Precision mirror grinding and machining of steel-bonded carbide
Steel-bonded cemented carbide is a bonded phase of tool steel or alloy steel. The refractory metal carbide (mainly WC, TiC) is prepared as a hard phase by powder metallurgy. Its structural feature is that the fine hard phase grains are dispersed in the steel matrix. The hard phase in the alloy primarily imparts high hardness and high wear resistance to the material, which in turn imparts steel properties to the material. Therefore, the steel-bonded cemented carbide has the comprehensive properties of steel and cemented carbide, making it widely used in various fields.
However, its own processing and manufacturing is very difficult, especially precision machining. This is because the hardness of the hard phase and the binder phase are largely different, the steel base is easily removed, and the hard spot is not easily removed. And the crystal grains thereof are easily peeled off from the surface of the alloy, thereby forming pores having the same size as the hard phase grains on the surface. At the same time, the toughness of the steel base is large. Under certain conditions of grinding temperature, contact pressure and relative speed, the grinding debris fills the pores between the abrasive grains, so that the grinding wheel sharply blocks the surface of the workpiece to generate burns. Therefore, the conventional processing method is difficult to obtain a low surface roughness, and the multi-stage polishing efficiency is low and the cost is high.
Electrolytic continuous dressing (ELID) metal combined with ultra-fine grain diamond grinding wheel is used to grind steel-bonded cemented carbide with a surface roughness of up to 10 nm and high efficiency. The use of ELID mirror grinding technology for precision machining of steel-bonded cemented carbides makes it easy to obtain low-roughness mirrors.
I. The basic principle of ELID grinding technology
On-line electrolytic dressing mirror grinding is a new ultra-precision machining technology developed in Japan in the early 1990s. It uses cast iron or iron fiber bond diamond or CBN grinding wheel to perform on-line electrolytic sharpening grinding of the grinding wheel by utilizing the anode dissolution phenomenon during electrolysis. The electrolysis power source uses a DC pulse power source, and the electrolyte uses an aqueous solution of a weak electrolyte. The cast iron grinding wheel is an anode. In the electrolysis, the iron element on the surface of the grinding wheel becomes an Fe2O3 oxide film, so that the unelectrolyzable diamond or CBN abrasive protrudes from the surface of the grinding wheel. The blunt abrasive is peeled off in time as the electrolysis progresses, so that the grinding wheel is always in a sharp state. At the same time, the generated oxide film acts to inhibit the electrolysis process from continuing, so that the wear of the grinding wheel is not too fast. When the abrasive grains on the surface of the grinding wheel wear, the oxide film is scraped off by the surface of the workpiece, and the electrolysis process continues, and the surface of the grinding wheel is continuously trimmed. This is a cyclical process that avoids excessive wear of the grinding wheel and automatically maintains the grinding state of the grinding wheel surface. See below.
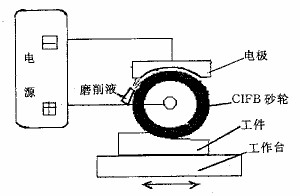
Schematic diagram of ELID grinding principle
II.Application of ELID Grinding Technology to Steel Bonded Cemented Carbide
The steel-bonded cemented carbide was mirror-polished, and the surface roughness of the workpiece was Ra=0.003 μm to 0.011 μm. If a finer grinding wheel (W1 or higher) is used, the Ra value will be significantly reduced and a better surface roughness will be obtained.
The surface roughness of the workpiece is not only closely related to the particle size and type of the abrasive used, but also closely related to the ratio of the grinding fluid. Grinding fluids with different compositions and contents have very different chemical properties, and the surface roughness is different.
Using HDMY-110 and HDMY-200 grinding fluids, we processed specimens of mirrored optical glass, sapphire, hardened steel, hard alloy, cermet, PCBN, monocrystalline silicon wafer and other materials. However, for steel-bonded cemented carbide, it is impossible to process a mirror surface that can reach 13. The special grinding fluid HDMY-201 and the diamond and CBN mixed abrasive iron-based grinding wheel were used, and the steel-bonded cemented carbide reaching the mirror surface (14) was ground under the same conditions. This is mainly because the composition and content of the grinding fluid have a great influence on the electrolysis speed, the film formation speed, the film thickness, the hardness of the film, and the surface texture of the workpiece to be processed.
Depending on the material being processed, the composition and ratio of the grinding fluid and the type and particle size of the iron-based abrasive can be adjusted reasonably to obtain the best grinding state. This results in a lower Ra value and meets the requirements of precision machining.