Deformation of chips during milling of titanium alloy
I. Chip morphology of milling titanium alloy under different media
When milling titanium alloy at high speed under different media, due to the different friction and heat dissipation conditions between the tool and the chip, the shape and surface condition of the chip are also different, as shown in Figure 2. Compared with dry milling, the friction between the tool and the chip is larger, the temperature in the milling area is higher, the deformation of the chip after passing through the rake face is larger, the stripe folds on the chip surface are more, and the flatness is poor.
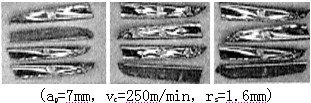
(ap = 7mm, vc = 250m / min, rs = 1.6mm)
Fig. 2 Chip status of titanium alloy under different media
II. Chip morphology of titanium alloy at different milling speeds
In the high-speed milling test of titanium alloys, the analysis of chip morphology generated under different milling speeds is very different. Therefore, the milling speed has a greater impact on the macroscopic morphology of chips. Figure 3 is a picture of the chips at different milling speeds.
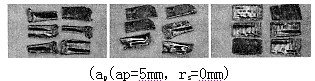
(ap (ap = 5mm, rs = 0mm)
Fig. 3 Chip morphology of titanium alloy at different milling speeds under air oil mist
From the analysis of the above figure, it can be concluded that as the milling speed increases, the chip shape becomes more and more regular. Especially when the milling speed reaches 300m / mim, after calculation and measurement, the length and width of the chip are close to the theoretical value (the deformation coefficient of titanium alloy is very small and almost equal to 1, or even less than 1). The main cause of irregular chips is that the lower the speed, the longer the contact time between the chip and the tool, the longer the friction time between the chip and the tool, so the deformation of the chip is more obvious at lower speed. The higher the speed, the shorter the time that the chip is rubbed by the tool, and the less obvious the deformation of the chip; In addition, as the milling speed increases, the milling temperature will gradually increase, the friction coefficient will decrease, and the smaller the frictional force on the chips. The smaller the chip deformation.
III. Micro analysis of chip deformation in titanium alloy
It can be seen from Figure 4 that the microscopic morphology of the chip surface is different under different media. There are some micro-cracks on the chips under the nitrogen oil mist medium (Figure 4 (c)). These micro-cracks are mainly distributed at the edges and ends of the chips. Most of the microcracks are in the same direction as the sliding direction of the chips along the rake face (region I in Fig. 5), and a small number of microcracks are perpendicular to the sliding direction of the titanium alloy chips (region II in Fig. 5). The reasons for micro-cracks in chips under nitrogen oil mist media may be:
1. Nitrogen oil mist is sprayed into the cutting area, which instantly takes away a lot of heat, causing the titanium alloy chips to generate thermal stress and thermal cracks;
2. Nitrogen in the nitrogen oil mist chemically reacts with titanium in the titanium alloy cuttings to form a more brittle titanium nitride. These titanium nitrides are distributed on the surface and inside of the chip, making the chip vulnerable to brittleness under strong extrusion and friction.

(ap = 7mm, vc = 300m / min, rs = 1.6mm)
Fig. 4 SEM photograph of partial frontal surface of titanium alloy chips under different cutting media
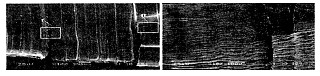
(ap (ap = 5mm, vc = 300m / min, rs = 1.6mm)
Fig.5 SEM image of the chip cracking area of titanium alloy under nitrogen oil mist medium
Because air oil mist also takes away a lot of heat in titanium alloy cutting. However, the titanium alloy chip does not have microcracks (Figure 4 (a)), so the first possibility is not true, so it can be considered that the microcracks are caused by the presence of nitrogen. Titanium alloy chips are easy to be brittle, which will reduce the impact of the chips on the milling cutter when it flows through the rake face, thereby reducing the milling force to a certain extent.
IV. Metallographic analysis of titanium alloy chips
1.Comparison of metallographic photos
During the formation of titanium alloy chips, the plasticity of the material is greater. Due to the resulting work hardening, the stress on the shear slip surface of the chip increases, and the strength limit of the material is locally reached. At this time, the chips are only cracked in the upper part and the lower parts are still connected, that is, the side close to the rake face is smooth and the other side is sawtooth-shaped, forming a concentrated shear sliding titanium alloy chip.
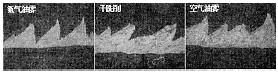
(ap (ap = 7mm, vc = 300m / min, rs = 1.6mm)
Fig. 6 Metallographic pictures of titanium alloy chips in different media
Figure 6 shows that the nodularization tendency of titanium alloy chips under nitrogen oil mist is very obvious, the connection at the bottom of the chips has become very rare, and sometimes the chip nodes and nodes are almost separated. The nodularization tendency of titanium alloy chips under air oil mist is more obvious than that during dry milling, but it is not as good as nitrogen oil mist.
The cause of chip nodularity under nitrogen oil mist and air oil mist is more obvious than dry milling. It is because the cooling effect of the oil mist reduces the plasticity of the titanium alloy on the cutting and sliding surface of the chip, and the chip is easily sheared along the sliding surface. Under nitrogen oil mist, brittle TiN was formed on the shear slip surface due to nitrogen and titanium. At high speeds, the high shear force strengthens the concentrated shear slip of the chips, thereby making the nodular features of the chips more prominent.
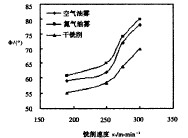
Fig. 7 Effect of milling speed on shear angle (r = 1.6)
2, Comparison of shear angle f
FIG. 7 is a graph of shear angle f as a function of speed. The figure shows that as the milling speed increases, the cutting angle of titanium alloy chips in air oil mist, nitrogen oil mist, and dry milling conditions has an increasing trend, that is, a trend of chip deformation decreasing. This trend is even more pronounced when the milling speed exceeds 275 m / min. There are two main reasons for this result, one is that the deformation time of the titanium alloy is reduced and the deformation of the titanium alloy is reduced; On the other hand, the chip speed has an influence on the average friction coefficient of the rake face. In high-speed cutting, the higher the cutting speed, the smaller the average friction coefficient of the rake face. When the cutting speed is very high, due to the high cutting temperature, the bottom layer of the chip is softened, forming a thin slightly soluble layer. In this case, the change in cutting speed has little effect on chip deformation.
In addition, at the same speed, the cutting angle of the chip under the nitrogen oil mist is larger than that of the air oil mist. The reason for this is that the presence of titanium nitride on the shear slip surface of titanium chips under a nitrogen medium reduces the plasticity of the shear slip surface. Chips are more prone to plastic instability during concentrated shear slip, so chip deformation is reduced and shear angle f is reduced.
When milling titanium alloy at high speed under different media, due to the different friction and heat dissipation conditions between the tool and the chip, the shape and surface condition of the chip are also different, as shown in Figure 2. Compared with dry milling, the friction between the tool and the chip is larger, the temperature in the milling area is higher, the deformation of the chip after passing through the rake face is larger, the stripe folds on the chip surface are more, and the flatness is poor.
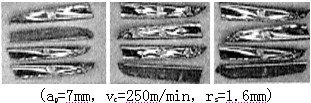
(ap = 7mm, vc = 250m / min, rs = 1.6mm)
Fig. 2 Chip status of titanium alloy under different media
II. Chip morphology of titanium alloy at different milling speeds
In the high-speed milling test of titanium alloys, the analysis of chip morphology generated under different milling speeds is very different. Therefore, the milling speed has a greater impact on the macroscopic morphology of chips. Figure 3 is a picture of the chips at different milling speeds.
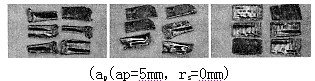
(ap (ap = 5mm, rs = 0mm)
Fig. 3 Chip morphology of titanium alloy at different milling speeds under air oil mist
From the analysis of the above figure, it can be concluded that as the milling speed increases, the chip shape becomes more and more regular. Especially when the milling speed reaches 300m / mim, after calculation and measurement, the length and width of the chip are close to the theoretical value (the deformation coefficient of titanium alloy is very small and almost equal to 1, or even less than 1). The main cause of irregular chips is that the lower the speed, the longer the contact time between the chip and the tool, the longer the friction time between the chip and the tool, so the deformation of the chip is more obvious at lower speed. The higher the speed, the shorter the time that the chip is rubbed by the tool, and the less obvious the deformation of the chip; In addition, as the milling speed increases, the milling temperature will gradually increase, the friction coefficient will decrease, and the smaller the frictional force on the chips. The smaller the chip deformation.
III. Micro analysis of chip deformation in titanium alloy
It can be seen from Figure 4 that the microscopic morphology of the chip surface is different under different media. There are some micro-cracks on the chips under the nitrogen oil mist medium (Figure 4 (c)). These micro-cracks are mainly distributed at the edges and ends of the chips. Most of the microcracks are in the same direction as the sliding direction of the chips along the rake face (region I in Fig. 5), and a small number of microcracks are perpendicular to the sliding direction of the titanium alloy chips (region II in Fig. 5). The reasons for micro-cracks in chips under nitrogen oil mist media may be:
1. Nitrogen oil mist is sprayed into the cutting area, which instantly takes away a lot of heat, causing the titanium alloy chips to generate thermal stress and thermal cracks;
2. Nitrogen in the nitrogen oil mist chemically reacts with titanium in the titanium alloy cuttings to form a more brittle titanium nitride. These titanium nitrides are distributed on the surface and inside of the chip, making the chip vulnerable to brittleness under strong extrusion and friction.

(ap = 7mm, vc = 300m / min, rs = 1.6mm)
Fig. 4 SEM photograph of partial frontal surface of titanium alloy chips under different cutting media
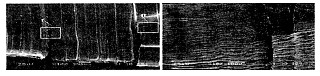
(ap (ap = 5mm, vc = 300m / min, rs = 1.6mm)
Fig.5 SEM image of the chip cracking area of titanium alloy under nitrogen oil mist medium
Because air oil mist also takes away a lot of heat in titanium alloy cutting. However, the titanium alloy chip does not have microcracks (Figure 4 (a)), so the first possibility is not true, so it can be considered that the microcracks are caused by the presence of nitrogen. Titanium alloy chips are easy to be brittle, which will reduce the impact of the chips on the milling cutter when it flows through the rake face, thereby reducing the milling force to a certain extent.
IV. Metallographic analysis of titanium alloy chips
1.Comparison of metallographic photos
During the formation of titanium alloy chips, the plasticity of the material is greater. Due to the resulting work hardening, the stress on the shear slip surface of the chip increases, and the strength limit of the material is locally reached. At this time, the chips are only cracked in the upper part and the lower parts are still connected, that is, the side close to the rake face is smooth and the other side is sawtooth-shaped, forming a concentrated shear sliding titanium alloy chip.
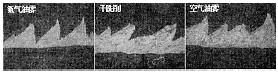
(ap (ap = 7mm, vc = 300m / min, rs = 1.6mm)
Fig. 6 Metallographic pictures of titanium alloy chips in different media
Figure 6 shows that the nodularization tendency of titanium alloy chips under nitrogen oil mist is very obvious, the connection at the bottom of the chips has become very rare, and sometimes the chip nodes and nodes are almost separated. The nodularization tendency of titanium alloy chips under air oil mist is more obvious than that during dry milling, but it is not as good as nitrogen oil mist.
The cause of chip nodularity under nitrogen oil mist and air oil mist is more obvious than dry milling. It is because the cooling effect of the oil mist reduces the plasticity of the titanium alloy on the cutting and sliding surface of the chip, and the chip is easily sheared along the sliding surface. Under nitrogen oil mist, brittle TiN was formed on the shear slip surface due to nitrogen and titanium. At high speeds, the high shear force strengthens the concentrated shear slip of the chips, thereby making the nodular features of the chips more prominent.
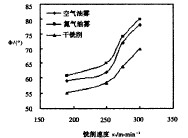
Fig. 7 Effect of milling speed on shear angle (r = 1.6)
2, Comparison of shear angle f
FIG. 7 is a graph of shear angle f as a function of speed. The figure shows that as the milling speed increases, the cutting angle of titanium alloy chips in air oil mist, nitrogen oil mist, and dry milling conditions has an increasing trend, that is, a trend of chip deformation decreasing. This trend is even more pronounced when the milling speed exceeds 275 m / min. There are two main reasons for this result, one is that the deformation time of the titanium alloy is reduced and the deformation of the titanium alloy is reduced; On the other hand, the chip speed has an influence on the average friction coefficient of the rake face. In high-speed cutting, the higher the cutting speed, the smaller the average friction coefficient of the rake face. When the cutting speed is very high, due to the high cutting temperature, the bottom layer of the chip is softened, forming a thin slightly soluble layer. In this case, the change in cutting speed has little effect on chip deformation.
In addition, at the same speed, the cutting angle of the chip under the nitrogen oil mist is larger than that of the air oil mist. The reason for this is that the presence of titanium nitride on the shear slip surface of titanium chips under a nitrogen medium reduces the plasticity of the shear slip surface. Chips are more prone to plastic instability during concentrated shear slip, so chip deformation is reduced and shear angle f is reduced.