High-speed milling of sidewalls of thin-walled structural parts
A large number of integral thin-walled structural parts are used in the modern aviation industry. Its main structure consists of side walls and webs. Because of its simple structure, large size and large machining allowance.
The relative rigidity is low, so the processing skill is poor. Under the influence of cutting force, cutting heat, cutting vibration and other factors, it is easy to process deformation, and it is difficult to control the machining accuracy and improve the machining efficiency. The problem of machining deformation and processing efficiency has become an important constraint for the processing of thin-walled structures. Therefore, for the special structure of the milling cutter and the characteristics of the machine tool, an effective milling method is proposed, which makes a new breakthrough in the processing technology of the thin-walled parts.
I. Optimize high speed milling toolpath
The key to machining thin-walled parts with high-speed cutting technology is the stability of the cutting process.
A lot of experimental work has proved that as the wall thickness of the part is reduced, the rigidity of the part is reduced. The machining deformation is increased, and the chattering vibration is prone to occur, which affects the processing quality and processing efficiency of the parts.
A tool path optimization scheme that takes full advantage of the overall rigidity of the part. The idea is to apply as much as possible the unmachined part of the part as a support for the milling part during the cutting process, so that the cutting process is in a state of better rigidity.
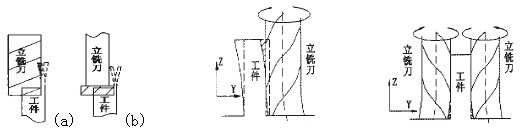
figure 1 Thin wall (sidewall) processing schematic, figure 2 Schematic diagram of single-axis milling, image 3 Schematic diagram of two-axis milling
As shown in Figure 1. For the milling of the side wall, the large radial depth of cut and small axial depth of cut milling are used within the allowable range of cutting. Make full use of the overall rigidity of the part (see Figure 1 (a)). In order to prevent the tool from interfering with the side wall, special shape milling cutters can be selected or designed to reduce the deformation and interference of the tool on the workpiece (see Figure 1(b)).
The use of parallel twin-spindle machining of thin-walled parts effectively controls the machining deformation of thin-walled parts. The machining accuracy and machining efficiency of the parts are significantly improved, and it can be applied to the side wall processing of simple shapes. However, the limitation is that the method can only process the side wall of a simple thin-walled part, and has a requirement for the spacing of the double-spindle of the machine tool, and the structure is complicated, which is not suitable for general use.
The relative rigidity is low, so the processing skill is poor. Under the influence of cutting force, cutting heat, cutting vibration and other factors, it is easy to process deformation, and it is difficult to control the machining accuracy and improve the machining efficiency. The problem of machining deformation and processing efficiency has become an important constraint for the processing of thin-walled structures. Therefore, for the special structure of the milling cutter and the characteristics of the machine tool, an effective milling method is proposed, which makes a new breakthrough in the processing technology of the thin-walled parts.
I. Optimize high speed milling toolpath
The key to machining thin-walled parts with high-speed cutting technology is the stability of the cutting process.
A lot of experimental work has proved that as the wall thickness of the part is reduced, the rigidity of the part is reduced. The machining deformation is increased, and the chattering vibration is prone to occur, which affects the processing quality and processing efficiency of the parts.
A tool path optimization scheme that takes full advantage of the overall rigidity of the part. The idea is to apply as much as possible the unmachined part of the part as a support for the milling part during the cutting process, so that the cutting process is in a state of better rigidity.
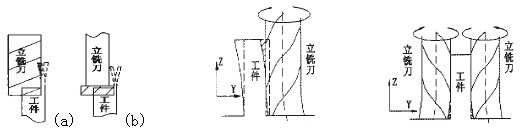
figure 1 Thin wall (sidewall) processing schematic, figure 2 Schematic diagram of single-axis milling, image 3 Schematic diagram of two-axis milling
As shown in Figure 1. For the milling of the side wall, the large radial depth of cut and small axial depth of cut milling are used within the allowable range of cutting. Make full use of the overall rigidity of the part (see Figure 1 (a)). In order to prevent the tool from interfering with the side wall, special shape milling cutters can be selected or designed to reduce the deformation and interference of the tool on the workpiece (see Figure 1(b)).
Efficient milling for deeper cavities and sidewalls. On the basis of studying dynamic milling, it is proposed that a reasonable large aspect ratio tool can effectively solve such problems. The natural frequency of the machine-tool-workpiece process system is adjusted by adjusting the overhang of the tool at higher spindle speeds and power states. Using the stability of the lobe effect, avoiding possible cutting vibrations, the deep cavity and sidewalls can be milled with a large axial depth of cut. The experimental results show that the method has a large metal removal rate and a high surface integrity.
II. Double spindle machining control deformation
II. Double spindle machining control deformation
Due to the milling force, the side wall of the workpiece will be deformed by the “knife” (see Figure 2). Therefore, it is difficult to achieve high-precision machining of thin-walled parts with an end mill. Although the conventional small feed rate and low depth of cut method can satisfy a certain processing precision, the efficiency is relatively low. The parallel dual-spindle scheme can effectively solve the deformation problem of a single spindle machined part. This method requires the application of two end mills of the same radius of gyration, effective length and helix angle, with the left and right turns respectively (see Figure 3). With the parallel double-spindle machining scheme, since the force on both sides of the workpiece is a symmetrical force, the machining deformation of the workpiece can be basically eliminated except for the machining error caused by a small amount of tool deformation.
The use of parallel twin-spindle machining of thin-walled parts effectively controls the machining deformation of thin-walled parts. The machining accuracy and machining efficiency of the parts are significantly improved, and it can be applied to the side wall processing of simple shapes. However, the limitation is that the method can only process the side wall of a simple thin-walled part, and has a requirement for the spacing of the double-spindle of the machine tool, and the structure is complicated, which is not suitable for general use.