Eliminate milling hole deformed bell phenomenon
During the machining process of engine and transmission parts, current process control measures cannot meet the hole machining requirements. The cause of failure is often caused by some failure modes of the machined hole. The distortion of the bell mouth during processing is a failure mode of the hole.
I. Hole bell category
To judge whether the bell hole is in the processing hole and whether the hole is invalid, first understand the several types of the bell mouth. According to the size of the big end and the small end of the bell mouth, the bell mouth of the hole has the following four combinations:
The large diameter and the small diameter of the bell mouth are in the allowable range of the processing aperture;
The large diameter and small diameter of the bell mouth hole exceed the allowable value range of the processing aperture;
The large diameter of the bell mouth exceeds the allowable value range of the processing aperture;
The diameter of the bell mouth is outside the allowable range of the machining aperture.
II. The consequences of failure bell hole
The processing hole has a bell mouth, and the taper is not allowed, which is a relatively difficult scale. In actual production, the difference between the front and rear aperture data of the bell mouth is allowed, and the number is not allowed. At present, there is no more authoritative standard to follow. There is no shape element in the existing shape tolerance, but some machining holes have cylindricity requirements. At this time, if the hole is machined, we can use the cylindricity requirement to refer to whether it is allowed: The shape of the bell mouth directly affects the actual value of the cylindricity. Once the value of the bell mouth exceeds the allowable value of the cylindricity, the workpiece has become a waste product (cylindricity is out of tolerance). This is just a special case of judging whether or not the bell mouth is allowed in the machining hole. In the actual processing process, many of the bell mouth holes are still judged without reference, but the consequences of failure are definitely present.
1. Failure consequences on processing cooperation
The different mating characteristics of the hole and the shaft determine the failure effect of the bell mouth. Interference fit, clearance fit and transition fit. During the three mating processes, some different failure consequences will occur due to the taper of the hole of the hole.
Clearance fit: The consequence of the failure is that the matching effect between the movements is deteriorated, and the fatigue damage of the moving parts is accelerated. If the piston ring moves up and down in the cylinder hole with the bell mouth, the diameter of the piston ring always changes up and down, and the continuous diameter change causes the piston ring to suffer fatigue damage prematurely; Second, the degree of wear of the moving parts is different. If the valve guide rod moves up and down in the conduit hole, because the matching hole of the guide rod - the conduit hole is the bell mouth hole, the diameter of the guide rod is prematurely worn at the small diameter of the bell mouth. However, the diameter of the guide rod at the large diameter is not obviously worn, so that the diameter above the length of the entire guide rod is not balanced, and finally the swing amplitude of the moving member is increased, wh
Interference fit: The imbalance of the overall fit and the amount of interference caused a balanced state of interference, which becomes a local trend of change in the imbalance of interference; It affects the retention balance of the glue adhesive after the capping assembly.
Transition coordination: Some approximation failure consequences between the two appear.
2. Potential failure consequences in the process
The flared hole appears in the machined hole, which is not only the failure effect of the flared hole, but also the flared hole in the semi-finished hole will affect the subsequent machining hole. When the final finishing is difficult to eliminate the flare phenomenon generated in the front, the final machining hole may still have a flare defect.
three, Reason for the formation of the bell mouth
There are many reasons for the flare of the machined hole, such as process, tool, equipment, blank and coolant.
1, the process
The process causes the flared holes in the machined holes. If the previous process does not eliminate the bell mouth, it affects the final processing; The radial clearance of the pilot hole/drill sleeve and the cutter is too large to cause a flare; The cutting parameters are unreasonable, and the resulting cutting heat changes greatly, resulting in the degree of heat of the processing hole wall is different, causing the bell mouth to appear. Therefore, if the process does not take into account the degree of influence of the previous step on the next step, there is often a risk of potential failure.
2, the tool
The rigidity of the arbor is poor; The tool diameter itself has a straight cone; The clamping accuracy of the tool is reduced; The cutting edge of the tool is large; The tool installation center line does not coincide or vibrate; The cutter bar of the tool is bent; The cutting angle of the tool is unreasonable, etc. These defects may be the reason why the machining hole has a bell mouth.
When the tool has some single failure reasons, it will cause the machining hole to have a bell mouth. This is a relatively simple statement. "The poor rigidity of the shank" will cause the horn to appear in the machined hole. In fact, this also needs to be formed under certain conditions. When the mast is less rigid, the centrifugal force of the head of the mast is larger during high-speed rotation, and the amount of swing of the head of the shank occurs (see Figure 1). When there is a processing blade on the mast, the blade may be in some positions to process the flare due to the different positions of the blade on the circumference of the mast. In some locations, processing does not necessarily result in a flare.
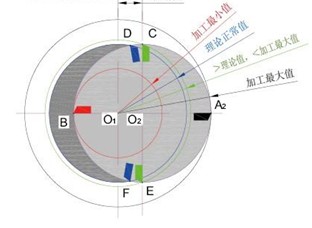
figure 1 The amount of swing in the head of the knife
We analyze the “barrier rigidity difference”. When some important holes are machined, when there are high requirements such as position, roundness and straightness, one way is to use auxiliary support. That is, the drill sleeve/guide hole is used to assist the machining when machining the entire hole; Another method of machining is that there is no drill sleeve and there is no guide hole, and the tool directly processes the hole. The above two methods are used to machine the hole. If the amount of the swing is present, the bell mouth may appear in different forms. The hole is machined under the drill sleeve/guide hole, and if the bell mouth is present, the bell mouth is generally inverted; If the tool directly processes the hole, the flare that appears is generally a horn.
Under the premise that the rigidity of the shank is poor, we use the shank with the guide bar to analyze the reason why the machining hole has the horn and the inverted bell.
The horn of the hole is formed: When the amount of swing of the arbor is present, it is processed without the auxiliary support of the drill sleeve/guide hole. If the one-tooth blade is in the arc DA2F area of Fig. 1, the cutter head during machining makes the tool amount smaller than the swing amount of the tool bar. That is, the amount of swing of the arbor under no load may be the slewing size of the initial machining orifice with the largest machining hole. As the mast continues to deepen the machining hole, the amount of swing of the arbor is constrained by the wall of the machined hole, which directly causes the oscillating amount of the shank to gradually decrease. This trend eventually caused the machining holes to appear in the bell.
The inverted bell mouth of the hole is formed: When the machined hole is carried out with the auxiliary support of the drill sleeve/guide hole, the tool bar has a certain amount of swing in high-speed rotation due to the difference in rigidity (see Fig. 2). After entering the drill sleeve/guide hole, the swing amount is limited by the drill sleeve hole wall/guide hole hole wall (ie, the cutter bar swing amount is reduced), and the gap between the cutter bar and the hole wall is unilaterally eliminated due to the existence of the swing amount. (See Figure 3). At this time, the head of the arbor is biased to one side, and the mounting root of the tool on the shank and the wall of the machined hole have an inclination angle with the axis of the spindle. The tool is deep into the hole wall with the tilting amplitude of the tool until the hole diameter of the machined hole reaches the maximum swing amount of the tool bar (see Figure 4); If the machining hole still needs to be processed at this time, the machining hole diameter is always performed under the maximum swing amount of the arbor (see Fig. 5). That is, a part is a case where the bell is inverted and a part is a cylindrical hole.
figure 2 The arbor has a certain amount of swing in high-speed rotation
image 3 The stencil strip has a unilateral elimination of the gap in the hole wall
Figure 4 The aperture reaches the maximum swing of the arbor
Figure 5 The machining aperture is performed at the maximum swing amount of the arbor
A cutting edge mast forms a flare in this case, and this is also the case when the multi-toothed mast is poorly rigid. The rigidity of the shank will appear as a flare, and the rigidity of the shank will also appear as a flare. The shrinkage difference caused by the uneven heat of the hole wall caused by the previous process causes the bell mouth to form.
3, equipment
Some failures of the equipment are also one of the reasons why the machining hole has a bell mouth, such as the vibration of the main shaft is intensified; The feeding direction of the tool on the CNC lathe is not parallel to the axis of rotation of the workpiece, and the tip of the tool is not equal to the center of the rotating part; In addition, the failure of the auxiliary member, such as the severe wear of the drill sleeve, causes the centering action of the machining tool to decrease and the amount of the swing to rise.
4, the blank
The hole wall of the machined hole has a large difference (round table shape), and once the tool is passivated, the rebound amount of the hole wall at the end of the process is different to form a bell mouth; The material of the hole wall has a different degree of looseness on the upper and lower sides, which leads to an increase in the amount of rebound of the hole wall during the processing, and forms a bell mouth.
5, cooling fluid
When the heat received by the wall of the hole and the heat generated by the tool are unbalanced during processing, the amount of expansion of the wall of the hole is different. For example, the cooling effect of the coolant on the tool hole and the hole wall when machining the through hole is not good when the blind hole is processed. In this way, once the heat generated by the tool changes greatly during the processing, the hole of the processing hole and the hole of the processing hole are heated differently, which may cause the bell hole to appear in the processing hole.
IV. Method for eliminating the bell mouth phenomenon
For the bell mouth of the machined hole, we need to correct the failure mode and the consequences of the analysis, the cause of the problem, and eliminate the appearance of the bell mouth. Specifically, we can try to solve it from the following aspects.
1, the process
When the machining holes are unreasonable in the process of the front and rear processes, the work steps, the cutting parameters, etc., the bell holes may appear in the machining holes. For example, there is no fixed usage rule for cutting parameters. In actual production, the cutting parameters that were originally used normally cannot meet the processing requirements effectively. The change point is the blank batch of the blank supplier or the blank supplied by the new blank casting supplier, resulting in a flared hole in the machined hole. For example, after the machining of the cylinder pump sleeve of a certain cylinder line, the bell mouth and the tool life are not up to the set requirements. The diameter of the pump sleeve hole is 29.72+0.05mm, and the hole condition is the through hole. The difference between the front and rear diameters of the bell mouth is 0.01~0.02mm, and the service life of the tool is reduced from 1800 pieces to 800 pieces.
Information about the hole: tool, carbide reamer;
Speed: 225r/min;
Feeding speed: 100mm/min;
Feed per tooth: 0.056mm/z;
Tool teeth: 8.
Because it is a special machine line, the spindle speed cannot be adjusted, so we try to solve the bell mouth phenomenon by modifying the feed rate. The modified feed per tooth is increased to 0.10 mm/z. By adjusting the feed per tooth of the reamer, the bell mouth phenomenon is finally eliminated, and the previous tool life is restored, that is, from about 800 pieces to 1800 pieces.
Analysis of the reasons for the above example: Due to the difference in casting blanks, the hardness of the material has increased compared to the previous ones, but it meets the requirements of the drawings. Under such conditions, there is almost no processing of the bell mouth when the reamer is sharp, but as the number of processing increases, the bell mouth becomes more and more obvious. Due to the small feed rate of the tool, in the face of the machining of the hard material edge, the actual grinding process replaces the previous normal cutting process. As a result, the wear of the tool is accelerated and the heat generated during the machining of the tool rises rapidly. Two reasons cause the bell hole phenomenon in the processing hole: the wear in the process of processing the hole and the processing of the hole end changes, resulting in a change in the pressing force on the hole wall during processing; During the processing, the wall of the hole undergoes heat change, and the wall of the hole ends with different shrinkage. Since the degree of heat generated by the machined hole and the hole of the machined hole is different, the amount of shrinkage of the hole wall is also different. When the feed amount of the gear is increased, the actual cutting length of the tool hole is shortened, and the generated heat is also balanced. In this way, the degree of change in the compression of the hole wall and the heat affected by the wall of the hole is reduced, and finally the bell mouth phenomenon of the machined hole is eliminated and the tool life is greatly improved.
2, the tool
The tool is one of the main causes of the flare. Therefore, the knives can be used to eliminate the bell mouth phenomenon of the machined hole, and the medicine can be remedy according to the cause of the failure of the tool, which can be implemented in various aspects:
(1) The rigidity of the mast satisfies: The boring noted when the design strength, select appropriate materials to meet the boring bar in the wobble processing is minimized;
(2) Correct cutting angle: When there is a difference in the rebound amount of the hole wall caused by the unbalanced thickness of the blank wall of the blank, the main deflection angle of 75 to 90 is selected to reduce the radial pressing force of the cutter on the hole wall, and the defect of the bell mouth can be avoided;
(3) Use a reasonable life: The tool edge is set to a reasonable service life value to ensure the sharpness in the cutting process, and to eliminate the hole wall extrusion and heat imbalance defects caused by the tool passivation;
(4) Pay attention to the details of the operation: The operator pays attention to all aspects of the details when adjusting the tool. Such as the guarantee of the clamping accuracy of the tool, the edge of the grinding edge and the control of the situation of the cone.
3, equipment
Do routine maintenance of the equipment, such as periodic vibration testing of the main shaft; Regularly check the auxiliary equipment of the equipment; the positional protection of the front and rear processes.
4, the blank
The difference between the upper and lower margins of the processing hole of the blank is large. For this kind of defect, the blank supplier can increase the thickness of the hole wall as much as possible in accordance with the blank drawing, which can reduce the deformation of the machined hole wall. Under the premise that the blank can not be changed, the machining requirements can be met by changing the tool's lead angle, setting the tool life reasonably or selecting a sharper tool.
5, cooling fluid
I. Hole bell category
To judge whether the bell hole is in the processing hole and whether the hole is invalid, first understand the several types of the bell mouth. According to the size of the big end and the small end of the bell mouth, the bell mouth of the hole has the following four combinations:
The large diameter and the small diameter of the bell mouth are in the allowable range of the processing aperture;
The large diameter and small diameter of the bell mouth hole exceed the allowable value range of the processing aperture;
The large diameter of the bell mouth exceeds the allowable value range of the processing aperture;
The diameter of the bell mouth is outside the allowable range of the machining aperture.
II. The consequences of failure bell hole
The processing hole has a bell mouth, and the taper is not allowed, which is a relatively difficult scale. In actual production, the difference between the front and rear aperture data of the bell mouth is allowed, and the number is not allowed. At present, there is no more authoritative standard to follow. There is no shape element in the existing shape tolerance, but some machining holes have cylindricity requirements. At this time, if the hole is machined, we can use the cylindricity requirement to refer to whether it is allowed: The shape of the bell mouth directly affects the actual value of the cylindricity. Once the value of the bell mouth exceeds the allowable value of the cylindricity, the workpiece has become a waste product (cylindricity is out of tolerance). This is just a special case of judging whether or not the bell mouth is allowed in the machining hole. In the actual processing process, many of the bell mouth holes are still judged without reference, but the consequences of failure are definitely present.
1. Failure consequences on processing cooperation
The different mating characteristics of the hole and the shaft determine the failure effect of the bell mouth. Interference fit, clearance fit and transition fit. During the three mating processes, some different failure consequences will occur due to the taper of the hole of the hole.
Clearance fit: The consequence of the failure is that the matching effect between the movements is deteriorated, and the fatigue damage of the moving parts is accelerated. If the piston ring moves up and down in the cylinder hole with the bell mouth, the diameter of the piston ring always changes up and down, and the continuous diameter change causes the piston ring to suffer fatigue damage prematurely; Second, the degree of wear of the moving parts is different. If the valve guide rod moves up and down in the conduit hole, because the matching hole of the guide rod - the conduit hole is the bell mouth hole, the diameter of the guide rod is prematurely worn at the small diameter of the bell mouth. However, the diameter of the guide rod at the large diameter is not obviously worn, so that the diameter above the length of the entire guide rod is not balanced, and finally the swing amplitude of the moving member is increased, wh
Interference fit: The imbalance of the overall fit and the amount of interference caused a balanced state of interference, which becomes a local trend of change in the imbalance of interference; It affects the retention balance of the glue adhesive after the capping assembly.
Transition coordination: Some approximation failure consequences between the two appear.
2. Potential failure consequences in the process
The flared hole appears in the machined hole, which is not only the failure effect of the flared hole, but also the flared hole in the semi-finished hole will affect the subsequent machining hole. When the final finishing is difficult to eliminate the flare phenomenon generated in the front, the final machining hole may still have a flare defect.
three, Reason for the formation of the bell mouth
There are many reasons for the flare of the machined hole, such as process, tool, equipment, blank and coolant.
1, the process
The process causes the flared holes in the machined holes. If the previous process does not eliminate the bell mouth, it affects the final processing; The radial clearance of the pilot hole/drill sleeve and the cutter is too large to cause a flare; The cutting parameters are unreasonable, and the resulting cutting heat changes greatly, resulting in the degree of heat of the processing hole wall is different, causing the bell mouth to appear. Therefore, if the process does not take into account the degree of influence of the previous step on the next step, there is often a risk of potential failure.
2, the tool
The rigidity of the arbor is poor; The tool diameter itself has a straight cone; The clamping accuracy of the tool is reduced; The cutting edge of the tool is large; The tool installation center line does not coincide or vibrate; The cutter bar of the tool is bent; The cutting angle of the tool is unreasonable, etc. These defects may be the reason why the machining hole has a bell mouth.
When the tool has some single failure reasons, it will cause the machining hole to have a bell mouth. This is a relatively simple statement. "The poor rigidity of the shank" will cause the horn to appear in the machined hole. In fact, this also needs to be formed under certain conditions. When the mast is less rigid, the centrifugal force of the head of the mast is larger during high-speed rotation, and the amount of swing of the head of the shank occurs (see Figure 1). When there is a processing blade on the mast, the blade may be in some positions to process the flare due to the different positions of the blade on the circumference of the mast. In some locations, processing does not necessarily result in a flare.
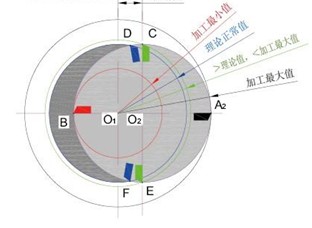
figure 1 The amount of swing in the head of the knife
We analyze the “barrier rigidity difference”. When some important holes are machined, when there are high requirements such as position, roundness and straightness, one way is to use auxiliary support. That is, the drill sleeve/guide hole is used to assist the machining when machining the entire hole; Another method of machining is that there is no drill sleeve and there is no guide hole, and the tool directly processes the hole. The above two methods are used to machine the hole. If the amount of the swing is present, the bell mouth may appear in different forms. The hole is machined under the drill sleeve/guide hole, and if the bell mouth is present, the bell mouth is generally inverted; If the tool directly processes the hole, the flare that appears is generally a horn.
Under the premise that the rigidity of the shank is poor, we use the shank with the guide bar to analyze the reason why the machining hole has the horn and the inverted bell.
The horn of the hole is formed: When the amount of swing of the arbor is present, it is processed without the auxiliary support of the drill sleeve/guide hole. If the one-tooth blade is in the arc DA2F area of Fig. 1, the cutter head during machining makes the tool amount smaller than the swing amount of the tool bar. That is, the amount of swing of the arbor under no load may be the slewing size of the initial machining orifice with the largest machining hole. As the mast continues to deepen the machining hole, the amount of swing of the arbor is constrained by the wall of the machined hole, which directly causes the oscillating amount of the shank to gradually decrease. This trend eventually caused the machining holes to appear in the bell.
The inverted bell mouth of the hole is formed: When the machined hole is carried out with the auxiliary support of the drill sleeve/guide hole, the tool bar has a certain amount of swing in high-speed rotation due to the difference in rigidity (see Fig. 2). After entering the drill sleeve/guide hole, the swing amount is limited by the drill sleeve hole wall/guide hole hole wall (ie, the cutter bar swing amount is reduced), and the gap between the cutter bar and the hole wall is unilaterally eliminated due to the existence of the swing amount. (See Figure 3). At this time, the head of the arbor is biased to one side, and the mounting root of the tool on the shank and the wall of the machined hole have an inclination angle with the axis of the spindle. The tool is deep into the hole wall with the tilting amplitude of the tool until the hole diameter of the machined hole reaches the maximum swing amount of the tool bar (see Figure 4); If the machining hole still needs to be processed at this time, the machining hole diameter is always performed under the maximum swing amount of the arbor (see Fig. 5). That is, a part is a case where the bell is inverted and a part is a cylindrical hole.
figure 2 The arbor has a certain amount of swing in high-speed rotation
image 3 The stencil strip has a unilateral elimination of the gap in the hole wall
Figure 4 The aperture reaches the maximum swing of the arbor
Figure 5 The machining aperture is performed at the maximum swing amount of the arbor
A cutting edge mast forms a flare in this case, and this is also the case when the multi-toothed mast is poorly rigid. The rigidity of the shank will appear as a flare, and the rigidity of the shank will also appear as a flare. The shrinkage difference caused by the uneven heat of the hole wall caused by the previous process causes the bell mouth to form.
3, equipment
Some failures of the equipment are also one of the reasons why the machining hole has a bell mouth, such as the vibration of the main shaft is intensified; The feeding direction of the tool on the CNC lathe is not parallel to the axis of rotation of the workpiece, and the tip of the tool is not equal to the center of the rotating part; In addition, the failure of the auxiliary member, such as the severe wear of the drill sleeve, causes the centering action of the machining tool to decrease and the amount of the swing to rise.
4, the blank
The hole wall of the machined hole has a large difference (round table shape), and once the tool is passivated, the rebound amount of the hole wall at the end of the process is different to form a bell mouth; The material of the hole wall has a different degree of looseness on the upper and lower sides, which leads to an increase in the amount of rebound of the hole wall during the processing, and forms a bell mouth.
5, cooling fluid
When the heat received by the wall of the hole and the heat generated by the tool are unbalanced during processing, the amount of expansion of the wall of the hole is different. For example, the cooling effect of the coolant on the tool hole and the hole wall when machining the through hole is not good when the blind hole is processed. In this way, once the heat generated by the tool changes greatly during the processing, the hole of the processing hole and the hole of the processing hole are heated differently, which may cause the bell hole to appear in the processing hole.
IV. Method for eliminating the bell mouth phenomenon
For the bell mouth of the machined hole, we need to correct the failure mode and the consequences of the analysis, the cause of the problem, and eliminate the appearance of the bell mouth. Specifically, we can try to solve it from the following aspects.
1, the process
When the machining holes are unreasonable in the process of the front and rear processes, the work steps, the cutting parameters, etc., the bell holes may appear in the machining holes. For example, there is no fixed usage rule for cutting parameters. In actual production, the cutting parameters that were originally used normally cannot meet the processing requirements effectively. The change point is the blank batch of the blank supplier or the blank supplied by the new blank casting supplier, resulting in a flared hole in the machined hole. For example, after the machining of the cylinder pump sleeve of a certain cylinder line, the bell mouth and the tool life are not up to the set requirements. The diameter of the pump sleeve hole is 29.72+0.05mm, and the hole condition is the through hole. The difference between the front and rear diameters of the bell mouth is 0.01~0.02mm, and the service life of the tool is reduced from 1800 pieces to 800 pieces.
Information about the hole: tool, carbide reamer;
Speed: 225r/min;
Feeding speed: 100mm/min;
Feed per tooth: 0.056mm/z;
Tool teeth: 8.
Because it is a special machine line, the spindle speed cannot be adjusted, so we try to solve the bell mouth phenomenon by modifying the feed rate. The modified feed per tooth is increased to 0.10 mm/z. By adjusting the feed per tooth of the reamer, the bell mouth phenomenon is finally eliminated, and the previous tool life is restored, that is, from about 800 pieces to 1800 pieces.
Analysis of the reasons for the above example: Due to the difference in casting blanks, the hardness of the material has increased compared to the previous ones, but it meets the requirements of the drawings. Under such conditions, there is almost no processing of the bell mouth when the reamer is sharp, but as the number of processing increases, the bell mouth becomes more and more obvious. Due to the small feed rate of the tool, in the face of the machining of the hard material edge, the actual grinding process replaces the previous normal cutting process. As a result, the wear of the tool is accelerated and the heat generated during the machining of the tool rises rapidly. Two reasons cause the bell hole phenomenon in the processing hole: the wear in the process of processing the hole and the processing of the hole end changes, resulting in a change in the pressing force on the hole wall during processing; During the processing, the wall of the hole undergoes heat change, and the wall of the hole ends with different shrinkage. Since the degree of heat generated by the machined hole and the hole of the machined hole is different, the amount of shrinkage of the hole wall is also different. When the feed amount of the gear is increased, the actual cutting length of the tool hole is shortened, and the generated heat is also balanced. In this way, the degree of change in the compression of the hole wall and the heat affected by the wall of the hole is reduced, and finally the bell mouth phenomenon of the machined hole is eliminated and the tool life is greatly improved.
2, the tool
The tool is one of the main causes of the flare. Therefore, the knives can be used to eliminate the bell mouth phenomenon of the machined hole, and the medicine can be remedy according to the cause of the failure of the tool, which can be implemented in various aspects:
(1) The rigidity of the mast satisfies: The boring noted when the design strength, select appropriate materials to meet the boring bar in the wobble processing is minimized;
(2) Correct cutting angle: When there is a difference in the rebound amount of the hole wall caused by the unbalanced thickness of the blank wall of the blank, the main deflection angle of 75 to 90 is selected to reduce the radial pressing force of the cutter on the hole wall, and the defect of the bell mouth can be avoided;
(3) Use a reasonable life: The tool edge is set to a reasonable service life value to ensure the sharpness in the cutting process, and to eliminate the hole wall extrusion and heat imbalance defects caused by the tool passivation;
(4) Pay attention to the details of the operation: The operator pays attention to all aspects of the details when adjusting the tool. Such as the guarantee of the clamping accuracy of the tool, the edge of the grinding edge and the control of the situation of the cone.
3, equipment
Do routine maintenance of the equipment, such as periodic vibration testing of the main shaft; Regularly check the auxiliary equipment of the equipment; the positional protection of the front and rear processes.
4, the blank
The difference between the upper and lower margins of the processing hole of the blank is large. For this kind of defect, the blank supplier can increase the thickness of the hole wall as much as possible in accordance with the blank drawing, which can reduce the deformation of the machined hole wall. Under the premise that the blank can not be changed, the machining requirements can be met by changing the tool's lead angle, setting the tool life reasonably or selecting a sharper tool.
5, cooling fluid
When high cutting heat occurs during the hole machining, the pressure of the coolant is selected as much as possible, so that the heat dissipation during machining is sufficient to ensure rapid cooling of the cutting edge of the tool and the wall of the machining hole. However, when the coolant pressure of the processing equipment cannot be lifted, we can choose to reduce the number of teeth to optimize the cooling degree of each tooth. For example, the 8 blades of the reamer are reduced to 6 blades, and the number of teeth is reduced. Choose to maintain the feed per tooth (when the process cycle does not affect the premise) or increase the feed to eliminate the flare phenomenon caused by the heat of the hole wall is too high.