Manufacturing Technology of Stamping Die
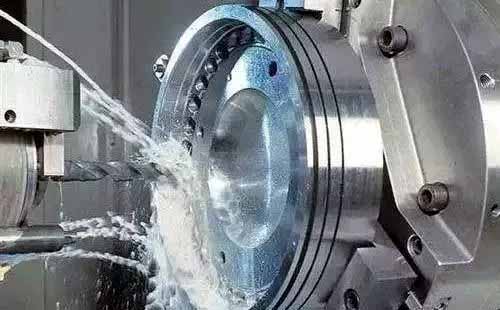
Before we analyze the manufacturing technology of stamping dies. We must first understand the composition of stamping die components.
Type 1Process parts of stamping dies, these parts directly participate in the completion of the process and have direct contact with the stamping blanks. Including working parts, positioning parts, unloading and pressing parts, etc.;
Type 2
The structural parts of the stamping die, such parts do not directly participate in the completion of the process, nor do they have direct contact with the blank. It only guarantees the completion of the mold process, or improves the function of the mold. Including guide parts, fastening parts, standard parts and other parts, as shown in Table 1.1.3. It should be pointed out that not all stamping dies must have the above six parts, especially single-process stamping dies, but working parts and necessary fixed parts are indispensable.
Stamping manufacturing technology
The modernization of stamping die manufacturing technology is the basis for the development of the die industry. With the development of science and technology, advanced technologies such as computer technology, information technology, and automation technology are constantly infiltrating, intersecting, and merging into traditional manufacturing technologies, transforming them, and forming advanced manufacturing technologies. For example, the new stamping die tapping technology has led many stamping manufacturers to reduce costs and caused a panic buying boom.The development of advanced manufacturing technology for stamping dies is mainly reflected in:
High-speed milling
Ordinary milling uses a low feed rate and a large amount of cutting, while high-speed milling uses a high-speed feed rate and a small amount of cutting. Compared with ordinary milling, high-speed milling has the following characteristics:
a. High efficiency: The spindle speed of high-speed milling is generally 15000r/min~40,000r/min, up to 100000r/min. When milling steel, its cutting speed is about 400m/min, which is 5-10 times higher than traditional milling processing; Compared with traditional machining methods (traditional milling, EDM, etc.), the efficiency of machining mold cavities is increased by 4 to 5 times.
B. High precision:
High-speed milling accuracy is generally 10μm, and some accuracy is even higher.
C. High surface quality: Due to the small temperature rise of the workpiece during high-speed milling (about 3°C), there is no metamorphic layer and micro-cracks on the surface, and thermal deformation is also small. The best surface roughness Ra is less than 1μm, which reduces the workload of subsequent grinding and polishing.
D. High-hard materials can be machined: It can mill 50-54HRC steel, and the highest milling hardness can reach 60HRC.
In view of the above-mentioned advantages of high-speed milling, high-speed machining is being widely used in mold manufacturing and is gradually replacing part of grinding and EDM.
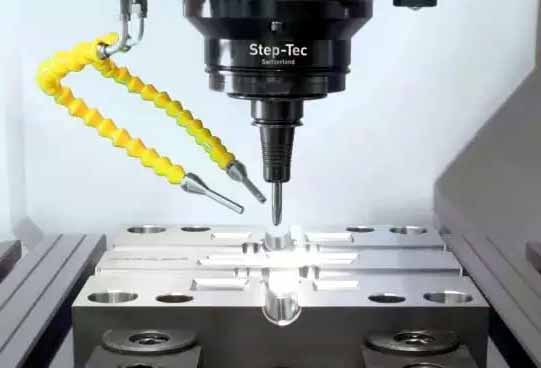
Electric discharge milling
EDM milling (also known as EDM generative machining) is a major development of EDM technology, which is a new technology that replaces the traditional use of forming electrodes to process mold cavities. Like CNC milling, EDM uses high-speed rotating rod-shaped electrodes to process two-dimensional or three-dimensional contours of the workpiece, without the need to manufacture complex and expensive shaped electrodes. The EDSCAN8E EDM machine tool launched by Japan's Mitsubishi Corporation is equipped with an electrode loss automatic compensation system and a CAD/CAM integrated system. The online automatic measurement system and dynamic simulation system reflect the level of today's EDM machine tool.Slow wire cutting technology
The development level of CNC slow-moving wire cutting technology has been quite high, the functions are quite complete, and the degree of automation has reached the level of unattended operation. The maximum cutting speed has reached 300mm2/min, the machining accuracy can reach ±1.5μm, and the machining surface roughness Ra0.1~0.2μm. The development of thin wire cutting technology with a diameter of 0.03~0.1mm can realize one-time cutting of concave and convex molds. It can also cut narrow grooves of 0.04mm and internal fillets with a radius of 0.02mm. The taper cutting technology has been able to perform precision machining of tapers above 30°.Grinding and polishing processing technology:
Grinding and polishing processes are characterized by high precision, good surface quality, and low surface roughness values. It is widely used in precision mold processing. Precision mold manufacturing widely uses advanced equipment and technologies such as CNC forming grinders, CNC optical curve grinders, CNC continuous track coordinate grinders and automatic polishing machines.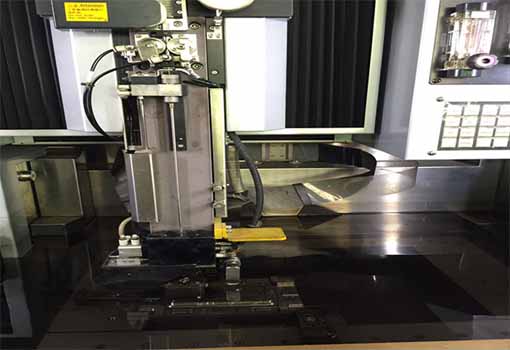
CNC measurement
The complexity of the product structure will inevitably lead to the complexity of the shape of the mold parts. Traditional geometric inspection methods can no longer adapt to the production of molds. Modern mold manufacturing has widely used three-coordinate numerical control measuring machines to measure the geometric quantities of mold parts, and the detection methods of mold processing have also made great progress. In addition to the three-coordinate CNC measuring machine, it can measure the data of complex curved surfaces with high precision. Its good temperature compensation device, reliable anti-vibration protection ability, strict dust removal measures and simple operation steps make it possible to automatically detect on-site.The application of advanced mold manufacturing technology has changed the traditional mold making technology: the quality depends on human factors and difficult to control conditions. The mold quality depends on physical and chemical factors, the overall level is easy to control, and the mold reproduction ability is strong.
High-strength steel
High-strength steel stamping dieToday's high-strength steel and ultra-high-strength steel have achieved the lightweight of vehicles and improved the collision strength and safety performance of vehicles, so they have become an important development direction of automotive steel. However, as the strength of the sheet metal increases, the traditional cold stamping process is prone to cracking during the forming process, which cannot meet the processing requirements of high-strength steel plates. Under the condition that the forming conditions cannot be met, the hot stamping forming technology of ultra-high-strength steel plates has been gradually studied internationally. This technology is a new process that integrates forming, heat transfer and structural phase transformation. It mainly uses the characteristics of increased plasticity of sheet metal and decreased yield strength in the state of high-temperature austenite, and the process of forming through molds. However, thermoforming requires in-depth research on process conditions, metal phase transition, and CAE analysis technology. This technology is monopolized by foreign manufacturers and has slow domestic development.
In the past, in the production of deep-drawing or heavy-stamping workpieces, everyone believed that the pressure-resistant (EP) lubricant was the best choice for mold protection. Sulfur and chlorine EP additives have been mixed into pure oil to increase the life of the mold has a long history. However, with the emergence of a new metal—high-strength steel and strict environmental protection requirements, the value of EP oil-based lubricants has decreased, and even lost the market.
In the molding of high-strength steel at high temperatures, EP oil-based lubricants lose their performance and cannot provide a physical mold protection diaphragm in extreme temperature applications. The extreme temperature type IRMCO high solid polymer lubricant can provide the necessary protection. As the metal deforms in the stamping die and the temperature continues to rise, EP oil-based lubricants will become thinner, and in some cases will reach the flash point or burn (smoke). IRMCO polymer lubricants generally have a much lower consistency when they are sprayed on. As the temperature rises during the forming process, it becomes thicker and tougher. In fact, high molecular polymer extreme temperature lubricants have "heat-seeking" and will stick to the metal, forming a diaphragm that can reduce friction. This protective barrier can allow the workpiece to extend without cracking and bonding when the most demanding workpiece is formed, thereby controlling friction and metal flow. It effectively protects the mold, prolongs the service life of the mold, and improves the strength of stamping.