Stamping Compound Die Design And Production
Comparison of Positive compound die and Flip chip compound die:
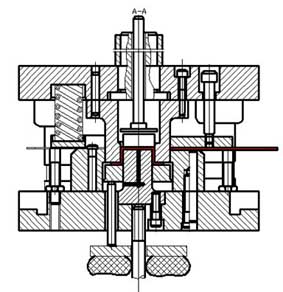
Positive compound die suitable for punching relatively soft, thin sheet material, require a higher flatness blanking member may also be made smaller hole punching margins blanking member.
Flip chip compound die should not be used for punching blanks with small hole margins.
However, the Flip compound die has a simple structure, and can directly use the press device of the press to carry out the unloading of the pusher, is reliable, easy to operate, and provides favorable conditions for mechanized output, so the application is very extensive.
According to the analysis of the parts, the precision requirements of the parts are lower, and the margins of the holes are larger. In order to improve economic efficiency and simplify the mold structure, it is suitable to use flip-chip composite mold production.
According to the above analysis, it is determined that the production of the part is produced by Flip compound die.
2. Overall design of the mold
2.1 Selection of mold type
After analysis, the workpiece dimensional accuracy is not high, the shape is simple, but the workpiece yield is large, according to the material thickness. In order to ensure a high productivity of the die, by comparison, it is decided to implement a process plan in which the process is concentrated. Elastic unloading device, flip-chip composite structure with natural leakage.
2.2 Operation and positioning method
2.2.1 Mode of operation
The production volume of parts is large, but the production is reasonably arranged, and the automatic feeding method is adopted to improve economic benefits.
2.2.2 Positioning method
Because the guide pin and the fixed stop pin have a simple structure, they are easy to manufacture. And the mold adopts the strip material, according to the specific structure of the mold and the economic benefit, the feeding direction of the control strip adopts the guide pin, the feeding step is controlled, and the fixed guide pin is adopted.
2.3 Unloading, product ejection method
2.3.1 Unloading method
The elastic pressure discharge plate has the dual functions of discharging and pressing, and is mainly used for the sheet material whose material thickness is less than or equal to 2 mm, because the pressing material acts, the punching piece is relatively flat. The single-edge clearance between the discharge plate and the punch is selected (0.1-0.2) t. If the elastic discharge plate is to guide the punch, the matching clearance between the two should be smaller than the punching clearance.
Often used as blanking die, punching die. The straightness of the workpiece is relatively high, the material thickness is 2mm relatively thin, and the unloading force is not large, because the elastic pressure discharge mold is more convenient than the rigid discharge mold.
The operator can see the moving strip fed in the mold, and the elastic piece is applied to the stripper plate is a flexible force, without damage to the workpiece surface, it can be elastic unloading.
2.3.2 Product ejection mode
Flip compound die due to production and use of product is ejected downwardly preferred embodiment.
2.4 Determine the feeding method
Because the selected stamping equipment is an open press, the vertical feeding mode is adopted, that is, feeding from front to back.
3. Determine Oriented Approach
Option One: A diagonal guide frame is used. Since the guide post is mounted on the diagonal of the center of the mold pressure, the upper mold base slides smoothly on the guide post. It is often used for blanking die or composite die for transverse feed progressive die or longitudinal feed.
Option II: The rear side guide frame is used. Since the front and left and right are not limited, feeding and operation are convenient. Because the guide post is installed on the rear side, the eccentricity will cause the guide bush to wear on one side, which will seriously affect the service life of the mold and cannot use the floating mold handle.
Option three: Four guide column formwork. It has the advantages of stable guiding, accurate and reliable guiding, and good rigidity. It is often used for stamping parts with large stamping parts or high precision requirements, as well as automatic stamping formwork for mass production.
Option four:
Intermediate guide column formwork.
The guide post is mounted on the symmetry line of the mold, and the guide is stable and accurate. Can only feed in one direction.
According to the above schemes, combined with the mold structure and feeding mode, in order to improve the life of the mold and the quality of the workpiece, the guiding method of the rear guide column is adopted. That is, the scheme 1 is the best.
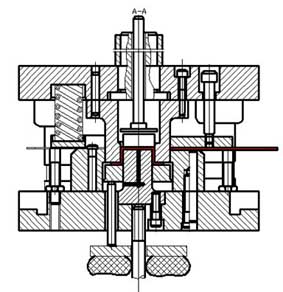
Positive compound die suitable for punching relatively soft, thin sheet material, require a higher flatness blanking member may also be made smaller hole punching margins blanking member.
Flip chip compound die should not be used for punching blanks with small hole margins.
However, the Flip compound die has a simple structure, and can directly use the press device of the press to carry out the unloading of the pusher, is reliable, easy to operate, and provides favorable conditions for mechanized output, so the application is very extensive.
According to the analysis of the parts, the precision requirements of the parts are lower, and the margins of the holes are larger. In order to improve economic efficiency and simplify the mold structure, it is suitable to use flip-chip composite mold production.
According to the above analysis, it is determined that the production of the part is produced by Flip compound die.
2. Overall design of the mold
2.1 Selection of mold type
After analysis, the workpiece dimensional accuracy is not high, the shape is simple, but the workpiece yield is large, according to the material thickness. In order to ensure a high productivity of the die, by comparison, it is decided to implement a process plan in which the process is concentrated. Elastic unloading device, flip-chip composite structure with natural leakage.
2.2 Operation and positioning method
2.2.1 Mode of operation
The production volume of parts is large, but the production is reasonably arranged, and the automatic feeding method is adopted to improve economic benefits.
2.2.2 Positioning method
Because the guide pin and the fixed stop pin have a simple structure, they are easy to manufacture. And the mold adopts the strip material, according to the specific structure of the mold and the economic benefit, the feeding direction of the control strip adopts the guide pin, the feeding step is controlled, and the fixed guide pin is adopted.
2.3 Unloading, product ejection method
2.3.1 Unloading method
The elastic pressure discharge plate has the dual functions of discharging and pressing, and is mainly used for the sheet material whose material thickness is less than or equal to 2 mm, because the pressing material acts, the punching piece is relatively flat. The single-edge clearance between the discharge plate and the punch is selected (0.1-0.2) t. If the elastic discharge plate is to guide the punch, the matching clearance between the two should be smaller than the punching clearance.
Often used as blanking die, punching die. The straightness of the workpiece is relatively high, the material thickness is 2mm relatively thin, and the unloading force is not large, because the elastic pressure discharge mold is more convenient than the rigid discharge mold.
The operator can see the moving strip fed in the mold, and the elastic piece is applied to the stripper plate is a flexible force, without damage to the workpiece surface, it can be elastic unloading.
2.3.2 Product ejection mode
Flip compound die due to production and use of product is ejected downwardly preferred embodiment.
2.4 Determine the feeding method
Because the selected stamping equipment is an open press, the vertical feeding mode is adopted, that is, feeding from front to back.
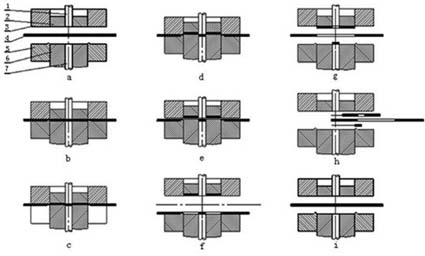
3. Determine Oriented Approach
Option One: A diagonal guide frame is used. Since the guide post is mounted on the diagonal of the center of the mold pressure, the upper mold base slides smoothly on the guide post. It is often used for blanking die or composite die for transverse feed progressive die or longitudinal feed.
Option II: The rear side guide frame is used. Since the front and left and right are not limited, feeding and operation are convenient. Because the guide post is installed on the rear side, the eccentricity will cause the guide bush to wear on one side, which will seriously affect the service life of the mold and cannot use the floating mold handle.
Option three: Four guide column formwork. It has the advantages of stable guiding, accurate and reliable guiding, and good rigidity. It is often used for stamping parts with large stamping parts or high precision requirements, as well as automatic stamping formwork for mass production.
Option four:
Intermediate guide column formwork.
The guide post is mounted on the symmetry line of the mold, and the guide is stable and accurate. Can only feed in one direction.
According to the above schemes, combined with the mold structure and feeding mode, in order to improve the life of the mold and the quality of the workpiece, the guiding method of the rear guide column is adopted. That is, the scheme 1 is the best.