Cutting Machining and Tool Design of Titanium Alloy Parts
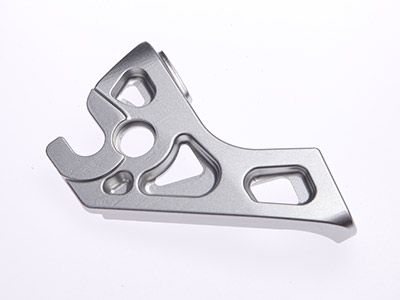
Introduction: Titanium alloy has a small modulus of elasticity. For example, the elastic modulus of TC4 is E=110 GPa, which is about half of that of steel. Therefore, the large elastic deformation of the workpiece caused by cutting force will reduce the accuracy of the workpiece, so the rigidity of the processing system should be improved. The workpiece must be clamped very firmly and the tool's tool moment to the workpiece support point is minimized. The tool must be sharp, otherwise vibration and friction will occur, which will shorten the durability of the tool and reduce the accuracy of the workpiece.
When cutting titanium alloys, only in the range of cutting speed of 1-5 mm/min can chip tumors form. Therefore, in general production conditions, when cutting titanium alloys, there will be no chip tumors. The friction coefficient between the workpiece and the tool is not very large, and it is easy to obtain a good surface quality. The use of a cooling lubricant has no effect on improving the micro-geometry of the surface of the titanium alloy. The lower surface roughness of the machined titanium alloy is due to the absence of built-up edge on the tool. The use of cooling lubricants has no effect on improving the micro-geometry of titanium alloy surfaces. The low roughness of machined surface in cutting titanium alloy is due to the absence of chip tumors on the tool.
However, in order to improve cutting conditions, reduce cutting temperatures, increase tool life, and to eliminate the risk of fire, it is necessary to use a large amount of soluble coolant during processing.
Usually there is no ignition and combustion phenomenon in the processing of titanium alloy parts, but there is ignition and combustion phenomenon in the micro-cutting process. In order to avoid this danger, the coolant should be used in large quantities; Remove chips from machine tools in time. Fire extinguishing equipment is available; Replace blunt cutters in time. When the surface of the workpiece is contaminated, it is easy to cause sparks. At this time, the cutting speed must be reduced. Compared with thin chips, thick chips are not easy to generate sparks, so it is necessary to increase the cutting volume, which will not make the temperature rise as quickly as cutting speed increases.
Selection criteria for the processing of titanium alloys: From the viewpoint of lowering the cutting temperature, a lower cutting speed and a larger amount of cutting should be employed. Because of the high cutting temperature, the titanium alloy absorbs oxygen and hydrogen from the atmosphere, which makes the surface of the workpiece hard and brittle, and makes the tool worn severely. Therefore, during the processing, the temperature of the tool tip must be kept at a suitable temperature to avoid excessive temperature.
When turning hard-skinned titanium alloy workpieces with YG8 turning tool under intermittent cutting conditions, the recommended cutting parameters are as follows: v=15~28m/min, f=0.25~0.35mm/r, ap=1~3mm.
When using a YG3 turning tool to finish a titanium alloy workpiece under continuous cutting conditions, the recommended cutting amount is: v=50~70m/min, f=0.1~0.2mm/r, ap=0.3~1mm. Table 2 shows the amount of cutting available for turning titanium alloys.
Cutting amount when turning titanium alloy:
Procedure Properties - Titanium Alloy Material - Hardness - Cutting Allowance (mm) - Cutting Speed (mm/min) - Tool Walking
Barren turning - TA1 ~ 7, TC1 ~ 2 - Soft - >
Oxide skin thickness
Barren turning -TA8, TC3~8-Medium->
Oxide skin thickness
Barren turning - TC9 ~ 10, TB1 ~ 2 - Hard - >
Oxide skin thickness
Rough Turning-TA1~7, TC1~2-Soft->
Rough Turning-TA8, TC3~8-Medium->
Rough Turning - TC9 ~ 10, TB1 ~ 2 - Hard - >
Finish Turning -TA1~7, TC1~2-Soft
Finish Turning-TA8, TC3-8-in
Finish Turning-TC9-10, TB1-2-Hard
The TC4 (hardness is HB320~360) is turned by YG6X turning tool, and the optimum cutting speed is 60mm/min when ap=1mm and f=0.1mm/r. On the basis of this, the cutting speed under different cutting amount and cutting depth is shown in Table 3.
Cutting speed of turning titanium alloy TC4
A typical turning tool for machining titanium alloys has the following characteristics:
The blade material is YG6X, YG10HT; The rake angle is small, generally γ0=4°~6°, which enhances the strength of the cutter head; There are negative chamfers of f=0.05~0.1mm to enhance the strength of the blade. The back angle is large, generally α0=14°~16°, to reduce the friction behind and improve the durability of the tool; Generally, it is not allowed to grind sharp corners or transition edges, and the rounded corners of the grinding edge are r=0.5mm, and the rough turning can reach r=1~2mm to enhance the strength of the cutting edge; When finishing turning or turning thin-walled parts, the main deviation angle of the tool is large, generally 75°~90°.
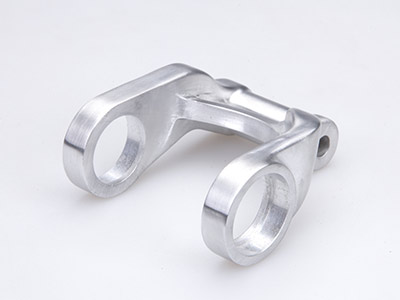
Cutting amount:
Rough turning: v=40~50m/min, f=0.2~0.3mm/r, ap=3~5mm.
Semi-finishing turning: v=40~45m/min, f=0.2~0.3mm/r, ap=1~2mm.
Fine turning: v=50~55m/min, f=0.1~0.15mm/r, ap=0.2~0.5mm.
Cooling with emulsions can effectively improve tool durability.
The high wear resistance and hardness of the cutter head under the premise of ensuring the strength of the cutter head is the key to the rational processing of titanium alloy. Therefore, the selected YG6X blade should be polished with diamond or SiC whetstone after the sharpening (back chamfering) to eliminate the sharpening of the kerf and enhance the strength of the blade.
When rough turning irregular black leather workpieces, the blade is generally ground by 3°~+5° blade inclination; In the case of fine turning, there is generally no blade inclination, and the tool wear at this time is mainly the adhesion (bonding) of the rake face.
Such a typical turning tool can reasonably solve the problem that the material activity increases with the increase of temperature and the thermal conductivity is poor when the titanium alloy is processed, and thus the tool durability is greatly improved.
3.2 Drilling
It is difficult to drill titanium alloys. Burning and drill breakage often occur in the process of drilling. The main reason is the poor grinding of the drill bit, the untimely chip removal, poor cooling and poor rigidity of the process system.
(1) Drill selection: For drills larger than 5 mm in diameter, it is best to use cemented carbide YG8 as the tool material; When processing holes smaller than 5mm, high-speed steel drill bits (such as M42 or B201) with hardness greater than 63HRC can be used; When the hole depth is less than twice the diameter, a bit (short type) bit is used; When the hole depth is more than twice the diameter, a twist drill is used. Geometric parameters of the drill bit: λ=0°~3°, αc=13°~15°, 2φ=120°~130°.
In order to facilitate the formation of chips, reduce friction and improve the cutting ability of the drill bit. The width of the guide edge band can be reduced to 0.1~0.3 mm according to the diameter of the drill bit, the cross edge can be grinded to 0.1D, and the top angle of the double edge grinding can be 2φ=130°~140°, 2φ=70°~80°.
Table 4 lists the geometric parameters of the double-point drill bit.
Geometric parameters of double-edge bit
Bit diameter (mm) - apex angle 2_ - second apex angle 2_0 - back angle of second edge a
>3~6-130°~140°-80°~140°-12°~18°-
>6~10-130°~140°-80°~140°-12°~18°-
>10~18-125°~140°-80°~140°-12°~18°-
>18~30-125°~140°-80°~140°-12°~18°-
(2) Cutting amount
Carbide drill bit: v=9~15m/min, f=0.05~0.2mm/r; high speed steel drill bit v=4~5m/min, f=0.05~0.3mm/r.
(3) When drilling deep holes or small diameter holes, manual feed can be taken.
The drill must be periodically withdrawn from the hole during drilling to remove the chips. In order to avoid the strong wear of the drill bit, the drill bit should not be allowed to stay in the hole, and the drill edge will rub the surface, causing the work hardening and making the drill bit dull. The cooling lubricant must be supplied adequately when drilling. Generally use soybean oil, if necessary, can add French OLTIP drilling and tapping special oil. As far as possible to improve the rigidity of the process system, fix the drilling die on the workbench, the drilling die should be close to the processing surface, as far as possible to shorten the bit.
The wear rate at the back corner of the bit is 0.4-0.5 mm, which is taken as the criterion for drill bluntness.
(4) Drilling examples:
A molybdenum high speed steel drill is used to drill α+β TC4 titanium alloy workpiece. The diameter of the drill is D=6.35 mm and the depth of the hole is H=12.7 mm.
The cutting parameters v=11.6 m/min and f=0.127 mm/r were selected and cooled using an emulsion.
The tool durability T is based on the wear width h = 0.38 mm, and each drill can drill 260 holes for excellent results.