High Precision Grinding Of Tablet PC Shell To See The Evolution Of CNC Technology
1: What is CNC? Which products use this process?
As one of the important industries in modern science and technology, tablet computers have formed a significant impact on the traditional computer industry. Although there are many flat products in the market at present, but from the aspect of product work molding, it is mainly divided into three types: injection molding, stamping molding and CNC molding, And among these three is none other than the most complex CNC process, but usually after the molding product to more high-end posture debut. That the beginning of the CNC technology used in flat panel products is like? What are the major improvements in these years? With the above two issues, let's take a look at the growth path of the CNC process.
What is a CNC?
CNC is commonly known as "CNC machine tools". I believe that many people have heard of this concept. It is an automated machine controlled by a program. The control system can logically process a program having control codes or other symbolic instructions and decode it by a computer. So that the numerical control equipment to perform well-defined actions, a piece of original metal sheet through a long time precision processing, and finally hit the desired shape.
◆ What products work molding application of CNC machining technology?
In practical applications, CNC molding technology with metal materials can create more precise product accuracy and bring better texture. At present, the most representative product on the tablet market is the Apple iPad series and the Nokia N1.
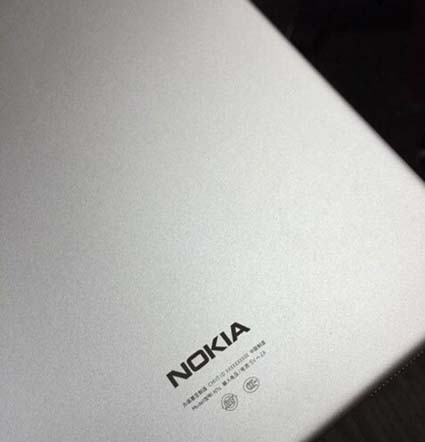
Nokia N1 and iPad series products adopt CNC process casing
CNC molding technology is more costly, with incredible accuracy and accuracy of up to 0.001mm, and each finished product has been carefully crafted. At present, CNC molding technology is also used in the production of precision parts for the aerospace and racing industries. This is why high-end flat-panel products use this technology.
2: An iPad Makes More People Know About CNC Processes
The first iPad released on January 28, 2010, and quickly won the market, and its success in addition to its high performance, the CNC process shell process is one of the highlights, its color is still its shape on the "high value", has been more liked by consumers. It can be said that the iPad generation adopts a CNC process to allow more people to understand the technology.
◆ The initial application of the first generation iPad to the fuselage thickness of 13.4mm
The thickness of the first generation iPad body is 13.4mm, CNC molding technology with magnesium alloy shell, to bring the product a more intense metal texture. Although from the perspective of our current eyes, the shell thickness is somewhat unsatisfactory. But at the time in terms of background, the process has just applied to flat products, has been able to do so is not easy.
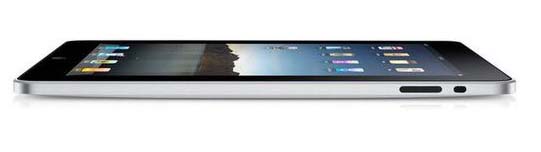
The initial application of the first iPad to the fuselage thickness of 13.4mm, the process is not so perfect
◆ Focus on more appearance is not too much internal design
At the beginning of the design, the main focus of the iPad generation of CNC shells was appearance, The body is smooth when gripped, but there is a grainy impression, making it feel better to play the product. In addition, the outer corners of the shell are rounded, making it more portable and giving people a visual experience.
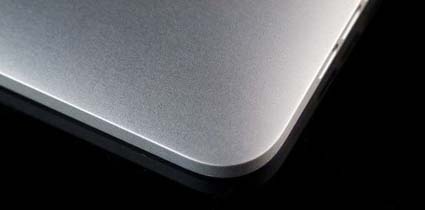
iPad generation using CNC technology, shell touch is a certain degree of granularity
In terms of internal design, the inner performance of the iPad shell is relatively rough. The fixing method of the internal screws and the design of the “baffle” are more abrupt, and the overall design sense inside the housing is poor. However, the presence of its striped design can provide better space for components and ensure the performance of the product. The thickened design of the shell key position, to a certain extent, guarantees the fixation of its function keys.
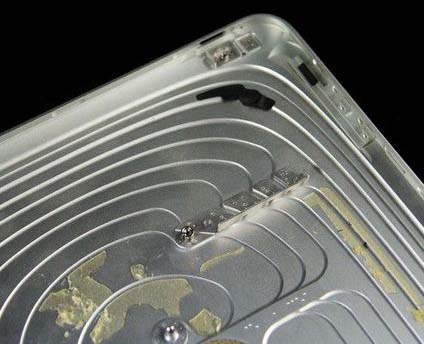
In addition to the use of CNC technology iPad internal screw fixation and "baffle" design is more abrupt
It can be seen that the preliminary CNC process is applied to tablet PCs and is still relatively rough. There are still many areas for improvement in internal design. However, the strict product accuracy and outstanding texture make this process superior to the injection molding and stamping process. Of course, this is only the initial CNC process. What progress has made in the process so far? We then look down.
3: The external process of the shell is improved. More beautiful and delicate
■The CNC process tends to be mature Nokia N1 and iPad Air 2 adopt this technology
With the development of CNC technology, more and more flat-panel products have been applied. The most representative ones are Apple's latest series of iPad Air 2 and Nokia N1 Tablet PCs. Both of these products use CNC technology.
What are the improvements in technology now?
What are the perfect designs?
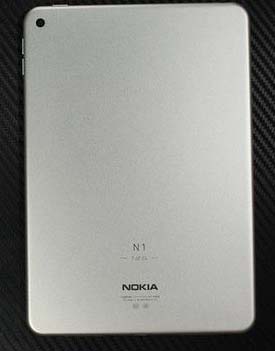
Nokia N1 shell using the latest CNC technology
◆Technology enhances appearance more beautiful
In terms of appearance, the products made by this process are more “slim” and the overall visual sense of the shell gives a sense of impact. The appearance of the product has become more exquisite (of course, this has a lot to do with the upgrading of the screen), and the border becomes more rounded, not a rigid "box" design, more comfortable when hand-held, The change can be said to be an improvement in craftsmanship.
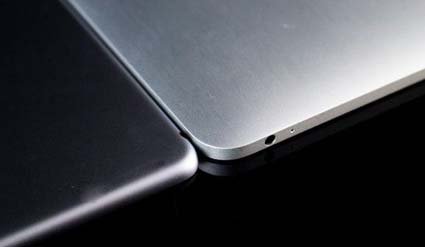
The border around the Nokia N1 has become more rounded, not a rigid "box" design
In addition, there are certain improvements in the details of the button position, so that the button position does not stay on the side frame, but to a certain extent close to the backplane. In this way, reducing the thickness of the fuselage does not affect the user's operation, and it can be said to be of double benefit. The realization of this design depends to a certain extent on the improvement of the process.
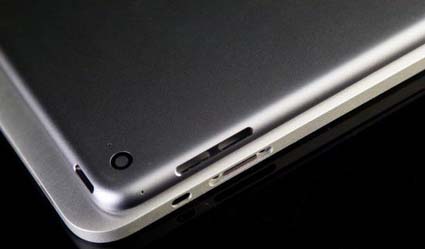
There is also a certain improvement in the details of the key position. It is easy to operate and also more beautiful.
The recessed design of the interface, in the previous technology has also been a certain improvement, Even if there is a certain gap between the positions of the keys, this design makes the position of the volume keys adjacent to the power-off key set, which is more beautiful on the side of the body.
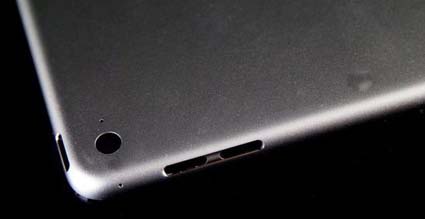
Closer and smaller gaps between two key positions The precision of the CNC process perfectly supports the design
It can be seen that today's CNC process has been greatly improved in appearance compared to before. The circular frame, the appearance of more refined, grinding process more mature, high-precision polished body will have a sense of industrial design. But these are just the appearance of the process of upgrading, then whether the internal process of the shell is also a qualitative improvement? Please continue to look down.
4: Internal design Beautiful and more reasonable design
Compared to the outside of the housing, the interior of the CNC housing is more attractive to the author, Now that the CNC has become “clean and neat” inside the housing, the screw fixings have become “small”. The location is close to the border, and it does not give people a sense of unexpected design. The overall design has been greatly improved.
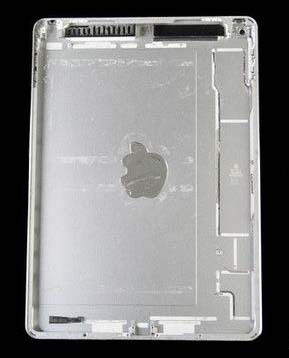
iPad Air 2 shell CNC process, the internal becomes "neat"
◆ reduce the overall thickness of the shell pay more attention to detail
At the initial stage of the CNC process application, the thickness of the four perimeter corners is the same as the border and there is no special design. Today, the body shell thickening corner after processing, can cope with a strong impact. This area is where the tablet is most likely to bump, so it should be well protected. This design on the one hand reduces the weight of the fuselage (reduces the overall thickness of the shell) and increases the overall firmness of the fuselage.
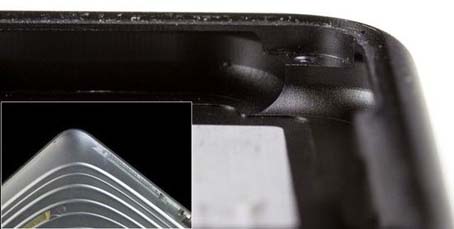
Nokia N1 shell four peripheral corner thickening processing to enhance the overall strength of the fuselage
At the interface of the fuselage, CNC process products are now fixed with complex structures to ensure the durability of the interface. If you’re playing tablet computers more verbally, then charge your tablet every day. The repeated insertion and removal of the power cord from the charging cable is a test of the durability of the interface. Nokia is considering this point, only to use the complex structure of the interface commonly used in the fuselage to make it stable and fixed.
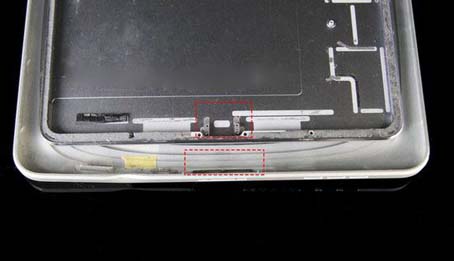
CNC process products using a complex structure be secured, thereby ensuring the durability of the interface
In addition to the above, a certain increase in the internal border of the groove, functions as fixed components, It can be said that it is a technological innovation, and the groove does not cover the border, but appears in the position where the components exist. The object of the process is better better fixation components.
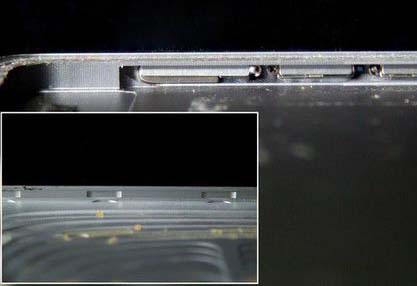
Groove design is also a manifestation of precision manufacturing
■ Summary:
It has been more than four years since the generation of the iPad application CNC process. During this time, whether it is the appearance of the shell or its internal integration, there has been a clear improvement. It can be said that in the current process, it is the highest precision and high-complexity grinding process. After that four years, what kind of heights will the CNC process achieve? No one of us can be sure. I believe that with the improvement of design in the future, the process will be more precise and reach a level that we could not imagine.
As one of the important industries in modern science and technology, tablet computers have formed a significant impact on the traditional computer industry. Although there are many flat products in the market at present, but from the aspect of product work molding, it is mainly divided into three types: injection molding, stamping molding and CNC molding, And among these three is none other than the most complex CNC process, but usually after the molding product to more high-end posture debut. That the beginning of the CNC technology used in flat panel products is like? What are the major improvements in these years? With the above two issues, let's take a look at the growth path of the CNC process.
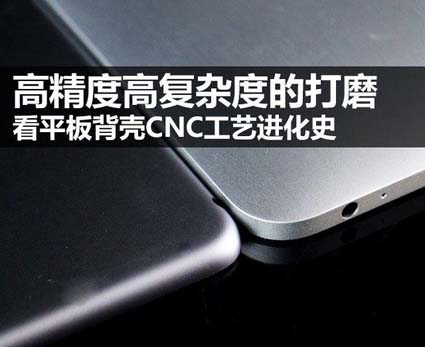
What is a CNC?
CNC is commonly known as "CNC machine tools". I believe that many people have heard of this concept. It is an automated machine controlled by a program. The control system can logically process a program having control codes or other symbolic instructions and decode it by a computer. So that the numerical control equipment to perform well-defined actions, a piece of original metal sheet through a long time precision processing, and finally hit the desired shape.
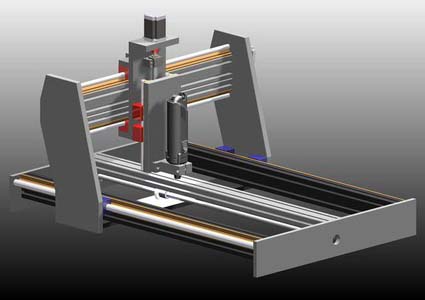
The control system can logically process the control code, and the blank can be processed into a semi-finished product part through tool cutting.
◆ What products work molding application of CNC machining technology?
In practical applications, CNC molding technology with metal materials can create more precise product accuracy and bring better texture. At present, the most representative product on the tablet market is the Apple iPad series and the Nokia N1.
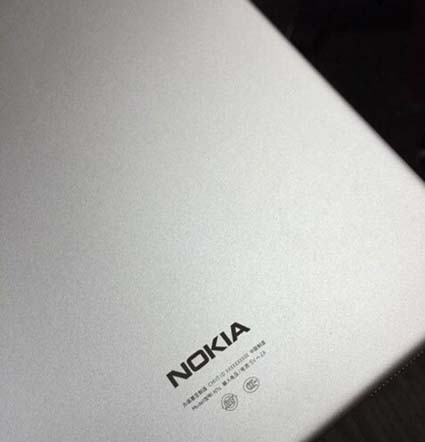
Nokia N1 and iPad series products adopt CNC process casing
2: An iPad Makes More People Know About CNC Processes
The first iPad released on January 28, 2010, and quickly won the market, and its success in addition to its high performance, the CNC process shell process is one of the highlights, its color is still its shape on the "high value", has been more liked by consumers. It can be said that the iPad generation adopts a CNC process to allow more people to understand the technology.
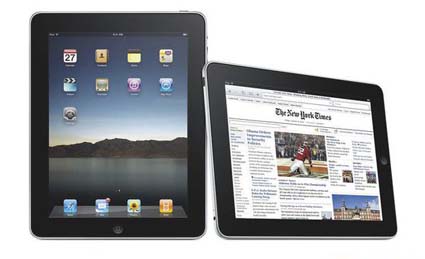
First generation iPad release, High-precision and high-complexity grinding CNC process shell is its highlight
◆ The initial application of the first generation iPad to the fuselage thickness of 13.4mm
The thickness of the first generation iPad body is 13.4mm, CNC molding technology with magnesium alloy shell, to bring the product a more intense metal texture. Although from the perspective of our current eyes, the shell thickness is somewhat unsatisfactory. But at the time in terms of background, the process has just applied to flat products, has been able to do so is not easy.
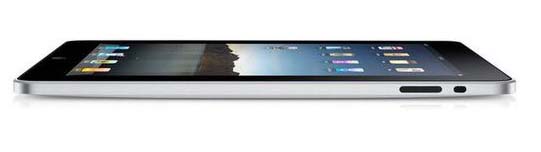
The initial application of the first iPad to the fuselage thickness of 13.4mm, the process is not so perfect
◆ Focus on more appearance is not too much internal design
At the beginning of the design, the main focus of the iPad generation of CNC shells was appearance, The body is smooth when gripped, but there is a grainy impression, making it feel better to play the product. In addition, the outer corners of the shell are rounded, making it more portable and giving people a visual experience.
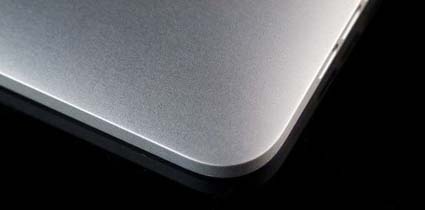
iPad generation using CNC technology, shell touch is a certain degree of granularity
In terms of internal design, the inner performance of the iPad shell is relatively rough. The fixing method of the internal screws and the design of the “baffle” are more abrupt, and the overall design sense inside the housing is poor. However, the presence of its striped design can provide better space for components and ensure the performance of the product. The thickened design of the shell key position, to a certain extent, guarantees the fixation of its function keys.
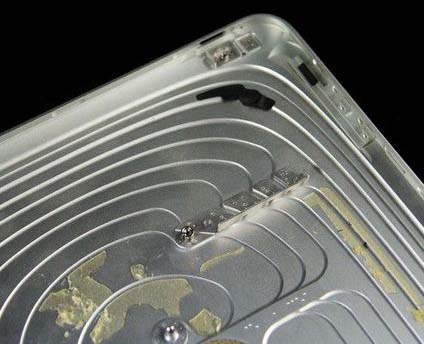
In addition to the use of CNC technology iPad internal screw fixation and "baffle" design is more abrupt
3: The external process of the shell is improved. More beautiful and delicate
■The CNC process tends to be mature Nokia N1 and iPad Air 2 adopt this technology
With the development of CNC technology, more and more flat-panel products have been applied. The most representative ones are Apple's latest series of iPad Air 2 and Nokia N1 Tablet PCs. Both of these products use CNC technology.
What are the improvements in technology now?
What are the perfect designs?
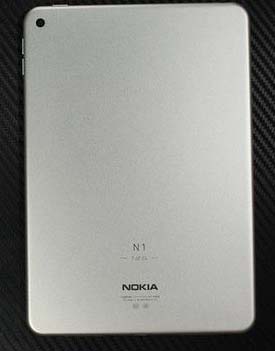
Nokia N1 shell using the latest CNC technology
In terms of appearance, the products made by this process are more “slim” and the overall visual sense of the shell gives a sense of impact. The appearance of the product has become more exquisite (of course, this has a lot to do with the upgrading of the screen), and the border becomes more rounded, not a rigid "box" design, more comfortable when hand-held, The change can be said to be an improvement in craftsmanship.
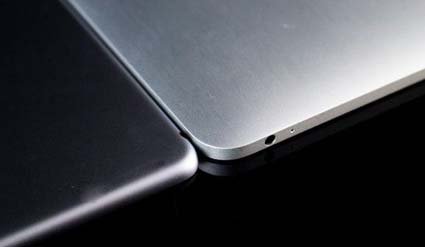
The border around the Nokia N1 has become more rounded, not a rigid "box" design
In addition, there are certain improvements in the details of the button position, so that the button position does not stay on the side frame, but to a certain extent close to the backplane. In this way, reducing the thickness of the fuselage does not affect the user's operation, and it can be said to be of double benefit. The realization of this design depends to a certain extent on the improvement of the process.
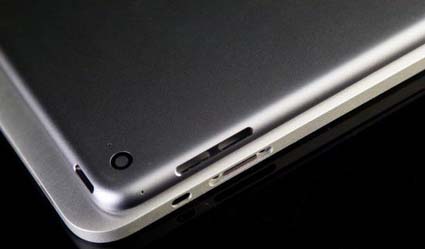
There is also a certain improvement in the details of the key position. It is easy to operate and also more beautiful.
The recessed design of the interface, in the previous technology has also been a certain improvement, Even if there is a certain gap between the positions of the keys, this design makes the position of the volume keys adjacent to the power-off key set, which is more beautiful on the side of the body.
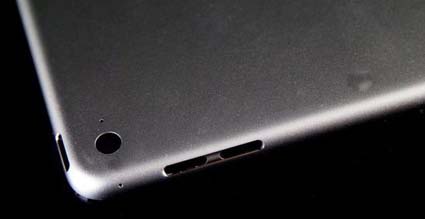
Closer and smaller gaps between two key positions The precision of the CNC process perfectly supports the design
4: Internal design Beautiful and more reasonable design
Compared to the outside of the housing, the interior of the CNC housing is more attractive to the author, Now that the CNC has become “clean and neat” inside the housing, the screw fixings have become “small”. The location is close to the border, and it does not give people a sense of unexpected design. The overall design has been greatly improved.
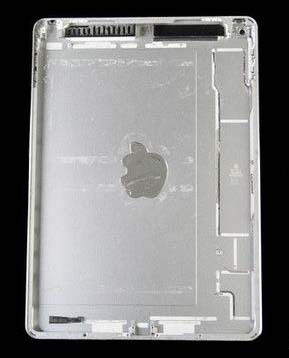
iPad Air 2 shell CNC process, the internal becomes "neat"
At the initial stage of the CNC process application, the thickness of the four perimeter corners is the same as the border and there is no special design. Today, the body shell thickening corner after processing, can cope with a strong impact. This area is where the tablet is most likely to bump, so it should be well protected. This design on the one hand reduces the weight of the fuselage (reduces the overall thickness of the shell) and increases the overall firmness of the fuselage.
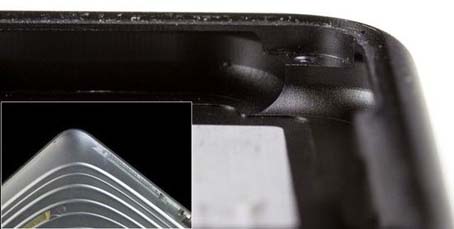
Nokia N1 shell four peripheral corner thickening processing to enhance the overall strength of the fuselage
At the interface of the fuselage, CNC process products are now fixed with complex structures to ensure the durability of the interface. If you’re playing tablet computers more verbally, then charge your tablet every day. The repeated insertion and removal of the power cord from the charging cable is a test of the durability of the interface. Nokia is considering this point, only to use the complex structure of the interface commonly used in the fuselage to make it stable and fixed.
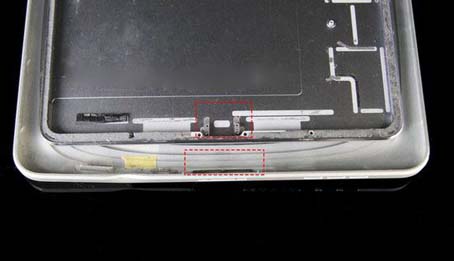
CNC process products using a complex structure be secured, thereby ensuring the durability of the interface
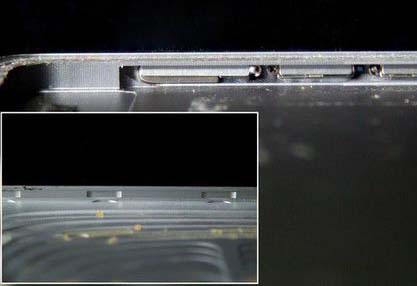
Groove design is also a manifestation of precision manufacturing
It has been more than four years since the generation of the iPad application CNC process. During this time, whether it is the appearance of the shell or its internal integration, there has been a clear improvement. It can be said that in the current process, it is the highest precision and high-complexity grinding process. After that four years, what kind of heights will the CNC process achieve? No one of us can be sure. I believe that with the improvement of design in the future, the process will be more precise and reach a level that we could not imagine.