Iron filings appear when trimming punching dies
When trimming a stamping die, iron scraps generally exist, especially around the lower die scrap knife. Iron shavings not only seriously affect product quality and cleanliness of the mold appearance, but also reduce production efficiency.
According to analysis, this is not perpendicular to the trimming edge; The part does not conform to the mold surface; Secondary cutting of the edge cutting edge; Unreasonable cutting edge clearance; Poor finish cutting edge; Secondary cutting of scrap knives; Cutting edge hardness is not enough; The cutting edge is too deep; The mold process design is unreasonable.
The control measures for this are:
1.Iron scraps are generated at the scrap knife
The generation of iron filings at the scrap knife site is mainly caused by the mold process.
Measures taken:
The shape of the cutting edge of the upper die trimming waste was changed 10mm to make a shape of the cutting edge. And the lower edge of the lower mold scrap is milled hollow.
2.The structure of the plate is out of shape and the gap between the cutting edges is unreasonable
The measures taken for the irregularities of the plate structure and the unreasonable cutting edge clearance are: Use OP10 to draw the plate to buckle the surface of each part of the trimming mold, and at the same time, adjust the gap between the upper and lower edges and adjust the depth of ingestion.
3, edge trimming
To improve the quality of the cross section and the life of the cutting edge when trimming the edge, the following three measures can be adopted:
1) The rounded edge of the trimming edge should be 3mm larger than the rounded corner of the trimmed piece. This can ensure that when the upper and lower molds are completely closed, the trimming edge is cut into 1-3mm and transitions slowly.
2) The upper edge of the trimming edge of the upper die is at an angle of 10 ° with the edge of the trimming piece.
3) Install guide block as much as possible to eliminate the lateral force on the cutting edge.
4. Mold process design
1) Use two or more trimmings. The advantages of using this measure are:
Under the condition of reasonable cutting edge clearance, no burrs and trimming iron chips will be generated, which is convenient for eliminating waste materials, and the quality of the product is stable and the production efficiency is high.
2) The entire side is trimmed. The advantage of adopting this measure is that no burr and trimming iron chips will be generated when the cutting edge clearance is reasonable, it is convenient to eliminate waste, and the quality of the product is stable and the production efficiency is high.
3) Trim in the middle separation area of the two pieces. Originally in the production process, the board was pressed by the cooperation of the upper die pressing core and the lower die punch, and the cutting edge of the upper and lower die was cooperated to cut off the waste material. It is changed to the middle waste material to achieve the final separation of the waste material through the forced breakthrough cutting of the upper mold breakthrough knife and the cooperative cutting of the trimming edges of the convex and concave molds on both sides. In this way, the waste space of the lower mold waste is large, and the waste is easy to be discharged.
According to analysis, this is not perpendicular to the trimming edge; The part does not conform to the mold surface; Secondary cutting of the edge cutting edge; Unreasonable cutting edge clearance; Poor finish cutting edge; Secondary cutting of scrap knives; Cutting edge hardness is not enough; The cutting edge is too deep; The mold process design is unreasonable.
The control measures for this are:
1.Iron scraps are generated at the scrap knife
The generation of iron filings at the scrap knife site is mainly caused by the mold process.
Measures taken:
The shape of the cutting edge of the upper die trimming waste was changed 10mm to make a shape of the cutting edge. And the lower edge of the lower mold scrap is milled hollow.
2.The structure of the plate is out of shape and the gap between the cutting edges is unreasonable
The measures taken for the irregularities of the plate structure and the unreasonable cutting edge clearance are: Use OP10 to draw the plate to buckle the surface of each part of the trimming mold, and at the same time, adjust the gap between the upper and lower edges and adjust the depth of ingestion.
3, edge trimming
To improve the quality of the cross section and the life of the cutting edge when trimming the edge, the following three measures can be adopted:
1) The rounded edge of the trimming edge should be 3mm larger than the rounded corner of the trimmed piece. This can ensure that when the upper and lower molds are completely closed, the trimming edge is cut into 1-3mm and transitions slowly.
2) The upper edge of the trimming edge of the upper die is at an angle of 10 ° with the edge of the trimming piece.
3) Install guide block as much as possible to eliminate the lateral force on the cutting edge.
4. Mold process design
1) Use two or more trimmings. The advantages of using this measure are:
Under the condition of reasonable cutting edge clearance, no burrs and trimming iron chips will be generated, which is convenient for eliminating waste materials, and the quality of the product is stable and the production efficiency is high.
2) The entire side is trimmed. The advantage of adopting this measure is that no burr and trimming iron chips will be generated when the cutting edge clearance is reasonable, it is convenient to eliminate waste, and the quality of the product is stable and the production efficiency is high.
3) Trim in the middle separation area of the two pieces. Originally in the production process, the board was pressed by the cooperation of the upper die pressing core and the lower die punch, and the cutting edge of the upper and lower die was cooperated to cut off the waste material. It is changed to the middle waste material to achieve the final separation of the waste material through the forced breakthrough cutting of the upper mold breakthrough knife and the cooperative cutting of the trimming edges of the convex and concave molds on both sides. In this way, the waste space of the lower mold waste is large, and the waste is easy to be discharged.
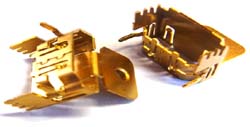