Comparison of different heat sink production and processing technologies
What is a heat sink? A heat sink is a device that dissipates heat-prone electronic components in electrical appliances. It is mostly made of aluminum alloy, brass, or bronze in a plate shape, sheet shape, or multi-sheet shape. For example, the CPU central processor in the computer needs to use a relatively large heat sink, and the power tube, line tube in the TV, and the power amplifier tube in the power amplifier must use the heat sink. In general, the heat sink should be coated with a layer of thermal grease on the contact surface between the electronic components and the heat sink, so that the heat emitted by the components is more effectively conducted to the heat sink, and then radiated to the surrounding air through the heat sink. As for the material of the heat sink, the thermal conductivity of each material is different, and the thermal conductivity is arranged from high to low, which are silver, copper, aluminum, and steel. However, if silver is used as the heat sink, it will be too expensive, so the best solution is to use copper. Although aluminum is a much cheaper heat sink, it is obviously less thermally conductive than copper (about 50% of copper). At present, the commonly used heat sink materials are copper and aluminum alloy, each of which has its advantages and disadvantages. Copper has good thermal conductivity, but it is more expensive, difficult to process, and overweight (many pure copper radiators exceed the CPU's limit on weight). It has a small heat capacity and is susceptible to oxidation. Pure aluminum is too soft to be used directly. All aluminum alloys used can provide sufficient hardness. The advantages of aluminum alloys are low price and light weight, but the thermal conductivity is much worse than copper. Some radiators have their own advantages, and a copper plate is embedded in the aluminum alloy radiator base. For ordinary users, the use of aluminum heat sink is sufficient to meet the heat dissipation needs. The northern heating radiator is also called a heat sink. The heat sink plays an important role in the composition of the heat sink. In addition to the active cooling of the fan, assessing the quality of a heat sink depends to a large extent on the heat sink's ability to absorb heat and conduct heat.
Basic production process of heat sink:
Product requirements --- Drawing development --- Mold making --- Testing die (extruded aluminum profile) --- Cutting and CNC processing --- Confirmation of functional size samples ) --- Production Input --- Packaging (Inspection) --- Delivery.
1. Aluminum extruded heat sink Aluminum material has been used in the radiator market for a long time due to its soft and easy processing characteristics. The aluminum extrusion technology is simply to heat the aluminum ingots at high temperature, and then let the aluminum liquid flow through the extrusion mold with grooves under high pressure to make the radiant fins. However, after cutting and grooving the original fins of the heat sink, the common heat sinks are made. The cost of the aluminum extrusion heat sink is low, and the technical threshold is not high. However, due to the limitation of the material, the thickness and length ratio of the heat dissipation fins cannot exceed 1:18. Therefore, it is difficult to increase the heat dissipation area in a limited space. Therefore, the heat dissipation effect of the aluminum extruded heat sink is relatively poor, and it is difficult to compete with the high-frequency CPU that is increasing today.
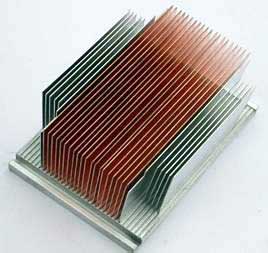
2. plug copper heat sink current mainstream of the main material used for the fins is nothing less than two kinds of aluminum and copper. And plug copper process is the combination of aluminum and copper, the respective advantages of the product came into being. The copper plug process is completed by the principle of thermal expansion and contraction. After the aluminum extruded heat sink is heated, the copper core is inserted thereinto, and then the overall cooling is performed. Because no third-party dielectric is used, the copper plugging process can greatly reduce the thermal resistance between the contact surfaces. Not only does it ensure the tightness of the copper-aluminum bond, it also fully utilizes the characteristics of aluminum's fast heat dissipation and copper's fast heat absorption. This copper plugging process has a moderate cost and good heat dissipation effect, and is the mainstream type of heat sink on the market.
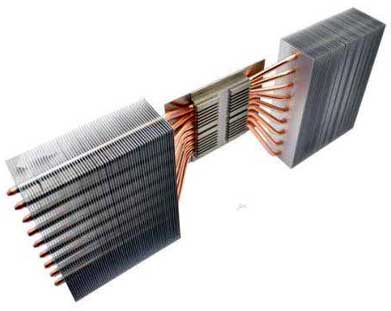
3. The compaction method is to stack a large number of copper or aluminum sheets, then press on both sides and polish the section. This section is in contact with the CPU core, and the other side is spread out to serve as a fin for the heat sink. The heat sink made by compaction method is characterized in that the number of fins can be made much. And does not require a high process to ensure that each fin can maintain good contact (or close) with the CPU core. The fins also have close contact by means of compression, and the heat conduction loss between them will be significantly reduced. It is precisely because the heat sink made by compaction method has many fins, the heat dissipation effect of this heat sink is often good, and the weight is much lighter than the traditional heat sink.
4. The forging heat sink forging process is formed by heating the aluminum block and filling the mold with high pressure. Its advantage is that the fin height can reach more than 50mm and the thickness is less than 1mm. It can get the largest heat dissipation area in the same volume, and it is easy to get good dimensional accuracy and surface finish in forging. However, due to the low plasticity of the metal during forging, cracking is easy to occur during deformation, and the deformation resistance is large, requiring large tonnage (more than 500 tons) forging machinery. It is also because of the high cost of equipment and molds that the cost of the product is extremely high, and even many overclocking enthusiasts can not afford it.
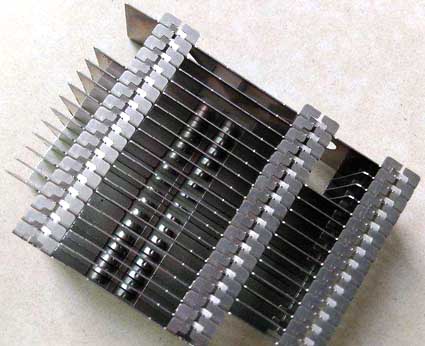
5. Bonding type heat sinks Because traditional aluminum extruded type heat sinks cannot break the limit of the thickness and length ratio of fins, they are combined heat sinks. This kind of heat sink is made of aluminum or copper plate first, and then it is combined on a heat sink with grooves by using thermal conductive paste or solder. The characteristics of the combined heat sink are that the fins break through the original proportional limit, and the heat dissipation effect is good, and different materials can be used as the fins. Of course, the shortcomings are also obvious, that is, the use of thermal paste and solder to connect the fin and the base will have an interface impedance problem. This affects heat dissipation. In order to improve these shortcomings, two new technologies have been used in the field of heat sinks. The first is the gear shaping technology. It uses a pressure of more than 60 tons to combine the aluminum sheet in the base of the copper sheet, and no medium is used between aluminum and copper. From a microscopic perspective, the atoms of aluminum and copper are connected to each other to a certain extent, thereby completely avoiding the disadvantages of thermal resistance caused by the traditional copper-aluminum combination and greatly improving the heat transfer ability of the product. The second is the reflow soldering technology. The biggest problem of the traditional bonding heat sink is the interface impedance problem, and the reflow soldering technology is an improvement on this problem. In fact, the process of reflow soldering is almost the same as the traditional bonding type heat sink, except that a special reflow furnace is used, which can accurately set the soldering temperature and time parameters. The solder uses lead-tin alloy to make the welding and the metal to be fully contacted, thereby avoiding missing soldering and empty soldering. Ensure that the connection between the fin and the base is as close as possible, minimize the interface thermal resistance, and control the melting time and temperature of the copper of each solder joint to ensure the uniformity of all solder joints. However, this special reflow furnace is very expensive. Motherboard manufacturers use more, but radiator manufacturers rarely use it.
6. Compared with aluminum extruded fins, the cutting process solves the limitation of the fin thickness-to-length ratio of the fins. The cutting process is to use special tools to cut the entire material into layers of fins. The heat sink fins can be as thin as 0.5mm. In addition, the fins of the heat sink and the base are integrated, so there is no problem of interface impedance. However, the effect of this cutting process in the production process is high waste and low quality rate, which makes the cost high, so the cutting process is mainly biased to copper heat sink.
Basic production process of heat sink:
Product requirements --- Drawing development --- Mold making --- Testing die (extruded aluminum profile) --- Cutting and CNC processing --- Confirmation of functional size samples ) --- Production Input --- Packaging (Inspection) --- Delivery.
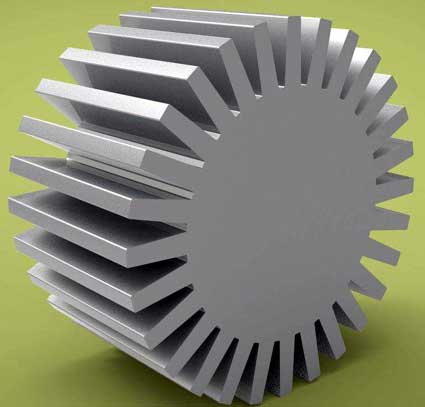
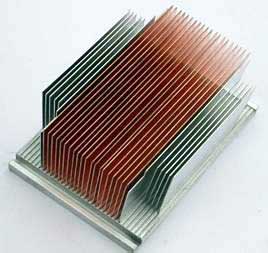
2. plug copper heat sink current mainstream of the main material used for the fins is nothing less than two kinds of aluminum and copper. And plug copper process is the combination of aluminum and copper, the respective advantages of the product came into being. The copper plug process is completed by the principle of thermal expansion and contraction. After the aluminum extruded heat sink is heated, the copper core is inserted thereinto, and then the overall cooling is performed. Because no third-party dielectric is used, the copper plugging process can greatly reduce the thermal resistance between the contact surfaces. Not only does it ensure the tightness of the copper-aluminum bond, it also fully utilizes the characteristics of aluminum's fast heat dissipation and copper's fast heat absorption. This copper plugging process has a moderate cost and good heat dissipation effect, and is the mainstream type of heat sink on the market.
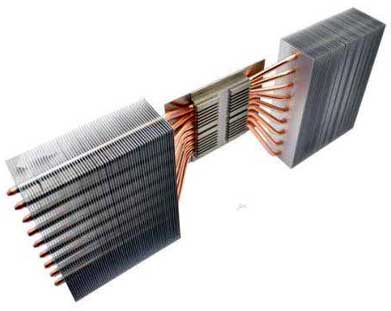
3. The compaction method is to stack a large number of copper or aluminum sheets, then press on both sides and polish the section. This section is in contact with the CPU core, and the other side is spread out to serve as a fin for the heat sink. The heat sink made by compaction method is characterized in that the number of fins can be made much. And does not require a high process to ensure that each fin can maintain good contact (or close) with the CPU core. The fins also have close contact by means of compression, and the heat conduction loss between them will be significantly reduced. It is precisely because the heat sink made by compaction method has many fins, the heat dissipation effect of this heat sink is often good, and the weight is much lighter than the traditional heat sink.
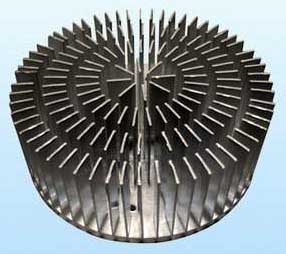
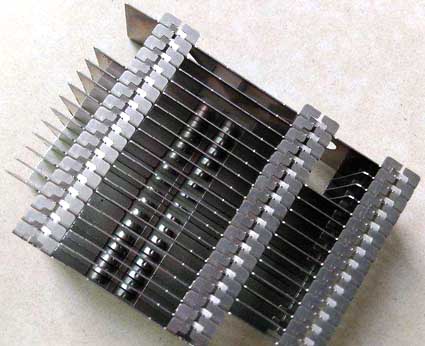
5. Bonding type heat sinks Because traditional aluminum extruded type heat sinks cannot break the limit of the thickness and length ratio of fins, they are combined heat sinks. This kind of heat sink is made of aluminum or copper plate first, and then it is combined on a heat sink with grooves by using thermal conductive paste or solder. The characteristics of the combined heat sink are that the fins break through the original proportional limit, and the heat dissipation effect is good, and different materials can be used as the fins. Of course, the shortcomings are also obvious, that is, the use of thermal paste and solder to connect the fin and the base will have an interface impedance problem. This affects heat dissipation. In order to improve these shortcomings, two new technologies have been used in the field of heat sinks. The first is the gear shaping technology. It uses a pressure of more than 60 tons to combine the aluminum sheet in the base of the copper sheet, and no medium is used between aluminum and copper. From a microscopic perspective, the atoms of aluminum and copper are connected to each other to a certain extent, thereby completely avoiding the disadvantages of thermal resistance caused by the traditional copper-aluminum combination and greatly improving the heat transfer ability of the product. The second is the reflow soldering technology. The biggest problem of the traditional bonding heat sink is the interface impedance problem, and the reflow soldering technology is an improvement on this problem. In fact, the process of reflow soldering is almost the same as the traditional bonding type heat sink, except that a special reflow furnace is used, which can accurately set the soldering temperature and time parameters. The solder uses lead-tin alloy to make the welding and the metal to be fully contacted, thereby avoiding missing soldering and empty soldering. Ensure that the connection between the fin and the base is as close as possible, minimize the interface thermal resistance, and control the melting time and temperature of the copper of each solder joint to ensure the uniformity of all solder joints. However, this special reflow furnace is very expensive. Motherboard manufacturers use more, but radiator manufacturers rarely use it.
6. Compared with aluminum extruded fins, the cutting process solves the limitation of the fin thickness-to-length ratio of the fins. The cutting process is to use special tools to cut the entire material into layers of fins. The heat sink fins can be as thin as 0.5mm. In addition, the fins of the heat sink and the base are integrated, so there is no problem of interface impedance. However, the effect of this cutting process in the production process is high waste and low quality rate, which makes the cost high, so the cutting process is mainly biased to copper heat sink.