Titanium Alloy Screw Polishing Knowledge
In the process of diversification and high-grade development of industrial products, how to improve the quality of molds directly affecting product quality is an important task.
In the manufacturing process of titanium alloy screw molds, smooth processing and mirror processing after shape processing are called surface grinding and polishing of parts, which is an important process to improve the quality of the mold.
Mastering a reasonable polishing method can improve the quality and service life of titanium alloy screw molds, thereby improving product quality.
Today, KangDing will share with customers a more comprehensive practical titanium polishing information, and hope that buyers have an understanding of titanium alloy screw polishing!
Commonly used titanium alloy screw polishing method and working principle
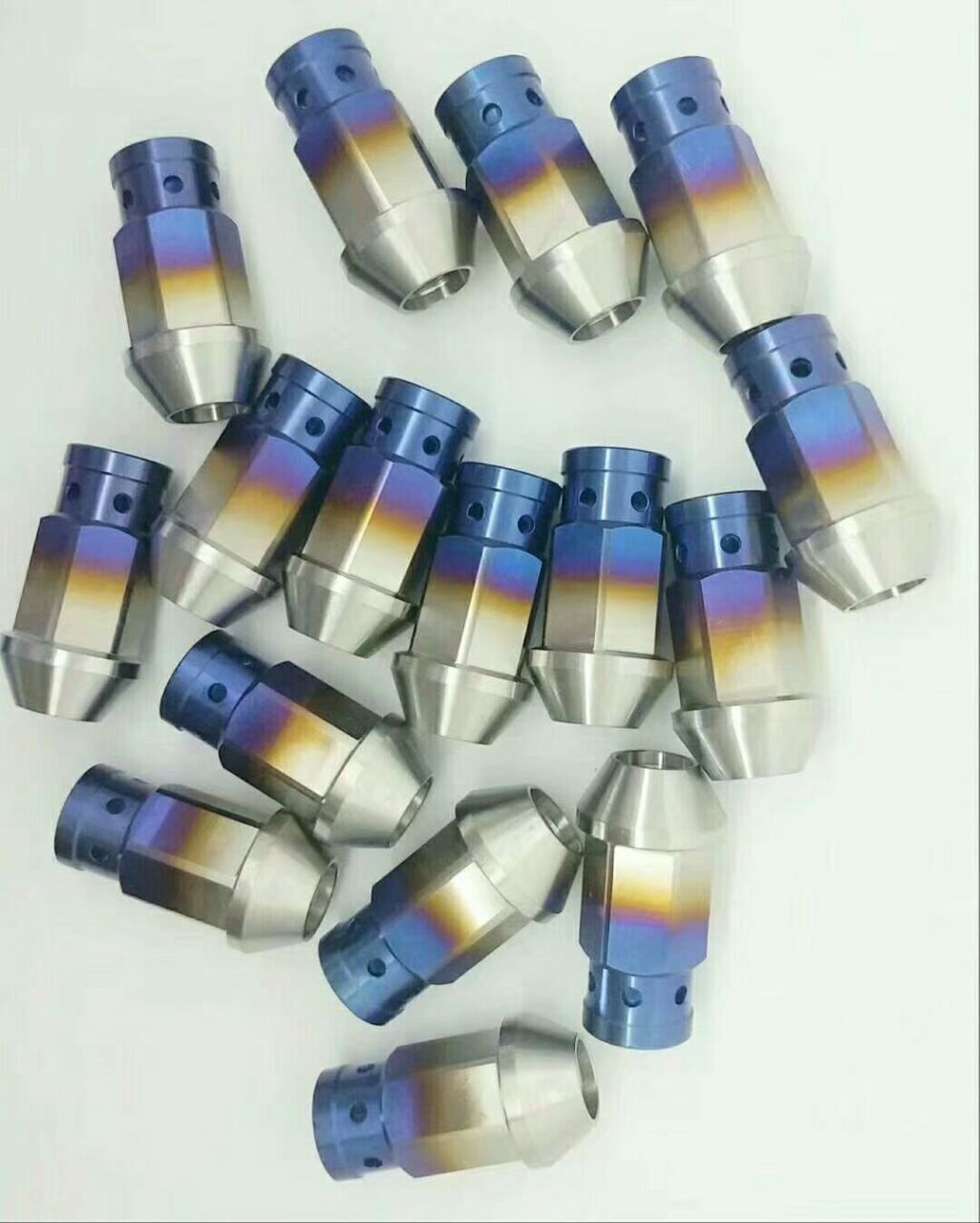
1. Mechanical polishing
Mechanical polishing is a polishing method that removes the convex portion of the surface of the workpiece by cutting or plastically deforming the surface of the material to obtain a smooth surface. Generally, oil stone strips, wool wheels, sandpaper, etc. are used, which are mainly manual operations, and the surface quality requirements are high, and the method of super-fine polishing can be used. Ultra-fine grinding and polishing is a special-purpose grinding tool. In the polishing liquid containing abrasive, it is pressed against the machined surface to perform high-speed rotary motion. Using this technique can achieve Ra0.008 μm surface roughness, various polishing methods best surface roughness. This method is often used in optical lens molds. Mechanical polishing is the main method of mold polishing.
2. Chemical polishing
Chemical polishing is a process in which a material in a chemical medium causes a slightly convex portion of the surface to preferentially dissolve, thereby obtaining a smooth surface. It can polish workpieces with complex shapes and can polish many workpieces at the same time with high efficiency. The surface roughness obtained by chemical polishing is generally Ra10 μm.
3. Electropolishing
The basic principle of electropolishing is the same as chemical polishing, which is to selectively dissolve the surface of the material to make the surface smooth. Compared with chemical polishing, it can eliminate the influence of the cathode reaction and has a good effect.
4. Ultrasonic polishing
Ultrasonic polishing uses the tool section for ultrasonic vibration. A process for polishing brittle hard materials by abrasive suspensions. The workpiece is placed in an abrasive suspension and placed in an ultrasonic field together, and the abrasive is ground and polished on the surface of the workpiece by the action of ultrasonic waves. Ultrasonic machining macro force is small, it does not cause deformation of the workpiece, but the tooling production and installation more difficult.
In the manufacturing process of titanium alloy screw molds, smooth processing and mirror processing after shape processing are called surface grinding and polishing of parts, which is an important process to improve the quality of the mold.
Mastering a reasonable polishing method can improve the quality and service life of titanium alloy screw molds, thereby improving product quality.
Today, KangDing will share with customers a more comprehensive practical titanium polishing information, and hope that buyers have an understanding of titanium alloy screw polishing!
Commonly used titanium alloy screw polishing method and working principle
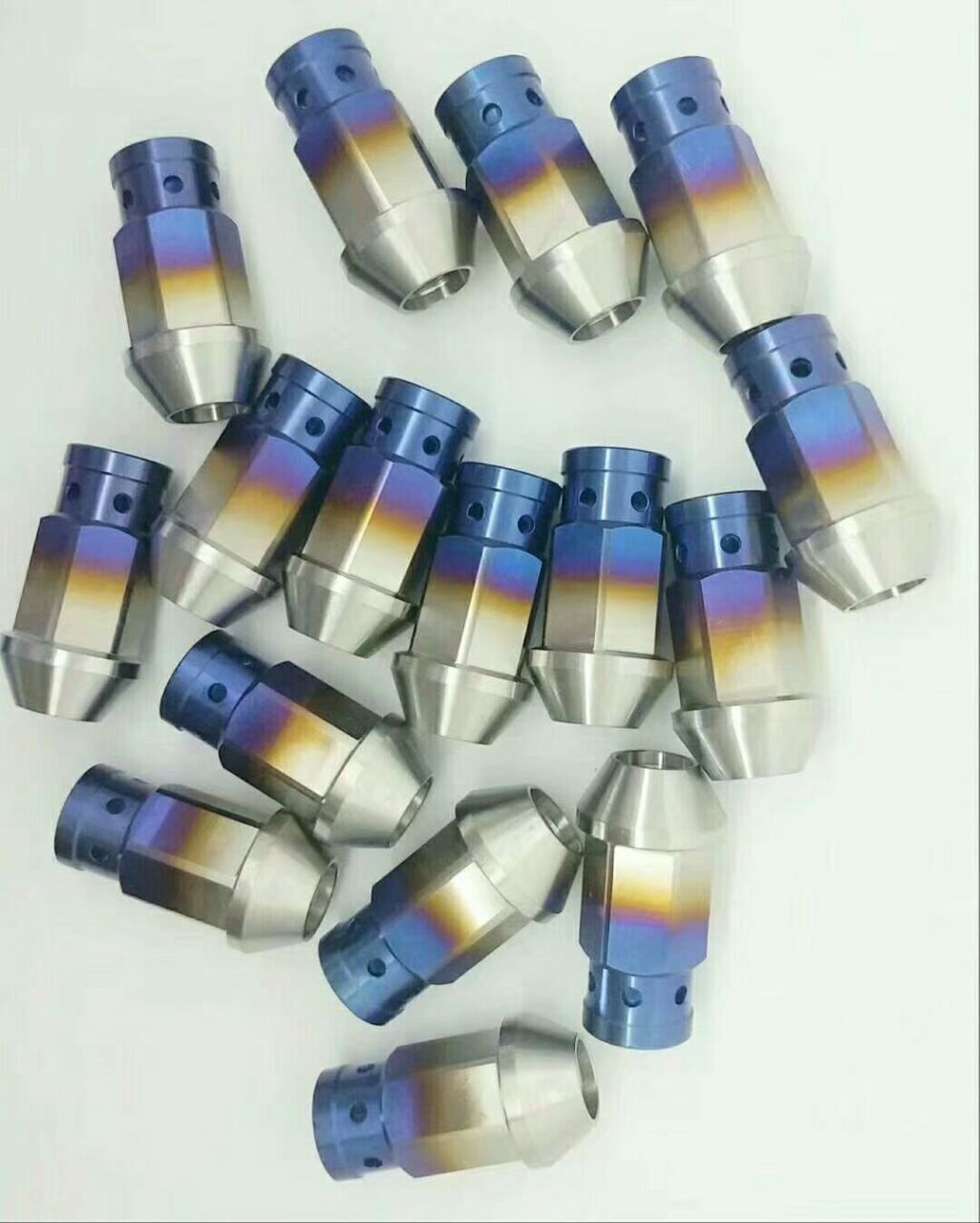
1. Mechanical polishing
Mechanical polishing is a polishing method that removes the convex portion of the surface of the workpiece by cutting or plastically deforming the surface of the material to obtain a smooth surface. Generally, oil stone strips, wool wheels, sandpaper, etc. are used, which are mainly manual operations, and the surface quality requirements are high, and the method of super-fine polishing can be used. Ultra-fine grinding and polishing is a special-purpose grinding tool. In the polishing liquid containing abrasive, it is pressed against the machined surface to perform high-speed rotary motion. Using this technique can achieve Ra0.008 μm surface roughness, various polishing methods best surface roughness. This method is often used in optical lens molds. Mechanical polishing is the main method of mold polishing.
2. Chemical polishing
Chemical polishing is a process in which a material in a chemical medium causes a slightly convex portion of the surface to preferentially dissolve, thereby obtaining a smooth surface. It can polish workpieces with complex shapes and can polish many workpieces at the same time with high efficiency. The surface roughness obtained by chemical polishing is generally Ra10 μm.
3. Electropolishing
The basic principle of electropolishing is the same as chemical polishing, which is to selectively dissolve the surface of the material to make the surface smooth. Compared with chemical polishing, it can eliminate the influence of the cathode reaction and has a good effect.
4. Ultrasonic polishing
Ultrasonic polishing uses the tool section for ultrasonic vibration. A process for polishing brittle hard materials by abrasive suspensions. The workpiece is placed in an abrasive suspension and placed in an ultrasonic field together, and the abrasive is ground and polished on the surface of the workpiece by the action of ultrasonic waves. Ultrasonic machining macro force is small, it does not cause deformation of the workpiece, but the tooling production and installation more difficult.
5. Fluid polishing
Fluid polishing relies on flowing liquid and the abrasive particles it carries to wash the surface of the workpiece for polishing purposes. Fluid dynamic grinding is driven by hydraulic pressure. The medium is mainly made of a special compound (polymeric substance) which flows at a relatively low pressure and is incorporated into an abrasive, and the abrasive can be made of silicon carbide powder.
6. Magnetic grinding and polishing
Magnetic grinding and polishing is the use of magnetic abrasive to form an abrasive brush under the action of a magnetic field to grind the workpiece. This method has high processing efficiency, good quality and easy control of processing conditions. With a suitable abrasive, the surface roughness of the machine can reach Ra 0.1 μm.
7. Electric spark ultrasonic composite polishing
In order to increase the polishing rate of the workpiece with a surface roughness Ra of 1.6 μm or more, Composite polishing using ultrasonic waves and a dedicated high-frequency narrow pulse high peak current pulse power supply, The vibration of the ultrasonic vibration and the electric pulse simultaneously acts on the surface of the workpiece to rapidly reduce the surface roughness. This is very effective in polishing the rough surface of the mold after machining by car, milling, electric spark and wire cutting.
Fluid polishing relies on flowing liquid and the abrasive particles it carries to wash the surface of the workpiece for polishing purposes. Fluid dynamic grinding is driven by hydraulic pressure. The medium is mainly made of a special compound (polymeric substance) which flows at a relatively low pressure and is incorporated into an abrasive, and the abrasive can be made of silicon carbide powder.
6. Magnetic grinding and polishing
Magnetic grinding and polishing is the use of magnetic abrasive to form an abrasive brush under the action of a magnetic field to grind the workpiece. This method has high processing efficiency, good quality and easy control of processing conditions. With a suitable abrasive, the surface roughness of the machine can reach Ra 0.1 μm.
7. Electric spark ultrasonic composite polishing
In order to increase the polishing rate of the workpiece with a surface roughness Ra of 1.6 μm or more, Composite polishing using ultrasonic waves and a dedicated high-frequency narrow pulse high peak current pulse power supply, The vibration of the ultrasonic vibration and the electric pulse simultaneously acts on the surface of the workpiece to rapidly reduce the surface roughness. This is very effective in polishing the rough surface of the mold after machining by car, milling, electric spark and wire cutting.
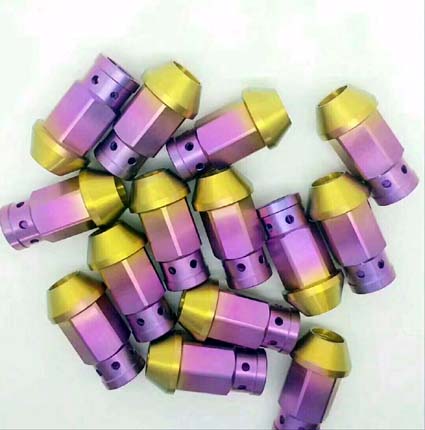