Process Measures To Prevent Sharpening Crack in Cemented Carbide Tools
Carbide inserts have high hardness, high brittleness, poor thermal conductivity and high heat shrinkage. They should usually be sharpened with diamond grinding wheels. However, because diamond wheels are expensive and difficult to repair after wear, many factories still use ordinary grinding wheels for sharpening. In the sharpening process, due to the high hardness of the cemented carbide, the abrasive grains of the ordinary grinding wheel are easily passivated. Severe friction causes local high temperature on the surface of the blade, which creates additional thermal stress, which is highly susceptible to thermal deformation and thermal cracking, directly affecting tool life and processing quality. Therefore, necessary measures should be taken to prevent the occurrence of sharpening cracks. Through the processing practice, the following process measures that can effectively prevent or reduce the sharpening cracks are summarized.
1. Negative edge sharpening method
The negative edge sharpening method refers to grinding a negative edge on the rake face or the flank face before sharpening the tool. Cemented carbide is a hard and brittle material. When the grinding wheel is vibrated, the tool is subjected to an impact load and is prone to cracking. At the same time, the instantaneous temperature rise and cooling of the grinding zone causes thermal stresses to exceed the strength limit of the cemented carbide and cause thermal cracking. The use of the negative edge sharpening method can increase the blade strength, enhance the blade's vibration resistance and the ability to withstand impact loads, and increase the heat receiving area to prevent the grinding heat from being directed to the blade, thereby reducing or preventing cracks.
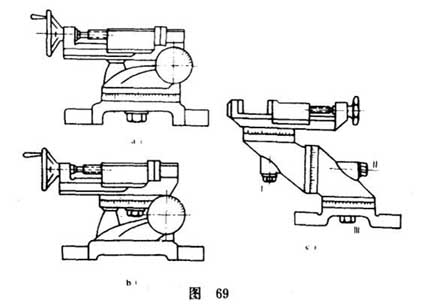
2. Impregnating the grinding wheel with molybdenum disulfide
At room temperature, and powdery molybdenum disulfide mixed solution made of ethanol. Then, in a closed container (to prevent evaporation of ethanol), a new ordinary grinding wheel is immersed in the mixed solution, and after 14 hours, it is taken out and naturally dried for 18 to 20 hours to completely dry the grinding wheel. The inner space of the grinding wheel treated by the above is filled with molybdenum disulfide, which can lubricate the abrasive grains, so that the grinding wheel has good chip removal and is not easy to block. Tests have shown that after grinding the carbide insert with a grinding wheel impregnated with molybdenum disulfide: The grinding is sharp, the abrasive grains are not easy to be passivated, the workpiece deformation is small, the chip discharge is smooth, and the shape of the grinding chips is basically strip-shaped, which can take away most of the grinding heat, thereby improving the grinding effect and improving the blade yield.
3. Reasonable use of grinding amount
If the friction is too large during the sharpening process, the grinding temperature will rise sharply and the blade will be prone to bursting. Therefore, it is very important to use the grinding amount reasonably. The most common reasonable grinding dosage is: The circumferential speed v = 10 ~ 15 m / min, the feed amount f vertical = 0.5 ~ 1.0 m / min, f transverse = 0.01 ~ 0.02 mm / stroke. When hand sharpening, the vertical and horizontal feeds should not be too large.
4. Other process measures
Insufficient rigidity of the tool bar, unstable tool clamping, and spindle runout of the machine tool may cause sharpening cracks. Therefore, the machining system consisting of machine tools, grinding wheels, clamps and tools should be sufficiently rigid and should control the axial and radial runout of the grinding wheel. There are many factors causing the sharpening crack of the cemented carbide tool. Only when the appropriate grinding wheel is selected and a reasonable grinding process is adopted, the crack generation can be effectively avoided and the sharpening quality can be improved.
1. Negative edge sharpening method
The negative edge sharpening method refers to grinding a negative edge on the rake face or the flank face before sharpening the tool. Cemented carbide is a hard and brittle material. When the grinding wheel is vibrated, the tool is subjected to an impact load and is prone to cracking. At the same time, the instantaneous temperature rise and cooling of the grinding zone causes thermal stresses to exceed the strength limit of the cemented carbide and cause thermal cracking. The use of the negative edge sharpening method can increase the blade strength, enhance the blade's vibration resistance and the ability to withstand impact loads, and increase the heat receiving area to prevent the grinding heat from being directed to the blade, thereby reducing or preventing cracks.
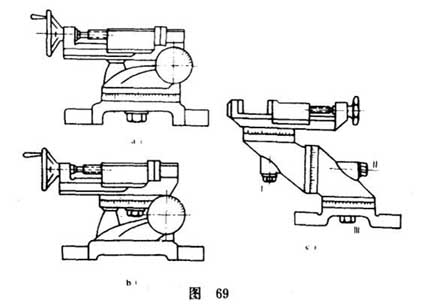
2. Impregnating the grinding wheel with molybdenum disulfide
At room temperature, and powdery molybdenum disulfide mixed solution made of ethanol. Then, in a closed container (to prevent evaporation of ethanol), a new ordinary grinding wheel is immersed in the mixed solution, and after 14 hours, it is taken out and naturally dried for 18 to 20 hours to completely dry the grinding wheel. The inner space of the grinding wheel treated by the above is filled with molybdenum disulfide, which can lubricate the abrasive grains, so that the grinding wheel has good chip removal and is not easy to block. Tests have shown that after grinding the carbide insert with a grinding wheel impregnated with molybdenum disulfide: The grinding is sharp, the abrasive grains are not easy to be passivated, the workpiece deformation is small, the chip discharge is smooth, and the shape of the grinding chips is basically strip-shaped, which can take away most of the grinding heat, thereby improving the grinding effect and improving the blade yield.
3. Reasonable use of grinding amount
If the friction is too large during the sharpening process, the grinding temperature will rise sharply and the blade will be prone to bursting. Therefore, it is very important to use the grinding amount reasonably. The most common reasonable grinding dosage is: The circumferential speed v = 10 ~ 15 m / min, the feed amount f vertical = 0.5 ~ 1.0 m / min, f transverse = 0.01 ~ 0.02 mm / stroke. When hand sharpening, the vertical and horizontal feeds should not be too large.
4. Other process measures
Insufficient rigidity of the tool bar, unstable tool clamping, and spindle runout of the machine tool may cause sharpening cracks. Therefore, the machining system consisting of machine tools, grinding wheels, clamps and tools should be sufficiently rigid and should control the axial and radial runout of the grinding wheel. There are many factors causing the sharpening crack of the cemented carbide tool. Only when the appropriate grinding wheel is selected and a reasonable grinding process is adopted, the crack generation can be effectively avoided and the sharpening quality can be improved.