Stamping
What is stamping?
Stamping is the application of external forces to plates, strips, tubes and profiles by presses and dies. Plastic deformation or separation to obtain the shape and size of the workpiece (stamping) forming processing methods. Stamping and forging are plastic processing (or pressure processing), collectively known as forging. Stamped blanks are mainly hot-rolled and cold-rolled steel sheets and strips. Of the steel in the world, 60 to 70% are plate materials, most of which are stamped into products. The car's body, chassis, fuel tanks, radiators, boiler steam drums, container shells, electric motors, and electrical appliances such as iron core silicon steel sheets are stamped and processed. There are also a large number of stamping parts in products such as instrumentation, household appliances, bicycles, office machinery, and household utensils.
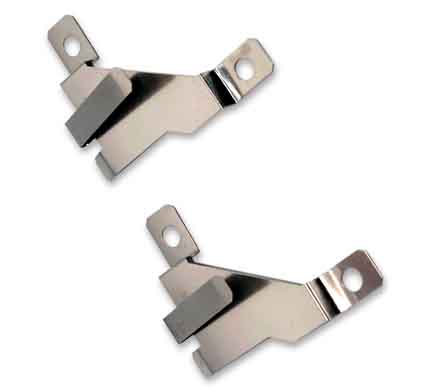
Stamping is the use of conventional or special press equipment power, so that the sheet material in the mold directly by the deformation force, and deformation, the production technology of product parts with certain shape, size and performance is obtained.
Sheets, moulds and equipment are the three elements of stamping.
Stamping temperature is divided into hot stamping and cold stamping.
The former is suitable for sheet material processing with high deformation resistance and poor plasticity;
The latter is performed at room temperature and is a commonly used stamping method for thin plates. It is one of the main methods of metal plastic processing (or pressure processing), and it is also affiliated with material forming engineering technology.
The die used for punching is referred to as die. Dies are special tools for the batch processing of materials (metal or non-metal) into the required stampings. Die is very important in stamping, there is no die that meets the requirements, batch stamping production is difficult to carry out; Without advanced dies, advanced stamping processes cannot be realized. Stamping processes and dies, stamping equipment and stamping materials constitute the three elements of stamping. Only when they are combined can stampings be obtained.
Stamping industry
The stamping industry is an industry that involves a very wide range of industries. It penetrates into all aspects of the manufacturing industry. In foreign countries, stamping is called sheet forming. In our country also has called it.
What is the status of China's stamping industry? The development of foreign stamping, This is a matter of concern to all of us. The vigorous development of stamping should be attributed to the development of daily necessities for automobiles, aircraft and household appliances.
Technology level
The stampings market is very imperfect and sound. However, the small stamping parts market is very mature in some areas in the south. Judging from the current situation, China's stamping parts market has the following problems:
(1) some of the production capacity oversupply.
(2) The market for household electrical appliances and electrical stamping parts is fiercely competitive. However, there are not many companies that have international competitiveness.
(3) The overall level is low and there is a lack of high-grade technologies. Slow technological progress.
(4) The level of material technology, mold technology, lubrication technology, and equipment are all at a relatively low level, far from meeting the needs of domestic production and development.
Processing features
Compared with castings and forgings, stampings are thin, uniform, light and strong. Stamping can produce processes that are difficult for other equipment to manufacture, such as workpieces with stiffeners, ribs, undulations, or flanging, to increase their rigidity.
Due to the use of precision molds, the accuracy of the workpiece can reach up to micrometers, and the repeat accuracy and specifications are consistent. Can be punched out of hole, bump and so on.
Cold stampings are generally no longer cut, or require only a small amount of cutting. The accuracy and surface condition of hot stamping parts are lower than those of cold stamping parts, but they are still better than castings and forgings, and the amount of machining is small.
Stamping is an efficient production method using composite molds, especially multi-position progressive molds. It can complete multiple stamping processes on one press (single station or multi-station) to realize full-automatic production from unwinding, leveling, blanking, forming and finishing. With high production efficiency, good working conditions and low production costs, it can produce hundreds of pieces per minute. Compared with other methods of mechanical processing and plastic processing, stamping has many unique advantages both technically and economically.
The main performance is as follows:
(1) The stamping process has high production efficiency, convenient operation and easy realization of mechanization and automation. This is because stamping is done by means of die and stamping equipment. The number of strokes of ordinary presses can reach tens of times per minute, and the high-speed pressure can reach hundreds of times or even more than 1,000 times per minute. And each punching stroke can get a punching piece.
(2) Since the die ensures the dimensional and shape accuracy of the stamping part during stamping, and generally does not damage the surface quality of the stamping part, The die life is generally longer, so the stamping quality is stable, interchangeability is good, with the "identical" feature.
(3) Stamping can process parts with a wide range of sizes and complex shapes.
Such as stopwatches as small as clocks, as large as car longitudinal beams, coverings, etc. In addition to the cold deformation hardening effect of the material during stamping, the stamping strength and stiffness are both high.
(4) Stamping generally does not generate scraps, material consumption is less, and no other heating equipment is required. Therefore, it is a saving material and energy-saving processing method, and the cost of stamping parts is low.
Due to the superiority of stamping, stamping processing has a wide range of applications in various fields of the national economy. For example, there are stamping and processing in aerospace, aviation, military, machinery, agricultural machinery, electronics, information, railways, post and telecommunications, transportation, chemicals, medical equipment, household appliances and light industry. Not only is it used by the entire industry, but everyone has direct contact with stamping products. There are many large, medium and small stampings on airplanes, trains, cars and tractors. The car body, frame and rim are all stamped out. According to relevant survey statistics, 80% of bicycles, sewing machines, and watches are stampings; 90% of televisions, tape recorders, and cameras are stampings; There are also food metal shells, steel refining boilers, enamel bowls and stainless steel cutlery, all of which are stamping products using moulds; Even the computer's hardware can not lack stampings parts.
Attention problem
1, mold problems
The molds used for stamping and processing are generally specialized. Sometimes a complex part requires several sets of molds to be processed and formed. The precision of mold manufacturing is high and the technical requirements are high. It is a technology-intensive product. Therefore, only in the case of large production volume of stamping parts, the advantages of stamping can be fully reflected, so as to obtain better economic benefits.
2, security issues
stamping processing also has some problems and shortcomings. Mainly in the punching process noise and vibration two kinds of pollution, and operator safety accidents occur from time to time. However, these problems are not entirely due to the stamping process and the mold itself, It is mainly due to the traditional stamping equipment and backward manual operation. With the advancement of science and technology, especially the development of computer technology, with the advancement of mechatronics technology, these problems will surely be resolved as soon as possible.
3, high-strength steel stamping
Today's high-strength steels and super-high-strength steels have achieved a very good weight reduction of vehicles and improved the collision strength and safety performance of vehicles. Therefore, they have become an important development direction for automotive steel products. However, with the increase of sheet strength, the traditional cold stamping process is prone to cracking during the forming process, and it cannot meet the processing requirements of high-strength steel plates. In the case that the molding conditions cannot be satisfied, hot stamping forming techniques for ultra-high-strength steel sheets have been gradually studied internationally. This technology is a new process that combines the forming, heat transfer, and tissue transformation. Mainly by using the high temperature austenite state, the plasticity of the sheet material is increased, and the yield strength is reduced, and the forming process is performed through the die. However, thermoforming requires in-depth research on process conditions, metal phase transitions, and CAE analysis technologies. Currently, this technology is monopolized by foreign manufacturers and domestic development is slow.
Solutions
In the past, in the production of deep-drawn or re-worked parts, everyone believed that pressure-resistant (EP) lubricants are the best choice for protecting the mold. Sulfur and chlorine EP additives have been mixed into pure oils to increase die life. However, with the advent of new metals, high-strength steels, strict environmental protection requirements, the value of EP oil-based lubricants has been reduced, and even lost the market.
In the molding of high-strength steel at high temperatures, EP oil-based lubricants lose their properties and cannot provide physical mold protection diaphragms in extreme temperature applications. The extremely high temperature type IRMCO high solid polymer lubricant can provide the necessary protection. As the metal is deformed in the stamping die and the temperature rises, the EP oil-based lubricating oil will become thinner, sometimes reaching a flash point or burning (smoke). IRMCO water based press lubricant spray up generally begins when much low consistency. As the temperature rises during the forming process, it becomes thicker and tougher. In fact, the high molecular polymer extreme temperature lubricant has a "heat-seeking property" and will stick to the metal to form a diaphragm which can reduce the friction. This protective barrier allows the work piece to be stretched to prevent friction and metal flow during the molding of the most demanding parts without cracking and sticking. Effectively protect the mold, prolong the service life of the mold, and increase the strength of the stamping.
Process classification
Stamping is mainly classified according to process and can be divided into two major categories: separation process and forming process.
The separation process is also referred to as blanking. Its purpose is to separate the stamped parts from the sheet material along a certain contour, and at the same time to ensure the quality requirements of the separation section.
The purpose of the forming process is to make the sheet plastically deform without breaking the blank to produce a workpiece of the desired shape and size.
In actual production, a variety of processes are often applied to one workpiece. Such as punching, bending, shearing, stretching, bulging, spinning, and rectification are several major stamping processes.
Separation process
Blanking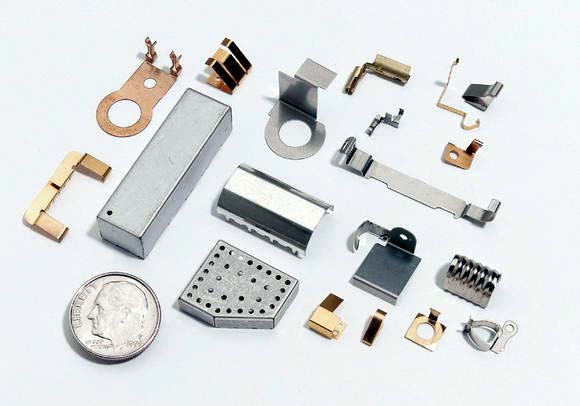
It is a basic stamping process that uses a mold to separate materials. It can be directly made into flat parts. Or prepare blanks for other stamping operations such as bending, deep drawing, forming, etc. It can also cut and trim the formed stamping parts. Punching is widely used in the automotive, home appliances, electronics, instrumentation, machinery, railways, communications, chemicals, light industry, textiles, and aerospace and other industrial sectors. Stamping processing accounts for about 50% to 60% of the entire stamping process.
Forming process
bending: A metal sheet, pipe and profiles bent at an angle, curvature and shape Plasticity molding method. Bending is one of the main processes widely used in the production of stampings. The bending of metal materials is essentially an elasto-plastic deformation process. After unloading, the workpiece will produce elastic deformation in the direction of recovery, called rebound. The impact of springback on the accuracy of the workpiece is the key technology that must be considered in the bending process.
Deep drawing is also called drawing or rolling. After using a die to make a punch, The resulting flat blank becomes a punching method of an open hollow part.
With the drawing process, cylindrical, stepped, tapered, spherical, box-shaped and other irregularly shaped thin-walled parts can be made.
If it cooperates with other press forming processes, it can also manufacture parts with extremely complex shapes.
In stamping production, there are many types of drawn parts. Because of its different geometrical characteristics, the location of the deformation zone, the nature of the deformation, the distribution of the deformation, and the stress state and distribution of the various parts of the billet have considerable, if not essential, differences. Therefore, the process parameters, number of processes and sequence determination methods and mold design principles and methods are not the same. According to the characteristics of deformation mechanics, various drawing parts can be divided into straight-wall rotating bodies (cylindrical pieces), straight-wall non-revolving bodies (box-shaped bodies), curved rotating bodies (curved-shaped parts) and curved non-revolving bodies, etc. Four types.
The pull-form applies tensile force to the sheet through a pull-type die, so that the sheet material produces uneven tensile stress and tensile strain. Then, the mating surface of the sheet material and the tension mold gradually expands until it completely fits the tension mold surface. The applicable object of the pull shape is mainly a certain plasticity of the manufacturing material. With a large surface area, the curvature changes gently and smoothly. High-quality double-curved skin (accurate shape, smooth streamline, stable quality). The pull shape is relatively simple due to the use of the process equipment and equipment used, so the cost is low and the flexibility is great; however, the material utilization rate and the productivity are low.

Flow forming is a metal rotary machining process. During the processing, the blank actively rotates with the flow forming die or the flow forming head rotates actively around the blank and the flow forming die. The flow forming head performs a feed movement with respect to the mandrel and the blank so that the blank is continuously deformed locally to obtain the desired hollow rotary part.
Shaping is the use of a given shape of the grinding tool to perform secondary trimming of the product's shape. Mainly reflected in the pressure plane, bouncing feet and so on. For some materials there is elasticity, can not guarantee the quality of a molding, the re-processing.
Flanging is a plastic processing method that bends the material of the narrow strip region of the edge of the prefabricated hole on the edge of the sheet blank or the billet into a vertical edge along a curve or a straight line. Flanging is mainly used to strengthen the edges of parts, cutting edge, make parts that are assembled and connected with other parts on parts, or have three-dimensional parts with complex specific shapes and reasonable space, and at the same time improve the rigidity of parts. It can also be used as a means to control cracks or wrinkles when forming large sheet metal. Therefore, it has been widely used in the automotive, aerospace, aerospace, electronics and household appliances industries.
Shrinkage is a stamping method that reduces the diameter of the open end of an already stretched non-flange hollow member or blank. Before and after the shrinkage, the diameter of the workpiece end should not be changed too much, otherwise the end material will wrinkle due to the intense deformation caused by the compression. Therefore, necks that have been reduced in size from a larger diameter to a smaller diameter often require multiple retractions.
Material
The surface and intrinsic properties of the stamping sheet have a great influence on the quality of the stamped product.
The requirements for stamping materials are:
1. Accurate and uniform thickness. Stamping die precision, small clearance, The excessive thickness of the sheet will increase the deformation force and cause the material to be stuck, or even crack the concave die. The thinning of sheet metal will affect the quality of finished products and even crack when drawing.
2. Smooth surface, no spots, no flaws, no scratches, no surface cracks. All surface defects will remain on the surface of the finished workpiece. Cracks may expand in the process of bending, deep drawing, and forming, resulting in waste.
3. Uniform yield strength, no obvious directionality. Anisotropy (see the plastic deformation of the sheet in the drawing process, such as deep drawing, flanging, bulging, etc., due to the emergence of anisotropic yielding, plastic deformation is inconsistent, will cause uneven deformation, so that the formation of inaccurate Defective or waste products.)
4. Uniform elongation is high. In the tensile test, the elongation before the thin neck phenomenon started at the specimen is called uniform elongation. During deep drawing, deformation of any area of the sheet material cannot exceed the uniform extension of the material, otherwise uneven deformation occurs.
5. Lower flexion ratio. The ratio of the material's yield limit to the strength limit is called the yield ratio. The low yield ratio can not only reduce the deformation resistance, but also reduce the tendency of wrinkling during deep drawing, reduce the springback after bending, and improve the accuracy of the bending part.
6, Low work hardening. The work hardening that occurs after cold deformation will increase the deformation resistance of the material and make it difficult to continue deformation, so generally low-hardening index sheets are used. The material with high hardening index has good plastic deformation stability (ie uniform plastic deformation), and local cracking is not easy to occur.
In actual production, process tests similar to the stamping process are commonly used. Such as deep-drawing performance test, bulging performance test and other test material stamping performance, in order to ensure the quality of finished products and high pass rate.
Dies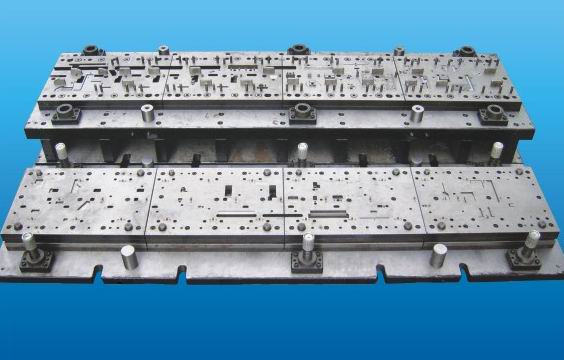
The precision and structure of the die directly affect the forming and precision of the stampings. Mold manufacturing cost and life are important factors affecting the cost and quality of stamping parts. More time is required for mold design and manufacturing, which extends the production lead time for new stampings. Die holder, die carrier, guiding element standardization and development of simple molds (for small batch production), Compound mold, multi-position progressive die (for mass production), The development of a quick mold changing device can reduce the amount of preparation work required for stamping and shorten the preparation time. The advanced stamping technology suitable for mass production can be reasonably applied to small batch and multi-variety production.
Professional setting
Apart from the forming of thick plate hydraulic press, mechanical press is usually used. Focused on modern high-speed multi-station mechanical presses, by configuring the machines such as uncoiling, leveling, product collection, and conveying, and the mold library and quick mold changing device, and using computer program control, a high-productivity automatic punching line can be formed.
lubricating
The general workpiece is in the stamping process. In the stamping process, especially during the cold forging stamping process, the temperature will rise rapidly and lubrication must be added. If direct stamping without lubrication is used, the life of the mold will be shortened and the precision will be reduced, in addition to the influence of the workpiece finish, and this will bring a lot of costs for the improvement of the mold. It is for this reason that stamping lubrication must be used in cold forging stamping.
Safe Production
In the case of producing tens or hundreds of stamped parts per minute, In the short period of time to complete the feeding, stamping, out of the pieces, waste and other processes, often personal, equipment and quality accidents.
Therefore, safe production in stamping is a very important issue. Stamping safety measures are:
1. To achieve mechanization, automatic feeding and discharging.
2. Set up mechanical guards to prevent hand injuries. Application of mold shield, automatic return device and manual tools for incoming and unloading.
3. Set up electrical protection and power off device. Set photoelectric or air curtain protection switch, two-handed or multi-manual series start switch, anti-misoperation device.
4. Improve the clutch and brake structure. After the danger signal is issued, the crankshaft, connecting rod and punch of the press can be immediately stopped in place.
Stamping is the application of external forces to plates, strips, tubes and profiles by presses and dies. Plastic deformation or separation to obtain the shape and size of the workpiece (stamping) forming processing methods. Stamping and forging are plastic processing (or pressure processing), collectively known as forging. Stamped blanks are mainly hot-rolled and cold-rolled steel sheets and strips. Of the steel in the world, 60 to 70% are plate materials, most of which are stamped into products. The car's body, chassis, fuel tanks, radiators, boiler steam drums, container shells, electric motors, and electrical appliances such as iron core silicon steel sheets are stamped and processed. There are also a large number of stamping parts in products such as instrumentation, household appliances, bicycles, office machinery, and household utensils.
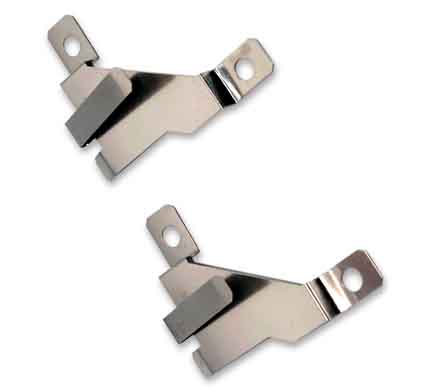
Stamping is the use of conventional or special press equipment power, so that the sheet material in the mold directly by the deformation force, and deformation, the production technology of product parts with certain shape, size and performance is obtained.
Sheets, moulds and equipment are the three elements of stamping.
Stamping temperature is divided into hot stamping and cold stamping.
The former is suitable for sheet material processing with high deformation resistance and poor plasticity;
The latter is performed at room temperature and is a commonly used stamping method for thin plates. It is one of the main methods of metal plastic processing (or pressure processing), and it is also affiliated with material forming engineering technology.
The die used for punching is referred to as die. Dies are special tools for the batch processing of materials (metal or non-metal) into the required stampings. Die is very important in stamping, there is no die that meets the requirements, batch stamping production is difficult to carry out; Without advanced dies, advanced stamping processes cannot be realized. Stamping processes and dies, stamping equipment and stamping materials constitute the three elements of stamping. Only when they are combined can stampings be obtained.
Stamping industry
The stamping industry is an industry that involves a very wide range of industries. It penetrates into all aspects of the manufacturing industry. In foreign countries, stamping is called sheet forming. In our country also has called it.
What is the status of China's stamping industry? The development of foreign stamping, This is a matter of concern to all of us. The vigorous development of stamping should be attributed to the development of daily necessities for automobiles, aircraft and household appliances.
Technology level
The stampings market is very imperfect and sound. However, the small stamping parts market is very mature in some areas in the south. Judging from the current situation, China's stamping parts market has the following problems:
(1) some of the production capacity oversupply.
(2) The market for household electrical appliances and electrical stamping parts is fiercely competitive. However, there are not many companies that have international competitiveness.
(3) The overall level is low and there is a lack of high-grade technologies. Slow technological progress.
(4) The level of material technology, mold technology, lubrication technology, and equipment are all at a relatively low level, far from meeting the needs of domestic production and development.
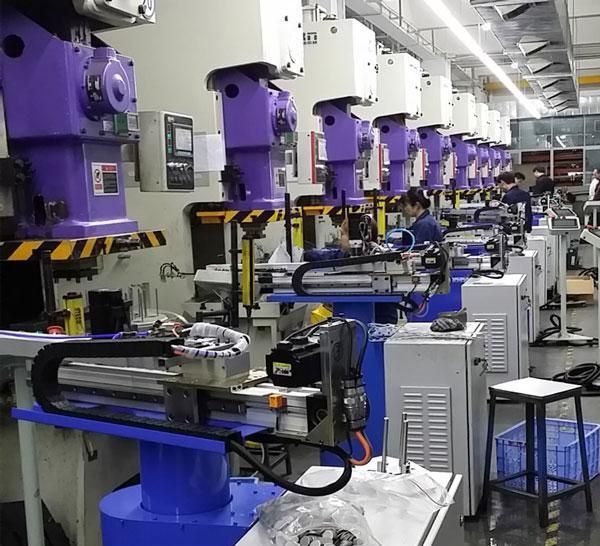
Processing features
Compared with castings and forgings, stampings are thin, uniform, light and strong. Stamping can produce processes that are difficult for other equipment to manufacture, such as workpieces with stiffeners, ribs, undulations, or flanging, to increase their rigidity.
Due to the use of precision molds, the accuracy of the workpiece can reach up to micrometers, and the repeat accuracy and specifications are consistent. Can be punched out of hole, bump and so on.
Cold stampings are generally no longer cut, or require only a small amount of cutting. The accuracy and surface condition of hot stamping parts are lower than those of cold stamping parts, but they are still better than castings and forgings, and the amount of machining is small.
Stamping is an efficient production method using composite molds, especially multi-position progressive molds. It can complete multiple stamping processes on one press (single station or multi-station) to realize full-automatic production from unwinding, leveling, blanking, forming and finishing. With high production efficiency, good working conditions and low production costs, it can produce hundreds of pieces per minute. Compared with other methods of mechanical processing and plastic processing, stamping has many unique advantages both technically and economically.
The main performance is as follows:
(1) The stamping process has high production efficiency, convenient operation and easy realization of mechanization and automation. This is because stamping is done by means of die and stamping equipment. The number of strokes of ordinary presses can reach tens of times per minute, and the high-speed pressure can reach hundreds of times or even more than 1,000 times per minute. And each punching stroke can get a punching piece.
(2) Since the die ensures the dimensional and shape accuracy of the stamping part during stamping, and generally does not damage the surface quality of the stamping part, The die life is generally longer, so the stamping quality is stable, interchangeability is good, with the "identical" feature.
(3) Stamping can process parts with a wide range of sizes and complex shapes.
Such as stopwatches as small as clocks, as large as car longitudinal beams, coverings, etc. In addition to the cold deformation hardening effect of the material during stamping, the stamping strength and stiffness are both high.
(4) Stamping generally does not generate scraps, material consumption is less, and no other heating equipment is required. Therefore, it is a saving material and energy-saving processing method, and the cost of stamping parts is low.
Due to the superiority of stamping, stamping processing has a wide range of applications in various fields of the national economy. For example, there are stamping and processing in aerospace, aviation, military, machinery, agricultural machinery, electronics, information, railways, post and telecommunications, transportation, chemicals, medical equipment, household appliances and light industry. Not only is it used by the entire industry, but everyone has direct contact with stamping products. There are many large, medium and small stampings on airplanes, trains, cars and tractors. The car body, frame and rim are all stamped out. According to relevant survey statistics, 80% of bicycles, sewing machines, and watches are stampings; 90% of televisions, tape recorders, and cameras are stampings; There are also food metal shells, steel refining boilers, enamel bowls and stainless steel cutlery, all of which are stamping products using moulds; Even the computer's hardware can not lack stampings parts.
Attention problem
1, mold problems
The molds used for stamping and processing are generally specialized. Sometimes a complex part requires several sets of molds to be processed and formed. The precision of mold manufacturing is high and the technical requirements are high. It is a technology-intensive product. Therefore, only in the case of large production volume of stamping parts, the advantages of stamping can be fully reflected, so as to obtain better economic benefits.
2, security issues
stamping processing also has some problems and shortcomings. Mainly in the punching process noise and vibration two kinds of pollution, and operator safety accidents occur from time to time. However, these problems are not entirely due to the stamping process and the mold itself, It is mainly due to the traditional stamping equipment and backward manual operation. With the advancement of science and technology, especially the development of computer technology, with the advancement of mechatronics technology, these problems will surely be resolved as soon as possible.
3, high-strength steel stamping
Today's high-strength steels and super-high-strength steels have achieved a very good weight reduction of vehicles and improved the collision strength and safety performance of vehicles. Therefore, they have become an important development direction for automotive steel products. However, with the increase of sheet strength, the traditional cold stamping process is prone to cracking during the forming process, and it cannot meet the processing requirements of high-strength steel plates. In the case that the molding conditions cannot be satisfied, hot stamping forming techniques for ultra-high-strength steel sheets have been gradually studied internationally. This technology is a new process that combines the forming, heat transfer, and tissue transformation. Mainly by using the high temperature austenite state, the plasticity of the sheet material is increased, and the yield strength is reduced, and the forming process is performed through the die. However, thermoforming requires in-depth research on process conditions, metal phase transitions, and CAE analysis technologies. Currently, this technology is monopolized by foreign manufacturers and domestic development is slow.
Solutions
In the past, in the production of deep-drawn or re-worked parts, everyone believed that pressure-resistant (EP) lubricants are the best choice for protecting the mold. Sulfur and chlorine EP additives have been mixed into pure oils to increase die life. However, with the advent of new metals, high-strength steels, strict environmental protection requirements, the value of EP oil-based lubricants has been reduced, and even lost the market.
In the molding of high-strength steel at high temperatures, EP oil-based lubricants lose their properties and cannot provide physical mold protection diaphragms in extreme temperature applications. The extremely high temperature type IRMCO high solid polymer lubricant can provide the necessary protection. As the metal is deformed in the stamping die and the temperature rises, the EP oil-based lubricating oil will become thinner, sometimes reaching a flash point or burning (smoke). IRMCO water based press lubricant spray up generally begins when much low consistency. As the temperature rises during the forming process, it becomes thicker and tougher. In fact, the high molecular polymer extreme temperature lubricant has a "heat-seeking property" and will stick to the metal to form a diaphragm which can reduce the friction. This protective barrier allows the work piece to be stretched to prevent friction and metal flow during the molding of the most demanding parts without cracking and sticking. Effectively protect the mold, prolong the service life of the mold, and increase the strength of the stamping.
Process classification
Stamping is mainly classified according to process and can be divided into two major categories: separation process and forming process.
The separation process is also referred to as blanking. Its purpose is to separate the stamped parts from the sheet material along a certain contour, and at the same time to ensure the quality requirements of the separation section.
The purpose of the forming process is to make the sheet plastically deform without breaking the blank to produce a workpiece of the desired shape and size.
In actual production, a variety of processes are often applied to one workpiece. Such as punching, bending, shearing, stretching, bulging, spinning, and rectification are several major stamping processes.
Separation process
Blanking
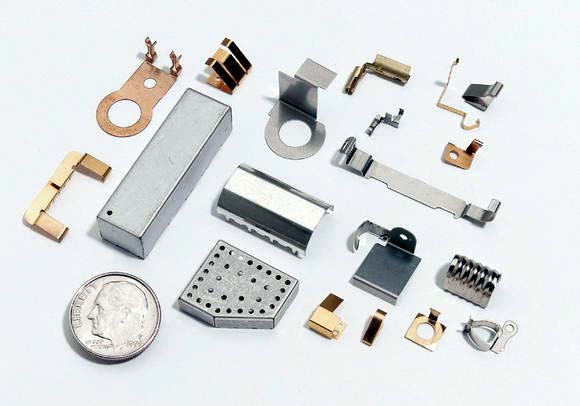
It is a basic stamping process that uses a mold to separate materials. It can be directly made into flat parts. Or prepare blanks for other stamping operations such as bending, deep drawing, forming, etc. It can also cut and trim the formed stamping parts. Punching is widely used in the automotive, home appliances, electronics, instrumentation, machinery, railways, communications, chemicals, light industry, textiles, and aerospace and other industrial sectors. Stamping processing accounts for about 50% to 60% of the entire stamping process.
Forming process
bending: A metal sheet, pipe and profiles bent at an angle, curvature and shape Plasticity molding method. Bending is one of the main processes widely used in the production of stampings. The bending of metal materials is essentially an elasto-plastic deformation process. After unloading, the workpiece will produce elastic deformation in the direction of recovery, called rebound. The impact of springback on the accuracy of the workpiece is the key technology that must be considered in the bending process.
Deep drawing is also called drawing or rolling. After using a die to make a punch, The resulting flat blank becomes a punching method of an open hollow part.
With the drawing process, cylindrical, stepped, tapered, spherical, box-shaped and other irregularly shaped thin-walled parts can be made.
If it cooperates with other press forming processes, it can also manufacture parts with extremely complex shapes.
In stamping production, there are many types of drawn parts. Because of its different geometrical characteristics, the location of the deformation zone, the nature of the deformation, the distribution of the deformation, and the stress state and distribution of the various parts of the billet have considerable, if not essential, differences. Therefore, the process parameters, number of processes and sequence determination methods and mold design principles and methods are not the same. According to the characteristics of deformation mechanics, various drawing parts can be divided into straight-wall rotating bodies (cylindrical pieces), straight-wall non-revolving bodies (box-shaped bodies), curved rotating bodies (curved-shaped parts) and curved non-revolving bodies, etc. Four types.
The pull-form applies tensile force to the sheet through a pull-type die, so that the sheet material produces uneven tensile stress and tensile strain. Then, the mating surface of the sheet material and the tension mold gradually expands until it completely fits the tension mold surface. The applicable object of the pull shape is mainly a certain plasticity of the manufacturing material. With a large surface area, the curvature changes gently and smoothly. High-quality double-curved skin (accurate shape, smooth streamline, stable quality). The pull shape is relatively simple due to the use of the process equipment and equipment used, so the cost is low and the flexibility is great; however, the material utilization rate and the productivity are low.

Flow forming is a metal rotary machining process. During the processing, the blank actively rotates with the flow forming die or the flow forming head rotates actively around the blank and the flow forming die. The flow forming head performs a feed movement with respect to the mandrel and the blank so that the blank is continuously deformed locally to obtain the desired hollow rotary part.
Shaping is the use of a given shape of the grinding tool to perform secondary trimming of the product's shape. Mainly reflected in the pressure plane, bouncing feet and so on. For some materials there is elasticity, can not guarantee the quality of a molding, the re-processing.
Flanging is a plastic processing method that bends the material of the narrow strip region of the edge of the prefabricated hole on the edge of the sheet blank or the billet into a vertical edge along a curve or a straight line. Flanging is mainly used to strengthen the edges of parts, cutting edge, make parts that are assembled and connected with other parts on parts, or have three-dimensional parts with complex specific shapes and reasonable space, and at the same time improve the rigidity of parts. It can also be used as a means to control cracks or wrinkles when forming large sheet metal. Therefore, it has been widely used in the automotive, aerospace, aerospace, electronics and household appliances industries.
Shrinkage is a stamping method that reduces the diameter of the open end of an already stretched non-flange hollow member or blank. Before and after the shrinkage, the diameter of the workpiece end should not be changed too much, otherwise the end material will wrinkle due to the intense deformation caused by the compression. Therefore, necks that have been reduced in size from a larger diameter to a smaller diameter often require multiple retractions.
Material
The surface and intrinsic properties of the stamping sheet have a great influence on the quality of the stamped product.
The requirements for stamping materials are:
1. Accurate and uniform thickness. Stamping die precision, small clearance, The excessive thickness of the sheet will increase the deformation force and cause the material to be stuck, or even crack the concave die. The thinning of sheet metal will affect the quality of finished products and even crack when drawing.
2. Smooth surface, no spots, no flaws, no scratches, no surface cracks. All surface defects will remain on the surface of the finished workpiece. Cracks may expand in the process of bending, deep drawing, and forming, resulting in waste.
3. Uniform yield strength, no obvious directionality. Anisotropy (see the plastic deformation of the sheet in the drawing process, such as deep drawing, flanging, bulging, etc., due to the emergence of anisotropic yielding, plastic deformation is inconsistent, will cause uneven deformation, so that the formation of inaccurate Defective or waste products.)
4. Uniform elongation is high. In the tensile test, the elongation before the thin neck phenomenon started at the specimen is called uniform elongation. During deep drawing, deformation of any area of the sheet material cannot exceed the uniform extension of the material, otherwise uneven deformation occurs.
5. Lower flexion ratio. The ratio of the material's yield limit to the strength limit is called the yield ratio. The low yield ratio can not only reduce the deformation resistance, but also reduce the tendency of wrinkling during deep drawing, reduce the springback after bending, and improve the accuracy of the bending part.
6, Low work hardening. The work hardening that occurs after cold deformation will increase the deformation resistance of the material and make it difficult to continue deformation, so generally low-hardening index sheets are used. The material with high hardening index has good plastic deformation stability (ie uniform plastic deformation), and local cracking is not easy to occur.
In actual production, process tests similar to the stamping process are commonly used. Such as deep-drawing performance test, bulging performance test and other test material stamping performance, in order to ensure the quality of finished products and high pass rate.
Dies
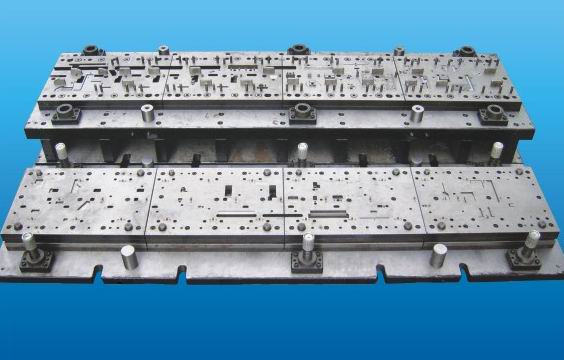
The precision and structure of the die directly affect the forming and precision of the stampings. Mold manufacturing cost and life are important factors affecting the cost and quality of stamping parts. More time is required for mold design and manufacturing, which extends the production lead time for new stampings. Die holder, die carrier, guiding element standardization and development of simple molds (for small batch production), Compound mold, multi-position progressive die (for mass production), The development of a quick mold changing device can reduce the amount of preparation work required for stamping and shorten the preparation time. The advanced stamping technology suitable for mass production can be reasonably applied to small batch and multi-variety production.
Apart from the forming of thick plate hydraulic press, mechanical press is usually used. Focused on modern high-speed multi-station mechanical presses, by configuring the machines such as uncoiling, leveling, product collection, and conveying, and the mold library and quick mold changing device, and using computer program control, a high-productivity automatic punching line can be formed.
lubricating
The general workpiece is in the stamping process. In the stamping process, especially during the cold forging stamping process, the temperature will rise rapidly and lubrication must be added. If direct stamping without lubrication is used, the life of the mold will be shortened and the precision will be reduced, in addition to the influence of the workpiece finish, and this will bring a lot of costs for the improvement of the mold. It is for this reason that stamping lubrication must be used in cold forging stamping.
Safe Production
In the case of producing tens or hundreds of stamped parts per minute, In the short period of time to complete the feeding, stamping, out of the pieces, waste and other processes, often personal, equipment and quality accidents.
Therefore, safe production in stamping is a very important issue. Stamping safety measures are:
1. To achieve mechanization, automatic feeding and discharging.
2. Set up mechanical guards to prevent hand injuries. Application of mold shield, automatic return device and manual tools for incoming and unloading.
3. Set up electrical protection and power off device. Set photoelectric or air curtain protection switch, two-handed or multi-manual series start switch, anti-misoperation device.
4. Improve the clutch and brake structure. After the danger signal is issued, the crankshaft, connecting rod and punch of the press can be immediately stopped in place.