Milling Cutter For Deep Groove Milling of Titanium Alloy
Small elastic modulus titanium alloy, small thermal conductivity coefficient of temperature, is a typical difficult materials, especially more difficult when cutting deep grooves. Figure 1 shows an example of machining a deep groove with a width of 4 mm, a depth of 30 mm and a length of 300 mm on a certain titanium alloy part.
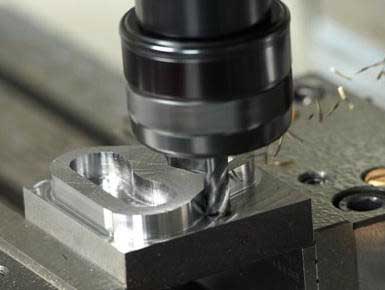
For ordinary materials (e.g., steel 45), the above-mentioned deep groove processing often uses high-speed steel (of W18Cr4V) cutter blade (φ120 × φ40 × 4,60 teeth) is milled, and sufficiently cooled, milled to obtain good results. However, for the titanium alloy TC4 material, when the above-mentioned saw blade milling cutter cuts a blind groove with a depth of 30 mm. When a new blade is used to machine the first to second workpieces, the tool wears and the cutting edge becomes dull. If the sharpening is not performed in time, the extrusion in front of the cutting edge will increase significantly, and the metal deformation in the cutting zone will also increase. At the same time, the back angle of the tool after wear is continuously reduced, thereby increasing the friction between the back of the tool and the machined surface, so that the cutting heat is increased, resulting in a sharp rise in the cutting temperature. When machining the third part, the tip of the knife on both sides of the cutter is obviously burnt out. If the back of the tool tooth and the Chip Pocket are stuck with titanium shavings, it indicates a serious squeeze during the cutting process. This is because, in addition to the small thermal conductivity coefficient of the titanium alloy, the friction coefficient of the titanium alloy material and the tool material is greatly increased, the cutting temperature is rapidly increased, and the chip removal is difficult due to the insufficient chip size. If the above-mentioned worn blade is sharpened, the burnt blade tip should be completely ground out, and the diameter of the blade should be ground by 3 to 4 mm, so that the number of sharpening of a tool is greatly reduced, so that the chip is chipped. The slot becomes smaller. Practice has shown that after such a sharpened blade, only one part can be processed. To this end, in the study, the new blade was tried to jump to increase the chip space of the milling cutter. It was found that this method can increase the life of the tool by about 3 times, and each blade can process 5 parts. This kind of tool can meet the needs of scientific research and trial production, but it can not meet the requirements of mass production.
We use the approach to be jump blade cutter teeth, can be used for milling TC4 titanium alloy blade cutter life has been significantly improved. This method reduces the friction between the tool and the titanium alloy material and increases the chip space, but the potential of this method is limited. From the perspective of production efficiency and cost, cemented carbide (YG15) welding tools and high-speed steel (W6Mo5Cr4V2Al) welding tools should be designed.
The grooving of the above workpieces was tested with cemented carbide welding tools and high-speed steel welding tools (the same cutting conditions), high-speed steel welding tools can process six parts, and YD15 welding tools can process 30 parts. Integrated saw blade milling cutter and skipper blade milling cutter. The test was carried out under the conditions of cutting amount of ap=7 mm, f=0.3 mm/r, and v=26 m/min, and the relationship between tool wear and the number of processing grooves was obtained.
In the deep groove milling of titanium alloy, the wear of the tool is mainly related to the tool material. For the difficult-to-machine material of titanium alloy, the fine-grained hard alloy material should be preferred, which can greatly improve the processing efficiency and processing quality. In addition, the structure of the cutting part of the tool is also very important, considering that the tooth has a large chip space, and it is necessary to consider a reasonable number of teeth to improve the processing efficiency. Therefore, we use 4- or 6-tooth hard alloy welded slot milling cutters to meet the requirements of batch processing of titanium alloy deep grooves.
Tests have shown that for deep groove milling of titanium alloys. Jumping saw milling cutter has a three-fold increase in tool life compared to conventional saw blade milling cutters; The YD15 carbide welding cutter can significantly improve tool life.
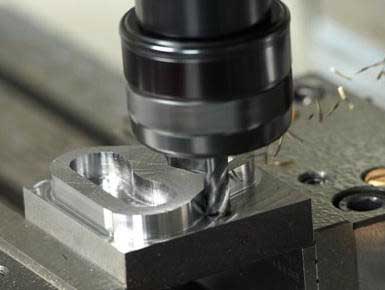
For ordinary materials (e.g., steel 45), the above-mentioned deep groove processing often uses high-speed steel (of W18Cr4V) cutter blade (φ120 × φ40 × 4,60 teeth) is milled, and sufficiently cooled, milled to obtain good results. However, for the titanium alloy TC4 material, when the above-mentioned saw blade milling cutter cuts a blind groove with a depth of 30 mm. When a new blade is used to machine the first to second workpieces, the tool wears and the cutting edge becomes dull. If the sharpening is not performed in time, the extrusion in front of the cutting edge will increase significantly, and the metal deformation in the cutting zone will also increase. At the same time, the back angle of the tool after wear is continuously reduced, thereby increasing the friction between the back of the tool and the machined surface, so that the cutting heat is increased, resulting in a sharp rise in the cutting temperature. When machining the third part, the tip of the knife on both sides of the cutter is obviously burnt out. If the back of the tool tooth and the Chip Pocket are stuck with titanium shavings, it indicates a serious squeeze during the cutting process. This is because, in addition to the small thermal conductivity coefficient of the titanium alloy, the friction coefficient of the titanium alloy material and the tool material is greatly increased, the cutting temperature is rapidly increased, and the chip removal is difficult due to the insufficient chip size. If the above-mentioned worn blade is sharpened, the burnt blade tip should be completely ground out, and the diameter of the blade should be ground by 3 to 4 mm, so that the number of sharpening of a tool is greatly reduced, so that the chip is chipped. The slot becomes smaller. Practice has shown that after such a sharpened blade, only one part can be processed. To this end, in the study, the new blade was tried to jump to increase the chip space of the milling cutter. It was found that this method can increase the life of the tool by about 3 times, and each blade can process 5 parts. This kind of tool can meet the needs of scientific research and trial production, but it can not meet the requirements of mass production.
We use the approach to be jump blade cutter teeth, can be used for milling TC4 titanium alloy blade cutter life has been significantly improved. This method reduces the friction between the tool and the titanium alloy material and increases the chip space, but the potential of this method is limited. From the perspective of production efficiency and cost, cemented carbide (YG15) welding tools and high-speed steel (W6Mo5Cr4V2Al) welding tools should be designed.
The grooving of the above workpieces was tested with cemented carbide welding tools and high-speed steel welding tools (the same cutting conditions), high-speed steel welding tools can process six parts, and YD15 welding tools can process 30 parts. Integrated saw blade milling cutter and skipper blade milling cutter. The test was carried out under the conditions of cutting amount of ap=7 mm, f=0.3 mm/r, and v=26 m/min, and the relationship between tool wear and the number of processing grooves was obtained.
In the deep groove milling of titanium alloy, the wear of the tool is mainly related to the tool material. For the difficult-to-machine material of titanium alloy, the fine-grained hard alloy material should be preferred, which can greatly improve the processing efficiency and processing quality. In addition, the structure of the cutting part of the tool is also very important, considering that the tooth has a large chip space, and it is necessary to consider a reasonable number of teeth to improve the processing efficiency. Therefore, we use 4- or 6-tooth hard alloy welded slot milling cutters to meet the requirements of batch processing of titanium alloy deep grooves.
Tests have shown that for deep groove milling of titanium alloys. Jumping saw milling cutter has a three-fold increase in tool life compared to conventional saw blade milling cutters; The YD15 carbide welding cutter can significantly improve tool life.
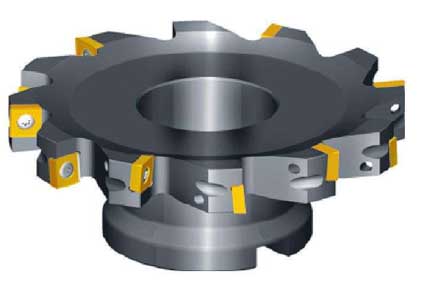