Application and Development of Titanium Alloys in Hot Hydrogen Treatment
Key words: hot hydrogen treatment of titanium alloys, reversible hydrogen alloying in titanium alloys, improving processing properties of titanium alloys, Processing titanium alloy structural parts
Titanium alloy thermal hydrogen treatment technology utilizes hydrogen induced plasticity, hydrogen induced phase transition and reversible alloying of hydrogen in titanium alloy. A new system, method and means for optimizing the structure and improving the processing performance of titanium-hydrogen system are presented. The technology can not only improve the processing performance of titanium alloy, but also improve the performance of titanium parts, reduce the manufacturing cost of titanium products, and improve the processing efficiency of titanium alloys.
Titanium alloy has low room temperature plasticity, low deformation limit, large deformation resistance, and easy to crack in cold forming, which greatly limits the cold processability of titanium alloy; Therefore, most titanium alloys must be formed in a hot state. However, the heat distortion temperature is high, the flow stress is large, and the strain rate is low. Especially for those hard-to-deformed titanium alloys with high strength, high toughness, high modulus and high temperature resistance, this phenomenon is particularly serious, which greatly limits their application; In addition, due to the high heat distortion temperature, the high temperature protection of the system or process is difficult and the cost is high; At the same time, titanium alloys require high requirements for mold materials during hot working, and require molds to have sufficient strength at temperatures above 900 °C. It has brought great difficulties to the selection and manufacture of molds, resulting in a series of problems such as long processing cycle and high production cost; Moreover, due to the high heat distortion temperature and high deformation resistance of titanium alloys, higher requirements have been placed on forming equipment. The ability of the existing forming equipment to process titanium alloy structural parts is greatly reduced, and higher requirements are put forward for the development of new forming equipment, which increases the cost and difficulty of equipment development.
The effect of hydrogen on the high temperature plasticity of titanium alloy is mainly manifested as
(1) Lower flow stress
(2) High temperature tensile plasticity improvement
(3) The deformation limit before the first crack occurs in the high temperature upset.
High-temperature plasticization is the earliest hot-hydrogen treatment technology that has received attention and has been extensively studied. Domestic and foreign scholars have attached great importance to this. As early as the 1970s, former Soviet scholars devoted themselves to research work in this area. A series of studies have shown that: Hydrogenation of titanium alloy can improve the hot press processing performance of the alloy, which is manifested by the reduction of hot deformation flow stress and the improvement of plasticity, which makes the hot deformation easier to achieve rolling, hot forging and other processes at lower temperatures; The hydrogen plasticization effect is particularly effective for high-aluminum content heat-strength titanium alloys and Ti3Al alloys, and is also applicable to near-α and α+β alloys, but has little effect on near-β alloys.
Kolachov's research on Ti3Al-based CT5 alloys found: Although it is difficult to deform in the temperature range of β-zone of 1050~1250 °C. However, the addition of 0.6% (mass fraction) of hydrogen, even at 900 ° C deformation of 80% does not produce cracks, plasticity is accompanied by a decrease in yield strength. The compressive flow stress of the hydrogen permeation sample is only 1/3 of the flow stress of the unhydrogenated sample.
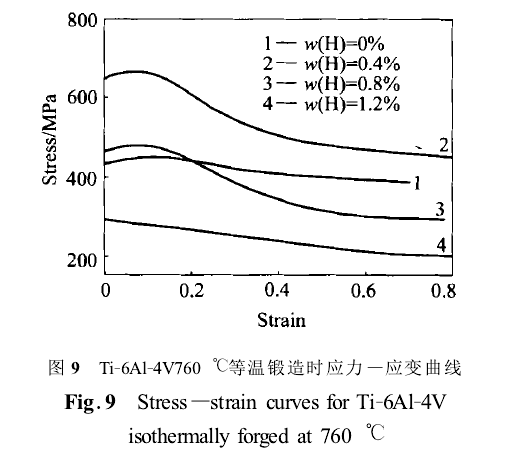
Fig.9 Stress- strain curves for Ti-6Al-4V isothermally forged at 760℃
The isothermal upsetting test of as-cast Ti-9Al-1Mo-3Zr-4Sn alloy with Ti3Al(alpha 2) as strengthening phase shows that: The maximum deformation of the hydrogen absorbing alloy can reach 60%, and can effectively reduce the deformation resistance of the alloy. σ0.2 from 950 ° C and 900 ° C of 200 MPa and 320 MPa. It is reduced to 50-60 MPa and 120-140 MPa, and the degree of influence of hydrogen on the deformation resistance of the alloy decreases with the increase of temperature.
Upsetting test of Ti-5Zr-9Al-5Sn-2Mo alloy shows: For samples with a hydrogen content of 0.45% (mass fraction), the forging flow stress at 800 ° C is about 50% lower than that of the non-hydrogenated sample.
The BT16 alloy upsetting test shows: In the test temperature range of 600 to 850 ° C, 0.2 to 0.3% (mass fraction) of hydrogen is added, and the yield stress is reduced by 1/3 to 1/2.
The BT6 high temperature tensile test shows: The flow stress of the sample in which 0.3% hydrogen was placed at 800 ° C was half lower than the flow stress of the non-hydrogenated sample, and the elongation was increased from 50% to 105%.
Conducted isothermal forging experiments on hydrogen permeating Ti-6Al-4V alloy. Figure 9 shows the stress-strain curves for alloys with different hydrogen contents at 760 and 820 °C. Figure 11 shows the effect of hydrogen content on peak flow stress at different temperatures.
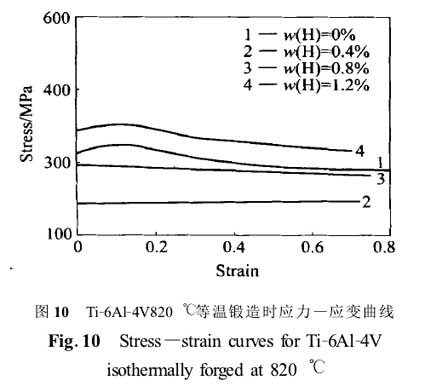
Flow stress- strain curves for Ti-6Al-4V isothermally forged at 820℃
The flow stress of the alloy decreases with the increase of hydrogen content. When the hydrogen content reaches 0.4% (mass fraction), the flow stress is the lowest, about 70% of the flow stress of the unhydrogenated alloy; Then, as the hydrogen content increases, the flow stress increases, which is mainly due to the precipitation of the hydride TiH2. Birla et al. added 0.4% (mass fraction) of hydrogen to the Ti-6Al-2Sn-4Zr-6Mo alloy, and the forging flow stress at 30 ° C was reduced by 30% to 35% compared to the case of non-hydrogenation.
Zhang Yong et al. studied the thermal compression behavior of Ti3Al-based Ti-25Al-10Nb-3V-1Mo as-cast and forged alloys: Hydrogen can significantly reduce the peak flow stress of hot compression, In the range of 900~1 000°C, the peak flow stress of the as-cast 0.2% (mass fraction) H hydrogen permeation sample is reduced by 37%~53% compared with the flow stress of the unhydrogenated sample.
The peak flow stress of the 0.2% (mass fraction) H hydrogen permeable sample in the forged state is reduced by 27% to 31% compared with the unhydrogenated sample.
From the point of view of flow stress, 0.2% (mass fraction) H can lower the thermal compression temperature of the alloy by 50 ° C, and increase the strain rate by an order of magnitude;
During isothermal compression, the tissue change caused by the increase in hydrogen content is equivalent to the tissue change produced by compression at higher temperatures. With the increase of hot pressing temperature, the Ti3Al phase evolved from partial dynamic recrystallization to complete dynamic recrystallization, and the volume fraction of Ti3Al phase decreased. When the hydrogen content reaches 0.2% (mass fraction), the temperature reaches 1 000 ° C, and the deformation characteristics of the β phase region are exhibited when deformed. The hydrogen-induced thermoplastic effect of titanium alloy has significant effect and significance in actual production, which can reduce the isothermal deformation temperature by 50-150 °C and the flow stress drop by more than 30%. It is possible to replace the existing mold materials with more mold materials, and to improve the mold life and metal utilization coefficient.
The role of hydrogen in titanium alloys is twofold:
On the one hand, hydrogen as a harmful impurity element has a very adverse effect on the performance of titanium alloys;
On the other hand, the structure of a certain process can be improved by reasonable and effective control of hydrogen permeation, phase transformation, hydrogen removal and other processes to improve the processing performance, otherwise, the positive effect of hydrogen can not be exerted.
It should be pointed out that the beneficial effect of hydrogen is mainly reflected in the processing of titanium alloy. Regardless of whether the process is hydrogenated or not, the reversible alloying of hydrogen must be used to vacuum-anneal the hydrogen content to a safe level to ensure that the titanium alloy parts do not undergo hydrogen embrittlement during use. Titanium alloy thermal hydrogen treatment technology is based on the reversible alloying of hydrogen, effectively controlling the hydrogen content, existence state and phase transformation process of titanium hydrogen system. To achieve the purpose of improving the performance of plastic processing, diffusion processing, cutting processing and metamorphic processing, and has become a new subject area. Russia has established a complete technical system, including hot hydrogen treatment, hydrogen plasticization, hydrogen densification and hydrogen mechanical processing. Titanium alloy hot hydrogen treatment technology is beneficial to improve the forming performance of titanium alloy, improve processing efficiency, reduce processing difficulty and improve the performance of parts. It can improve the processing and manufacturing level of titanium alloy. Its application prospects are good, and it is possible to promote it to the processing of metals similar to titanium.
Titanium alloy thermal hydrogen treatment technology utilizes hydrogen induced plasticity, hydrogen induced phase transition and reversible alloying of hydrogen in titanium alloy. A new system, method and means for optimizing the structure and improving the processing performance of titanium-hydrogen system are presented. The technology can not only improve the processing performance of titanium alloy, but also improve the performance of titanium parts, reduce the manufacturing cost of titanium products, and improve the processing efficiency of titanium alloys.
Titanium alloy has low room temperature plasticity, low deformation limit, large deformation resistance, and easy to crack in cold forming, which greatly limits the cold processability of titanium alloy; Therefore, most titanium alloys must be formed in a hot state. However, the heat distortion temperature is high, the flow stress is large, and the strain rate is low. Especially for those hard-to-deformed titanium alloys with high strength, high toughness, high modulus and high temperature resistance, this phenomenon is particularly serious, which greatly limits their application; In addition, due to the high heat distortion temperature, the high temperature protection of the system or process is difficult and the cost is high; At the same time, titanium alloys require high requirements for mold materials during hot working, and require molds to have sufficient strength at temperatures above 900 °C. It has brought great difficulties to the selection and manufacture of molds, resulting in a series of problems such as long processing cycle and high production cost; Moreover, due to the high heat distortion temperature and high deformation resistance of titanium alloys, higher requirements have been placed on forming equipment. The ability of the existing forming equipment to process titanium alloy structural parts is greatly reduced, and higher requirements are put forward for the development of new forming equipment, which increases the cost and difficulty of equipment development.
The effect of hydrogen on the high temperature plasticity of titanium alloy is mainly manifested as
(1) Lower flow stress
(2) High temperature tensile plasticity improvement
(3) The deformation limit before the first crack occurs in the high temperature upset.
High-temperature plasticization is the earliest hot-hydrogen treatment technology that has received attention and has been extensively studied. Domestic and foreign scholars have attached great importance to this. As early as the 1970s, former Soviet scholars devoted themselves to research work in this area. A series of studies have shown that: Hydrogenation of titanium alloy can improve the hot press processing performance of the alloy, which is manifested by the reduction of hot deformation flow stress and the improvement of plasticity, which makes the hot deformation easier to achieve rolling, hot forging and other processes at lower temperatures; The hydrogen plasticization effect is particularly effective for high-aluminum content heat-strength titanium alloys and Ti3Al alloys, and is also applicable to near-α and α+β alloys, but has little effect on near-β alloys.
Kolachov's research on Ti3Al-based CT5 alloys found: Although it is difficult to deform in the temperature range of β-zone of 1050~1250 °C. However, the addition of 0.6% (mass fraction) of hydrogen, even at 900 ° C deformation of 80% does not produce cracks, plasticity is accompanied by a decrease in yield strength. The compressive flow stress of the hydrogen permeation sample is only 1/3 of the flow stress of the unhydrogenated sample.
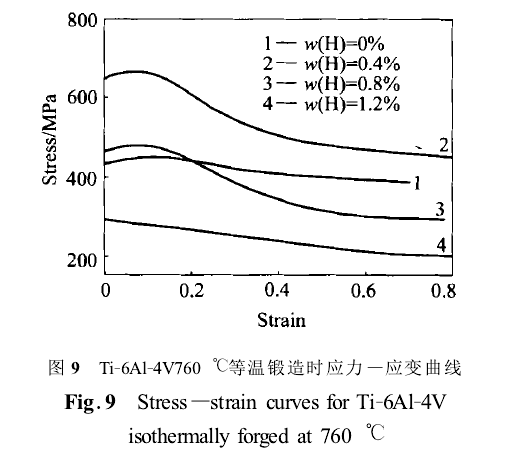
Fig.9 Stress- strain curves for Ti-6Al-4V isothermally forged at 760℃
The isothermal upsetting test of as-cast Ti-9Al-1Mo-3Zr-4Sn alloy with Ti3Al(alpha 2) as strengthening phase shows that: The maximum deformation of the hydrogen absorbing alloy can reach 60%, and can effectively reduce the deformation resistance of the alloy. σ0.2 from 950 ° C and 900 ° C of 200 MPa and 320 MPa. It is reduced to 50-60 MPa and 120-140 MPa, and the degree of influence of hydrogen on the deformation resistance of the alloy decreases with the increase of temperature.
Upsetting test of Ti-5Zr-9Al-5Sn-2Mo alloy shows: For samples with a hydrogen content of 0.45% (mass fraction), the forging flow stress at 800 ° C is about 50% lower than that of the non-hydrogenated sample.
The BT16 alloy upsetting test shows: In the test temperature range of 600 to 850 ° C, 0.2 to 0.3% (mass fraction) of hydrogen is added, and the yield stress is reduced by 1/3 to 1/2.
The BT6 high temperature tensile test shows: The flow stress of the sample in which 0.3% hydrogen was placed at 800 ° C was half lower than the flow stress of the non-hydrogenated sample, and the elongation was increased from 50% to 105%.
Conducted isothermal forging experiments on hydrogen permeating Ti-6Al-4V alloy. Figure 9 shows the stress-strain curves for alloys with different hydrogen contents at 760 and 820 °C. Figure 11 shows the effect of hydrogen content on peak flow stress at different temperatures.
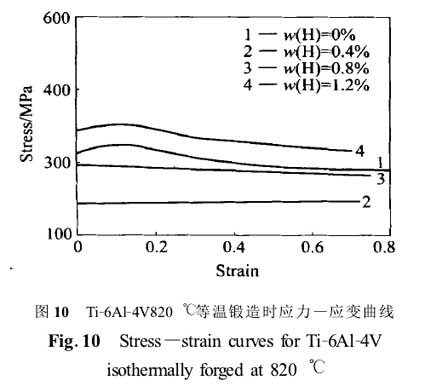
Flow stress- strain curves for Ti-6Al-4V isothermally forged at 820℃
The flow stress of the alloy decreases with the increase of hydrogen content. When the hydrogen content reaches 0.4% (mass fraction), the flow stress is the lowest, about 70% of the flow stress of the unhydrogenated alloy; Then, as the hydrogen content increases, the flow stress increases, which is mainly due to the precipitation of the hydride TiH2. Birla et al. added 0.4% (mass fraction) of hydrogen to the Ti-6Al-2Sn-4Zr-6Mo alloy, and the forging flow stress at 30 ° C was reduced by 30% to 35% compared to the case of non-hydrogenation.
Zhang Yong et al. studied the thermal compression behavior of Ti3Al-based Ti-25Al-10Nb-3V-1Mo as-cast and forged alloys: Hydrogen can significantly reduce the peak flow stress of hot compression, In the range of 900~1 000°C, the peak flow stress of the as-cast 0.2% (mass fraction) H hydrogen permeation sample is reduced by 37%~53% compared with the flow stress of the unhydrogenated sample.
The peak flow stress of the 0.2% (mass fraction) H hydrogen permeable sample in the forged state is reduced by 27% to 31% compared with the unhydrogenated sample.
From the point of view of flow stress, 0.2% (mass fraction) H can lower the thermal compression temperature of the alloy by 50 ° C, and increase the strain rate by an order of magnitude;
During isothermal compression, the tissue change caused by the increase in hydrogen content is equivalent to the tissue change produced by compression at higher temperatures. With the increase of hot pressing temperature, the Ti3Al phase evolved from partial dynamic recrystallization to complete dynamic recrystallization, and the volume fraction of Ti3Al phase decreased. When the hydrogen content reaches 0.2% (mass fraction), the temperature reaches 1 000 ° C, and the deformation characteristics of the β phase region are exhibited when deformed. The hydrogen-induced thermoplastic effect of titanium alloy has significant effect and significance in actual production, which can reduce the isothermal deformation temperature by 50-150 °C and the flow stress drop by more than 30%. It is possible to replace the existing mold materials with more mold materials, and to improve the mold life and metal utilization coefficient.
The role of hydrogen in titanium alloys is twofold:
On the one hand, hydrogen as a harmful impurity element has a very adverse effect on the performance of titanium alloys;
On the other hand, the structure of a certain process can be improved by reasonable and effective control of hydrogen permeation, phase transformation, hydrogen removal and other processes to improve the processing performance, otherwise, the positive effect of hydrogen can not be exerted.
It should be pointed out that the beneficial effect of hydrogen is mainly reflected in the processing of titanium alloy. Regardless of whether the process is hydrogenated or not, the reversible alloying of hydrogen must be used to vacuum-anneal the hydrogen content to a safe level to ensure that the titanium alloy parts do not undergo hydrogen embrittlement during use. Titanium alloy thermal hydrogen treatment technology is based on the reversible alloying of hydrogen, effectively controlling the hydrogen content, existence state and phase transformation process of titanium hydrogen system. To achieve the purpose of improving the performance of plastic processing, diffusion processing, cutting processing and metamorphic processing, and has become a new subject area. Russia has established a complete technical system, including hot hydrogen treatment, hydrogen plasticization, hydrogen densification and hydrogen mechanical processing. Titanium alloy hot hydrogen treatment technology is beneficial to improve the forming performance of titanium alloy, improve processing efficiency, reduce processing difficulty and improve the performance of parts. It can improve the processing and manufacturing level of titanium alloy. Its application prospects are good, and it is possible to promote it to the processing of metals similar to titanium.