China's Sheet Metal Suppliers
What is sheet metal? Sheet metal processing and technology
Sheet metal is one of the fundamental forms used in metalworking, and it can be cut and bent into a variety of shapes. Sheet metal is a comprehensive cold working process for sheet metal, including shearing, punching/cutting/compounding, folding, riveting, splicing, forming (such as car body), etc. Its notable feature is the uniform thickness of the same part.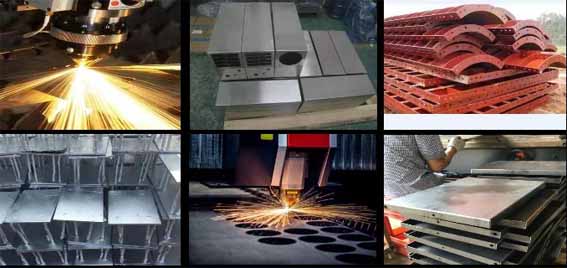
Process characteristics of sheet metal
Sheet metal has the characteristics of light weight, high strength, electrical conductivity (can be used for electromagnetic shielding), low cost, and good mass production performance. It has been widely used in the fields of electronics, communications, automotive industry, and medical equipment. For example, in computer cases, mobile phones, and MP3, sheet metal is an indispensable part. As the application of sheet metal becomes more and more extensive, the design of sheet metal parts has become a very important part of the product development process. Mechanical engineers must be proficient in the design skills of sheet metal parts, so that the designed sheet metal not only meets the requirements of the function and appearance of the product, but also makes the stamping die manufacturing simple and low-cost.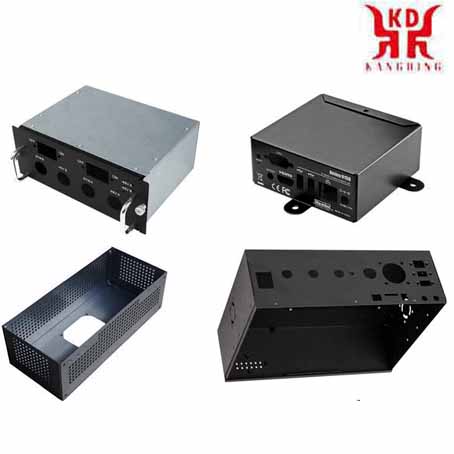
Sheet metal materials
There are many sheet metal materials suitable for stamping processing. Sheet metal materials widely used in the electronic and electrical industry include:⒈ Ordinary cold rolled plate SPCC: SPCC refers to the continuous rolling of steel ingots through cold rolling mills into steel coils or sheets of required thickness. There is no protection on the surface of SPCC, it is easily oxidized when exposed to the air, especially in a humid environment, the oxidation speed is accelerated, and dark red rust appears. The surface should be painted, electroplated or other protections when in use.
⒉ Galvanized steel sheet SECC: The substrate of SECC is ordinary cold-rolled steel coil, which becomes electro-galvanized products after degreasing, pickling, electroplating and various post-treatment processes on the continuous electro-galvanizing production line. SECC not only has the mechanical properties and similar processability of general cold-rolled steel sheet, but also has superior corrosion resistance and decorative appearance. It is highly competitive and replaceable in the market of electronic products, home appliances and furniture. For example, SECC is commonly used in computer cases.
⒊ Hot-dip galvanized steel sheet SGCC:Hot-dip galvanized steel coil refers to the semi-finished product after hot-rolling and pickling or cold-rolling. After cleaning, annealing, and immersing in a molten zinc bath at a temperature of about 460°C, the steel sheet is plated with a zinc layer, and then quenched and tempered, leveled and chemically treated. SGCC material is harder than SECC material, has poor ductility (avoid deep drawing design), thicker zinc layer, and poor electric weldability.
⒋ Stainless steel SUS301:The content of Cr (chromium) is lower than that of SUS304, and the corrosion resistance is poor, but it can obtain good tensile force and hardness after cold working. It has good elasticity and is mostly used for shrapnel springs and anti-EMI.
⒌ Stainless steel SUS304:One of the most widely used stainless steels, because it contains Ni (nickel), it has better corrosion resistance and heat resistance than Cr (chromium) steel. It has very good mechanical properties, no heat treatment hardening, and no elasticity.
Sheet metal forming process
Generally speaking, the basic equipment of sheet metal technology includes shearing machine, CNC punch/laser, plasma, water jet cutting machine, bending machine, and drilling machine. And various auxiliary equipment such as: decoiler, leveling machine, deburring machine, spot welding machine, etc.Generally, the four most important steps of sheet metal processing are shearing, punching/cutting, folding/rolling, welding, surface treatment, etc.
Sheet metal is sometimes used as a pull metal. The word comes from the English platemetal. Generally, some metal sheets are plastically deformed by hand or die stamping to form the desired shape and size. And it can be further welded or a small amount of mechanical processing to form more complex parts, such as chimneys, iron stoves, and car shells commonly used in households are all sheet metal parts.
The processing of sheet metal is called sheet metal processing. Specific examples include making chimneys, iron barrels, oil tanks, ventilation pipes, elbows, elbows, and funnels from plates. The main processes are cutting, bending, bending, forming, welding, riveting, etc., which require certain geometric knowledge.
Sheet metal parts are thin sheet metal parts, which are parts that can be processed by stamping, bending, and stretching. A general definition is:
Parts with constant thickness during processing. Corresponding to castings, forgings, machining parts, etc., for example, the outer iron shell of a car is sheet metal, and some kitchen utensils made of stainless steel are also sheet metal.
Modern sheet metal technology includes: Filament power supply winding machining, Laser cutting, heavy processing, metal bonding, metal drawing, plasma cutting, precision welding, roll forming, sheet metal bending, die forging, water jet cutting, precision welding, etc.
The surface treatment of sheet metal parts is also a very important part of the sheet metal processing process, because it has the functions of preventing parts from rusting and beautifying the appearance of products. The main function of the surface pretreatment of sheet metal parts is to remove oil stains, oxide scales, rust and so on.
It prepares for the surface post-treatment, and the post-treatment is mainly spray (baking) paint, plastic spray and anti-rust coating, etc.
In 3D software, SolidWorks, UG, Pro/E, SolidEdge, TopSolid, CATIA, etc. all have a design of sheet metal parts. It is mainly through the editing of 3D graphics to obtain the data required for sheet metal processing (such as unfolded drawings, bending lines, etc.). And provide data for CNC punch/laser, plasma, water jet cutting machine/composite machine and CNC bending machine, etc.
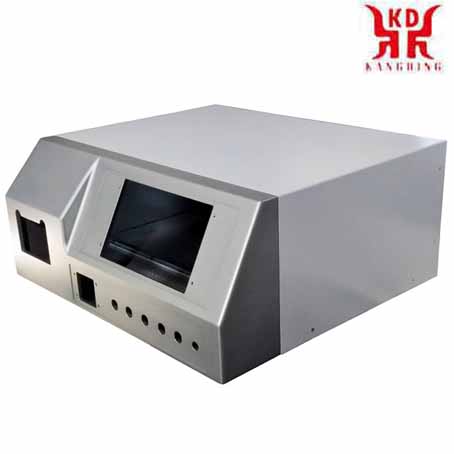
Process design of sheet metal
In meeting the requirements of product functions and appearance, the design of sheet metal should ensure simple stamping process, easy stamping die production, high quality of sheet metal stamping, and stable dimensions.The process of sheet metal processing
After the drawing is completed, choose different blanking methods according to the different unfolding drawings and batches, including laser, CNC punching, shearing, molds, etc., and then make the corresponding unfolding according to the drawing. The CNC punching machine is affected by the tool, and for the processing of some special-shaped workpieces and irregular holes, large burrs will appear on the edges. It is necessary to carry out the post-deburring treatment, and at the same time, it will have a certain influence on the accuracy of the workpiece;Laser processing has no tool restriction, flat section, suitable for processing special-shaped workpieces, but it takes a long time to process small workpieces. Place the worktable next to the CNC and the laser, which is conducive to placing the sheet on the machine for processing and reducing the workload of lifting the board.
Some usable side materials are placed in designated places to provide materials for trial molds during bending. After the workpiece is blanked, the corners, burrs, and contacts should be trimmed (grinding) as necessary. Use a flat file to trim the tool joints, use a grinder to trim the workpieces with larger burrs, and use a corresponding small file to trim the small inner hole contacts to ensure a beautiful appearance. At the same time, the trimming of the shape also ensures the positioning during bending, so that the position of the workpiece on the bending machine during bending is consistent, and the size of the same batch of products is consistent.
After the blanking is completed, it enters the next process, and different workpieces enter the corresponding process according to the processing requirements. There are bending, pressure riveting, flanging and tapping, spot welding, convex hull, and step difference. Sometimes the nut or stud is pressed after one or two bends. Among them, the convex hull of the mold and the step difference should be considered to be processed first, so as to avoid interference in other processes after the first processing, and the required processing cannot be completed. If there are hooks on the upper cover or the lower shell, they cannot be touch-welded after bending and must be processed before bending.
When bending, you must first determine the tool and slot used for bending according to the size on the drawing and the thickness of the material. Avoiding deformation caused by collision between the product and the tool is the key to the selection of the upper mold (in the same product, different types of upper molds may be used). The selection of the lower mold is determined according to the thickness of the plate. The second is to determine the order of bending: the general rule of bending is first inside and then outside, first small and then big, first special and then common. The workpiece with dead edges is first bend the workpiece to 30°-40°, and then the workpiece is pressed to death with a leveling die.
When riveting, consider the height of the stud and choose the same different mold, and then adjust the pressure of the press to ensure that the stud and the surface of the workpiece are flush. Avoid that the stud is not pressed firmly or pressed out beyond the surface of the workpiece, causing the workpiece to be scrapped.
Welding includes argon arc welding, spot welding, carbon dioxide shielded welding, manual arc welding and so on. Spot welding must first consider the welding position of the workpiece, and consider making positioning tooling to ensure the accuracy of the spot welding position during mass production.
In order to weld firmly, make bumps on the workpiece to be welded. The bumps can be evenly contacted with the plate before energized welding, so as to ensure that the heating of each point is consistent, and the welding position can also be determined. Similarly, to perform welding, adjust the preload time, holding time, maintenance time, and rest time to ensure that the workpiece can be spot welded firmly. After spot welding, weld scars will appear on the surface of the workpiece, which should be treated with a flat grinder. Argon arc welding is mainly used when two large workpieces are to be connected together, or the corners of a workpiece are treated to achieve a flat and smooth surface of the workpiece. The heat generated during argon arc welding can easily deform the workpiece. After welding, use a grinder and a flat grinder to process, especially the corners.
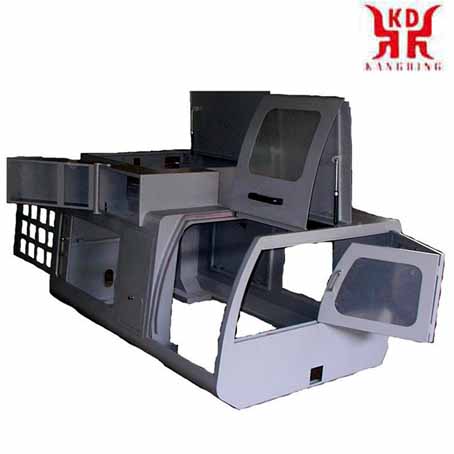
The workpiece must be surface treated after the bending, riveting and other processes are completed. The surface treatment of different plates is different. After cold plate processing, the surface is generally electroplated. After electroplating, spraying is not performed. After chemical treatment, spray treatment is required. The surface of the electroplated board is cleaned, degreased, and then sprayed. The stainless steel plate (with mirror panel, fog panel, wire drawing board) can be wire drawn before bending, no spraying, if spraying needs to be roughed; Aluminum plates are generally oxidized, and different oxidized background colors are selected according to different colors of spraying. Commonly used are black and natural color oxidation; The aluminum plate needs to be sprayed after chromate oxidation treatment. Surface pretreatment can clean the surface, significantly improve the adhesion of the coating film, and can double the corrosion resistance of the coating film. The process of cleaning the workpiece, first hang the workpiece on the assembly line: First, it passes through the cleaning solution (alloy degreasing powder), then enters the clean water, then passes through the spray area, then passes through the drying area, and finally the workpiece is removed from the assembly line.
After the surface pretreatment, enter the spraying process. When the workpiece is required to be sprayed after assembly, the teeth or part of the conductive holes need to be protected. The tooth hole can be inserted into the soft glue stick or screwed into the screw, and the high temperature tape should be used for conductive protection. Large quantities of positioning tooling are made to position and protect, so that the inside of the workpiece will not be sprayed during spraying. The nut (flanging) hole that can be seen on the outer surface of the workpiece is protected with a screw to avoid the need for tooth retraction at the nut (flanging) hole of the workpiece after spraying.
Some large batches of workpieces also use tooling protection; When the workpiece is not equipped with spraying, the area that does not need to be sprayed is blocked with high temperature resistant tape and paper, and some exposed nut (stud) holes are protected by screws or high temperature resistant rubber. If the workpiece is sprayed on both sides, use the same method to protect the nut (stud) hole; Small workpieces are sprayed with lead wires or paper clips and other items together; some workpieces have high requirements on the surface and must be scraped before spraying; Some workpieces are protected by special heat-resistant stickers at the grounding symbol. When spraying, the workpiece is hung on the assembly line first, and the dust on the surface is blown off with the air pipe. Enter the spraying area for spraying. After spraying, follow the assembly line into the drying area, and finally remove the sprayed workpiece from the assembly line. There are two types of manual spraying and automatic spraying, so the tooling used is different.
Enter the assembly process after spraying. Before assembling, tear off the protective sticker originally used in spraying, and make sure that the internal threaded hole of the part is not sprinkled with paint or powder. During the entire process, wear gloves to avoid dust on your hands from sticking to the workpiece, and some workpieces need to be blown clean with an air gun.
After the assembly is completed, it will enter the packaging process. After inspection, the workpiece is put into a special packaging bag for protection; Some workpieces without special packaging are packaged with bubble film, etc., before packaging the bubble film is cut to the size of the workpiece, so as not to cut while packaging and affect the packaging speed; Large batches can be customized for special cartons or bubble bags, rubber pads, pallets, wooden boxes, etc. After packaging, put it into the carton, and then paste the corresponding finished product or semi-finished product label on the carton.
In addition to strict requirements in the production process, the quality of sheet metal parts requires quality inspection independent of production. 1. Strictly check the size according to the drawings. 2. Strictly check the appearance quality, and repair or scrap the items that do not match the size. The appearance is not allowed to be scratched, and the color difference, corrosion resistance, adhesion, etc. after spraying shall be inspected. In this way, errors in unfolding drawings, bad habits in the manufacturing process, and errors in the manufacturing process can be found. Such as CNC stamping programming errors, mold errors, etc.