Mechanical processing explanation - WEDM processing technology
WEDM processing objects: Ordinary metals, high hardness alloy materials, synthetic diamonds, semiconductor materials, conductive ceramics, ferrite materials, and the like.
WEDM processing range: In addition to general precision machining. It can process large size and thick workpieces, and begin to involve the field of precision micro-processing.
Wire EDM machining shape: Wire cutting is not only suitable for the machining of two-dimensional contours, but also for processing various taper, variable taper and three-dimensional and suitable curved surfaces with different shapes.
1, the basic principle
The basic principle of EDM is also processed by the electrical corrosion phenomenon caused by the pulse discharge of the tool electrode on the workpiece. However, wire EDM does not require the fabrication of shaped electrodes. Instead, a moving wire (molybdenum wire or copper wire) is used as an electrode, and the workpieces of various shapes are cut by the relative movement of the wire and the workpiece in the horizontal plane. If the wire is regularly tilted relative to the workpiece, the tapered workpiece can also be cut. The workpiece is connected to the positive pole of the pulse power supply, and the electrode wire is connected to the negative pole.
2, the characteristics of EDM cutting processing
EDM wire electric discharge having a commonality, and used to hard machining hardened steel and alloys. Most of the current wire cutting machines use digital program control technology features:
advantage:
It is suitable for the processing of materials that are difficult to machine by mechanical processing methods, such as hardened steel, hard alloy, and heat resistant alloy.
The metal wire is used as the tool electrode, which saves the electrode design and manufacturing cost and time, can easily process the shape and the through hole with complicated shape, and can carry out the nesting processing.
The gap between concave and convex in punching can be adjusted arbitrarily.
Disadvantages:
The material to be processed must be electrically conductive
Cannot process blind holes
Traditional processing is impossible to obtain a right angle
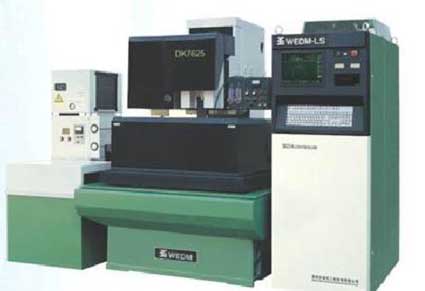
EDM is easy to get right angles
1. No need to make electrodes compared with EDM; (production preparation time is short)
2. The wire moves along the length direction, with less loss during processing and high machining accuracy. (The molybdenum wire for fast wire can be reused)
3. It can process precise, complex and small inner and outer surfaces, as well as materials with high melting point and high hardness. (only conductive materials can be processed)
4. High processing efficiency, high material utilization rate and low cost.
5. High degree of automation and easy operation.
6. Busbar can not be machined on surfaces and blind holes that are not straight lines.
3, the wire EDM process
The positive pole of the pulse power supply is connected to the workpiece, and the negative pole is connected to the electrode wire. The wire reciprocates at a rate that continuously enters and exits the discharge zone. A quantity of liquid medium is injected between the wire and the workpiece. The stepping motor has a relative movement of the table and the workpiece in the horizontal plane, and a pulse discharge occurs between the wire and the workpiece. By controlling the relative motion trajectory and feed speed between the wire and the workpiece, it is possible to cut a workpiece having a certain shape and size.
4. Wire EDM machine tool
According to the wire speed of the wire, it is divided into a fast wire cutting machine and a slow wire cutting machine.
(1) High-speed wire cutting machine
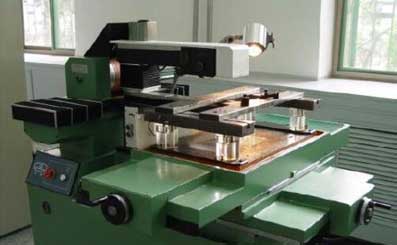
The electrode wire of this kind of machine tool makes high-speed reciprocating motion, and the wire running speed is generally 8~10m/s.
The commonly used electrode wire is molybdenum wire, and the working fluid is an emulsion.
Good economy, but the stability of the wire is poor, the processing accuracy is relatively low, and the surface is rough.
The processing precision that can be achieved at present is ± 0.01mm, surface roughness Ra=3.2~0.8μm
(2) Low speed wire cutting machine
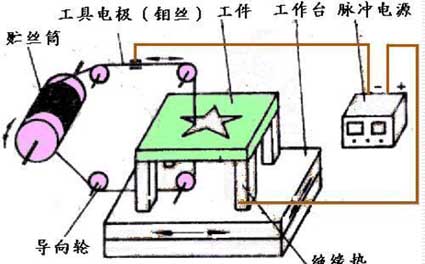
The wire of this type of machine tool is used for low-speed one-way movement, and the wire speed is generally less than 0.2m/s. The commonly used electrode wire is copper wire, which is generally disposable, and the processing liquid is deionized water.
The wire has good stability, high processing precision and good surface quality, but the cost is high.
The processing precision can reach 0.001mm, and the surface roughness Ra<0.4μm.
WEDM processing range: In addition to general precision machining. It can process large size and thick workpieces, and begin to involve the field of precision micro-processing.
Wire EDM machining shape: Wire cutting is not only suitable for the machining of two-dimensional contours, but also for processing various taper, variable taper and three-dimensional and suitable curved surfaces with different shapes.

1, the basic principle
The basic principle of EDM is also processed by the electrical corrosion phenomenon caused by the pulse discharge of the tool electrode on the workpiece. However, wire EDM does not require the fabrication of shaped electrodes. Instead, a moving wire (molybdenum wire or copper wire) is used as an electrode, and the workpieces of various shapes are cut by the relative movement of the wire and the workpiece in the horizontal plane. If the wire is regularly tilted relative to the workpiece, the tapered workpiece can also be cut. The workpiece is connected to the positive pole of the pulse power supply, and the electrode wire is connected to the negative pole.
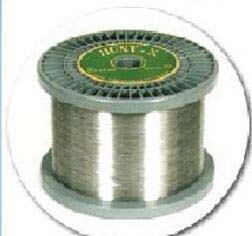
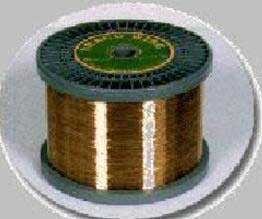
2, the characteristics of EDM cutting processing
EDM wire electric discharge having a commonality, and used to hard machining hardened steel and alloys. Most of the current wire cutting machines use digital program control technology features:
advantage:
It is suitable for the processing of materials that are difficult to machine by mechanical processing methods, such as hardened steel, hard alloy, and heat resistant alloy.
The metal wire is used as the tool electrode, which saves the electrode design and manufacturing cost and time, can easily process the shape and the through hole with complicated shape, and can carry out the nesting processing.
The gap between concave and convex in punching can be adjusted arbitrarily.
Disadvantages:
The material to be processed must be electrically conductive
Cannot process blind holes
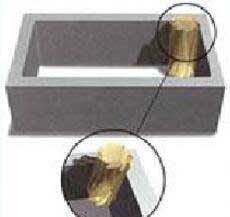
Traditional processing is impossible to obtain a right angle
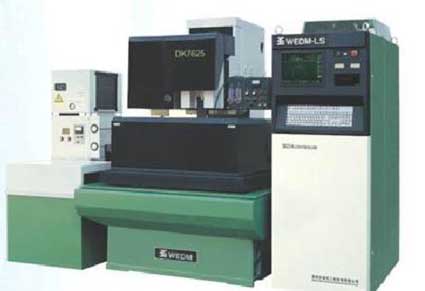
EDM is easy to get right angles
1. No need to make electrodes compared with EDM; (production preparation time is short)
2. The wire moves along the length direction, with less loss during processing and high machining accuracy. (The molybdenum wire for fast wire can be reused)
3. It can process precise, complex and small inner and outer surfaces, as well as materials with high melting point and high hardness. (only conductive materials can be processed)
4. High processing efficiency, high material utilization rate and low cost.
5. High degree of automation and easy operation.
6. Busbar can not be machined on surfaces and blind holes that are not straight lines.
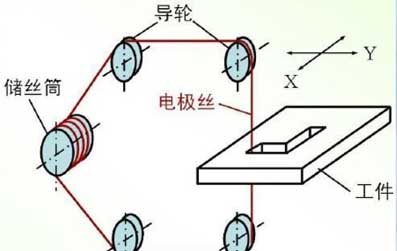
3, the wire EDM process
The positive pole of the pulse power supply is connected to the workpiece, and the negative pole is connected to the electrode wire. The wire reciprocates at a rate that continuously enters and exits the discharge zone. A quantity of liquid medium is injected between the wire and the workpiece. The stepping motor has a relative movement of the table and the workpiece in the horizontal plane, and a pulse discharge occurs between the wire and the workpiece. By controlling the relative motion trajectory and feed speed between the wire and the workpiece, it is possible to cut a workpiece having a certain shape and size.
4. Wire EDM machine tool
According to the wire speed of the wire, it is divided into a fast wire cutting machine and a slow wire cutting machine.
(1) High-speed wire cutting machine
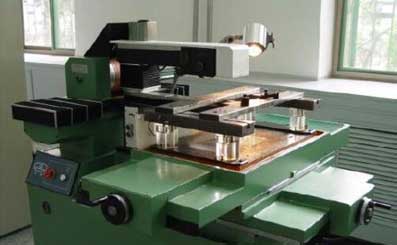
The electrode wire of this kind of machine tool makes high-speed reciprocating motion, and the wire running speed is generally 8~10m/s.
The commonly used electrode wire is molybdenum wire, and the working fluid is an emulsion.
Good economy, but the stability of the wire is poor, the processing accuracy is relatively low, and the surface is rough.
The processing precision that can be achieved at present is ± 0.01mm, surface roughness Ra=3.2~0.8μm
(2) Low speed wire cutting machine
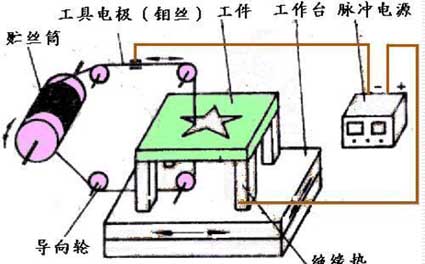
The wire of this type of machine tool is used for low-speed one-way movement, and the wire speed is generally less than 0.2m/s. The commonly used electrode wire is copper wire, which is generally disposable, and the processing liquid is deionized water.
The wire has good stability, high processing precision and good surface quality, but the cost is high.
The processing precision can reach 0.001mm, and the surface roughness Ra<0.4μm.