5 New Technologies for CNC Machining of Engine Metal Parts
Engine is the heart of automobile. 4C parts, such as cylinder block, cylinder head, crankshaft, are the core components. Their quality directly affects the performance of the engine. In the manufacture of 4C parts, the problems of chip accumulation in the chamber, processing deformation and the cost of post-processing of cutting fluid have always been the most difficult problems in the manufacture of key parts of engines. It restricts the improvement of product delivery quality and the reduction of product manufacturing cost. Through project practice, we have studied and applied new technologies such as grinding technology, flexible cleaning technology, simulated cylinder head technology, MQL technology and cluster layout, which have effectively solved the above problems.
Inverted Grinding Technology:
That is, the grinding wheel spindle is perpendicular to the bottom surface, the workpiece is placed vertically in the machine tool, and the two grinding wheel spindles drive two CBN grinding wheels to perform vertical grinding from both sides of the workpiece. The technical principle is shown in Fig. 1.
The inverted grinding technology has the following three advantages in processing camshaft:
1. The workpiece is in a vertical state during machining. The gravity of the workpiece hindering the machining in the horizontal machining is converted into a useful top tightening force, which avoids the deformation of the product caused by the gravity of the workpiece and improves the guaranteeing ability of the camshaft grinding precision.
2. The spindle of double grinding is symmetrically distributed along the axis of the workpiece. In the double grinding spindle method, the radial force of the workpiece is balanced by counteracting the directional force, and the normal grinding force is balanced by the center frame, thus realizing the force balance of the camshaft during grinding. It solves the product deformation caused by the grinding force in camshaft machining.
3. CBN efficient grinding technology doubles efficiency. The high-strength, long-life CBN grinding wheel is used in the grinding, and the two CBN grinding wheels work simultaneously during grinding, which greatly improves the grinding efficiency.
Flexible cleaning process
The flexible cleaning process expands the application range of the machining center and innovatively achieves the perfect combination of high pressure cleaning and machining. The process makes full use of the flexibility of the machining center and the high pressure characteristics of the internal cooling system of the machining center. By optimizing the structure of the inner cooling hole of the tool in the machining center, the high-pressure internal cooling cutting fluid for cooling the spindle and the tool is sprayed from the spindle of the machine tool. High-pressure internal cold water of up to 5MPa is impacted to the processing part, which plays a good auxiliary chip breaking effect; After processing, a special tool is used for fixed-point high-pressure cleaning, and high-pressure deburring is performed again; With the help of the linkage characteristics of the machining center, flexible cleaning is carried out for the parts that can not be effectively cleaned by the cleaning machine.
The outstanding advantages of the flexible cleaning process of the machine tool are mainly four points:
1. The cleaning pressure is high.
The jet force of the pressure wash is proportional to the nozzle outlet pressure. The internal cold pressure of the machine tool is 5 MPa and that of the traditional pressure cleaner is 1.5 MPa. Under the same other conditions, the water jet force of the cold hole in the tool is 2.12 times larger than that of the washing machine. Cleaning the chips with the water flow in the cold holes in the machine tool will improve the cleaning quality.
2. Good orientation.
The diameter of the cold hole in the tool is Φ1.5mm, and the hole diameter is small, which is beneficial to improve the cleaning rate and the orientation of the water column, and is not easy to scatter.
3. High flexibility.
Machining center can realize 5-axis linkage, can achieve multi-angle, no dead-angle cleaning, can effectively solve the problem of special-shaped surface debris.
4. Low cost.
The cleaning and processing time are coincident, which greatly improves the equipment utilization.
Simulated cylinder head technology
In the engine assembly, after the completion of the assembly of the cylinder block and the cylinder head, the cylinder bore is subjected to the pressing force from the cylinder head, causing deformation, causing an increase in friction between the cylinder bore and the piston, affecting the performance and life of the engine. Before the cylinder is finished, the cylinder hole can be finished and super-finished after the hardened simulated cylinder head is assembled, which can reduce the deformation of the cylinder bore after the assembly of the whole machine. This technique of assembling the simulated cylinder head is the analog cylinder head technology. The cylinder assembly is simulated after the cylinder head is finished, and the deformation caused by the assembly of the cylinder block and the cylinder head is considered in advance, and the quality of the assembled product is effectively ensured. The deformation data analysis of assembling the simulated cylinder head and the product cylinder head is shown in Table 1 and Table 2.
Through the analysis and comparison of the deformation after assembling the real cylinder head and the simulated cylinder head. It can be found that the deformation trend after assembling the simulated cylinder head is the same as that when assembling the real cylinder head, and the difference of deformation is small. Simulated cylinder head can be used instead of real cylinder head for cylinder hole finishing and superfinishing.
In the case of assembling the simulated cylinder head, the cylinder bore is machined to the required parameter requirements for product performance, and the cylinder bore is deformed after the simulated cylinder head is removed. However, after the assembly line is assembled with the actual cylinder head, the cylinder hole is restored to the stress state when the cylinder head is tightened, thereby ensuring the accuracy after assembly.
MQL technology
MQL technology, namely gas-liquid mixed micro-lubrication technology, is a new type of cutting lubrication technology. The proper amount of MQL oil is mixed with compressed air and sprayed into the processing surface through the cold hole in the tool to cool, lubricate and clean the chips. At present, this technology has been fully applied in the field of crankshaft processing, and it has been verified and applied in the processing of cylinder and cylinder head.
As a green quasi-dry processing technology, MQL technology has the following three advantages:
1. There is no need to replace MQL oil during processing, only need to be added regularly, no waste water is discharged, and the oil mist is discharged directly after purification by equipment, effectively avoiding environmental pollution caused by industrial production.
2. Improve tool cutting conditions, suppress and reduce the cutting heat generated during machining, and improve tool life.
3. A small amount of MQL oil replaces the cutting fluid, reducing the consumption of excipients and the post-processing cost of the cutting fluid.
Inverted Grinding Technology:
That is, the grinding wheel spindle is perpendicular to the bottom surface, the workpiece is placed vertically in the machine tool, and the two grinding wheel spindles drive two CBN grinding wheels to perform vertical grinding from both sides of the workpiece. The technical principle is shown in Fig. 1.
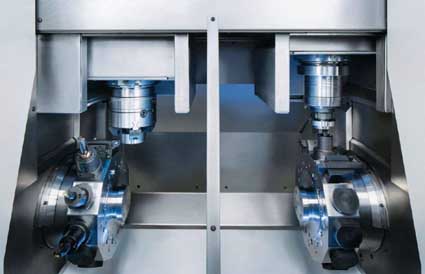
1. The workpiece is in a vertical state during machining. The gravity of the workpiece hindering the machining in the horizontal machining is converted into a useful top tightening force, which avoids the deformation of the product caused by the gravity of the workpiece and improves the guaranteeing ability of the camshaft grinding precision.
2. The spindle of double grinding is symmetrically distributed along the axis of the workpiece. In the double grinding spindle method, the radial force of the workpiece is balanced by counteracting the directional force, and the normal grinding force is balanced by the center frame, thus realizing the force balance of the camshaft during grinding. It solves the product deformation caused by the grinding force in camshaft machining.
3. CBN efficient grinding technology doubles efficiency. The high-strength, long-life CBN grinding wheel is used in the grinding, and the two CBN grinding wheels work simultaneously during grinding, which greatly improves the grinding efficiency.
Flexible cleaning process
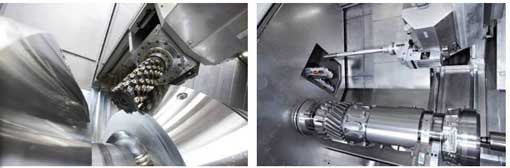
The outstanding advantages of the flexible cleaning process of the machine tool are mainly four points:
1. The cleaning pressure is high.
The jet force of the pressure wash is proportional to the nozzle outlet pressure. The internal cold pressure of the machine tool is 5 MPa and that of the traditional pressure cleaner is 1.5 MPa. Under the same other conditions, the water jet force of the cold hole in the tool is 2.12 times larger than that of the washing machine. Cleaning the chips with the water flow in the cold holes in the machine tool will improve the cleaning quality.
2. Good orientation.
The diameter of the cold hole in the tool is Φ1.5mm, and the hole diameter is small, which is beneficial to improve the cleaning rate and the orientation of the water column, and is not easy to scatter.
3. High flexibility.
Machining center can realize 5-axis linkage, can achieve multi-angle, no dead-angle cleaning, can effectively solve the problem of special-shaped surface debris.
4. Low cost.
The cleaning and processing time are coincident, which greatly improves the equipment utilization.
Simulated cylinder head technology
In the engine assembly, after the completion of the assembly of the cylinder block and the cylinder head, the cylinder bore is subjected to the pressing force from the cylinder head, causing deformation, causing an increase in friction between the cylinder bore and the piston, affecting the performance and life of the engine. Before the cylinder is finished, the cylinder hole can be finished and super-finished after the hardened simulated cylinder head is assembled, which can reduce the deformation of the cylinder bore after the assembly of the whole machine. This technique of assembling the simulated cylinder head is the analog cylinder head technology. The cylinder assembly is simulated after the cylinder head is finished, and the deformation caused by the assembly of the cylinder block and the cylinder head is considered in advance, and the quality of the assembled product is effectively ensured. The deformation data analysis of assembling the simulated cylinder head and the product cylinder head is shown in Table 1 and Table 2.
Through the analysis and comparison of the deformation after assembling the real cylinder head and the simulated cylinder head. It can be found that the deformation trend after assembling the simulated cylinder head is the same as that when assembling the real cylinder head, and the difference of deformation is small. Simulated cylinder head can be used instead of real cylinder head for cylinder hole finishing and superfinishing.
In the case of assembling the simulated cylinder head, the cylinder bore is machined to the required parameter requirements for product performance, and the cylinder bore is deformed after the simulated cylinder head is removed. However, after the assembly line is assembled with the actual cylinder head, the cylinder hole is restored to the stress state when the cylinder head is tightened, thereby ensuring the accuracy after assembly.
MQL technology
MQL technology, namely gas-liquid mixed micro-lubrication technology, is a new type of cutting lubrication technology. The proper amount of MQL oil is mixed with compressed air and sprayed into the processing surface through the cold hole in the tool to cool, lubricate and clean the chips. At present, this technology has been fully applied in the field of crankshaft processing, and it has been verified and applied in the processing of cylinder and cylinder head.
As a green quasi-dry processing technology, MQL technology has the following three advantages:
1. There is no need to replace MQL oil during processing, only need to be added regularly, no waste water is discharged, and the oil mist is discharged directly after purification by equipment, effectively avoiding environmental pollution caused by industrial production.
2. Improve tool cutting conditions, suppress and reduce the cutting heat generated during machining, and improve tool life.
3. A small amount of MQL oil replaces the cutting fluid, reducing the consumption of excipients and the post-processing cost of the cutting fluid.