Application of five-axis high-speed machining center in automobile cover mould
High-speed cutting theory is increasingly accepted with the development of CNC machining equipment and high-speed machining tool technology; High-speed cutting is a comprehensive concept, which involves many different areas of technology, it appears the traditional processing concepts undergone fundamental changes. Faced with such new processing technology, how to use it effectively is a new challenge for the automotive mold manufacturing process.
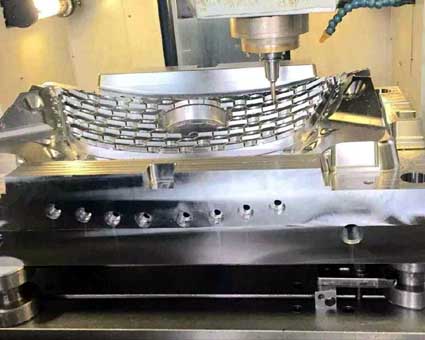
First, the automobile cover mould has its own manufacturing characteristics, mainly in:
The working part of the mold is composed of non-mathematic curved surfaces, and the surface thereof is required to be smooth, smooth and free of ripples, and the ridge lines are clear. Since a car cover part usually requires several pairs of molds to complete, and each work profile must conform to the same mathematical model. Therefore, the surface roughness and shape accuracy requirements are high. There are a number of different punching directions in the wedge mold, which requires the manufacturing equipment to have any rotation angle.
II. High-speed milling equipment performance
The main process performance of five-axis high-speed milling equipment: The maximum spindle speed is 18000r/min. The fastest feed rate of the spindle is 25m/min. The A-axis rotation angle is ±110 degrees. The C axis rotation angle is ±360 degrees. Axial and radial depth of cut ≤ 0.3 mm. The length of the installation tool must not exceed 300mm, the weight should not exceed 5kg, and the five axes can be linked.
High-speed milling features: Due to high rotation speed, fast feed, and small cutting amount, the cutting force is small, the cutting temperature is low, and the tool deflection is small, and a high surface roughness can be obtained, and the processing efficiency is high;
However, the cutting load is required to be uniform.
III. High-speed milling process design
The mold processing of the car cover is mainly based on the profile. According to different processing purposes, it is divided into three stages: roughing, semi-finishing and finishing.
1, rough processing
With the goal of maximizing the amount of material removed per unit time, surface quality and shape accuracy are not required. Since the workpieces are mostly made of castings, the surface of the processing is hard and uneven, and there are few high-speed milling equipment. Rough machining We use powerful milling CNC equipment, and the tool selection Φ63R8 ring milling cutter for contour cutting.
2, semi-finishing
Eliminate the error left by the roughing, the shape reaches a certain precision, and the finishing allowance is more uniform, ready for high-speed finishing. Since the margin left after the roughing is a zigzag shape, especially the margin at the corner is larger, the conventional numerical control equipment is still used, and the Φ30 ball end milling cutter is selected for semi-finishing.
The process is: First use a small-diameter ball-end milling cutter to make the balance at the corners uniform, and then use Φ30 ball-end milling cutter to combine large-scale surfaces.
3, finishing
Remove the semi-finishing allowance to meet the technical requirements of the profile. The high-precision milling equipment is used for finishing, and the Φ20 ball-end milling cutter is selected for parallel line cutting to obtain a high-quality working surface and reduce the fit of the fitter.
Compared with three-axis simultaneous milling, five-axis simultaneous milling has certain advantages. It maintains a certain (or a certain range) angle of the tool axis with the workpiece surface by the movement of the two rotating shafts. Avoiding the maximum cutting speed point and cutting speed to zero point, the cutting force is kept stable, and the processing of the steep wall does not need to lengthen the tool holder. For contour surfaces and holes with different punching directions on the mold, five-axis simultaneous milling can also simplify the machining process and reduce the assist time for tool alignment. However, the spindle of the five-axis linkage device is too large, and the diameter of the clamped tool is small and short, and may interfere with the workpiece during machining. This limits its angle of rotation, making it difficult to machine parts such as narrow and deep troughs and deep cavities.
Therefore, the five-axis linkage milling method is mainly used in the manufacture of automobile outer cover molds, and is currently mainly used for mold parts with relatively flat profiles, small curvature and little change. Such as automotive exterior cover molds. However, the outer cover parts of the automobile have complicated profiles and large changes in curvature.
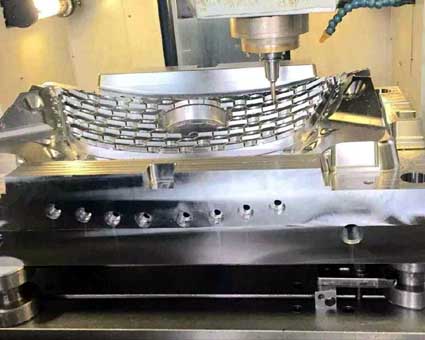
First, the automobile cover mould has its own manufacturing characteristics, mainly in:
The working part of the mold is composed of non-mathematic curved surfaces, and the surface thereof is required to be smooth, smooth and free of ripples, and the ridge lines are clear. Since a car cover part usually requires several pairs of molds to complete, and each work profile must conform to the same mathematical model. Therefore, the surface roughness and shape accuracy requirements are high. There are a number of different punching directions in the wedge mold, which requires the manufacturing equipment to have any rotation angle.
II. High-speed milling equipment performance
The main process performance of five-axis high-speed milling equipment: The maximum spindle speed is 18000r/min. The fastest feed rate of the spindle is 25m/min. The A-axis rotation angle is ±110 degrees. The C axis rotation angle is ±360 degrees. Axial and radial depth of cut ≤ 0.3 mm. The length of the installation tool must not exceed 300mm, the weight should not exceed 5kg, and the five axes can be linked.
High-speed milling features: Due to high rotation speed, fast feed, and small cutting amount, the cutting force is small, the cutting temperature is low, and the tool deflection is small, and a high surface roughness can be obtained, and the processing efficiency is high;
However, the cutting load is required to be uniform.
III. High-speed milling process design
The mold processing of the car cover is mainly based on the profile. According to different processing purposes, it is divided into three stages: roughing, semi-finishing and finishing.
1, rough processing
With the goal of maximizing the amount of material removed per unit time, surface quality and shape accuracy are not required. Since the workpieces are mostly made of castings, the surface of the processing is hard and uneven, and there are few high-speed milling equipment. Rough machining We use powerful milling CNC equipment, and the tool selection Φ63R8 ring milling cutter for contour cutting.
2, semi-finishing
Eliminate the error left by the roughing, the shape reaches a certain precision, and the finishing allowance is more uniform, ready for high-speed finishing. Since the margin left after the roughing is a zigzag shape, especially the margin at the corner is larger, the conventional numerical control equipment is still used, and the Φ30 ball end milling cutter is selected for semi-finishing.
The process is: First use a small-diameter ball-end milling cutter to make the balance at the corners uniform, and then use Φ30 ball-end milling cutter to combine large-scale surfaces.
3, finishing
Remove the semi-finishing allowance to meet the technical requirements of the profile. The high-precision milling equipment is used for finishing, and the Φ20 ball-end milling cutter is selected for parallel line cutting to obtain a high-quality working surface and reduce the fit of the fitter.
The choice of three-axis simultaneous milling and five-axis simultaneous milling in finishing:
Since the surface machining is a point contact milling method, the curvature of the mold surface changes greatly. When using a ball end mill for three-axis simultaneous milling, the point of contact between the tool and the workpiece changes as the curvature changes. The cutting point has a cutting speed of zero and a minimum cutting force. Participation in the cutting at this point will reduce the quality of the machined surface, increase the wear of the blade, and increase the Z-direction of the machine tool spindle. The cutting point of the tool radial point is the largest, and the cutting force is the largest. At this point, the cutting also accelerates the blade wear at this point. (The picture shows the failure mode of the blade during the three-axis simultaneous cutting process.) That is, the cutting force is constantly changing throughout the cutting process, and the larger the tool diameter, the larger the cutting force changes. Therefore, try to choose a small diameter ball head tool to reduce the change in cutting force. However, for steep wall machining, the small diameter and long arbor are not conducive to high speed machining.
Since the surface machining is a point contact milling method, the curvature of the mold surface changes greatly. When using a ball end mill for three-axis simultaneous milling, the point of contact between the tool and the workpiece changes as the curvature changes. The cutting point has a cutting speed of zero and a minimum cutting force. Participation in the cutting at this point will reduce the quality of the machined surface, increase the wear of the blade, and increase the Z-direction of the machine tool spindle. The cutting point of the tool radial point is the largest, and the cutting force is the largest. At this point, the cutting also accelerates the blade wear at this point. (The picture shows the failure mode of the blade during the three-axis simultaneous cutting process.) That is, the cutting force is constantly changing throughout the cutting process, and the larger the tool diameter, the larger the cutting force changes. Therefore, try to choose a small diameter ball head tool to reduce the change in cutting force. However, for steep wall machining, the small diameter and long arbor are not conducive to high speed machining.
Compared with three-axis simultaneous milling, five-axis simultaneous milling has certain advantages. It maintains a certain (or a certain range) angle of the tool axis with the workpiece surface by the movement of the two rotating shafts. Avoiding the maximum cutting speed point and cutting speed to zero point, the cutting force is kept stable, and the processing of the steep wall does not need to lengthen the tool holder. For contour surfaces and holes with different punching directions on the mold, five-axis simultaneous milling can also simplify the machining process and reduce the assist time for tool alignment. However, the spindle of the five-axis linkage device is too large, and the diameter of the clamped tool is small and short, and may interfere with the workpiece during machining. This limits its angle of rotation, making it difficult to machine parts such as narrow and deep troughs and deep cavities.
Therefore, the five-axis linkage milling method is mainly used in the manufacture of automobile outer cover molds, and is currently mainly used for mold parts with relatively flat profiles, small curvature and little change. Such as automotive exterior cover molds. However, the outer cover parts of the automobile have complicated profiles and large changes in curvature.
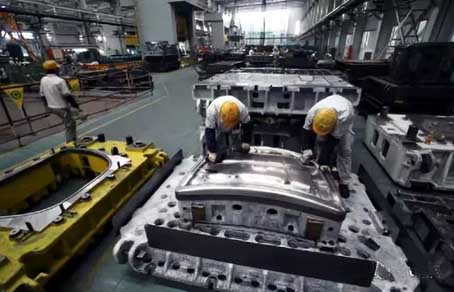