Effect of Radial Cutting Depth Change of Titanium Alloy on High Speed Milling Force
The machined titanium tool is made of Walter carbide insert end mill, grade ZDGT150416R-K85 WMG40, uncoated, diameter 25mm, corner radius r=1.6mm, two teeth, see Figure 1. The milling force test of high-speed milling of ferroalloy TC4 was carried out under dry milling, air oil mist and nitrogen oil mist medium.
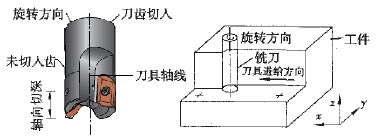
Figure 1 End mill structure diagram and milling diagram
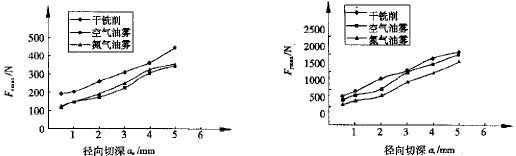
(a) Maximum milling force in the x direction, (b) Maximum milling force in the y direction
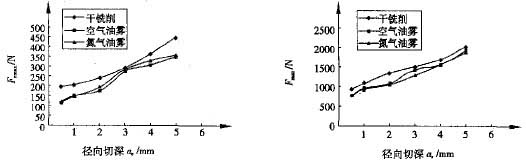
(c) Maximum milling force in the z direction. (d) Maximum milling force
Fig. 2 Curve of milling force with ae under different media
It can be seen from Figure 2:
Fxmax, Fymax, Fzmax, and Fmax in the three media all increase with time, and their increasing trends are basically linear. The reason is that as the radial depth of cut increases, the milling wrap angle between the tool and the workpiece increases, which increases the milling area of the tool, thereby increasing the friction between the tool and the workpiece. So it leads to Fymax: increase; In the test, insert milling was used, and the tool's helix angle was 0 °. Therefore, as the radial cutting depth ae increases, the maximum milling force changes in the x and z directions are not very obvious, which is consistent with the theoretical analysis. The curves were linearly and exponentially fitted, and their correlation coefficients R2 were all above 0.91.
Figure 2 (a) shows that the increasing trend of Fxmax with ae in the three milling media is basically the same, but the amplitude is not obvious. The dry milling Fxmax is slightly larger than the air oil mist and nitrogen oil mist. From Figure 2 (b), (c), (d), it can be seen that Fymax, Fzmax, and Fmax increase with ae, and the change curves under different media are similar; Fymax, Fzmax, and Fmax in air oil mist and nitrogen oil mist are all smaller than in dry milling. The combined forces of dry milling were 22.2%, 15.07%, 25.75%, 5.98%, 8.3% and 5.45% larger than air oil mist, respectively. It is 18.3%, 16.6%, 27.5%, 15.96%, 8.38% and 7.92% larger than nitrogen oil mist. In addition, the milling force under air oil mist and nitrogen oil mist is approximately the same.