall performance. At the same time, in the face of the trend of complex structure design of titanium alloy, the overall structure, deep cavity structure, thin-walled structure and so on are widely adopted, which poses a serious challenge for tool selection and cutting mode determination. Kangding company has been standing in the forefront of advanced manufacturing, finishing center of titanium alloy parts processing innovation. "After our technical team has worked out the tool selection method and cutting strategy for different material properties and geometric characteristics of aeronautical titanium alloy structural parts. Seco has always been able to provide the corresponding products and solutions, and successfully achieve the workpiece machining accuracy and processing efficiency requirements, and also effectively reduce tool loss. ”
High-efficiency roughing of titanium alloy complex cavity
Irregular complex cavities are typical structures for aerospace parts. For the roughing of complex cavities of titanium alloys, the finishing center technical optimization team believes that the large feed tool is the best tool type.
The relationship between the radius of the tool arc bottom edge and its maximum cutting thickness is:
It can be seen from the above formula that when the cutting depth is increased, the radius of the arc edge can be increased, the main deflection angle can be reduced to maintain a thin cutting thickness, the tool life can be improved, and the processing time can be shortened.
The high feed tool achieves a high feed rate. As shown in Fig. 1, compared with the traditional end milling, the large feed tool adopts a large arc radius and a small lead angle design, which reduces the axial depth and reduces the cutting thickness. This large feed milling method that reduces chip thickness effectively reduces the main cutting edge load. At the same time, the extremely small thickness of the chips can also take away a lot of cutting heat, improve tool durability and shorten processing time. This advantage is also very suitable for rough machining of complex cavities.
In the complex cavity roughing process of Kangding Precision Machining Center. Seco offers an indexable large feed milling cutter that not only achieves higher cutting speeds and feed rates during machining. Due to the small milling depths brought by the large feed milling method, a more uniform milling allowance can be achieved, which is advantageous for stable milling of subsequent machining.
Plug milling cutter can be used for deep groove processing of titanium alloy
"For deep groove machining of aerospace titanium alloy structural parts, due to the difficult processing characteristics of the material itself and the geometric characteristics of deep groove cavities and corners, the precision and stability of the machining are very difficult to guarantee, which once plagued us. After understanding our needs and difficulties, Seco Tools gave a solution for inserting and milling tools, which achieved good results and far exceeded our expectations. "
Plug milling is an efficient processing method for deep grooves or corners. For the deep cavity machining and corner machining of complex structural parts, the plunge milling technology has unique advantages. “In actual machining, plunge milling is very different from traditional milling. Plunge milling uses the end of the tool for cutting, not the side, which mainly produces axial forces. Plug milling cutter can be used in large tool overhang applications, in deep groove processing or difficult to machine materials, combined with good toughness of the blade material and sharp groove. It can help customers achieve good production efficiency, processing results and economic advantages. ”
Round insert milling cutter improves processing efficiency with its flexibility
In order to better promote the processing of titanium alloys, for the multi-type surface features existing in aerospace structural parts, Seco Tools uses a circular insert milling cutter that can adapt to various types of surface machining to improve processing efficiency.
Because of its unique geometric angle and high strength, circular blades are very suitable for the processing of titanium alloy, which is a difficult-to-machine material, and can obtain high metal removal rate and tool life.
"Round insert milling cutter can also be used in many kinds of cutting methods, such as circular interpolation and spiral interpolation slope milling, square shoulder milling, milling groove, slotting milling and slope milling. It is a flexible tool in three-dimensional milling."
Different part structure requirements
Different parts structure, its needs and focus in processing are also different. For simpler contours or cavity structures, the economics of processing cannot be ignored; For grooving, safety under strict standards is critical.
In the contour or simple cavity structure processing, Seco's corn milling cutter was selected. Corn milling cutters not only achieve large depth of cut, large cutting width and powerful milling, but also greatly increase cutting force and cutting efficiency. What's important is that the corn milling cutter can use a variety of geometric blades in the actual processing, and each blade can be indexed multiple times, greatly reducing the cutting cost of rough machining of large titanium alloy parts.
The cost of aerospace components is very high and the safety during production is critical. In order to match our strong product strength, our company has extremely strict requirements for the slotting processing of titanium alloy. There are many narrow groove geometry features for aerospace titanium structural components. The JCO710 corrugated milling cutter developed by Seco Tools offers long tool life and very high machining safety, making it ideal for high-efficiency roughing of stainless steel and titanium alloys with large axial depths. It is applied to the processing of large parts in the aerospace industry and achieves good results.
Aviation parts generally have the characteristics of material and structure which are difficult to process. High tool costs, processing quality and processing efficiency are difficult to guarantee, which is a common challenge in production, especially for titanium alloy structural parts. The development of modern aircraft design technology provides a broad space for the development of titanium alloys with superior overall performance. At the same time, in the face of the trend of complex structure design of titanium alloy, the overall structure, deep cavity structure, thin-walled structure and so on are widely adopted, which poses a serious challenge for tool selection and cutting mode determination. Kangding company has been standing in the forefront of advanced manufacturing, finishing center of titanium alloy parts processing innovation. "After our technical team has worked out the tool selection method and cutting strategy for different material properties and geometric characteristics of aeronautical titanium alloy structural parts. Seco has always been able to provide the corresponding products and solutions, and successfully achieve the workpiece machining accuracy and processing efficiency requirements, and also effectively reduce tool loss. ”
High-efficiency roughing of titanium alloy complex cavity
Irregular complex cavities are typical structures for aerospace parts. For the roughing of complex cavities of titanium alloys, the finishing center technical optimization team believes that the large feed tool is the best tool type.
The relationship between the radius of the tool arc bottom edge and its maximum cutting thickness is:
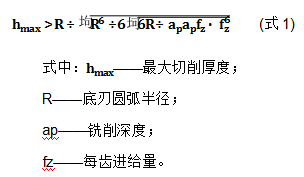
The high feed tool achieves a high feed rate. As shown in Fig. 1, compared with the traditional end milling, the large feed tool adopts a large arc radius and a small lead angle design, which reduces the axial depth and reduces the cutting thickness. This large feed milling method that reduces chip thickness effectively reduces the main cutting edge load. At the same time, the extremely small thickness of the chips can also take away a lot of cutting heat, improve tool durability and shorten processing time. This advantage is also very suitable for rough machining of complex cavities.
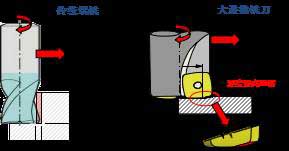
In the complex cavity roughing process of Kangding Precision Machining Center. Seco offers an indexable large feed milling cutter that not only achieves higher cutting speeds and feed rates during machining. Due to the small milling depths brought by the large feed milling method, a more uniform milling allowance can be achieved, which is advantageous for stable milling of subsequent machining.
Plug milling cutter can be used for deep groove processing of titanium alloy
"For deep groove machining of aerospace titanium alloy structural parts, due to the difficult processing characteristics of the material itself and the geometric characteristics of deep groove cavities and corners, the precision and stability of the machining are very difficult to guarantee, which once plagued us. After understanding our needs and difficulties, Seco Tools gave a solution for inserting and milling tools, which achieved good results and far exceeded our expectations. "
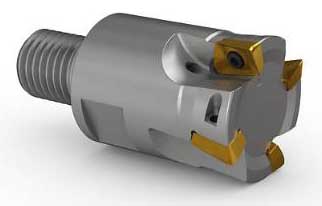
Plug milling is an efficient processing method for deep grooves or corners. For the deep cavity machining and corner machining of complex structural parts, the plunge milling technology has unique advantages. “In actual machining, plunge milling is very different from traditional milling. Plunge milling uses the end of the tool for cutting, not the side, which mainly produces axial forces. Plug milling cutter can be used in large tool overhang applications, in deep groove processing or difficult to machine materials, combined with good toughness of the blade material and sharp groove. It can help customers achieve good production efficiency, processing results and economic advantages. ”
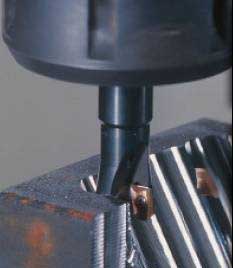
Round insert milling cutter improves processing efficiency with its flexibility
In order to better promote the processing of titanium alloys, for the multi-type surface features existing in aerospace structural parts, Seco Tools uses a circular insert milling cutter that can adapt to various types of surface machining to improve processing efficiency.
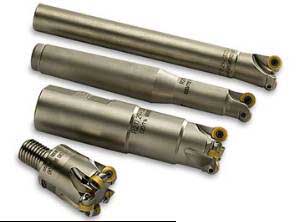
"Round insert milling cutter can also be used in many kinds of cutting methods, such as circular interpolation and spiral interpolation slope milling, square shoulder milling, milling groove, slotting milling and slope milling. It is a flexible tool in three-dimensional milling."
Different part structure requirements
Different parts structure, its needs and focus in processing are also different. For simpler contours or cavity structures, the economics of processing cannot be ignored; For grooving, safety under strict standards is critical.
In the contour or simple cavity structure processing, Seco's corn milling cutter was selected. Corn milling cutters not only achieve large depth of cut, large cutting width and powerful milling, but also greatly increase cutting force and cutting efficiency. What's important is that the corn milling cutter can use a variety of geometric blades in the actual processing, and each blade can be indexed multiple times, greatly reducing the cutting cost of rough machining of large titanium alloy parts.
The cost of aerospace components is very high and the safety during production is critical. In order to match our strong product strength, our company has extremely strict requirements for the slotting processing of titanium alloy. There are many narrow groove geometry features for aerospace titanium structural components. The JCO710 corrugated milling cutter developed by Seco Tools offers long tool life and very high machining safety, making it ideal for high-efficiency roughing of stainless steel and titanium alloys with large axial depths. It is applied to the processing of large parts in the aerospace industry and achieves good results.
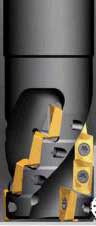