Machining Technology of Titanium Alloy Parts (Force Bearing Parts and Fasteners of Aircraft Landing Gear)
Key words: landing gear, titanium alloy parts, mechanical processing, tool requirements, turning technology, milling technology, coolant, drilling, threading
Abstract:Titanium alloy material has high strength ratio, small deformation coefficient,hot strong resistance,low temperature toughness,corrosion resistance and good welding performance advantages, so it is more and more used in aircraft landing gear's structure bearing parts, fasteners, etc.,but because of its small coefficient of thermal conductivity and the small elastic modulus , the processing performance difference, low efficiency, easy to burn and deformation, it will make an effect on the product processing and quality. This paper combined with the landing gear type of scientific research and production practice, from material, equipment, personnel, process documents, processing conditions and other several aspects to control and optimization of process documents, so as to improve the machining efficiency, save the production cost,ensured the product quality.
1. Material control
1) Titanium alloy raw materials must be re-inspected as required to ensure that raw materials and molded parts meet performance requirements. Mainly inspect the product certificate, identification, forging sampling location, test type, specification and quantity, the full size of the blank state, mechanical properties, etc., to prevent parts defects.
2) In the machining of titanium alloy materials, Castrol water-soluble coolant is mainly used. According to the ratio, it is mixed with water, the coolant pressure is in, and the flow rate is controlled. The coolant containing halogen elements is prone to stress and chemical corrosion to titanium alloys and is prohibited.
2. CNC equipment control
2.1 Equipment requirements
CNC equipment can provide reliable and accurate control of feed motion, tool and workpiece installation to maximize rigidity to avoid vibration and tremor. Increase coolant pressure and flow during processing to ensure adequate coolant on the cutting edge.
2.2 Tool requirements
Titanium alloy workpiece has a high affinity and the cutting temperature of the tool tip is high in the process of processing, resulting in poor wear resistance and toughness of the tool. Titanium-tungsten-cobalt cemented carbide tools are not used. During the processing, the type of coating tool is selected according to the part structure (cavity or boss), the balance distribution, and the degree of surface hardening of the blank. It is divided into roughing, semi-finishing and finishing to reduce the cutting temperature, reduce the sticking knife, collapse the knife, keep the blade sharp and improve the tool durability. In low-speed intermittent cutting, the connecting rod is selected according to the part structure to enhance the overall rigidity of the tool and achieve the vibration reduction efficiency. The cutter body should use a fine-grained base to ensure the coating has strong adhesion and strength, and improve the machining quality of the parts and the cutting efficiency of the tool.
2.3 Fixture requirements
Since the elastic modulus of the titanium alloy material is small, the workpiece is easily deformed, and the clamping force during cutting should not be too large, and an auxiliary support should be used if necessary. The actual cutting force is taken into consideration when designing the fixture structure to ensure that the parts are not deformed by clamping.
3. Manufacturing Control
3.1 General requirements for titanium alloy structural design
The transfer radius of parts should be as large as possible when the structure permits. Ra value of surface roughness of parts should be less than or equal to. For reaming, the Ra value of the surface roughness of the hole machined by boring method should be less than or equal to. When designing a holed part, the edge of the hole has a smooth chamfer. For parts with a large load, the tension zone should be reduced as much as possible to avoid the threaded holes. Avoid using grinding methods to meet the surface roughness of the part required by the design.
3.2 General technical requirements for titanium alloy turning
1) Requirements for tools
The tip of the tool is in the form of a circular arc to increase the strength and prevent burning and collapse. Improve blade edge and built-up edge in time to improve tool durability. The geometric parameters of turning titanium alloy parts, carbide and high speed steel turning tools can be selected according to Table 1 and Table 2.
Table 1 Carbide turning tools recommended geometric parameters
2) Selection of turning parameters
When turning parts with carbide tools, the turning speed ranges from 20m/min to 60m/min. When turning with high speed steel tools, the turning speed ranges from 15m/min to 55m/min. The cutting speed of coated turning tools is increased by 5%-25% on the basis of the cutting speed of cemented carbide tools and high speed steel tools.
3) Requirements for coolant
Before turning, the coolant nozzle should be adjusted to align with the tool tip, and the high-pressure water-soluble emulsion should be preferentially selected to impact the tool rake face.
3.3 General technical requirements for titanium alloy milling
1) Requirements for tools
The shank that holds the milling cutter on the machine spindle should be as short as possible to ensure maximum rigidity of the machine-clamp-tool-workpiece system. When processing titanium alloy die parts, it is required that the tool can withstand the impact of acceleration and deceleration process, and has appropriate flexural strength. Large feed milling cutters and corn milling cutters are used for roughing, round insert milling cutters and solid carbide milling cutters for finishing parts. When processing the closed contour profile, it is necessary to use an end mill with an end edge over center, an Iskar DR shallow hole drill, and a carbide drill. The milling cutter coated with titanium nitride and aluminium nitride is selected.
2) Requirements for coolant
Oil mist cooling or continuous sufficient water-soluble coolant should be used in the finishing of cemented carbide tools. When machining with a high speed steel tool or roughing with a cemented carbide tool, an emulsion suitable for gravity cutting is used as the coolant.
3) Milling process parameters
A, conventional milling
The conventional milling parameters of high speed steel and carbide milling cutters can be selected according to Table 3 and Table 4.
Table 4. Milling parameters of cemented carbide milling cutter in conventional milling
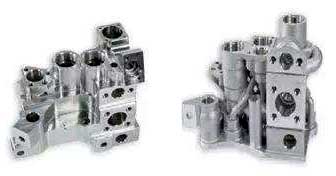
B, CNC milling titanium alloy processing
Tool selection: When milling on CNC machines, indexable carbide coated cutters are used. Mainly used Sandvik GC1030, Kenner KC522M and so on.
Stage division: Due to the characteristics of titanium alloys, the processing stage should be reasonably divided during the manufacturing process of parts. According to the balance distribution, heat dissipation conditions and part structure, it is divided into rough milling and finishing milling.
Regional division: According to the part structure and the distribution of the margin.
Reasonable classification of processing areas: For example, convex type, cavity type, cylindrical type, etc., tool selection can be standardized. To achieve balanced removal allowance, which effectively reduces the cutting time of the down milling processing method and improves the processing efficiency.
Program optimization: In NC machining, as far as possible to ensure that the cutter in the forward milling. Check the size of the corner of the part on the programming design to reduce the sudden change of the load during the machining process.
Parameter control: For the rough machining process of the part, the machining tool path of the program is rationally optimized. CNC milling of high-speed steel milling cutters and CNC milling of carbide knives are processed according to the recommended parameters to improve the machining efficiency of the parts.
C. The cutting speed of the coated milling cutter is increased by 5%-25% based on the spindle speed of the carbide tool and the high speed steel tool.
D, Milling oxide peel
In the process of milling oxide skin, because of the uneven distribution of spare Parts'surface, the Iska vertical milling cutter is mainly suitable for the plane processing of titanium alloy parts. In the contour processing, Walter corn milling cutter is used, and the outer contour oxide scale can also be processed by Isa vertical milling cutter.
3.4 General technical requirements for titanium alloy holes
1) drilling
High-speed steel or cemented carbide bits are used for drilling, and TiN-Al titanium coated drilling tools are used for drilling holes with high accuracy. Requirements for drilling bits for titanium alloy parts:
The apex angle is 2Ψ=120°~127°;
Back angle a=12°~14°;
Helix angle β=35°~40°;
The rake face and the bit axis are у=5° (high speed steel drill bit);
The rake face and the bit axis are у=0° (hard alloy drill bit);
The amount of flank wear (overall wear) of high speed steel drill bits should not exceed 0.6 mm.
When drilling with a high-speed steel drill with a standard structure, the cutting speed value is multiplied by the correction factor Kv = 0.8.
In order to avoid work hardening, the drill bit is not allowed to rotate in the original position without feeding. To reduce the depth of work hardening on the surface of the threaded bottom hole, use a sharpened drill bit.
2) The cutting parameters of countersinks, reaming holes and reaming holes are reasonable
3.5 General Technical Requirements for Thread Tapping of Titanium Alloy
1) The tap of the machined titanium alloy parts is more rigid.
2) When tapping hole threads with taps, a set of taps consisting of two or three taps is used, lubricated and cooled with extrusion lubricant.
3) When the through hole is processed to a depth of 1.5 times or more of the thread diameter, it is processed by a combination of two or three taps, and the number of taps depends on the depth of the threaded hole to be processed.
4) Geometric parameters of the tap: the rake angle y=5°~7°; the back angle a=6°~8°;
5) Oil is used when making thread holes by hand and emulsifier or oil is used when processing straight thread on machine tools. Parts should be cleaned after work.
Abstract:Titanium alloy material has high strength ratio, small deformation coefficient,hot strong resistance,low temperature toughness,corrosion resistance and good welding performance advantages, so it is more and more used in aircraft landing gear's structure bearing parts, fasteners, etc.,but because of its small coefficient of thermal conductivity and the small elastic modulus , the processing performance difference, low efficiency, easy to burn and deformation, it will make an effect on the product processing and quality. This paper combined with the landing gear type of scientific research and production practice, from material, equipment, personnel, process documents, processing conditions and other several aspects to control and optimization of process documents, so as to improve the machining efficiency, save the production cost,ensured the product quality.
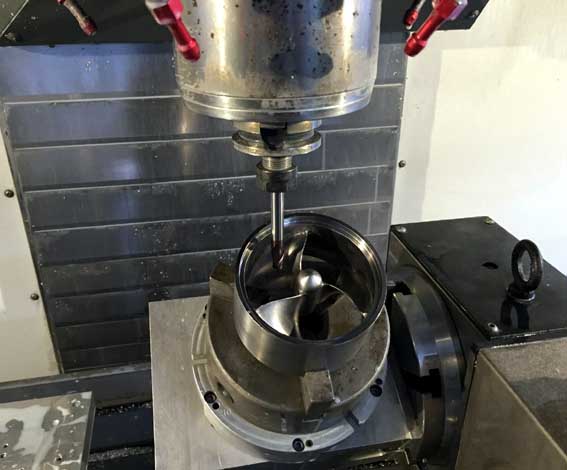
1. Material control
1) Titanium alloy raw materials must be re-inspected as required to ensure that raw materials and molded parts meet performance requirements. Mainly inspect the product certificate, identification, forging sampling location, test type, specification and quantity, the full size of the blank state, mechanical properties, etc., to prevent parts defects.
2) In the machining of titanium alloy materials, Castrol water-soluble coolant is mainly used. According to the ratio, it is mixed with water, the coolant pressure is in, and the flow rate is controlled. The coolant containing halogen elements is prone to stress and chemical corrosion to titanium alloys and is prohibited.
2. CNC equipment control
2.1 Equipment requirements
CNC equipment can provide reliable and accurate control of feed motion, tool and workpiece installation to maximize rigidity to avoid vibration and tremor. Increase coolant pressure and flow during processing to ensure adequate coolant on the cutting edge.
2.2 Tool requirements
Titanium alloy workpiece has a high affinity and the cutting temperature of the tool tip is high in the process of processing, resulting in poor wear resistance and toughness of the tool. Titanium-tungsten-cobalt cemented carbide tools are not used. During the processing, the type of coating tool is selected according to the part structure (cavity or boss), the balance distribution, and the degree of surface hardening of the blank. It is divided into roughing, semi-finishing and finishing to reduce the cutting temperature, reduce the sticking knife, collapse the knife, keep the blade sharp and improve the tool durability. In low-speed intermittent cutting, the connecting rod is selected according to the part structure to enhance the overall rigidity of the tool and achieve the vibration reduction efficiency. The cutter body should use a fine-grained base to ensure the coating has strong adhesion and strength, and improve the machining quality of the parts and the cutting efficiency of the tool.
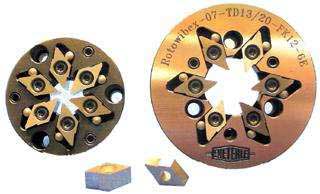
Since the elastic modulus of the titanium alloy material is small, the workpiece is easily deformed, and the clamping force during cutting should not be too large, and an auxiliary support should be used if necessary. The actual cutting force is taken into consideration when designing the fixture structure to ensure that the parts are not deformed by clamping.
3. Manufacturing Control
3.1 General requirements for titanium alloy structural design
The transfer radius of parts should be as large as possible when the structure permits. Ra value of surface roughness of parts should be less than or equal to. For reaming, the Ra value of the surface roughness of the hole machined by boring method should be less than or equal to. When designing a holed part, the edge of the hole has a smooth chamfer. For parts with a large load, the tension zone should be reduced as much as possible to avoid the threaded holes. Avoid using grinding methods to meet the surface roughness of the part required by the design.
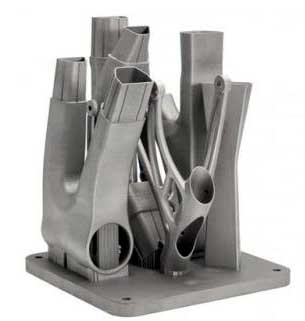
1) Requirements for tools
The tip of the tool is in the form of a circular arc to increase the strength and prevent burning and collapse. Improve blade edge and built-up edge in time to improve tool durability. The geometric parameters of turning titanium alloy parts, carbide and high speed steel turning tools can be selected according to Table 1 and Table 2.
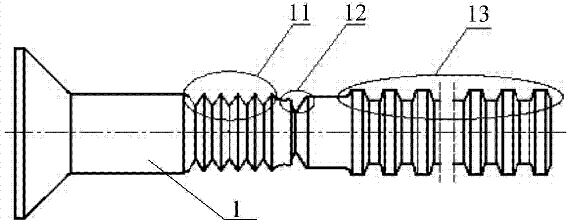
Parts Strength (MPa) | Rake angle | Back corner | Principal deflection angle | Auxiliary deflection angle | Blade inclination angle | Tool tip arc radius (mm) |
≤1000 | 5° | 10° | 20°-70° |
6° |
0° |
1-2 |
>1000 | 1°-5° | 6°-8° |
75°-90° |
0°-3° | ||
≤1000 | 5° | 15° |
0° |
0.3-0.8 |
||
>1000 | 5° | 6°-8° |
Table 2 High-speed steel turning tool recommended geometric parameters
Parts Strength (MPa) | Rake angle | Back corner | Principal deflection angle | Auxiliary deflection angle | Blade inclination angle | Tool tip arc radius (mm) |
≤1000 | 11° | 7° | 25°-45° |
6° |
0° | 0.5-2 |
>1000 | 7°-11° | 4°-7° |
60°-85° |
0°-3° | ||
≤1000 | 11° | 7° | 0° | 0.3-0.8 | ||
>1000 | 11° | 5°-7° |
2) Selection of turning parameters
When turning parts with carbide tools, the turning speed ranges from 20m/min to 60m/min. When turning with high speed steel tools, the turning speed ranges from 15m/min to 55m/min. The cutting speed of coated turning tools is increased by 5%-25% on the basis of the cutting speed of cemented carbide tools and high speed steel tools.
3) Requirements for coolant
Before turning, the coolant nozzle should be adjusted to align with the tool tip, and the high-pressure water-soluble emulsion should be preferentially selected to impact the tool rake face.
3.3 General technical requirements for titanium alloy milling
1) Requirements for tools
The shank that holds the milling cutter on the machine spindle should be as short as possible to ensure maximum rigidity of the machine-clamp-tool-workpiece system. When processing titanium alloy die parts, it is required that the tool can withstand the impact of acceleration and deceleration process, and has appropriate flexural strength. Large feed milling cutters and corn milling cutters are used for roughing, round insert milling cutters and solid carbide milling cutters for finishing parts. When processing the closed contour profile, it is necessary to use an end mill with an end edge over center, an Iskar DR shallow hole drill, and a carbide drill. The milling cutter coated with titanium nitride and aluminium nitride is selected.
2) Requirements for coolant
Oil mist cooling or continuous sufficient water-soluble coolant should be used in the finishing of cemented carbide tools. When machining with a high speed steel tool or roughing with a cemented carbide tool, an emulsion suitable for gravity cutting is used as the coolant.
3) Milling process parameters
A, conventional milling
The conventional milling parameters of high speed steel and carbide milling cutters can be selected according to Table 3 and Table 4.
Table 3 Milling parameters for conventional milling of high speed steel milling cutter
Spindle speed (r/min) |
Tool diamete r (mm) |
Number of teeth (number) |
Feed speed (mm/min) |
Radial cut width (mm) |
Axial depth of cut (mm) |
100-200 | 20 | 4 | 40-80 | 3-5 | 5-10 |
100-150 | 30 | 4 | 40-70 | 3-5 | 5-10 |
200-400 | 16 | 2 | 30-60 | 1-3 | 1-5 |
150-250 | 30 | 4 | 25-70 | 1-3 | 1-5 |
Table 4. Milling parameters of cemented carbide milling cutter in conventional milling
Spindle speed (r/min) |
Tool diamete r (mm) |
Number of teeth (number) |
Feed speed (mm/min) |
Radial cut width (mm) |
Axial depth of cut (mm) |
150-250 | 20 | 4 | 50-120 | 3-5 | 5-10 |
100-200 | 30 | 4 | 50-100 | 3-5 | 5-10 |
300-450 | 16 | 2 | 50-140 | 1-3 | 1-5 |
200-300 | 30 | 4 | 35-100 | 1-3 | 1-5 |
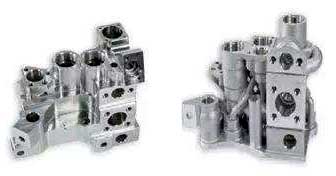
B, CNC milling titanium alloy processing
Tool selection: When milling on CNC machines, indexable carbide coated cutters are used. Mainly used Sandvik GC1030, Kenner KC522M and so on.
Stage division: Due to the characteristics of titanium alloys, the processing stage should be reasonably divided during the manufacturing process of parts. According to the balance distribution, heat dissipation conditions and part structure, it is divided into rough milling and finishing milling.
Regional division: According to the part structure and the distribution of the margin.
Reasonable classification of processing areas: For example, convex type, cavity type, cylindrical type, etc., tool selection can be standardized. To achieve balanced removal allowance, which effectively reduces the cutting time of the down milling processing method and improves the processing efficiency.
Program optimization: In NC machining, as far as possible to ensure that the cutter in the forward milling. Check the size of the corner of the part on the programming design to reduce the sudden change of the load during the machining process.
Parameter control: For the rough machining process of the part, the machining tool path of the program is rationally optimized. CNC milling of high-speed steel milling cutters and CNC milling of carbide knives are processed according to the recommended parameters to improve the machining efficiency of the parts.
C. The cutting speed of the coated milling cutter is increased by 5%-25% based on the spindle speed of the carbide tool and the high speed steel tool.
D, Milling oxide peel
In the process of milling oxide skin, because of the uneven distribution of spare Parts'surface, the Iska vertical milling cutter is mainly suitable for the plane processing of titanium alloy parts. In the contour processing, Walter corn milling cutter is used, and the outer contour oxide scale can also be processed by Isa vertical milling cutter.
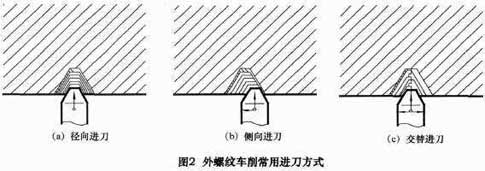
3.4 General technical requirements for titanium alloy holes
1) drilling
High-speed steel or cemented carbide bits are used for drilling, and TiN-Al titanium coated drilling tools are used for drilling holes with high accuracy. Requirements for drilling bits for titanium alloy parts:
The apex angle is 2Ψ=120°~127°;
Back angle a=12°~14°;
Helix angle β=35°~40°;
The rake face and the bit axis are у=5° (high speed steel drill bit);
The rake face and the bit axis are у=0° (hard alloy drill bit);
The amount of flank wear (overall wear) of high speed steel drill bits should not exceed 0.6 mm.
When drilling with a high-speed steel drill with a standard structure, the cutting speed value is multiplied by the correction factor Kv = 0.8.
In order to avoid work hardening, the drill bit is not allowed to rotate in the original position without feeding. To reduce the depth of work hardening on the surface of the threaded bottom hole, use a sharpened drill bit.
2) The cutting parameters of countersinks, reaming holes and reaming holes are reasonable
3.5 General Technical Requirements for Thread Tapping of Titanium Alloy
1) The tap of the machined titanium alloy parts is more rigid.
2) When tapping hole threads with taps, a set of taps consisting of two or three taps is used, lubricated and cooled with extrusion lubricant.
3) When the through hole is processed to a depth of 1.5 times or more of the thread diameter, it is processed by a combination of two or three taps, and the number of taps depends on the depth of the threaded hole to be processed.
4) Geometric parameters of the tap: the rake angle y=5°~7°; the back angle a=6°~8°;
5) Oil is used when making thread holes by hand and emulsifier or oil is used when processing straight thread on machine tools. Parts should be cleaned after work.