Machining accuracy and assembly lead to high motor bearing temperature
Since the bearings are widely used in three-phase asynchronous motors, there are not many failures of the three-phase asynchronous motors caused by the bearings. The fault of the motor bearing is mostly caused by overheating of the bearing. Let's explore how to discriminate motor bearings from overheating and malfunctions and solutions.
First, the motor bearing overheating
At present, the motor manufacturer's bearing temperature before the motor leaves the factory is an item that must be checked. In addition to the high temperature not exceeding the 95 °C limit, there is no uniform standard for the high temperature of the bearing below the high temperature during operation. According to the general habit, after the motor runs for 1.5-2 hours, the bearing temperature is stable and the temperature rises ≤35K, which can be considered normal. However, when the bearing runs for a short time (such as 15min) and rises to 65°C or runs for more than 1.5h, it still has no downward trend, and less than 1.5h but the bearing stable temperature exceeds 75°C. Both can be considered as high bearing temperatures (65 ° C, 75 ° C for summer, 55 ° C, 65 ° C in cold winter).
Second, the failure phenomenon and solution
1. The bearing is squeezed
Balls or rollers can be easily rotated in the raceway because of the play between them and the inner jacket of the bearing. If the inner or outer ring of the bearing sleeve is squeezed, the clearance is reduced. Because the value of the bearing clearance is small, it is sensitive to changes in the clearance. The clearance becomes smaller, and the bearing rolling body and the ferrule generate a large contact stress, which increases the friction and heat of the bearing.
The countermeasures against extrusion are as follows:
(1) When the bearing is in hot state, the inner ring is greatly expanded, which may cause a negative play. A small amount of negative clearance is beneficial to the normal operation of the bearing, but the larger negative clearance is unfavorable for the bearing operation, the temperature is higher, and the degree of negative clearance is reduced by the expansion of the outer ring. In addition, when the bearing is running, the outer ring of the bearing and the bearing sleeve must also have an interference, and the rolling element is squeezed, causing the bearing to be damaged prematurely due to heat generation.
(2) In order to avoid the bearing casing from sliding circumferentially in the bearing chamber, the cumulative tolerance of the end cap (or bearing sleeve) and the inner and outer cover depths of the bearing in the axial direction is “+”. And accumulate at the plane joint surface of the inner and outer covers to ensure that the inner and outer covers clamp the bearing shell. For flameproof motors, this clearance should not be greater than 0.2mm. This tolerance can be guaranteed by CNC or digital display machines.
2. Insufficient machining accuracy of parts and improper assembly of the motor leads to heat generation of the bearing
There are two points in the bearing process that cause the bearing to heat up:
(1) The ends of the motor base are not concentric, causing the center lines of the end caps or bearing sleeves of the two ends of the cover or the bearing sleeve to be not overlapped. Affects the inner and outer rings of the bearing are not parallel and the bearings at both ends are not concentric, causing additional wear and heat.
(2) The end cap or bearing sleeve is eccentrically processed, causing the end caps or bearing sleeves at both ends to be distracted to cause the bearing to heat up. In particular, the bearing sleeve parts should be pointed out. From the perspective of ensuring the coaxiality, if the bearing sleeve can be omitted, it is not needed. Because there is a bearing sleeve, the bearing is first loaded into the bearing sleeve, and the bearing sleeve is then loaded into the end cover, and one more radial matching dimensional chain error. For ensuring coaxiality, it is obviously better to load the bearing directly into the end cap. The above two points require the mechanical operator to ensure the coaxiality in strict accordance with the processing technology when processing the parts.
There are two points in the improper assembly of the motor that cause the bearing to heat up:
(1) The end cover is not properly assembled with the base. If the paint is not cleaned at the end, the end cap bolts are unevenly loaded, and the end caps are biased to make the bearing heat.
(2) The bearing cap, especially the bearing inner cover, is unevenly loaded when the bearing is installed, so that the bearing cap and the rotating shaft are rubbed to make the bearing heat. In order to ensure the quality of the assembly, first wipe the oil on the mating surface thoroughly before assembly. The bolts should be symmetrically tightened so that each bolt is evenly stressed and the rotor is flexible. Otherwise, the bolts should be re-adjusted and tightened. In addition, it is better to use the hot-sleeve method when assembling the bearing, because the inner or outer ring of the bearing is tapped by the copper sleeve with the boring head (some assemblers even hit the bearing directly with the hoe), the bearing will be unevenly stressed and the bearing will be damaged. The heating method should be heated on an oven or an induction core bearing heater, and should not be heated by oil. Because the oil will penetrate into the bearing and mix with the grease when cooking, the grease will deteriorate. The temperature is controlled within 100 ° C when heating, because the grease must not exceed 100 ° C, otherwise it will flow out. In addition, at high temperatures (such as over 200 ° C), the transformation of retained austenite to martensite in the bearing steel will cause the circumferential length of the inner and outer rings of the bearing to increase and cause vibration and heat. In addition, such a high temperature is equivalent to annealing the bearing to reduce the bearing hardness.
3. Lubrication of bearings
First, the bearing grease grade should be selected correctly. When assembling the bearing grease, be sure to insert the grease into the bearing raceway with the oil gun, and the amount of grease must be packed. Because the grease that is squeezed in is the source of the oil film produced when the bearing is working. The second is the amount of oil added, the test reflects that too much or too little oil is not suitable. Too much will cause the bearing to heat up, too little, the bearing will ring, it will not be lubricated, and it will also heat up, so it can only be just right. Generally, when the amount of grease is 2P, it is 1/2 of the bearing chamber, and when it is 4P or more, it is 2/3. The grease must be kept clean and free from deterioration or contamination.
First, the motor bearing overheating
At present, the motor manufacturer's bearing temperature before the motor leaves the factory is an item that must be checked. In addition to the high temperature not exceeding the 95 °C limit, there is no uniform standard for the high temperature of the bearing below the high temperature during operation. According to the general habit, after the motor runs for 1.5-2 hours, the bearing temperature is stable and the temperature rises ≤35K, which can be considered normal. However, when the bearing runs for a short time (such as 15min) and rises to 65°C or runs for more than 1.5h, it still has no downward trend, and less than 1.5h but the bearing stable temperature exceeds 75°C. Both can be considered as high bearing temperatures (65 ° C, 75 ° C for summer, 55 ° C, 65 ° C in cold winter).
Second, the failure phenomenon and solution
1. The bearing is squeezed
Balls or rollers can be easily rotated in the raceway because of the play between them and the inner jacket of the bearing. If the inner or outer ring of the bearing sleeve is squeezed, the clearance is reduced. Because the value of the bearing clearance is small, it is sensitive to changes in the clearance. The clearance becomes smaller, and the bearing rolling body and the ferrule generate a large contact stress, which increases the friction and heat of the bearing.
The countermeasures against extrusion are as follows:
(1) When the bearing is in hot state, the inner ring is greatly expanded, which may cause a negative play. A small amount of negative clearance is beneficial to the normal operation of the bearing, but the larger negative clearance is unfavorable for the bearing operation, the temperature is higher, and the degree of negative clearance is reduced by the expansion of the outer ring. In addition, when the bearing is running, the outer ring of the bearing and the bearing sleeve must also have an interference, and the rolling element is squeezed, causing the bearing to be damaged prematurely due to heat generation.
(2) In order to avoid the bearing casing from sliding circumferentially in the bearing chamber, the cumulative tolerance of the end cap (or bearing sleeve) and the inner and outer cover depths of the bearing in the axial direction is “+”. And accumulate at the plane joint surface of the inner and outer covers to ensure that the inner and outer covers clamp the bearing shell. For flameproof motors, this clearance should not be greater than 0.2mm. This tolerance can be guaranteed by CNC or digital display machines.
2. Insufficient machining accuracy of parts and improper assembly of the motor leads to heat generation of the bearing
There are two points in the bearing process that cause the bearing to heat up:
(1) The ends of the motor base are not concentric, causing the center lines of the end caps or bearing sleeves of the two ends of the cover or the bearing sleeve to be not overlapped. Affects the inner and outer rings of the bearing are not parallel and the bearings at both ends are not concentric, causing additional wear and heat.
(2) The end cap or bearing sleeve is eccentrically processed, causing the end caps or bearing sleeves at both ends to be distracted to cause the bearing to heat up. In particular, the bearing sleeve parts should be pointed out. From the perspective of ensuring the coaxiality, if the bearing sleeve can be omitted, it is not needed. Because there is a bearing sleeve, the bearing is first loaded into the bearing sleeve, and the bearing sleeve is then loaded into the end cover, and one more radial matching dimensional chain error. For ensuring coaxiality, it is obviously better to load the bearing directly into the end cap. The above two points require the mechanical operator to ensure the coaxiality in strict accordance with the processing technology when processing the parts.
There are two points in the improper assembly of the motor that cause the bearing to heat up:
(1) The end cover is not properly assembled with the base. If the paint is not cleaned at the end, the end cap bolts are unevenly loaded, and the end caps are biased to make the bearing heat.
(2) The bearing cap, especially the bearing inner cover, is unevenly loaded when the bearing is installed, so that the bearing cap and the rotating shaft are rubbed to make the bearing heat. In order to ensure the quality of the assembly, first wipe the oil on the mating surface thoroughly before assembly. The bolts should be symmetrically tightened so that each bolt is evenly stressed and the rotor is flexible. Otherwise, the bolts should be re-adjusted and tightened. In addition, it is better to use the hot-sleeve method when assembling the bearing, because the inner or outer ring of the bearing is tapped by the copper sleeve with the boring head (some assemblers even hit the bearing directly with the hoe), the bearing will be unevenly stressed and the bearing will be damaged. The heating method should be heated on an oven or an induction core bearing heater, and should not be heated by oil. Because the oil will penetrate into the bearing and mix with the grease when cooking, the grease will deteriorate. The temperature is controlled within 100 ° C when heating, because the grease must not exceed 100 ° C, otherwise it will flow out. In addition, at high temperatures (such as over 200 ° C), the transformation of retained austenite to martensite in the bearing steel will cause the circumferential length of the inner and outer rings of the bearing to increase and cause vibration and heat. In addition, such a high temperature is equivalent to annealing the bearing to reduce the bearing hardness.
3. Lubrication of bearings
First, the bearing grease grade should be selected correctly. When assembling the bearing grease, be sure to insert the grease into the bearing raceway with the oil gun, and the amount of grease must be packed. Because the grease that is squeezed in is the source of the oil film produced when the bearing is working. The second is the amount of oil added, the test reflects that too much or too little oil is not suitable. Too much will cause the bearing to heat up, too little, the bearing will ring, it will not be lubricated, and it will also heat up, so it can only be just right. Generally, when the amount of grease is 2P, it is 1/2 of the bearing chamber, and when it is 4P or more, it is 2/3. The grease must be kept clean and free from deterioration or contamination.
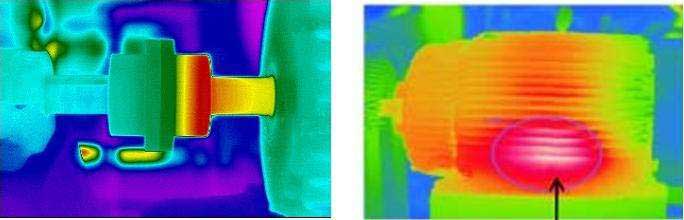