How to Choose Different Tools for High Speed Precision Cutting of Stainless Steel Parts?
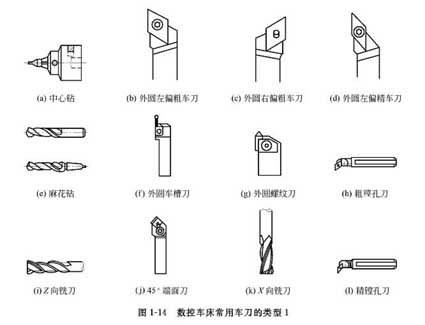
1. Selection of high speed steel: High speed steel is mainly used to manufacture complex multi-blade tools such as milling cutters, drills, taps and broaches. Ordinary high-speed steel W18Cr4V tool has low durability and does not meet the needs. Good results can be obtained by cutting stainless steel with a new high speed steel tool.
Under the same turning conditions, W18Cr4V and 95w18Cr4V two kinds of cutting tools are used to process 1Cr17Ni2 parts. The number of parts processed by tool grinding at one time is 2-3 and 12 respectively, while the tool durability with 95w18Cr4V is increased several times. This is due to the increased carbon content of the 95w18Cr4V steel, which increases the carbide content in the steel. The hardness at room temperature is 2HRC, and the hardness is better. At 600°C, the HRC48.5 of W18Cr4V rises to HRC51~52, and the wear resistance is 2~3 times higher than that of W18Cr4V.
The surface milling cutter made of high vanadium high speed steel W12Cr4V4Mo is used to process 1Cr17Ni2, which can obtain higher tool durability. Because the vanadium content increases, VC with high hardness can be formed in the steel, and fine VC exists in the crystal medium, which can prevent grain growth and improve the wear resistance of the steel; W12Cr4V4Mo has good red hardness and hardness up to HRC 51.7 at 600 °C, so it is suitable for making complex tools for cutting stainless steel. However, its strength (sb=3140 MPa) and impact toughness (ak=2.5 J/cm3) are slightly lower than W18Cr4V, so pay attention to it when using it.
With the continuous development of tool making technology, for large batches of workpieces, the use of carbide multi-blade, complex tools for cutting results will be better.
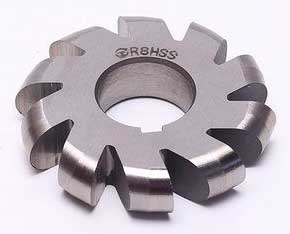
2. Selection of cemented carbide tools:
YG-based cemented carbide has good toughness, can use a large rake angle, and the blade can also be sharpened to make the cutting light, and the chip and the tool are not easy to bond, which is more suitable for processing stainless steel. This advantage of YG-based alloys is especially important in the case of vibrating roughing and interrupted cutting. In addition, YG alloys have good thermal conductivity, and their thermal conductivity is nearly twice as high as that of high-speed steel and twice as high as YT-based alloys. Therefore, YG alloys are widely used in stainless steel cutting, especially in the manufacture of rough turning tools, cutting knives, reaming drills and reamers.
For a long period of time, ordinary grades such as YG6, YG8, YG8N, YW1, and YW2 have been used as cutting tool materials for cutting stainless steel, but they have not achieved satisfactory results. Using new grades of cemented carbide such as 813, 758, 767, 640, 712, 798, YM051, YM052, YM10, YS2T, YD15, etc., cutting stainless steel can obtain better results. The cutting of austenitic stainless steel with 813 grade carbide tool is very effective. Because 813 alloy has high hardness (≥HRA91), strength (sb=1570MPa), good high temperature toughness, oxidation resistance and anti-adhesion, its structure has good compactness and wear resistance.