Plasma Polishing Step After 3D Printing of Metal Parts
What is plasma polishing?
The plasma is the fourth form of substance, which is a phenomenon of electromagnetic gas discharge. The plasma is dissolved in polishing Brine under high temperature and pressure. Under high temperature and high pressure, electrons will escape from the nucleus and the nucleus will form a positively charged ion. When these ions reach a certain amount, they can become a plasma state, and the plasma state energy is large. When these plasma and the object to be polished are rubbed, the workpiece is polished without dead angle, which will make the object achieve the effect of surface brightness in an instant.
Plasma polishing technology is mainly developed for the polishing problems of stainless steel, zinc alloy, copper alloy and aluminum alloy on the market. This technology removes the burrs on the stainless steel surface while achieving a mirror finish on the surface. High purity, effectively reducing the contamination of electronic products. The characteristics of the polished product are mainly reflected in: Reduced roughness, improved finish, precision, hard and durable, reduced notch sensitivity, smooth and tidy, reduced friction coefficient, reduced wear, etc.
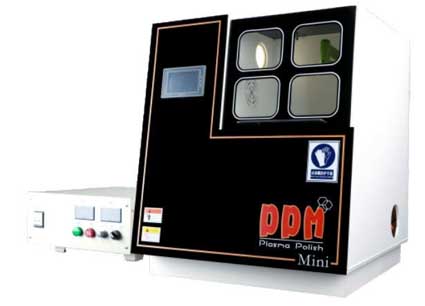
Electrolyte plasma polishing technology is suitable for polishing metal surfaces, eliminating burrs, sharpening sharp edges, cleaning weld seams, removing oxidized colors, oxide scales and stains on the surface of materials, and removing oil from surfaces.
The technology has broad application prospects, including: Polishing of complex structural parts, Surface treatment of aerospace precision parts, Surface polishing of high quality parts of weapons, Finishing of all types of machine and instrument components, Polishing and finishing of corrosion resistant parts of chemical equipment, Polishing of medical equipment and medical implant parts, Polishing of propellers and hydraulic equipment blades, Polishing of food processing equipment parts and stainless steel tableware products, And polishing of sanitary technology equipment, lighting equipment parts, furniture parts, etc.
The characteristics of the polished product are mainly reflected in: The metal surface is free of oil and polishing wax, and the roughness is reduced, which improves the surface smoothness and brightness of the metal, and has no stress change. Plasma is also called the fourth state of matter. It is an electromagnetic gas discharge phenomenon that partially ionizes gaseous particles. Such ionized gases include atoms, molecules, radicals, ions, and electrons. The plasma is that at high temperature and pressure, the polishing agent is water-soluble, and the electrons escape from the nucleus. The nucleus forms a positively charged ion that can become a plasma when these ions reach a certain amount. The energy of plasma state is very large, when these plasma and the object to be polished friction, in an instant will make the object achieve the effect of surface brightness. Plasma polishing is a new metal surface treatment process.Only the molecular layer on the surface of the workpiece reacts with the plasma. The atoms in the molecule are generally 0.1-0.3 nm apart and the treatment depth is 0.3-4.5 nm. The surface roughness of the polishing object is in the range of 1 mm. Therefore, plasma chemical activation of workpiece surface, removal of surface molecule contamination layer, cross-linking surface chemicals.
The advantages of plasma polishing. Polishing technology is one of the key technologies for metal surface treatment. Polishing is an indispensable production step in both traditional industries and the digital digital industry. Polishing is the process of finishing the surface of the workpiece. After the polishing process, the surface roughness of the workpiece is reduced. Generally speaking, with the improvement of gloss, the mechanical, physical and chemical properties of the workpiece after polishing are improved to varying degrees. For example, the roughness is lowered, the smoothness is improved, the corrosion resistance is improved, the notch sensitivity is lowered, the friction coefficient is lowered, and the wear is reduced.
The plasma is the fourth form of substance, which is a phenomenon of electromagnetic gas discharge. The plasma is dissolved in polishing Brine under high temperature and pressure. Under high temperature and high pressure, electrons will escape from the nucleus and the nucleus will form a positively charged ion. When these ions reach a certain amount, they can become a plasma state, and the plasma state energy is large. When these plasma and the object to be polished are rubbed, the workpiece is polished without dead angle, which will make the object achieve the effect of surface brightness in an instant.
Plasma polishing technology is mainly developed for the polishing problems of stainless steel, zinc alloy, copper alloy and aluminum alloy on the market. This technology removes the burrs on the stainless steel surface while achieving a mirror finish on the surface. High purity, effectively reducing the contamination of electronic products. The characteristics of the polished product are mainly reflected in: Reduced roughness, improved finish, precision, hard and durable, reduced notch sensitivity, smooth and tidy, reduced friction coefficient, reduced wear, etc.
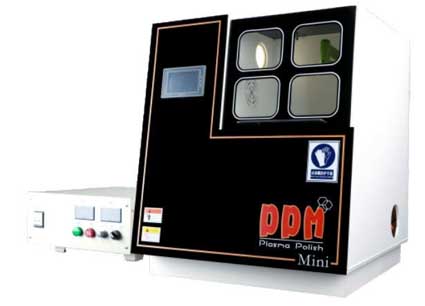
Manufacturing parts with complex geometry and functional integration is one of the main advantages of 3D printing technology. But 3D printed parts are also facing the challenge of improving surface quality. Post-processing 3D printed parts is an effective way to improve surface quality. Plasma polishing is one of the common post-treatment processes for metal 3D printing.
Electrolyte plasma polishing technology is suitable for polishing metal surfaces, eliminating burrs, sharpening sharp edges, cleaning weld seams, removing oxidized colors, oxide scales and stains on the surface of materials, and removing oil from surfaces.
The technology has broad application prospects, including: Polishing of complex structural parts, Surface treatment of aerospace precision parts, Surface polishing of high quality parts of weapons, Finishing of all types of machine and instrument components, Polishing and finishing of corrosion resistant parts of chemical equipment, Polishing of medical equipment and medical implant parts, Polishing of propellers and hydraulic equipment blades, Polishing of food processing equipment parts and stainless steel tableware products, And polishing of sanitary technology equipment, lighting equipment parts, furniture parts, etc.
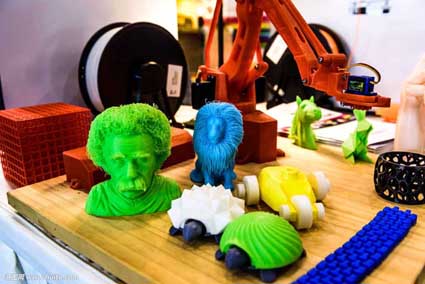
The characteristics of the polished product are mainly reflected in: The metal surface is free of oil and polishing wax, and the roughness is reduced, which improves the surface smoothness and brightness of the metal, and has no stress change. Plasma is also called the fourth state of matter. It is an electromagnetic gas discharge phenomenon that partially ionizes gaseous particles. Such ionized gases include atoms, molecules, radicals, ions, and electrons. The plasma is that at high temperature and pressure, the polishing agent is water-soluble, and the electrons escape from the nucleus. The nucleus forms a positively charged ion that can become a plasma when these ions reach a certain amount. The energy of plasma state is very large, when these plasma and the object to be polished friction, in an instant will make the object achieve the effect of surface brightness. Plasma polishing is a new metal surface treatment process.Only the molecular layer on the surface of the workpiece reacts with the plasma. The atoms in the molecule are generally 0.1-0.3 nm apart and the treatment depth is 0.3-4.5 nm. The surface roughness of the polishing object is in the range of 1 mm. Therefore, plasma chemical activation of workpiece surface, removal of surface molecule contamination layer, cross-linking surface chemicals.
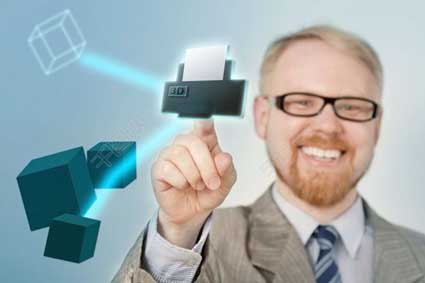
The advantages of plasma polishing. Polishing technology is one of the key technologies for metal surface treatment. Polishing is an indispensable production step in both traditional industries and the digital digital industry. Polishing is the process of finishing the surface of the workpiece. After the polishing process, the surface roughness of the workpiece is reduced. Generally speaking, with the improvement of gloss, the mechanical, physical and chemical properties of the workpiece after polishing are improved to varying degrees. For example, the roughness is lowered, the smoothness is improved, the corrosion resistance is improved, the notch sensitivity is lowered, the friction coefficient is lowered, and the wear is reduced.