Several major materials machining earphone cavity, you know how much?
The appearance of the earphones also directly affects everyone's desire to buy. Good-looking headphones, not only have a visual sense, the choice of materials will also make a huge difference in appearance.
Machining the cavity of a metal headset is a lot more complicated than making a plastic headset cavity. Most metal earphones need to use CNC technology to cut and mill a whole piece of metal into a cavity shape. Using a milling machine is very time consuming, and a small amount can be processed per day. After cutting from the CNC, it may need to be polished, polished, painted or electroplated. Once there is a problem with each step here, it will affect the yield and thus the cost, which is why the good-looking metal earbuds are often not cheap.
However, the earphone cavity made of metal looks high-quality, but it also needs to be taken care of. In particular, the surface after metal plating is also easily troubled by scratches.
If you look back, the first earbuds should be made of metal. But the earplugs were just a product of the laboratory, not a consumer product. So the design does not need to consider the appearance.
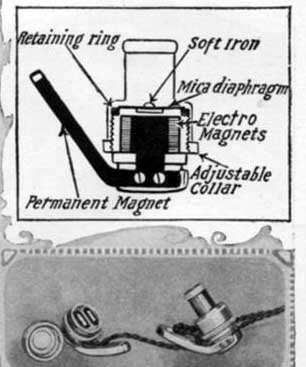
Early earbuds were mostly made of ABS-like plastic. Later, the surface treatment technology of the earplug cavity gradually increased, and chrome plating and frosted spray painting were used, and the appearance gradually became eye-catching. Until now, plastic is still the core material for the production of the earplug housing cavity. The main reason is that plastic is cheap to mold and suitable for mass production. In addition, the easy processing of plastics also facilitates designers to implement cavity designs of various special shapes.
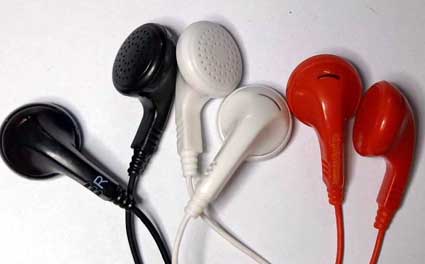
But plastic is always a fragile and easy-to-wear material. Another situation is that plastic is always prone to the impression of low prices and cannot make the product sell for a higher price, so the earplugs of metal cavities have gradually increased.
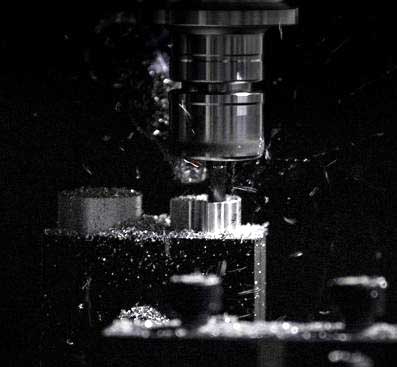
Machining the cavity of a metal headset is a lot more complicated than making a plastic headset cavity. Most metal earphones need to use CNC technology to cut and mill a whole piece of metal into a cavity shape. Using a milling machine is very time consuming, and a small amount can be processed per day. After cutting from the CNC, it may need to be polished, polished, painted or electroplated. Once there is a problem with each step here, it will affect the yield and thus the cost, which is why the good-looking metal earbuds are often not cheap.
However, the earphone cavity made of metal looks high-quality, but it also needs to be taken care of. In particular, the surface after metal plating is also easily troubled by scratches.
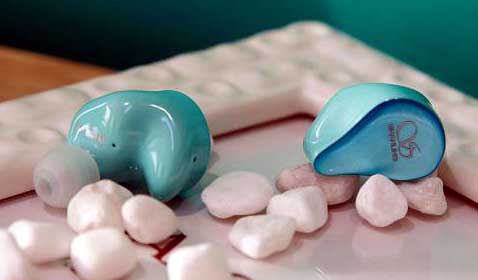
And between metal CNC and plastic, there is a newly popular material-photosensitive resin. This is a liquid material that can undergo rapid physical and chemical changes in a short period of time after being irradiated with ultraviolet rays, and then cross-link and cure the oligomer. It was first developed and applied by Bayer in Germany in 1968.
This material has been used in the earphone field for some time, and in fact, we often come into contact with this material in our lives. For example, the filling materials we use when filling teeth, and the "phototherapy manicure" that women often call, the raw materials used are actually a kind of photosensitive resin.
In the field of earphones, the earliest material was also used in medical-hearing aids. Later, in 1995, an American mixer Jerry Harvey used this material to develop a customized In-Ear Monitor for band musicians. This also became the starting point of the wave of custom headphones.
The custom earphone mentioned here is made by collecting earprints of the contours of individual ears, and according to its shape, using a photosensitive resin to make a shell of the same shape as the cavity of the earphone, and placing a sounding unit in it. After the cavity and the panel are joined together, a layer of bright lacquer is completed after polishing. This layer of bright lacquer is harder and more abrasion-resistant, which makes the shell look brighter and protects the shell. Because the shape itself is customizable, plus the photosensitive resin itself can fuse many different colors, and can even create the appearance of "multicolored black", so custom headphones have always been considered as the most personalized headset products .
In the past, using a photosensitive resin as a cavity also required a mold to be manufactured in advance. If it is a custom headset, the shell of each mold must be made separately, which is very time consuming. Then some manufacturers developed "male model" products-their shapes can be adapted to most consumers as much as possible. The reusable mold greatly reduces the production time and the cost of the mold, and also allows many people to experience the experience of approaching traditional custom headphones at a relatively low price. In addition, the resin material does not irritate the skin like metal when worn, and is a very mild material. The characteristics of wear resistance and dirt resistance, together with a variety of color customization services, have made many young people more and more like this more personalized headset.
Nowadays, the application of 3D printing technology has made the above-mentioned headphones that require CNC cutting and resin injection molding to form a cavity, which has evolved again in production. In addition to printing metal, photosensitive materials are also very commonly used in 3D printing. As a result, many earphone brands have begun to use 3D printing technology to make cavities, and it is believed that more products using related technologies will be available in the future.
This material has been used in the earphone field for some time, and in fact, we often come into contact with this material in our lives. For example, the filling materials we use when filling teeth, and the "phototherapy manicure" that women often call, the raw materials used are actually a kind of photosensitive resin.
In the field of earphones, the earliest material was also used in medical-hearing aids. Later, in 1995, an American mixer Jerry Harvey used this material to develop a customized In-Ear Monitor for band musicians. This also became the starting point of the wave of custom headphones.
The custom earphone mentioned here is made by collecting earprints of the contours of individual ears, and according to its shape, using a photosensitive resin to make a shell of the same shape as the cavity of the earphone, and placing a sounding unit in it. After the cavity and the panel are joined together, a layer of bright lacquer is completed after polishing. This layer of bright lacquer is harder and more abrasion-resistant, which makes the shell look brighter and protects the shell. Because the shape itself is customizable, plus the photosensitive resin itself can fuse many different colors, and can even create the appearance of "multicolored black", so custom headphones have always been considered as the most personalized headset products .
In the past, using a photosensitive resin as a cavity also required a mold to be manufactured in advance. If it is a custom headset, the shell of each mold must be made separately, which is very time consuming. Then some manufacturers developed "male model" products-their shapes can be adapted to most consumers as much as possible. The reusable mold greatly reduces the production time and the cost of the mold, and also allows many people to experience the experience of approaching traditional custom headphones at a relatively low price. In addition, the resin material does not irritate the skin like metal when worn, and is a very mild material. The characteristics of wear resistance and dirt resistance, together with a variety of color customization services, have made many young people more and more like this more personalized headset.
Nowadays, the application of 3D printing technology has made the above-mentioned headphones that require CNC cutting and resin injection molding to form a cavity, which has evolved again in production. In addition to printing metal, photosensitive materials are also very commonly used in 3D printing. As a result, many earphone brands have begun to use 3D printing technology to make cavities, and it is believed that more products using related technologies will be available in the future.