3D Printing Manufacturing Complex Titanium Alloy Insert
During the space launch, the cost of feeding each kilogram of items into satellite orbit is about $20,000. Saving each gram of weight helps to increase the efficiency of space exploration. KangDing has worked with the engineering department of Atos, a global digital services provider, to redevelop a titanium alloy insert that is widely used in satellites.
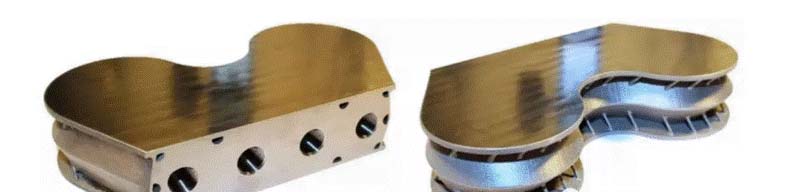
When designing or manufacturing a spacecraft component, the biggest challenge is to optimize weight without sacrificing component strength or performance. Titanium alloy inserts are widely used in the aerospace industry to transfer high mechanical loads in structures such as satellites. Thanks to its sleek, optimized design and metal 3D printing, the new titanium inserts weigh only one-third the weight of stainless steel and have improved performance.
Insert into the sandwich panel structure
Titanium inserts typically used to connect other equipment to the satellite, Such inserts are subjected to high loads and require a large and heavy structure to be lifted. This means that they must have a high strength to weight ratio, high strength and rigidity, and must be very light in weight. These inserts are placed in a composite structural sandwich panel that is common in aerospace structures, and the load is transferred by bonding with the sandwich panel.
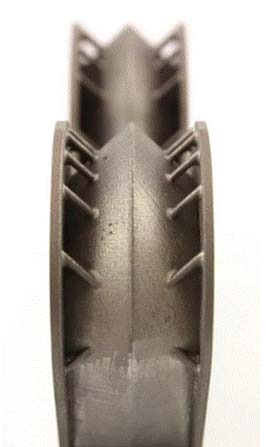
Conventional inserts are usually machined from aluminum or titanium alloys, and the interior is completely solid and of high quality. In addition to the high cost of materials, heavy-duty components also increase the operating cost of spacecraft for each launch, and metal 3D printing provides an opportunity for weight reduction of aerospace structural components.
Optimize design with 3D printing
Engineers face the challenge of changing traditional thinking. This design is designed to meet all requirements from the concept phase to the manufacturing phase. Atos relies on expertise in aerospace engineering and structural simulation to design this new component from the inside out, improving its overall performance.
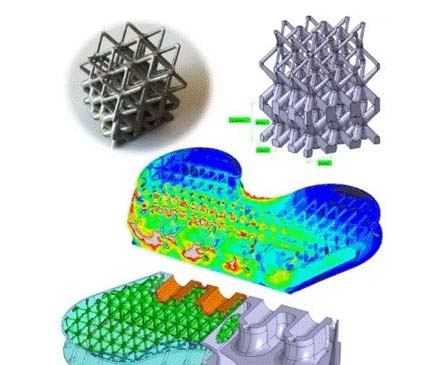
With 3D printing, the interior of the object can be designed with a hollow or lightweight structure. KangDing and Atos engineers began by reducing the amount of material used inside the parts. The R&D team used advanced techniques such as topology optimization and lattice structure design to reduce the insert quality from 1454 grams to 500 grams.
In addition to reducing weight, the team also solved the thermoelastic stress problem in the original design. Since these inserts carbon fiber reinforced polymer splint curing process has been mounted, and therefore subject to thermal stress elastically. Optimized design reduces the effects of these stresses and improves load distribution, extending the life of the insert.
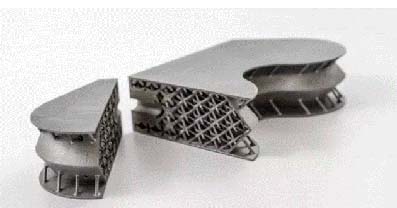
The cross section of the insert shows the lightweight structure inside
The KangDing Metal 3D Printing Factory is responsible for the production of two new titanium alloy (TiAl6V4) inserts. Metal 3D printing has proven its great potential in the aerospace industry, and there has been no previous means to achieve such fast delivery times.
Atos Spain's Director of Mechanical Engineering commented: "Lightening weight will help increase the payload of satellite equipment and save a lot of cost per launch. It is precisely because of this highly complex product created in the field of metal additive manufacturing in such a short period of time that Atos and KangDing are among the leading suppliers of metal 3D printing solutions. ”
From the past cases, we can see that KangDing has penetrated into various application fields, constantly challenged the status of traditional processing methods, and constantly explored the profound application of 3D printing in traditional manufacturing, promoted change, and promoted the development of 3D printing.