Stainless Steel Turning Method and Several Main Setting Parameters
Key words:Stainless Steel Turning Method, Tool Material, Tool Parameters, Cutting Amount, Coating Tool
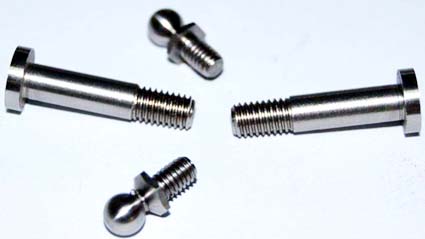
The currently applied stainless steel is mainly divided into martensitic stainless steel, ferritic stainless steel and austenitic stainless steel according to its state of organization. The alloy steel containing more than 11.7% chromium or more than 8% nickel is often called stainless steel. The addition of more metallic elements (Cr and Ni) to the alloy steel grade changes the physical and chemical properties of the alloy. Enhanced corrosion resistance, both in air and in acid solution, are not susceptible to oxidative rust and still have higher strength at higher temperatures (>450 ° C). Therefore, it is widely used in aviation, aerospace, chemical, petroleum, construction and food industries and daily life.
1. The main cutting characteristics of stainless steel
(1) Large cutting force
Among them, austenitic stainless steel is particularly prominent. Although the hardness of this material is not high, the grade 1Cr18Ni9Ti is taken as an example, its hardness is ≤187HBW, but the plasticity is very good (elongation after fracture δ=40%, reduction of area Ψ=60%). Therefore, the plastic deformation is large during the cutting process, and the cutting force is increased. When the cutting parameters are the same, the energy consumption of austenitic stainless steel is about 50% higher than that of low carbon steel.
(2) Serious work hardening
In stainless steel, the work hardening phenomenon of austenitic and austenitic ferritic stainless steel is the most prominent. They are plastically large, and the lattice is strongly twisted when plastically deformed; At the same time, the austenite has poor stability, and some austenite transforms into martensite under the action of cutting force; Further, compound impurities are easy to decompose and distribute dispersedly under the action of cutting heat, resulting in hardening layer in cutting process. All of this makes the work hardening phenomenon more obvious.
(3) The tool is prone to adhesion and wear
Stainless steel materials produce high temperatures during the cutting process and have a high affinity with the tool material.
It makes the tool and material bond and diffuse, and it is easy to form "knife tumors", which causes the tool adhesion and wear, and reduces the service life of the tool.
(4) The local temperature in the cutting zone is high
This type of material requires a large cutting force, and the power consumed by the separation and cutting is also large, resulting in more cutting heat. The heat transferred into the tool can reach 20%, while only 9% when processing carbon steel. At the same time, the thermal conductivity of stainless steel is not good (the thermal conductivity of stainless steel is about 1/3 of that of carbon steel). A large amount of cutting heat is concentrated on the interface between the cutting zone and the blade-to-chip contact, so that the local temperature of the cutting zone is high.
2. Selection of tool materials
According to the cutting characteristics of the aforementioned stainless steel, the tool material is required to have good heat resistance, high wear resistance, and small affinity with stainless steel. Currently used tool materials are cemented carbide, high speed steel and coated tools.
(1) Carbide tool
In general, YG-based carbide machining tools are preferred for most difficult-to-machine materials. It is best not to use YT type hard alloys, especially when processing 1Cr18Ni9Ti austenitic stainless steel, YT type hard alloy should be absolutely avoided. Since titanium (Ti) in stainless steel and Ti in the YT-based cemented carbide have an affinity, the cutting tends to take away the Ti in the alloy, which causes the tool wear to be intensified. YG cemented carbide has good toughness, high wear resistance and hardness. It is more suitable for the processing of stainless steel materials. It can adopt a larger front angle to make the cutting lighter. Thermal conductivity is also good; At the same time, the chip and the tool are not easy to bond.
(2) high speed steel tool
When the shape, size and structure of the workpiece are inconvenient to use cemented carbide cutter, or the cemented carbide cutter is easy to damage. High-performance high-speed steel tools are required. Ordinary high-speed steel (such as W18Cr4V, etc.) has a very low tool life and does not meet the requirements.
New high-speed steel cutting tools may be employed: Such as cobalt-containing high-speed steel (W2Mo9Cr4Vco8), aluminum-containing super-hard high-speed steel (W6Mo5Cr4V2Al), nitrogen-containing high-speed steel (W12Mo3Cr4V3N) and so on.
(3) New tool material coating tool
Chemical vapor deposition (CVD) or physical vapor deposition (PVD) methods are employed. A tool material obtained by substantially coating a thin layer of a highly wear-resistant, insoluble metal (or non-metallic) compound in a cemented carbide or other material tool. The coating of the coated tool prevents direct contact between the chip and the tool, reduces friction and reduces various mechanical thermal stresses. The use of coated tools can reduce cutting time, reduce costs, reduce the number of tool changes, improve machining accuracy, and long tool life. Coated tools reduce or eliminate the use of cutting fluids.
3 Determination of tool parameters
Reasonable selection of prop parameters is very important to improve tool life and workpiece quality. Under the premise of ensuring that the knife has sufficient strength and strives to avoid the edge, the larger rake angle should be used, which not only reduces the cutting force and cutting temperature, but also reduces the hardening depth. The front angle of turning various stainless steels is generally 12°-13°. Under the premise of ensuring sufficient tools, a larger relief angle should be chosen. Generally take 10 ° -20 °. It is also possible to use a negative chamfer on the main cutting edge to strengthen the head to improve the wear resistance of the tool. Due to the toughness and plasticity of stainless steel, it is difficult to break the chip during cutting. The method of forcing deformation is mainly to reasonably select the parameters and cutting amount of the chip breaker on the rake face. On the basis of reasonable choice of cutting amount, we generally adopt the method of double-edge inclination plus external slanting chip flute. The outer turning tool grinds the double-edged angle to make the chip surface face-shaped. The outer slanting arc-shaped chip flutes are sharpened on the knives of the cutters, so that the chips are curled into the pagoda-like coils or the short-tight spiral coils along the guide flute. When processing stainless steel, the adhesion of the chips to the cutter is strong, and the built-up edge is likely to occur. Therefore, the front and back flank and cutting edge of the tool should have a small surface roughness value to reduce the cutting resistance. Reduce cutting adhesion and improve tool life.
4. Cutting amount
(1) Cutting speed v
In order to ensure a reasonable tool life, the cutting speed can be reduced. Generally, the cutting speed can be 40%-60% of ordinary carbon steel when cutting stainless steel.
(2) Feed rate f
In order to improve the quality of the machined surface, it is advisable to use a smaller value for the feed.
(3) Cutting depth AP
(4) Generally, ap=2-5mm can be selected for roughing, and ap=0/2-0.5mm for finishing.
The amount of cutting process of stainless steel
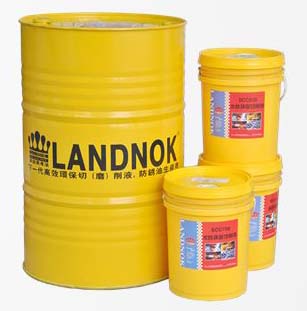
5, cutting fluid
Due to the poor machinability of stainless steel and the high temperature in the cutting zone, the cutting fluid is required to have high cooling performance, lubricating performance and permeability. In order to enhance the cooling effect, high pressure spraying or oil mist cooling may be employed.
Commonly used cutting fluids are:
(1) Sulfurized oil: It has certain cooling performance and lubricating performance, and has abundant sources and low cost.
(2) Carbon tetrachloride + mineral oil or other oils: The addition of carbon tetrachloride to mineral oil or other oils greatly improves the permeability of the cutting fluid, especially due to the finishing of stainless steel materials.
6. Examples
In the CNC lathe rough 1Cr18Ni9Ti stainless steel shaft parts (diameter 60mm). With coated cutter, the cutting speed n=800r/min backing knife amount ap=0.7-1mm, the feeding amount f=0.2-0.3mm/r, the cutting is light and the chip breaking is good. Tool wear is less, and one blade can be processed continuously for more than 4 hours, saving time for tool change. At the same time, I use the used blades of the finished car for roughing, which can save the cost of the tool and save energy by secondary use of the blade to achieve the same effect.
7. Conclusion
Based on the above, the basic principles of turning stainless steel materials are:
Tool materials are made of tough, high-strength carbide or coated tools. Tool parameters should be as reasonable as possible and sharpen the tool as sharply as possible. It is easy to curl and break the chips, and the cutting amount should be appropriate and the cutting fluid supply should be sufficient. The relevant measures should be used as much as possible. When using coated tools, it is reasonable to use turning elements. Through multiple trials, batch processing of coated tools is even better, and the processing efficiency of ordinary lathes is more than five times higher than before.
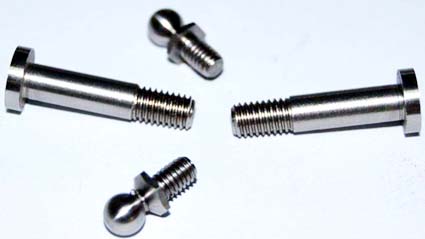
The currently applied stainless steel is mainly divided into martensitic stainless steel, ferritic stainless steel and austenitic stainless steel according to its state of organization. The alloy steel containing more than 11.7% chromium or more than 8% nickel is often called stainless steel. The addition of more metallic elements (Cr and Ni) to the alloy steel grade changes the physical and chemical properties of the alloy. Enhanced corrosion resistance, both in air and in acid solution, are not susceptible to oxidative rust and still have higher strength at higher temperatures (>450 ° C). Therefore, it is widely used in aviation, aerospace, chemical, petroleum, construction and food industries and daily life.
1. The main cutting characteristics of stainless steel
(1) Large cutting force
Among them, austenitic stainless steel is particularly prominent. Although the hardness of this material is not high, the grade 1Cr18Ni9Ti is taken as an example, its hardness is ≤187HBW, but the plasticity is very good (elongation after fracture δ=40%, reduction of area Ψ=60%). Therefore, the plastic deformation is large during the cutting process, and the cutting force is increased. When the cutting parameters are the same, the energy consumption of austenitic stainless steel is about 50% higher than that of low carbon steel.
(2) Serious work hardening
In stainless steel, the work hardening phenomenon of austenitic and austenitic ferritic stainless steel is the most prominent. They are plastically large, and the lattice is strongly twisted when plastically deformed; At the same time, the austenite has poor stability, and some austenite transforms into martensite under the action of cutting force; Further, compound impurities are easy to decompose and distribute dispersedly under the action of cutting heat, resulting in hardening layer in cutting process. All of this makes the work hardening phenomenon more obvious.
(3) The tool is prone to adhesion and wear
Stainless steel materials produce high temperatures during the cutting process and have a high affinity with the tool material.
It makes the tool and material bond and diffuse, and it is easy to form "knife tumors", which causes the tool adhesion and wear, and reduces the service life of the tool.
(4) The local temperature in the cutting zone is high
This type of material requires a large cutting force, and the power consumed by the separation and cutting is also large, resulting in more cutting heat. The heat transferred into the tool can reach 20%, while only 9% when processing carbon steel. At the same time, the thermal conductivity of stainless steel is not good (the thermal conductivity of stainless steel is about 1/3 of that of carbon steel). A large amount of cutting heat is concentrated on the interface between the cutting zone and the blade-to-chip contact, so that the local temperature of the cutting zone is high.
2. Selection of tool materials
According to the cutting characteristics of the aforementioned stainless steel, the tool material is required to have good heat resistance, high wear resistance, and small affinity with stainless steel. Currently used tool materials are cemented carbide, high speed steel and coated tools.
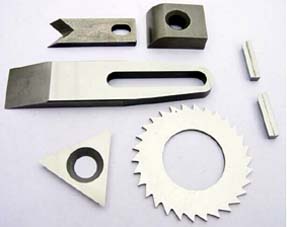
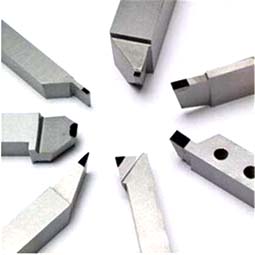
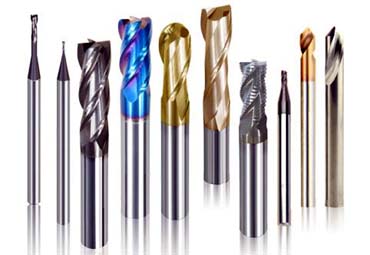
(1) Carbide tool
In general, YG-based carbide machining tools are preferred for most difficult-to-machine materials. It is best not to use YT type hard alloys, especially when processing 1Cr18Ni9Ti austenitic stainless steel, YT type hard alloy should be absolutely avoided. Since titanium (Ti) in stainless steel and Ti in the YT-based cemented carbide have an affinity, the cutting tends to take away the Ti in the alloy, which causes the tool wear to be intensified. YG cemented carbide has good toughness, high wear resistance and hardness. It is more suitable for the processing of stainless steel materials. It can adopt a larger front angle to make the cutting lighter. Thermal conductivity is also good; At the same time, the chip and the tool are not easy to bond.
(2) high speed steel tool
When the shape, size and structure of the workpiece are inconvenient to use cemented carbide cutter, or the cemented carbide cutter is easy to damage. High-performance high-speed steel tools are required. Ordinary high-speed steel (such as W18Cr4V, etc.) has a very low tool life and does not meet the requirements.
New high-speed steel cutting tools may be employed: Such as cobalt-containing high-speed steel (W2Mo9Cr4Vco8), aluminum-containing super-hard high-speed steel (W6Mo5Cr4V2Al), nitrogen-containing high-speed steel (W12Mo3Cr4V3N) and so on.
(3) New tool material coating tool
Chemical vapor deposition (CVD) or physical vapor deposition (PVD) methods are employed. A tool material obtained by substantially coating a thin layer of a highly wear-resistant, insoluble metal (or non-metallic) compound in a cemented carbide or other material tool. The coating of the coated tool prevents direct contact between the chip and the tool, reduces friction and reduces various mechanical thermal stresses. The use of coated tools can reduce cutting time, reduce costs, reduce the number of tool changes, improve machining accuracy, and long tool life. Coated tools reduce or eliminate the use of cutting fluids.
3 Determination of tool parameters
Reasonable selection of prop parameters is very important to improve tool life and workpiece quality. Under the premise of ensuring that the knife has sufficient strength and strives to avoid the edge, the larger rake angle should be used, which not only reduces the cutting force and cutting temperature, but also reduces the hardening depth. The front angle of turning various stainless steels is generally 12°-13°. Under the premise of ensuring sufficient tools, a larger relief angle should be chosen. Generally take 10 ° -20 °. It is also possible to use a negative chamfer on the main cutting edge to strengthen the head to improve the wear resistance of the tool. Due to the toughness and plasticity of stainless steel, it is difficult to break the chip during cutting. The method of forcing deformation is mainly to reasonably select the parameters and cutting amount of the chip breaker on the rake face. On the basis of reasonable choice of cutting amount, we generally adopt the method of double-edge inclination plus external slanting chip flute. The outer turning tool grinds the double-edged angle to make the chip surface face-shaped. The outer slanting arc-shaped chip flutes are sharpened on the knives of the cutters, so that the chips are curled into the pagoda-like coils or the short-tight spiral coils along the guide flute. When processing stainless steel, the adhesion of the chips to the cutter is strong, and the built-up edge is likely to occur. Therefore, the front and back flank and cutting edge of the tool should have a small surface roughness value to reduce the cutting resistance. Reduce cutting adhesion and improve tool life.
4. Cutting amount
(1) Cutting speed v
In order to ensure a reasonable tool life, the cutting speed can be reduced. Generally, the cutting speed can be 40%-60% of ordinary carbon steel when cutting stainless steel.
(2) Feed rate f
In order to improve the quality of the machined surface, it is advisable to use a smaller value for the feed.
(3) Cutting depth AP
(4) Generally, ap=2-5mm can be selected for roughing, and ap=0/2-0.5mm for finishing.
The amount of cutting process of stainless steel
Name | v/m.min | f/mm.r | Ap/mm | Tool |
Truning outer circle | 40-120 | 0.1-0.5 | 0.2-1 | Coated tool |
Boring hole | 40-100 | 0.1-0.5 | 0.1-0.4 | Coated tool |
cut off | 40-100 | 0.1-0.25 | Coated tool | |
Truning thread | 20-50 | 0.1-1 | Coated tool | |
drill hole | 12-20 | 0.1-0.25 | High-speed steel cutting tools | |
Reaming | 8-18 | 0.1-0.4 | 0.1-1 | High-speed steel cutting tools |
Hinged hole | 2.5-5 | 0.1-0.2 | 0.1-1 | High-speed steel cutting tools |
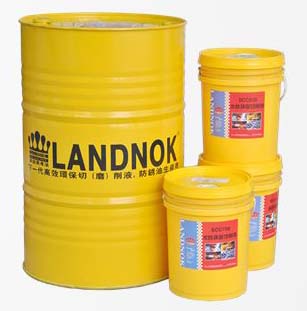
5, cutting fluid
Due to the poor machinability of stainless steel and the high temperature in the cutting zone, the cutting fluid is required to have high cooling performance, lubricating performance and permeability. In order to enhance the cooling effect, high pressure spraying or oil mist cooling may be employed.
Commonly used cutting fluids are:
(1) Sulfurized oil: It has certain cooling performance and lubricating performance, and has abundant sources and low cost.
(2) Carbon tetrachloride + mineral oil or other oils: The addition of carbon tetrachloride to mineral oil or other oils greatly improves the permeability of the cutting fluid, especially due to the finishing of stainless steel materials.
6. Examples
In the CNC lathe rough 1Cr18Ni9Ti stainless steel shaft parts (diameter 60mm). With coated cutter, the cutting speed n=800r/min backing knife amount ap=0.7-1mm, the feeding amount f=0.2-0.3mm/r, the cutting is light and the chip breaking is good. Tool wear is less, and one blade can be processed continuously for more than 4 hours, saving time for tool change. At the same time, I use the used blades of the finished car for roughing, which can save the cost of the tool and save energy by secondary use of the blade to achieve the same effect.
7. Conclusion
Based on the above, the basic principles of turning stainless steel materials are:
Tool materials are made of tough, high-strength carbide or coated tools. Tool parameters should be as reasonable as possible and sharpen the tool as sharply as possible. It is easy to curl and break the chips, and the cutting amount should be appropriate and the cutting fluid supply should be sufficient. The relevant measures should be used as much as possible. When using coated tools, it is reasonable to use turning elements. Through multiple trials, batch processing of coated tools is even better, and the processing efficiency of ordinary lathes is more than five times higher than before.