Machining Accuracy and Surface Quality Control Method of Aluminum Alloy Thin-walled Cavity Parts
1. The main factor affecting the machining accuracy and surface quality of aluminum alloy thin-walled cavity parts is that they are easily deformed during processing. Solve the deformation problem of aluminum alloy thin-walled cavity parts during processing. It can improve the working efficiency of milling of such parts, improve the precision and quality of parts, and realize the rapid production of products.
2. Reasons for deformation of thin-walled parts. Need to analyze the processing of aluminum alloy thin-walled cavity parts. It is necessary to analyze the processing process of thin-walled aluminum alloy cavity parts, which are generally made of aluminum alloy sheet as a whole. This kind of parts have large metal removal and low rigidity, and will be deformed due to residual stress, clamping force and cutting motion in the process of processing.
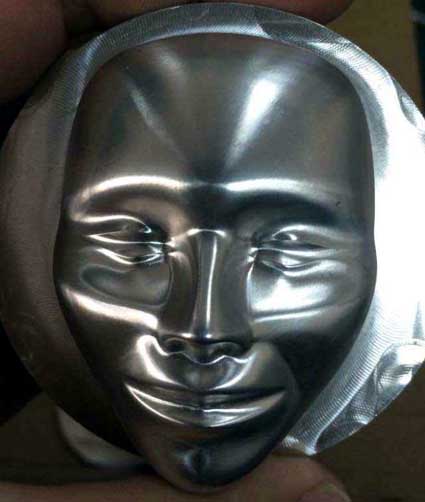
(1), Residual Stress:
In the process of forming metal materials, the arrangement of metal crystals is not the neat arrangement of ideal state. The size and shape of crystals are different, and there are original residual stresses, which release slowly with time and produce certain deformation.
In addition, during the metal cutting process. The plastic deformation of the cutting and the frictional heat between the tool and the workpiece make the temperature difference between the processed surface and the inner layer large, generate large thermal stress, and form thermal stress plastic deformation.
The deformation produced during metal cutting is not caused by a single cause, but is often the result of a combination of several causes. Moreover, this combination effect is not invariable in the process of processing. With the continuous change of processing, it is difficult to judge which cause has the greatest impact on the deformation. We can only start with the causes of deformation and adopt the same technological methods to minimize the processing deformation.
(2), Clamping force:
Due to the relatively thin wall of the thin-walled cavity parts of the aluminum alloy, whether the vise clamp or the chuck clamp is used, the lateral or radial clamping force is generated, and the clamping deformation is inevitable. The degree of deformation of the clamping is related to the size of the clamping force. If the clamping force is large, an irreversible plastic deformation will be formed; If it is small, it will form elastic deformation, and the elastic deformation will recover after the parts are unloaded. However, the cutting process is performed when the elastic deformation is not restored, and the recovery of the single elastic deformation brings new deformation to the processed part.
(3), Cutting motion:
The cutting process is the process by which the tool interacts with the workpiece, which causes the tool to remove some of the material from the workpiece. The cutting motion causes the extrusion, stretching and breaking of the crystal particles of the material. These phenomena cause displacement between atoms of the crystal, resulting in irreversible plastic deformation.
3. Control and reduce the processing method of aluminum alloy thin-wall cavity parts processing deformation. Analyze the causes of deformation of aluminum alloy thin-walled cavity parts during processing, combined with daily processing and production experience. We start from four aspects: process flow, heat treatment, clamping method and cutting, etc. Research and discussion on controlling and reducing the deformation of aluminum alloy thin-walled cavity parts.
Optimize the process flow:
The process can separate coarse and fine machining. After roughing, heat treatment is carried out on the parts, and the cutting stress and residual stress of the parts are fully released, and then finishing is carried out. The processing quality of the parts will be greatly improved. The practice of roughing and finishing separately has the following advantages:
(1) Reduce the influence of residual stress on machining deformation.
After the roughing is completed, the stress generated by the rough machining of the parts can be removed by heat treatment, and the influence of stress on the finishing quality can be reduced.
(2) Improve processing accuracy and surface quality, rough and finish machining are separated. Finishing is only a small allowance, which produces less processing stress and deformation, and can greatly improve the quality of parts.
(3) Improve production efficiency. Since roughing only removes excess material, leaving enough margin for finishing, but considering the size and tolerance, the performance of different types of machine tools can be effectively utilized to improve cutting efficiency.
Heat treatment:
After the parts are machined, the structure of the metal in the table will change greatly, and the influence of cutting motion will produce large residual stress. In order to reduce the deformation of the part, it is necessary to fully release the residual stress of the material. Aluminum alloy thin-walled cavity parts are generally treated by low-temperature annealing.
Improve the clamping method:
In the processing of ordinary parts, the clamping method is usually clamped with a bench vice. For round parts, chuck clamping can also be used. Whether clamping with Bench Vise or chuck, clamping stress will be produced to varying degrees. The clamping stress and the elastic recovery after the part is removed will cause some deformation of the part. In the roughing stage, because only the remaining material is removed, a bench vise can be used.
High-speed machining:
High efficiency, high precision and high coding quality, low cutting temperature and low cutting force. High efficiency, high precision and high coding quality, low cutting temperature and low cutting force. In the process of cutting, the main factors affecting the surface quality of the workpiece are chips, phosphorus burrs, vibration, grinding quality of the cutting edge, defects of the workpiece material and the use of cutting fluid. Compared with conventional cutting, high-speed cutting has the advantages of deep cutting, fast material deformation and high strain rate, and is not easy to produce chip nodules and phosphorus thorns.
2. Reasons for deformation of thin-walled parts. Need to analyze the processing of aluminum alloy thin-walled cavity parts. It is necessary to analyze the processing process of thin-walled aluminum alloy cavity parts, which are generally made of aluminum alloy sheet as a whole. This kind of parts have large metal removal and low rigidity, and will be deformed due to residual stress, clamping force and cutting motion in the process of processing.
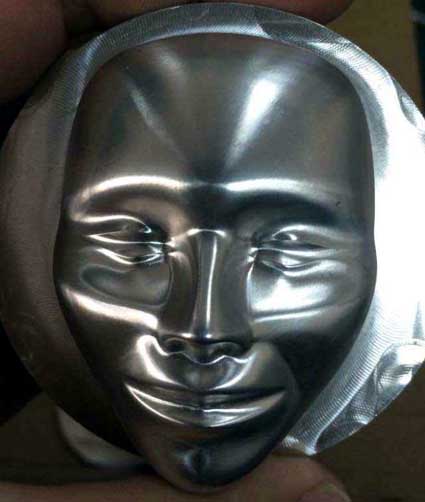
(1), Residual Stress:
In the process of forming metal materials, the arrangement of metal crystals is not the neat arrangement of ideal state. The size and shape of crystals are different, and there are original residual stresses, which release slowly with time and produce certain deformation.
In addition, during the metal cutting process. The plastic deformation of the cutting and the frictional heat between the tool and the workpiece make the temperature difference between the processed surface and the inner layer large, generate large thermal stress, and form thermal stress plastic deformation.
The deformation produced during metal cutting is not caused by a single cause, but is often the result of a combination of several causes. Moreover, this combination effect is not invariable in the process of processing. With the continuous change of processing, it is difficult to judge which cause has the greatest impact on the deformation. We can only start with the causes of deformation and adopt the same technological methods to minimize the processing deformation.
(2), Clamping force:
Due to the relatively thin wall of the thin-walled cavity parts of the aluminum alloy, whether the vise clamp or the chuck clamp is used, the lateral or radial clamping force is generated, and the clamping deformation is inevitable. The degree of deformation of the clamping is related to the size of the clamping force. If the clamping force is large, an irreversible plastic deformation will be formed; If it is small, it will form elastic deformation, and the elastic deformation will recover after the parts are unloaded. However, the cutting process is performed when the elastic deformation is not restored, and the recovery of the single elastic deformation brings new deformation to the processed part.
(3), Cutting motion:
The cutting process is the process by which the tool interacts with the workpiece, which causes the tool to remove some of the material from the workpiece. The cutting motion causes the extrusion, stretching and breaking of the crystal particles of the material. These phenomena cause displacement between atoms of the crystal, resulting in irreversible plastic deformation.
3. Control and reduce the processing method of aluminum alloy thin-wall cavity parts processing deformation. Analyze the causes of deformation of aluminum alloy thin-walled cavity parts during processing, combined with daily processing and production experience. We start from four aspects: process flow, heat treatment, clamping method and cutting, etc. Research and discussion on controlling and reducing the deformation of aluminum alloy thin-walled cavity parts.
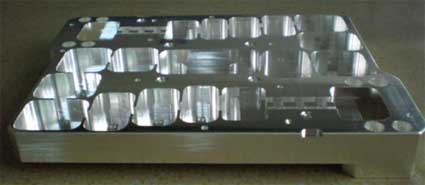
Optimize the process flow:
The process can separate coarse and fine machining. After roughing, heat treatment is carried out on the parts, and the cutting stress and residual stress of the parts are fully released, and then finishing is carried out. The processing quality of the parts will be greatly improved. The practice of roughing and finishing separately has the following advantages:
(1) Reduce the influence of residual stress on machining deformation.
After the roughing is completed, the stress generated by the rough machining of the parts can be removed by heat treatment, and the influence of stress on the finishing quality can be reduced.
(2) Improve processing accuracy and surface quality, rough and finish machining are separated. Finishing is only a small allowance, which produces less processing stress and deformation, and can greatly improve the quality of parts.
(3) Improve production efficiency. Since roughing only removes excess material, leaving enough margin for finishing, but considering the size and tolerance, the performance of different types of machine tools can be effectively utilized to improve cutting efficiency.
Heat treatment:
After the parts are machined, the structure of the metal in the table will change greatly, and the influence of cutting motion will produce large residual stress. In order to reduce the deformation of the part, it is necessary to fully release the residual stress of the material. Aluminum alloy thin-walled cavity parts are generally treated by low-temperature annealing.
Improve the clamping method:
In the processing of ordinary parts, the clamping method is usually clamped with a bench vice. For round parts, chuck clamping can also be used. Whether clamping with Bench Vise or chuck, clamping stress will be produced to varying degrees. The clamping stress and the elastic recovery after the part is removed will cause some deformation of the part. In the roughing stage, because only the remaining material is removed, a bench vise can be used.
High-speed machining:
High efficiency, high precision and high coding quality, low cutting temperature and low cutting force. High efficiency, high precision and high coding quality, low cutting temperature and low cutting force. In the process of cutting, the main factors affecting the surface quality of the workpiece are chips, phosphorus burrs, vibration, grinding quality of the cutting edge, defects of the workpiece material and the use of cutting fluid. Compared with conventional cutting, high-speed cutting has the advantages of deep cutting, fast material deformation and high strain rate, and is not easy to produce chip nodules and phosphorus thorns.
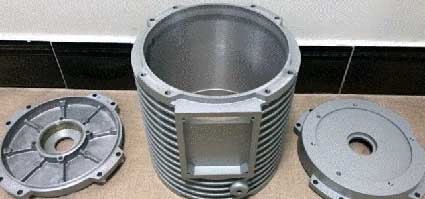