High-speed milling of molds and precision complex parts
In the past few years, high speed milling has been used as an alternative and complement to conventional milling or electrical discharge machining. High-speed milling firmly establishes the status of keeping pace with traditional machining processes. Due to its significant advantages in processing 3D curved surfaces and superhard materials, it is mainly used in mold manufacturing and small batch precision and complex parts processing industries. For the automotive industry, which requires the production of high-volume parts, high-speed milling also has its own unique features. Especially in the field of automotive mold processing, the booming automobile industry in recent years has presented severe challenges to Chinese automotive mold companies. It is not only reflected in the strict requirements of the delivery cycle, but also a comprehensive challenge to the design capability, process capability and manufacturing capability of the automotive mold industry. From the breakthrough of process and manufacturing capabilities, high-speed milling technology has significant processing advantages in shortening the mold manufacturing cycle and improving manufacturing precision.
There are thousands of molds required for a car. The manufacturing cycle and quality of the mold directly affect the production cycle and quality of the car. High-speed milling has unique advantages in the manufacture of complex parts for automotive parts. For example, when the high-speed milling center processes the injection mold of the safety door lock, the hardness of the material used in the mold is 54HRC. The smallest tool used is 0.6mm, the maximum depth of cut is 4.8mm, and the surface roughness is Ra0.4mm. Moreover, the benching process is no longer needed and the machining time is shortened. Another example is when processing the injection mold of the gearbox of the window automatic lifting system, the hardness of the material used in the mold is 58HRC. The workpiece is directly milled up to 85%, and the remaining 15% is completed by electrical machining. The total machining time is 16h, which reduces the machining time by 50%.
III. Processing automotive interior parts mould
The replacement of the car is not only reflected in the improvement of performance, but also in the update of the appearance and interior parts of the car. Most of the automotive interior parts are injection molded parts, and the consumption of the mold is large. High-speed milling can improve the manufacturing precision of the mold and prolong the service life of the mold, thereby improving the quality of the injection molded parts.
It can be seen that high-speed milling has shown great technical advantages in the processing of automotive parts molds and interior parts molds. In terms of processing technology, high-speed milling is mainly used in the following aspects in automotive mold processing.
1. High-speed milling machining electrode
The electrical discharge machining process basically requires two electrodes to machine a workpiece. For better electrical discharge machining, it is necessary to duplicate the same electrode and to distinguish between roughing and finishing electrodes by surface quality. A well-consistent electrode reduces the time required for electrical discharge machining. Traditionally milled electrodes require manual polishing with poor consistency, and the manually polished electrodes always have sharp corners, while tip discharges affect the quality of electrical machining. The high-speed milling of the electrodes eliminates the need for manual polishing, and the near-perfect consistency between the roughing and finishing electrodes optimizes the efficiency of the electrical discharge machining. At the same time, high-speed milling can process thin walls, so that ribbed integral electrodes can be processed. This eliminates the cumulative position error caused by multiple clamping in conventional milling, which saves time and improves quality.
3. Direct high-speed milling to complete hardened steel mold
This method is the biggest manifestation of the advantages of high-speed milling in mold processing. Take the high-speed milling crankshaft and connecting rod forging die of Mikron in the commercial vehicle forging factory of Dongfeng Motor Co., Ltd. as an example.
The traditional milling process is: Roughing of shape → profile milling roughing groove → heat treatment → shape finishing → numerical control electric spark rough, finishing groove → fitter polishing groove → surface strengthening treatment.
The process of high speed milling is: Roughing of shape → Heat treatment → Shape finishing → High-speed milling groove → Surface strengthening treatment.
The use of high-speed milling direct machining to complete hardened steel molds has obvious processing advantages. It reduced total processing costs from more than 27,000 yuan in traditional processing to 22,000 yuan.
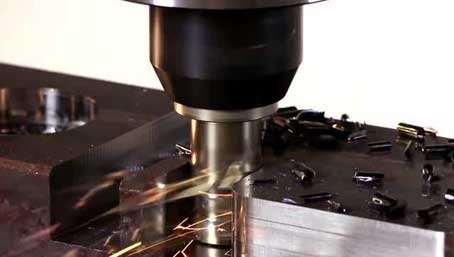
I. Rapid prototyping parts rapid manufacturing
With the boom in the automotive market, the replacement of automobiles has become faster and faster, requiring new product development cycles to be as short as possible. The high-speed milling process has high efficiency and can cut complex profile cavities. In particular, combined with flexible machining methods such as vertical and horizontal conversion 5-axis linkage, it is an excellent solution for rapid manufacturing of prototype parts.
II. Auto parts mold processing
With the boom in the automotive market, the replacement of automobiles has become faster and faster, requiring new product development cycles to be as short as possible. The high-speed milling process has high efficiency and can cut complex profile cavities. In particular, combined with flexible machining methods such as vertical and horizontal conversion 5-axis linkage, it is an excellent solution for rapid manufacturing of prototype parts.
II. Auto parts mold processing
III. Processing automotive interior parts mould
The replacement of the car is not only reflected in the improvement of performance, but also in the update of the appearance and interior parts of the car. Most of the automotive interior parts are injection molded parts, and the consumption of the mold is large. High-speed milling can improve the manufacturing precision of the mold and prolong the service life of the mold, thereby improving the quality of the injection molded parts.
It can be seen that high-speed milling has shown great technical advantages in the processing of automotive parts molds and interior parts molds. In terms of processing technology, high-speed milling is mainly used in the following aspects in automotive mold processing.
1. High-speed milling machining electrode
The electrical discharge machining process basically requires two electrodes to machine a workpiece. For better electrical discharge machining, it is necessary to duplicate the same electrode and to distinguish between roughing and finishing electrodes by surface quality. A well-consistent electrode reduces the time required for electrical discharge machining. Traditionally milled electrodes require manual polishing with poor consistency, and the manually polished electrodes always have sharp corners, while tip discharges affect the quality of electrical machining. The high-speed milling of the electrodes eliminates the need for manual polishing, and the near-perfect consistency between the roughing and finishing electrodes optimizes the efficiency of the electrical discharge machining. At the same time, high-speed milling can process thin walls, so that ribbed integral electrodes can be processed. This eliminates the cumulative position error caused by multiple clamping in conventional milling, which saves time and improves quality.
Comparison of traditional milling and high-speed milling
Processing method - total number of processes - total time (h) - groove processing (h) - machining accuracy (mm) - surface roughness
Traditional milling processing—22—256—179—±0.2~±0.5—Ra1.6
High-speed milling processing—17—120—44—±0.10—Ra0.4
2. Roughing and semi-finishing of the mold
Since high-speed milling can be machined directly on hardened steel, it is theoretically possible to mill the mold directly. However, when the mold cavity has special requirements, it also needs the cooperation of electric machining. Therefore, the roughing and semi-finishing of the mold cavity can be performed by a high-speed milling machine after the material is heat-treated. With a small margin left, the final finishing of the mold is done by electrical discharge machining.
Processing method - total number of processes - total time (h) - groove processing (h) - machining accuracy (mm) - surface roughness
Traditional milling processing—22—256—179—±0.2~±0.5—Ra1.6
High-speed milling processing—17—120—44—±0.10—Ra0.4
2. Roughing and semi-finishing of the mold
Since high-speed milling can be machined directly on hardened steel, it is theoretically possible to mill the mold directly. However, when the mold cavity has special requirements, it also needs the cooperation of electric machining. Therefore, the roughing and semi-finishing of the mold cavity can be performed by a high-speed milling machine after the material is heat-treated. With a small margin left, the final finishing of the mold is done by electrical discharge machining.
3. Direct high-speed milling to complete hardened steel mold
This method is the biggest manifestation of the advantages of high-speed milling in mold processing. Take the high-speed milling crankshaft and connecting rod forging die of Mikron in the commercial vehicle forging factory of Dongfeng Motor Co., Ltd. as an example.
The traditional milling process is: Roughing of shape → profile milling roughing groove → heat treatment → shape finishing → numerical control electric spark rough, finishing groove → fitter polishing groove → surface strengthening treatment.
The process of high speed milling is: Roughing of shape → Heat treatment → Shape finishing → High-speed milling groove → Surface strengthening treatment.
The use of high-speed milling direct machining to complete hardened steel molds has obvious processing advantages. It reduced total processing costs from more than 27,000 yuan in traditional processing to 22,000 yuan.