How to Choose Down Milling and Inverse Milling for NC Machine Tool Processing Parts
In the process of using NC machine tools, how to make the right choice for forward milling and reverse milling?
How to define forward milling and reverse milling?
As shown in the following figure: Climb milling is that the cutting speed of the tool is the same as that of the workpiece. Reverse milling is the opposite of the cutting speed of the tool and the moving direction of the workpiece.
Characteristics of Climb milling and reverse milling
1. Influence on cutting force
In reverse milling, the vertical cutting force acting on the workpiece is always upward, which tends to lift the workpiece and easily causes vibration. Affecting the clamping of workpiece, this situation is particularly prominent in Milling Thin-walled and stiffness poor workpiece. The vertical cutting component acting on the workpiece during the down-milling always presses the workpiece, which is advantageous for the clamping of the workpiece.
2. Influence on the elastic deformation of the tool
When cutting the workpiece contour with an end mill. The reaction force of the workpiece to the tool points to the direction of the tool. The elastic deformation of the tool results in the phenomenon of tool yielding (undercutting).
When the end milling cutter is used to reverse milling the workpiece contour. The reaction force of the workpiece to the cutter points to the inside of the contour, and the elastic deformation of the cutter causes the phenomenon of "gnawing the cutter" (over-cutting). The smaller the tool diameter and the longer the tool rod is extended, the more obvious the phenomena of "letting the knife" and "gnawing the knife" are.
Therefore, when rough machining adopts forward milling, less finishing allowance can be left. When reverse milling is used in rough machining, more finishing allowance should be left to prevent the scrap of workpiece caused by "gnawing cutter".
3. Influence on tool wear
The vertical milling component of the down-milling presses the workpiece against the table. The knife teeth and the machined surface slide and the friction phenomenon is small, which is beneficial for reducing the tooth wear, reducing the work hardening phenomenon and reducing the surface roughness.
In addition, the cutting thickness of the cutter teeth from the maximum to zero. The impact force when cutting the cutter into the workpiece is large, especially when the surface to be processed of the workpiece is a blank or has a hard skin, the cutter will generate a large vibration.
However, when the milling is performed, the distance that the teeth travel on the workpiece is shorter than that of the reverse milling, and the average cutting thickness is large. Therefore, under the same cutting conditions, when using up-cut milling, the tool is prone to wear and consumes more cutting power.
How to choose forward milling and reverse milling?
1, the principle of selection
When using down-cut milling, the machine first needs to have a clearance elimination mechanism to reliably eliminate the gap between the feed screw and the nut of the table to prevent vibration during milling.
The workbench is ideally driven by hydraulics. Secondly, the surface of the workpiece blank is required to have no hard skin, and the process system must have sufficient rigidity. If the above conditions can be met, down-cut milling should be used as much as possible, especially for difficult-to-machine materials. The use of down-cutting reduces cutting distortion and reduces cutting forces and cutting power.
When roughing parts, reverse milling is usually used. In order to prevent "gnawing cutter" during finishing, the way of down milling is usually adopted.
2. Relationship with tool radius compensation
When performing contour milling on CNC machines, tool radius compensation is often used for programming and machining. The tool radius compensation is further divided into tool radius left compensation and tool radius right compensation.
The method for judging the tool radius left compensation is:
The tool is turning forward (clockwise) and the tool is located to the left of the machined profile as it looks in the forward direction of the tool. On the contrary, the tool is located to the right of the machining contour. This compensation method is called tool radius right compensation.
Therefore, whether it is the inner contour or the outer contour machining, the machining method using the tool radius left compensation programming milling is the down milling. The machining method using the tool radius right compensation programming milling is the up-cut milling.
When using a disc milling cutter to machine a plane profile, when the cutting width of the tool is greater than 50% of the tool diameter, the cutting process has both down-cut milling and reverse milling.
3. Selection of forward milling and reverse milling for NC milling machine
CNC machine tools generally have anti-backlash function, the backlash of the transmission mechanism is small, and CNC machine tools mostly perform part finishing. Therefore, CNC milling usually adopts the processing method of the down-cut milling, that is, the tool radius is compensated by the left compensation for programming and machining.
How to define forward milling and reverse milling?
As shown in the following figure: Climb milling is that the cutting speed of the tool is the same as that of the workpiece. Reverse milling is the opposite of the cutting speed of the tool and the moving direction of the workpiece.
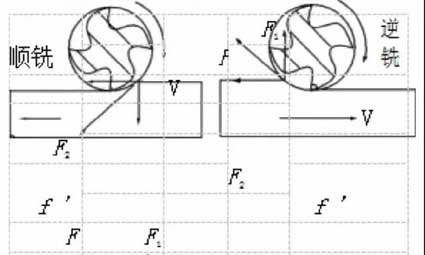
Characteristics of Climb milling and reverse milling
1. Influence on cutting force
In reverse milling, the vertical cutting force acting on the workpiece is always upward, which tends to lift the workpiece and easily causes vibration. Affecting the clamping of workpiece, this situation is particularly prominent in Milling Thin-walled and stiffness poor workpiece. The vertical cutting component acting on the workpiece during the down-milling always presses the workpiece, which is advantageous for the clamping of the workpiece.
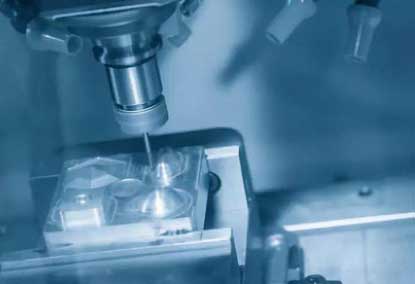
2. Influence on the elastic deformation of the tool
When cutting the workpiece contour with an end mill. The reaction force of the workpiece to the tool points to the direction of the tool. The elastic deformation of the tool results in the phenomenon of tool yielding (undercutting).
When the end milling cutter is used to reverse milling the workpiece contour. The reaction force of the workpiece to the cutter points to the inside of the contour, and the elastic deformation of the cutter causes the phenomenon of "gnawing the cutter" (over-cutting). The smaller the tool diameter and the longer the tool rod is extended, the more obvious the phenomena of "letting the knife" and "gnawing the knife" are.
Therefore, when rough machining adopts forward milling, less finishing allowance can be left. When reverse milling is used in rough machining, more finishing allowance should be left to prevent the scrap of workpiece caused by "gnawing cutter".
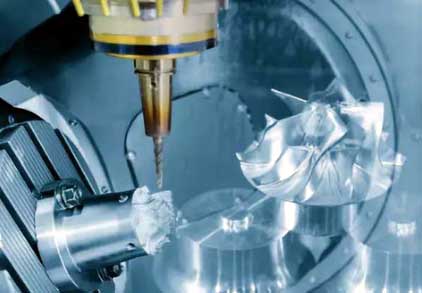
3. Influence on tool wear
The vertical milling component of the down-milling presses the workpiece against the table. The knife teeth and the machined surface slide and the friction phenomenon is small, which is beneficial for reducing the tooth wear, reducing the work hardening phenomenon and reducing the surface roughness.
In addition, the cutting thickness of the cutter teeth from the maximum to zero. The impact force when cutting the cutter into the workpiece is large, especially when the surface to be processed of the workpiece is a blank or has a hard skin, the cutter will generate a large vibration.
However, when the milling is performed, the distance that the teeth travel on the workpiece is shorter than that of the reverse milling, and the average cutting thickness is large. Therefore, under the same cutting conditions, when using up-cut milling, the tool is prone to wear and consumes more cutting power.
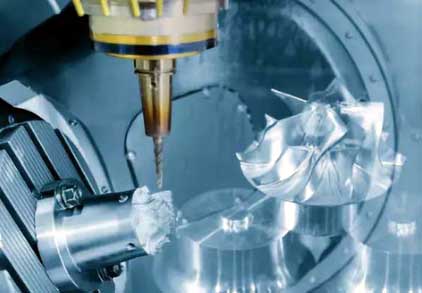
How to choose forward milling and reverse milling?
1, the principle of selection
When using down-cut milling, the machine first needs to have a clearance elimination mechanism to reliably eliminate the gap between the feed screw and the nut of the table to prevent vibration during milling.
The workbench is ideally driven by hydraulics. Secondly, the surface of the workpiece blank is required to have no hard skin, and the process system must have sufficient rigidity. If the above conditions can be met, down-cut milling should be used as much as possible, especially for difficult-to-machine materials. The use of down-cutting reduces cutting distortion and reduces cutting forces and cutting power.
When roughing parts, reverse milling is usually used. In order to prevent "gnawing cutter" during finishing, the way of down milling is usually adopted.
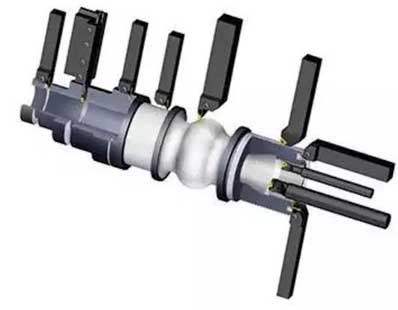
2. Relationship with tool radius compensation
When performing contour milling on CNC machines, tool radius compensation is often used for programming and machining. The tool radius compensation is further divided into tool radius left compensation and tool radius right compensation.
The method for judging the tool radius left compensation is:
The tool is turning forward (clockwise) and the tool is located to the left of the machined profile as it looks in the forward direction of the tool. On the contrary, the tool is located to the right of the machining contour. This compensation method is called tool radius right compensation.
Therefore, whether it is the inner contour or the outer contour machining, the machining method using the tool radius left compensation programming milling is the down milling. The machining method using the tool radius right compensation programming milling is the up-cut milling.
When using a disc milling cutter to machine a plane profile, when the cutting width of the tool is greater than 50% of the tool diameter, the cutting process has both down-cut milling and reverse milling.
3. Selection of forward milling and reverse milling for NC milling machine
CNC machine tools generally have anti-backlash function, the backlash of the transmission mechanism is small, and CNC machine tools mostly perform part finishing. Therefore, CNC milling usually adopts the processing method of the down-cut milling, that is, the tool radius is compensated by the left compensation for programming and machining.
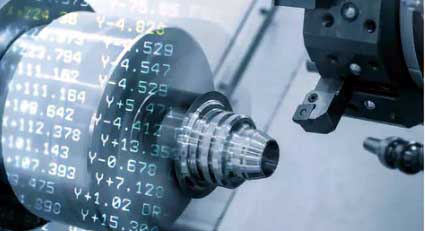