Application and Quality Inspection of Stamping Parts
Application of stamping parts
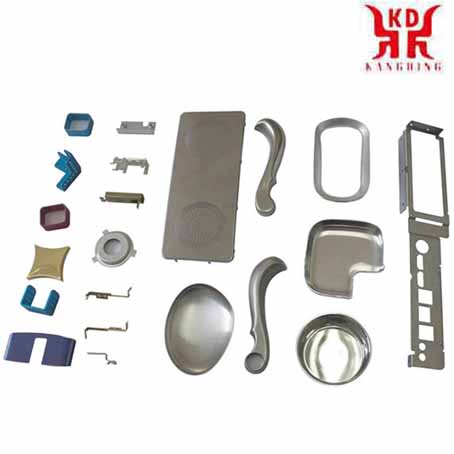
Stamping parts are the production technology that makes the metal sheet directly subjected to the deformation force and deformed in the mold with the help of the power of conventional or special stamping equipment, so as to obtain product parts with a certain shape, size and performance. Sheet metal, die and stamping equipment are the three elements of stamping processing. Stamping is a method of metal cold deformation processing. Therefore, it is called cold stamping or sheet metal stamping, or stamping for short. It is one of the main methods of metal plastic processing (or pressure processing), and it also belongs to material forming engineering technology.
1. Stamping parts in the automotive industry. Such as wheels, gears, etc. are mainly drawn by deep drawing. Mainly concentrated in automobile factories, tractor factories, aircraft manufacturing and other stamping.
2. Stamping parts in the household industry. For example, aluminum windows are mainly punched and formed by punching.
Vehicles, such as cars, boats, airplanes, etc., have many metal parts inside. It needs to be made into a whole stamping part, the shape and size are what you want.
3. Stamping parts in the electrical industry. Such as rice cooker, washing machine and other components. This is a new industry, developed with the development of electrical appliances.
4. Stamping parts for household daily use. Make some crafts, such as tableware, etc.
Stainless steel basins, stainless steel barrels, mainframe shells, and TV shells at home in daily life. The cooking metal linings in the rice cookers are all metal stamping parts. Shapes like basins and barrels need to be stamped and stretched.
5. Stamping parts in the mobile phone industry. For example, card slot, fixed frame, etc.
6. Special stamping parts. Such as stamping of aviation parts.
Quality inspection method of stamping parts
Touch inspectionWipe the surface of the outer cover with clean gauze. The inspector needs to wear touch gloves to touch the surface of the stamping part along the longitudinal direction of the stamping part. This inspection method depends on the inspector's experience. If necessary, oilstone can be used to polish the detected suspicious area and verify it, but this method can be regarded as an effective quick inspection method.
Whetstone polishing
1. First wipe the surface of the outer cover with a clean gauze, and then polish it with oilstone (20×20×100mm or larger). Use relatively small whetstone to polish the arc and hard-to-reach places (for example: 8×100mm semi-circular whetstone)
2. The choice of whetstone particle size depends on the surface condition (such as roughness, galvanizing, etc.). It is recommended to use fine-grained oilstone. The direction of whetstone grinding is basically along the longitudinal direction, and it fits well on the surface of the stamping parts, and some special places can also be supplemented with horizontal grinding.
Flexible gauze polishing
Wipe the surface of the outer cover with clean gauze. Use a flexible sand net to close the surface of the stamping part and grind it to the entire surface in the longitudinal direction. Any pitting or indentation will be easily found.
Oil inspection
Wipe clean the surface of the outer covering stamping parts with clean gauze. Then use a clean brush to apply oil evenly to the entire outer surface of the stamping in the same direction. Put the oiled stamping parts under strong light for inspection. It is recommended that the stamping parts be erected on the body position. This method can easily find tiny pits, pits, and ripples on the stamping parts.
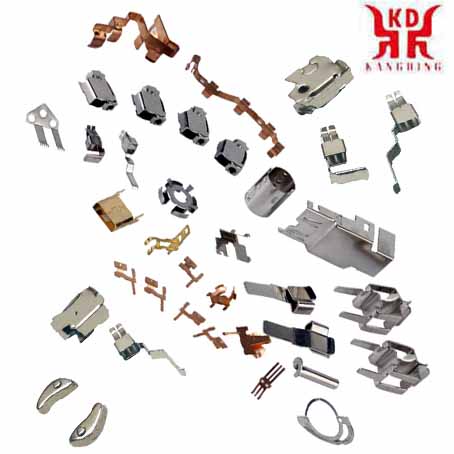
Visual inspection
Visual inspection is mainly used to find abnormal appearance and macro defects of stamping parts.
Inspection fixture
Put the stamping parts into the inspection tool, and inspect the stamping parts according to the operating requirements of the inspection tool manual.
In actual production, process tests similar to the stamping process are commonly used, such as drawing performance test, bulging performance test, etc. to test the stamping performance of the material to ensure the quality of the finished product and a high pass rate.
The precision and structure of the mold directly affect the forming and precision of the stamping parts. Mold manufacturing cost and life are important factors that affect the cost and quality of stamping parts. Mold design and manufacturing require more time, which prolongs the production preparation time of new stamping parts.
The standardization of mold bases and guides and the development of simple molds, compound molds, continuous progressive molds, and the development of rapid mold change devices can reduce the workload and shorten the preparation time for stamping production. It can be suitable for reducing the amount of preparation for stamping production and shortening the preparation time, so that the advanced stamping technology suitable for mass production can be reasonably applied to small batch and multi-variety production.
In addition to forming with hydraulic presses, stamping equipment generally uses mechanical presses. Conveying and other machinery, as well as a mold library and a quick mold change device, and controlled by a computer program, can form a high-productivity automatic stamping production line.
In the case of producing dozens or hundreds of stamping parts per minute, the processes of feeding, stamping, discharging, and discharging waste can be completed in a short time.
Generally, in the stamping process of the workpiece, because the temperature of the stamping process, especially in the cold forging stamping process, will rise quickly, lubricating products must be added for lubrication. If you do not use lubrication and directly press, weld-assemble, the parts without oil on the surface are easy to weld and assemble. Research and practice show that metal inert gas arc welding, tungsten gas shielded arc welding, and resistance welding have good results.
PREV:CNC Stamping Parts Supplier
NEXT:NONE
NEXT:NONE