How stainless steel Parts tapping?
Stainless steel parts tapping is much more difficult than tapping on common steel. Frequently, due to the large torque, the tap is “killed” in the screw hole, the tooth is broken or broken, the surface of the thread is not smooth, the groove is grooved, the size is too bad, the disorder and the tap wear are serious. Therefore, the corresponding technical measures should be taken to solve the problem of tapping stainless steel threads.
1. When tapping stainless steel threads, the phenomenon of "expanding teeth" is more serious, and the tap is easy to "bite" in the hole, so the bottom hole of the thread should be enlarged appropriately. In general, the diameter of the threaded bottom hole with a pitch of 1 mm or less is equal to the nominal diameter minus the pitch; When the pitch is greater than 1 mm, the diameter of the bottom hole of the thread is equal to the nominal diameter minus 1.1 times the pitch.
1. When tapping stainless steel threads, the phenomenon of "expanding teeth" is more serious, and the tap is easy to "bite" in the hole, so the bottom hole of the thread should be enlarged appropriately. In general, the diameter of the threaded bottom hole with a pitch of 1 mm or less is equal to the nominal diameter minus the pitch; When the pitch is greater than 1 mm, the diameter of the bottom hole of the thread is equal to the nominal diameter minus 1.1 times the pitch.
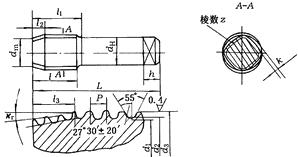
figure 1. Grooveless tap processing stainless steel
2. Choosing the right tap and reasonable cutting amount is the key to the quality of tapping. Tap material, should be selected from cobalt or aluminum super hard high speed steel; The main declination and the pitch, the number of taps are related, the head cone kr=5°~7°, the two cones and the three cones are kr=10°~20°; The calibration part generally takes 3 to 4 thread lengths and has an inverted cone of 0.05 to 0.1 mm/100 mm; The direction of the chip flute generally takes b=8°~15°, which can control the flow direction of the chip. For the straight groove tap, the front end of the tap can be changed into a spiral shape; The rake angle of the tap is generally gp = 15 ° ~ 20 °, and the back angle is 8 ° ~ 12 °.
3. Tapless taps can be used to tap stainless steel, see Figure 7. The diameter of the bottom hole before extruding with a slotless tap is:
D0=dw-(0.5-0.6)P
Where: dw——the outer diameter of the workpiece thread, mm;
P - pitch.
4. When tapping stainless steel, ensure that there is sufficient cooling lubricant. Typically the choice of sulfurized oil + 15% ~ 20% CCl4; White lead oil + engine oil or other mineral oil; Kerosene is diluted with chlorinated paraffin.
5. In the process of tapping, if the tap is broken, the workpiece can be placed in a nitric acid solution for corrosion, and the high-speed steel wire cone can be quickly corroded without scrapping the workpiece.
Commonly used tap for stainless steel processing
The material of stainless steel taps is different from that of ordinary taps, and special taps are usually coated (such as TiN).
As for the broken tap, it depends on what processing method you use, such as manual or processing center, professional tapping equipment. If it is manually processed, it is possible that the tap itself is not suitable for processing stainless steel, and may also be the cause of improper operation.
If it is machined with a tapping machine, the reasons are as follows:
1. The technology of tap is not correct. Stainless steel processing needs screw tap or tip taps. In addition, the material is inferior. It is recommended that the tap be a powerful taper with a cobalt material.
2. The bottom hole problem, processing stainless steel generally speaking the bottom hole is bigger than the processing steel. In addition, the reason for the accuracy of the tapping machine (especially when the small-sized threaded hole is machined, it is easy to break the tap);
3. tap chuck selection is not suitable (now generally used tap chucks are protected by torque)
4. machine selection: mainly depends on the size of the thread hole you want to process, as well as the accuracy requirements and so on.