Titanium Alloy Cutting And Tool Design
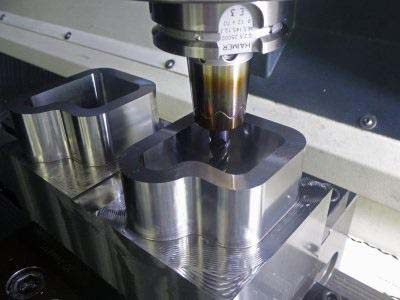
Introduction: The elastic modulus of titanium alloys is small, such as TC4's elastic modulus E = 110 GPa, which is about half that of steel. Therefore, the elastic deformation of the workpiece caused by the cutting force will reduce the accuracy of the workpiece, and the rigidity of the processing system must be improved. The workpiece must be clamped firmly so that the cutter moment on the workpiece support point is minimized. The tool must be sharp, otherwise vibration and friction will occur, which will shorten the tool life and reduce the accuracy of the workpiece.
When cutting titanium, only the cutting speed in the range of 1 ~ 5mm / min, and have a BUE formation. Therefore, when the titanium alloy is cut under normal production conditions, no built-up edge is generated. The coefficient of friction between the workpiece and the tool is not very large and it is easy to obtain a good surface quality. The use of cooling lubricating fluids has no effect on improving the microscopic geometry of the titanium alloy surface. When machining titanium alloys, the machined surface roughness is low due to the absence of built-up edge on the tool.
However, in order to improve the cutting conditions, reduce the cutting temperature, increase the tool life, and to eliminate the risk of fire, it is necessary to use a large amount of soluble coolant during processing.
Normally, titanium alloy parts are not ignited and burned during processing, but they may be ignited and burnt during processing in the micro-cutting state. In order to avoid this danger, you should: Use a lot of coolant; Promptly remove swarf from the machine; equipped with fire fighting equipment; Change the blunt tool in time; When the surface of the workpiece is contaminated, it is easy to cause sparks. At this time, the cutting speed must be reduced. Compared to thin swarf, thick swarf is less prone to sparks, so it is necessary to increase the depth of cut. Increasing the depth of cut does not cause the temperature to rise rapidly as fast as the cutting speed.
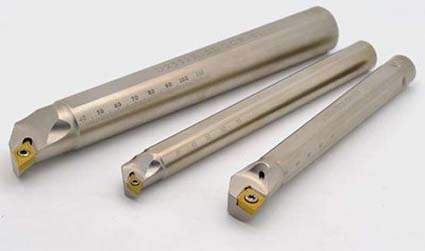
Selection criteria for cutting titanium alloy cutting amount: From the viewpoint of reducing the cutting temperature, a lower cutting speed and a larger cutting amount should be adopted. Due to the high cutting temperature, titanium alloy absorbs oxygen and hydrogen from the atmosphere, causing the surface of the workpiece to be hard and brittle, causing severe wear of the tool. Therefore, during the processing, the temperature of the tool tip must be maintained at a suitable temperature to avoid excessive temperature.
Under the condition of intermittent cutting, the recommended cutting amount is v=15~28m/min, f=0.25~0.35mm/r, and ap=1~3mm when turning the hard - skinned titanium alloy workpiece with a YG8 lathe tool.
Under continuous cutting conditions, when using a YG3 turning tool to finish a titanium alloy workpiece, the recommended cutting amounts are: v=50~70m/min, f=0.1~0.2mm/r, ap=0.3~1mm. Table 2 shows the cutting amount available for turning titanium alloys.
Cutting amount when turning titanium alloy
Process Properties - Titanium Alloy Material - Hardness - Cutting allowance (mm) - Cutting speed (mm/min) - Number of passes
Waste lathing-TA1~7, TC1~2-soft->
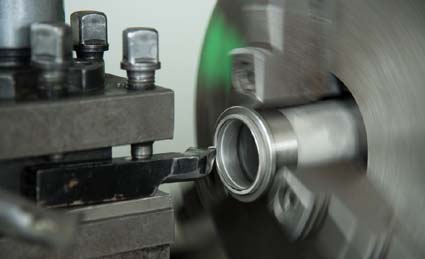
Oxide thickness
Waste lathing-TA8, TC3~8-in->
Oxide thickness
Waste lathing-TC9~10, TB1~2-hard ->
Oxide thickness
Rough turning- TA1~7, TC1~2-soft ->
Rough turning -TA8, TC3~8-in ->
Rough turning -TC9~10,TB1~2-hard ->
Finish turning - TA1~7, TC1~2- soft
Finish turning -TA8, TC3~8-
Finish turning -TC9~10, TB1~2-hard
Turning TC4 (hardness HB320~360) with YG6X turning tool, the optimum cutting speed is 60mm/min when a = 1mm and f = 0.1mm/r. Based on this, the cutting speeds under different cutting amount and cutting depth are shown in Table 3.
Turning speed of titanium alloy TC4
Typical turning tools for machining titanium alloys have the following characteristics:
The blade material is YG6X, YG10HT; the rake angle is small, generally γ0=4°~6°, and the strength of the cutter head is enhanced; A negative chamfer with f=0.05~0.1mm to enhance the strength of the blade; The rear angle is larger, generally α0=14°~16°, to reduce the back friction and improve the tool durability; Generally do not allow to grind sharp edge or transition, and grind corner radius r = about 0.5mm, Roughing up to r = 1 ~ 2mm, in order to enhance the strength of the cutting edge; When finish turning or turning thin-walled parts, the tool's leading angle is larger, generally 75°~90°.
Cutting amount:
Roughing car: v=40~50m/min, f=0.2~0.3mm/r, ap=3~5mm.
Semi-finish turning: v=40~45m/min, f=0.2~0.3mm/r, ap=1~2mm.
Finish turning: v=50~55m/min, f=0.1~0.15mm/r, ap=0.2~0.5mm.
Emulsion cooling can effectively increase tool life. In the premise of guaranteeing the strength of the cutter head, making the cutter head with high wear resistance and hardness is the key to properly processing the titanium alloy. Therefore, the selected YG6X blade should be backed with diamond or silicon carbide whetstone (back chamfer) after sharpening, so as to eliminate the need for sharpening the saw blade and enhance the strength of the blade.
When rough turning an irregular black skin workpiece, the blade is generally ground to a 3°~+5° blade inclination; When finish turning, there is generally no blade angle, and the tool wear at this time is mainly the rake face adhesion (bonding) wear. This typical turning tool can reasonably solve the problem that when the titanium alloy is processed, the material activity increases as the temperature increases and the thermal conductivity is poor, so the tool durability is greatly improved.
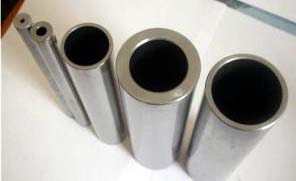
Drilling
Titanium drilling more difficult, often appear burned and broken drill knife phenomenon in the process, The main reasons for this are bad grinding of the drill bit, unsatisfied scraps discharge, poor cooling, and poor rigidity of the process system.
(1) the selection of the drill bit:
For drills with a diameter of more than 5mm, it is best to use hard alloy YG8 as a tool material; When processing holes smaller than 5mm, high-speed steel drills with hardness higher than 63HRC (such as M42 or B201) can be used; When the hole depth is less than twice the diameter, use a chute (short) drill; When the hole depth is greater than twice the diameter, a twist drill is used. The geometric parameters of the drill: λ = 0° ~ 3°, αc = 13° ~ 15°, 2φ = 120° ~ 130°.
To facilitate the formation of swarf, reduce friction and improve the cutting ability of the drill, According to the diameter of the drill, the width of the leading edge can be reduced to 0.1~0.3mm, and the chisel edge can be ground to 0.1D, and the double edge grinding angle 2φ=130°~140°, 2φ=70°~80°. Table 4 lists the geometric parameters of the double-edge bit.
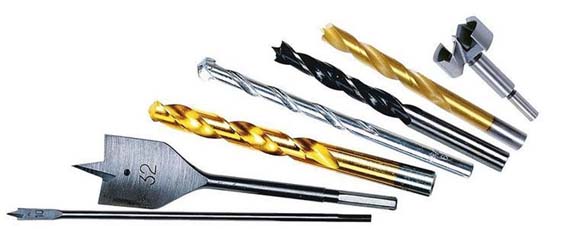
Double front angle drill bit geometry
Drill diameter (mm) - apex angle 2φ - second apex angle 2φ0 - second edge relief angle α
>3~6-130°~140°-80°~140°-12°~18°-
>6~10-130°~140°-80°~140°-12°~18°-
>10~18-125°~140°-80°~140°-12°~18°-
>18~30-125°~140°-80°~140°-12°~18°-
(2) Cutting amount
Hard alloy drill: v = 9 ~ 15m/min, f = 0.05 ~ 0.2mm/r; high-speed steel drill v = 4 ~ 5m/min, f = 0.05 ~ 0.3mm/r.
(3) When drilling deep holes or small diameter holes, manual feed can be taken. When drilling, you must periodically withdraw the drill from the hole to clear the swarf. In order to avoid the strong wear of the drill bit, the drill bit cannot be stuck in the hole and the drill bit will rub the machining surface, which will cause work hardening and make the drill bit dull. Drill hole must be well supplied with cooling lubricant. Soybean oil is generally used, and if necessary, French OLTIP drilling and tapping special oil can be added. As much as possible to improve the rigidity of the process system, the drill die is fixed on the workbench, and the drill die should be close to the machining surface to make the drill bit as short as possible.
To take the bit back corner wear, h = 0.4 ~ 0.5mm drill blunt as standard.
(4) Drilling example:
Using a molybdenum high speed steel drill to perform drilling on α+β TC4 titanium alloy workpieces. The drill diameter D is 6.35mm and the hole depth H is 12.7mm. The selected cutting parameters were v=11.6m/min, f=0.127mm/r, and the emulsion cooling was used. The tool durability T has a wear width h of 0.38 mm, and each drill can drill 260 holes with excellent results.
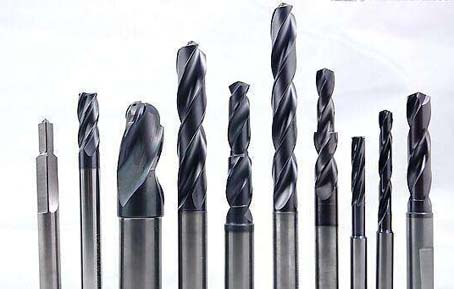