How To Choose The Geometric Parameters of Cutting Tool When Machining Stainless Steel?
Front angle g0: The hardness and strength of stainless steel are not high, but its plasticity and toughness are good, and its thermal strength is high. Chips are not easy to be cut off during cutting. Under the premise of ensuring that the knife has sufficient strength, a larger rake angle should be selected, which not only can reduce the plastic deformation of the metal to be cut, but also can reduce the cutting force and the cutting temperature, and at the same time reduce the depth of the hardened layer.
The front angle of turning various stainless steels is approximately 12° to 30°. For martensitic stainless steel (such as 2Cr13), the rake angle can take a larger value; For austenitic and austenitic + ferritic stainless steels, the rake angle should be a small value; For stainless steel without quenching and tempering or with lower hardness after quenching and tempering, a larger front angle is preferred. For smaller diameter or thin-walled workpieces, a larger rake angle should be used.
GN = 10°~20° for high speed steel milling cutter and GN = 5°~10° for cemented carbide milling cutter. The reamer generally takes g0=8°~12°; The tap is generally taken as g0=15°-20° (machine) or g0=20° (hand).
Back angle a0: Increasing the rear angle can reduce the friction between the flank and the machined surface, but reduce the strength and heat dissipation of the cutting edge. The reasonable value of the back angle depends on the cutting thickness, and the cutting thickness is small, and a larger relief angle should be selected.
Stainless steel turning tools or boring tools usually take a0=10°~20° (finishing) or a0=6°~10° (roughing); The end milling cutter of high speed steel is A0 = 10°~20° and the end milling cutter is A0 = 15°~20°. The hardness alloy end milling cutter is A0 = 5°~10°, and the end milling cutter is A0 = 12°~16°. The reamer and the tap take a0=8°~12°.
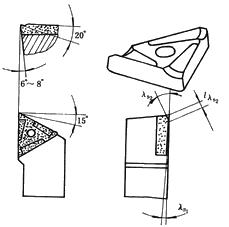
figure 1 Dual-edged tilt-angle chip-breaking turning tool
Principal deviation angle K r, secondary deviation angle k'r, and re: Reducing the main deflection angle can increase the working length of the blade, which is conducive to heat dissipation. However, the radial force is increased during the cutting process, and vibration is easily generated, often taking kr=45°-75°. If the rigidity of the machine is insufficient, it can be increased appropriately. The secondary declination is usually taken as k'r = 8° to 15°. In order to strengthen the cutting edge, the circular arc of the cutting edge with e=0.5-1.0 mm should be grinded.
Edge inclination ls: In order to increase the strength of the cutting edge, the blade inclination angle is generally taken as ls=-8° to -3°, and the larger value is ls=-15° to -5° in the intermittent cutting.
In production practice, in order to increase chip deformation, improve the strength of the tool tip and heat dissipation. The double-edged angle turning tool has achieved good chip breaking effect and widened the chip breaking range, as shown in Figure 1. The inclination angle of the first edge is ls1≥0° and the inclination angle of the second edge is near the tip of the tool. Ls2 ≈ -20 °, the blade edge length of the second edge is lls2. ≈ap/3.
When the double-edged inclined turning tool's g0=20°, a0=6°~8°, kr=90° or 75°, chamfered front angle g01=-10°, re=0.15~0.2 mm. Cutting under conditions of Vc=80-100 m/min, f=0.2-0.3 mm/r, and ap=4-15 mm, the chip breaking effect is good and the tool durability is high.
It is required that the surface roughness of the front and rear face of the cutter be small, and that the VB of the blunt benchmark cone of the cutter be 1/2 of that of the general material.
The front angle of turning various stainless steels is approximately 12° to 30°. For martensitic stainless steel (such as 2Cr13), the rake angle can take a larger value; For austenitic and austenitic + ferritic stainless steels, the rake angle should be a small value; For stainless steel without quenching and tempering or with lower hardness after quenching and tempering, a larger front angle is preferred. For smaller diameter or thin-walled workpieces, a larger rake angle should be used.
GN = 10°~20° for high speed steel milling cutter and GN = 5°~10° for cemented carbide milling cutter. The reamer generally takes g0=8°~12°; The tap is generally taken as g0=15°-20° (machine) or g0=20° (hand).
Back angle a0: Increasing the rear angle can reduce the friction between the flank and the machined surface, but reduce the strength and heat dissipation of the cutting edge. The reasonable value of the back angle depends on the cutting thickness, and the cutting thickness is small, and a larger relief angle should be selected.
Stainless steel turning tools or boring tools usually take a0=10°~20° (finishing) or a0=6°~10° (roughing); The end milling cutter of high speed steel is A0 = 10°~20° and the end milling cutter is A0 = 15°~20°. The hardness alloy end milling cutter is A0 = 5°~10°, and the end milling cutter is A0 = 12°~16°. The reamer and the tap take a0=8°~12°.
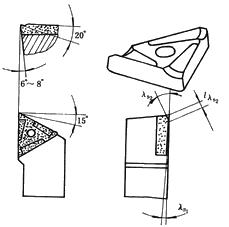
figure 1 Dual-edged tilt-angle chip-breaking turning tool
Principal deviation angle K r, secondary deviation angle k'r, and re: Reducing the main deflection angle can increase the working length of the blade, which is conducive to heat dissipation. However, the radial force is increased during the cutting process, and vibration is easily generated, often taking kr=45°-75°. If the rigidity of the machine is insufficient, it can be increased appropriately. The secondary declination is usually taken as k'r = 8° to 15°. In order to strengthen the cutting edge, the circular arc of the cutting edge with e=0.5-1.0 mm should be grinded.
Edge inclination ls: In order to increase the strength of the cutting edge, the blade inclination angle is generally taken as ls=-8° to -3°, and the larger value is ls=-15° to -5° in the intermittent cutting.
In production practice, in order to increase chip deformation, improve the strength of the tool tip and heat dissipation. The double-edged angle turning tool has achieved good chip breaking effect and widened the chip breaking range, as shown in Figure 1. The inclination angle of the first edge is ls1≥0° and the inclination angle of the second edge is near the tip of the tool. Ls2 ≈ -20 °, the blade edge length of the second edge is lls2. ≈ap/3.
When the double-edged inclined turning tool's g0=20°, a0=6°~8°, kr=90° or 75°, chamfered front angle g01=-10°, re=0.15~0.2 mm. Cutting under conditions of Vc=80-100 m/min, f=0.2-0.3 mm/r, and ap=4-15 mm, the chip breaking effect is good and the tool durability is high.
It is required that the surface roughness of the front and rear face of the cutter be small, and that the VB of the blunt benchmark cone of the cutter be 1/2 of that of the general material.