What is Cold Stamping and Mold Making?
Cold stamping is the application of pressure to a material by means of a die mounted on a press to cause separation or plastic deformation. Thereby obtaining a pressure method of the required parts (commonly known as stamping parts or punching). Because it is usually processed at room temperature of the press, it is called cold stamping.
The main feature of the cold stamping production process is that it is processed by die and stamping equipment, which is easy to automate, high in productivity and easy to operate. For ordinary presses, each piece can produce several to dozens of stampings per minute, while high-speed punches can produce hundreds or even thousands of stampings per minute. The parts obtained by cold stamping generally do not need to be machined, so it is a method of saving energy and saving raw materials. Since the raw materials used for cold stamping are mostly sheets or strips with good surface quality, the dimensional tolerances of the stampings are guaranteed by the die, so the dimensions are stable and the interchangeability is good. The cold stamping product has a thin wall, light weight and good rigidity, and can be processed into parts with complicated shapes, from the second hand of the clock to the longitudinal beam of the car and the cover.
However, since the die manufacturing is generally a single-piece small-volume production with high precision and high technical requirements, it is a technology-intensive product with high manufacturing cost. Therefore, cold stamping production can only achieve higher economic effects in the case of large quantities.
In summary, cold stamping has unique characteristics compared with other processing methods, so it is widely used in industrial production, especially in mass production. A considerable number of industrial sectors are increasingly using cold stamping products, such as machinery manufacturing, vehicle production, aerospace, electronics, electrical appliances, light industry, instrumentation and daily necessities. In these industrial sectors, the proportion of stamping parts is quite large. Many parts that have been manufactured by casting, forging and cutting methods have been replaced by stamping parts with light weight and good rigidity. Through stamping processing, productivity is greatly improved and costs are reduced. It can be said that if the stamping process is not widely used in production, it is difficult to upgrade the product in many industrial sectors to improve productivity, improve quality, and reduce costs.
In summary, cold stamping has unique characteristics compared with other processing methods, so it is widely used in industrial production, especially in mass production. A considerable number of industrial sectors are increasingly using cold stamping products, such as machinery manufacturing, vehicle production, aerospace, electronics, electrical appliances, light industry, instrumentation and daily necessities. In these industrial sectors, the proportion of stamping parts is quite large. Many parts that have been manufactured by casting, forging and cutting methods have been replaced by stamping parts with light weight and good rigidity. Through stamping processing, productivity is greatly improved and costs are reduced. It can be said that if the stamping process is not widely used in production, it is difficult to upgrade the product in many industrial sectors to improve productivity, improve quality, and reduce costs.
1. Cold stamping process aspect
Research and application of important trends in the development of various stamping technologies aimed at increasing productivity and product quality, reducing costs and expanding the range of stamping process applications. At present, domestic and rapid emergence of advanced technology for the production has a precision stamping press, a flexible membrane forming, superplastic forming, multi-point forming, explosion and other high-energy electromagnetic forming, high precision stamping and cold extrusion technology, etc. . These stamping advanced technologies have achieved good technical and economic effects in actual production.
Precision stamping is an effective method to improve the accuracy of stamping parts, and an important way to expand the range of stamping processing. At present, precision precision can reach IT6~IT7, and the thickness of sheet can reach 25mm. The fine punching method can not only be punched, but also can be formed (precision bending, deep drawing, flanging, cold extrusion, embossing and countersinking, etc.).
2. Die design and manufacturing aspects
Stamping is the basic condition for the production of die. At present, there are two trends in die design and manufacturing that should be given enough attention.
(1) mold structure and precision are developing in two aspects
On the one hand, in order to meet the needs of high-volume, automatic, precision, safety and other large-scale automated production. The die is developing in the direction of high efficiency, precision, long life, multi-station and multi-function; On the other hand, in order to adapt to the rapid requirements of product upgrading in the market, the design and manufacturing of various rapid prototyping methods and simple economical dies have been rapidly developed.
(2) Modernization of mold design and manufacturing
Advanced technologies such as computer technology and information technology have been widely used in mold technology, and profound changes have taken place in the level of mold technology design and manufacture. At present, the most prominent is the mold CAD/CAM/CAE. The mold industry in the world today is the world leader in the development of mold technology in Japan, the United States and European industrialized countries, occupying half of the world's molds. They have modern design methods and advanced mold making equipment, especially in recent years, these countries have developed CAD/CAM systems as the arm of the mold industry, and the momentum of development is booming.
With the rapid development of mold technology, mold CAD/CAM is rapidly developed and widely used due to its advanced technology. Its technical and economic effects are unmatched by traditional mold design and manufacturing methods. The specific characteristics are as follows:
1. Shortened the mold production cycle.
2. High mold quality.
3. Significantly reduce production efficiency.
4. CAD/CAM technology frees technicians from computational drawing and NC programming to generate more creative labor.
Modern mold manufacturing and mold industry have new features compared with the traditional mold industry:
High productivity
Modern mold productivity is much higher than traditional molds, the main reason is that modern molds have multiple stations, multi-cavity molds or multi-function. For example, the high-productivity progressive die has more than 50 2-positions and the rubber shoe mold has 18 2-positions. In addition to stamping and forming, a set of multi-functional molds also undertake assembly tasks such as assembly and riveting, and can directly produce assemblies.
2. High precision
Modern molds require an order of magnitude higher accuracy than conventional molds. The precision of the precision plastic mold of the station-level progressive die has reached 0.003mm or even higher.
Some high precision, especially those that are fully embedded, have a long life.
The long-life mold is the basic condition for ensuring high production efficiency of high-punching equipment. The life of modern die is generally more than 5 million times. The life of cemented carbide molds can reach 2-6 million times, injection molds 40-600,000 pieces, die-casting molds 5-10 million pieces, and the traditional mold life is only 1/5 or 1/10 of modern molds.
3. Cavity shape and mold structure are complex
The cavity structure of modern molds is more complicated as people's requirements for product shape, dimensional accuracy, and overall productivity increase, as well as the wide application of many new materials and processes.
Based on the above characteristics, we can discover the modern mold industry to become an independent industrial system. Standardization of molds, high level of specialization, production and supply systems for mold standardization and high quality mold materials. In addition, technical talent and capital are intensive. Molds have changed from traditional labor-intensive to technology-intensive. Talent-intensive and capital-intensive industries. Technology-intensive is reflected in the CAD/CAM of the mold, and advanced design methods and equipment will inevitably require high-quality professionals to form a talent-intensive type. At the same time, the high industry is also an important symbol of modern molds. However, it takes a while to implement CIMS in mold production. However, with the development and wide application of CAD/CAM integration technology, and the development of related high-tech, in the near future, automation CIMS will be realized in mold production. Make mold technology, and the entire human mold technology to achieve new flying over.
Throughout the development of modern mold technology, we can see that mold manufacturing technology is always moving toward high, new directions, and accompanied by the development of manual steering automation. All in all, mold design and manufacturing will completely get rid of the production methods that rely mainly on labor, so that the mold manufacturing can be more rationalized, the structure is more simplified, the precision is higher, and it will provide new vitality for the development of various industries in the future.
The main feature of the cold stamping production process is that it is processed by die and stamping equipment, which is easy to automate, high in productivity and easy to operate. For ordinary presses, each piece can produce several to dozens of stampings per minute, while high-speed punches can produce hundreds or even thousands of stampings per minute. The parts obtained by cold stamping generally do not need to be machined, so it is a method of saving energy and saving raw materials. Since the raw materials used for cold stamping are mostly sheets or strips with good surface quality, the dimensional tolerances of the stampings are guaranteed by the die, so the dimensions are stable and the interchangeability is good. The cold stamping product has a thin wall, light weight and good rigidity, and can be processed into parts with complicated shapes, from the second hand of the clock to the longitudinal beam of the car and the cover.
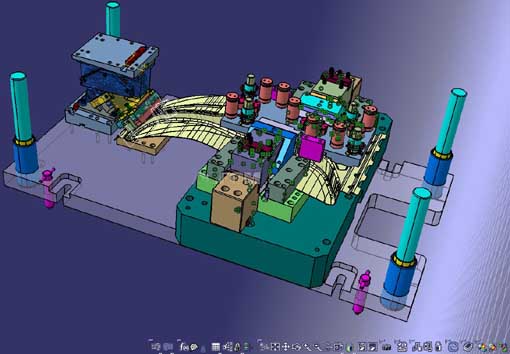
However, since the die manufacturing is generally a single-piece small-volume production with high precision and high technical requirements, it is a technology-intensive product with high manufacturing cost. Therefore, cold stamping production can only achieve higher economic effects in the case of large quantities.
In summary, cold stamping has unique characteristics compared with other processing methods, so it is widely used in industrial production, especially in mass production. A considerable number of industrial sectors are increasingly using cold stamping products, such as machinery manufacturing, vehicle production, aerospace, electronics, electrical appliances, light industry, instrumentation and daily necessities. In these industrial sectors, the proportion of stamping parts is quite large. Many parts that have been manufactured by casting, forging and cutting methods have been replaced by stamping parts with light weight and good rigidity. Through stamping processing, productivity is greatly improved and costs are reduced. It can be said that if the stamping process is not widely used in production, it is difficult to upgrade the product in many industrial sectors to improve productivity, improve quality, and reduce costs.
In summary, cold stamping has unique characteristics compared with other processing methods, so it is widely used in industrial production, especially in mass production. A considerable number of industrial sectors are increasingly using cold stamping products, such as machinery manufacturing, vehicle production, aerospace, electronics, electrical appliances, light industry, instrumentation and daily necessities. In these industrial sectors, the proportion of stamping parts is quite large. Many parts that have been manufactured by casting, forging and cutting methods have been replaced by stamping parts with light weight and good rigidity. Through stamping processing, productivity is greatly improved and costs are reduced. It can be said that if the stamping process is not widely used in production, it is difficult to upgrade the product in many industrial sectors to improve productivity, improve quality, and reduce costs.
1. Cold stamping process aspect
Research and application of important trends in the development of various stamping technologies aimed at increasing productivity and product quality, reducing costs and expanding the range of stamping process applications. At present, domestic and rapid emergence of advanced technology for the production has a precision stamping press, a flexible membrane forming, superplastic forming, multi-point forming, explosion and other high-energy electromagnetic forming, high precision stamping and cold extrusion technology, etc. . These stamping advanced technologies have achieved good technical and economic effects in actual production.
Precision stamping is an effective method to improve the accuracy of stamping parts, and an important way to expand the range of stamping processing. At present, precision precision can reach IT6~IT7, and the thickness of sheet can reach 25mm. The fine punching method can not only be punched, but also can be formed (precision bending, deep drawing, flanging, cold extrusion, embossing and countersinking, etc.).
2. Die design and manufacturing aspects
Stamping is the basic condition for the production of die. At present, there are two trends in die design and manufacturing that should be given enough attention.
(1) mold structure and precision are developing in two aspects
On the one hand, in order to meet the needs of high-volume, automatic, precision, safety and other large-scale automated production. The die is developing in the direction of high efficiency, precision, long life, multi-station and multi-function; On the other hand, in order to adapt to the rapid requirements of product upgrading in the market, the design and manufacturing of various rapid prototyping methods and simple economical dies have been rapidly developed.
(2) Modernization of mold design and manufacturing
Advanced technologies such as computer technology and information technology have been widely used in mold technology, and profound changes have taken place in the level of mold technology design and manufacture. At present, the most prominent is the mold CAD/CAM/CAE. The mold industry in the world today is the world leader in the development of mold technology in Japan, the United States and European industrialized countries, occupying half of the world's molds. They have modern design methods and advanced mold making equipment, especially in recent years, these countries have developed CAD/CAM systems as the arm of the mold industry, and the momentum of development is booming.
With the rapid development of mold technology, mold CAD/CAM is rapidly developed and widely used due to its advanced technology. Its technical and economic effects are unmatched by traditional mold design and manufacturing methods. The specific characteristics are as follows:
1. Shortened the mold production cycle.
2. High mold quality.
3. Significantly reduce production efficiency.
4. CAD/CAM technology frees technicians from computational drawing and NC programming to generate more creative labor.
Modern mold manufacturing and mold industry have new features compared with the traditional mold industry:
High productivity
Modern mold productivity is much higher than traditional molds, the main reason is that modern molds have multiple stations, multi-cavity molds or multi-function. For example, the high-productivity progressive die has more than 50 2-positions and the rubber shoe mold has 18 2-positions. In addition to stamping and forming, a set of multi-functional molds also undertake assembly tasks such as assembly and riveting, and can directly produce assemblies.
2. High precision
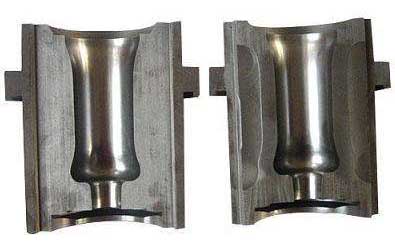
Modern molds require an order of magnitude higher accuracy than conventional molds. The precision of the precision plastic mold of the station-level progressive die has reached 0.003mm or even higher.
Some high precision, especially those that are fully embedded, have a long life.
The long-life mold is the basic condition for ensuring high production efficiency of high-punching equipment. The life of modern die is generally more than 5 million times. The life of cemented carbide molds can reach 2-6 million times, injection molds 40-600,000 pieces, die-casting molds 5-10 million pieces, and the traditional mold life is only 1/5 or 1/10 of modern molds.
3. Cavity shape and mold structure are complex
The cavity structure of modern molds is more complicated as people's requirements for product shape, dimensional accuracy, and overall productivity increase, as well as the wide application of many new materials and processes.
Based on the above characteristics, we can discover the modern mold industry to become an independent industrial system. Standardization of molds, high level of specialization, production and supply systems for mold standardization and high quality mold materials. In addition, technical talent and capital are intensive. Molds have changed from traditional labor-intensive to technology-intensive. Talent-intensive and capital-intensive industries. Technology-intensive is reflected in the CAD/CAM of the mold, and advanced design methods and equipment will inevitably require high-quality professionals to form a talent-intensive type. At the same time, the high industry is also an important symbol of modern molds. However, it takes a while to implement CIMS in mold production. However, with the development and wide application of CAD/CAM integration technology, and the development of related high-tech, in the near future, automation CIMS will be realized in mold production. Make mold technology, and the entire human mold technology to achieve new flying over.
Throughout the development of modern mold technology, we can see that mold manufacturing technology is always moving toward high, new directions, and accompanied by the development of manual steering automation. All in all, mold design and manufacturing will completely get rid of the production methods that rely mainly on labor, so that the mold manufacturing can be more rationalized, the structure is more simplified, the precision is higher, and it will provide new vitality for the development of various industries in the future.