Electrical steel Iron Core Manufacturing
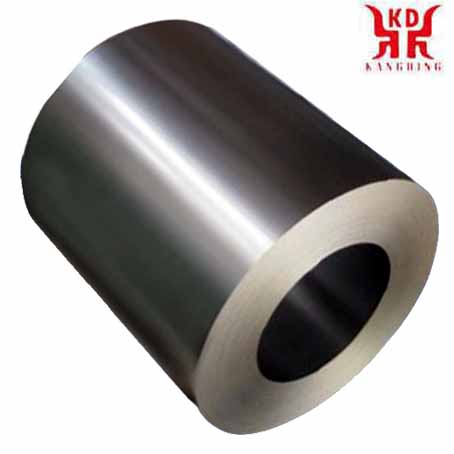
What is a silicon steel sheet iron core? High-precision, flatness silicon steel sheet stamping
Electrical steel (lamination steel, silicon electrical steel, silicon steel, relay steel, transformer steel) is an iron alloy. tailored to produce specific magnetic properties: small hysteresis area resulting in low power loss per cycle, low core loss, and high permeability.Electrical steel, also known as silicon steel sheet, is an important soft magnetic alloy that is indispensable in the power, electronics and military industries, and it is also the metal functional material with the largest output. Mainly used as the iron core of various motors, generators and transformers. Its production process is complicated and the manufacturing technology is strict. Foreign production technologies are protected in the form of patents and regarded as the life of an enterprise. The manufacturing technology and product quality of electrical steel plates are one of the important indicators to measure the level of special steel production and technological development in a country.
The silicon steel sheet core is an iron-silicon alloy formed by adding a small amount of silicon (generally less than 4.5%) to pure iron, called silicon steel. This type of core has the highest saturation magnetic flux density value of 20000Gs; Because of their good magnetoelectric properties, easy mass production, low price, and low mechanical stress, they are widely used in the power electronics industry. Such as power transformers, distribution transformers, current transformers and other iron cores.
Silicon steel sheet, the English name is silicon lamination, it is a kind of ferrosilicon soft magnetic alloy with very low carbon content, and the silicon content is generally 0.5 to 4.5%. Adding silicon can increase the resistivity and maximum permeability of iron, reduce coercivity, core loss (iron loss) and magnetic aging.
(Electrical steel) Silicon steel is the most used material among the magnetic materials used in power transformers. Especially suitable for low frequency and high power. Commonly used are cold-rolled silicon steel sheet DG3, cold-rolled non-oriented electrical steel strip DW, and cold-rolled oriented electrical steel strip DQ. Suitable for all kinds of electronic systems, small and medium power low-frequency transformers and chokes, reactors, inductor cores in household appliances. This kind of alloy has good toughness and can be processed by punching and cutting. The iron core has laminated and winding types. However, the loss increases sharply at high frequencies, and the general use frequency does not exceed 400 Hz.
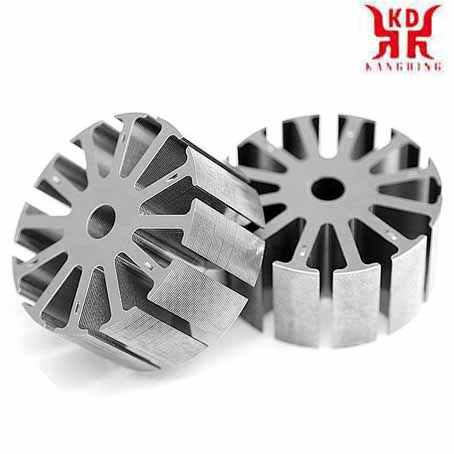
What is electrical steel?
Electrical steel has a history of hundreds of years. Electrical steel includes Si<0.5% electrical steel and silicon steel with Si content 0.5~6.5%. Mainly used as iron cores of various motors, transformers and ballasts, it is an important soft magnetic alloy indispensable in the power, electronics and military industries. Electrical steel uses the largest amount of magnetic materials, and it is also an important energy-saving metal functional material. Electrical steel, especially oriented silicon steel, has complex manufacturing processes and equipment, strict composition control, long manufacturing processes, and many factors that affect performance. Therefore, the quality of oriented silicon steel products is often regarded as an important indicator to measure the technical level of a country's special steel manufacturing, and it has won the reputation of "artistic products" among special steels.Development History
The development stage of hot-rolled silicon steel (1882~1955)The permeability of iron is thousands to tens of thousands times higher than that of air. When the iron core is magnetized, the magnetic flux density is high, which can generate a magnetic field far stronger than the external magnetic field. Ordinary hot-rolled low-carbon steel sheet is the earliest iron core soft magnetic material used in the industry. In 1886, the Westinghouse Electric Company in the United States first used a hot-rolled low-carbon steel plate with an impurity content of about 0.4% to make a transformer laminated core. In 1890, 0.35mm thick hot-rolled low-carbon steel sheet was widely used to manufacture motor and transformer cores. However, due to the low resistivity of low carbon steel, the core loss is large; the carbon and nitrogen content is high, and the magnetic aging is serious. In 1882, Hardfield, England, began to study silicon steel, and in 1898 published the magnetic results of 4.4% Si-Fe alloy. In 1903, the United States obtained the right to use Hardfield's patent. In the same year, the United States and Germany began to produce hot-rolled silicon steel sheets. In 1905, the United States had mass production. In a very short period of time, it has completely replaced ordinary hot-rolled low-carbon steel to manufacture motors and transformers, and its iron loss is more than half lower than that of ordinary low-carbon steel. The period from 1906 to 1930 was a stage in which manufacturers and users had a unified understanding of the cost, mechanical properties, and design and manufacturing reforms of hot-rolled silicon steel sheets, as well as improvements in product quality and output.
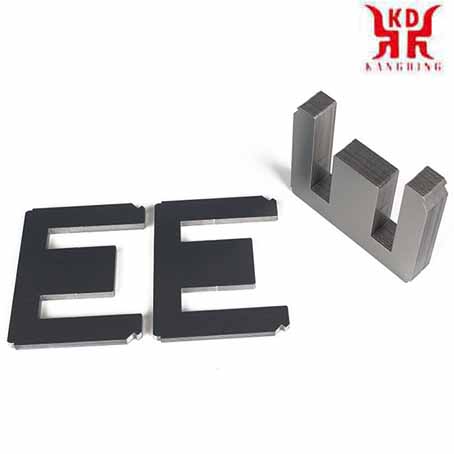
Development stage of cold-rolled electrical steel (1930~1967)
This stage is mainly the development stage of cold-rolled ordinary oriented silicon steel (GO) plate. In 1930, American Gauss began to conduct a large number of experiments using cold rolling and annealing methods to explore the manufacturing process of oriented silicon steel strips with easy magnetization directions of grains and parallel to the rolling direction. In 1933, Gauss used two cold rolling and annealing methods to produce 3% Si steel with high magnetic properties along the rolling direction. In 1934, he applied for a patent and published it publicly. In 1935, Armco Steel Company cooperated with Westinghouse Electric Company for production according to Gaussian patented technology. After that, Armco Steel adopted technologies such as rapid analysis of trace carbon and continuously improved manufacturing processes and equipment to gradually improve product quality. Until 1958, after mastering the two pre-process manufacturing processes of MnS inhibitor and slab high-temperature heating, the patented technology for manufacturing oriented silicon steel was basically perfect, and the magnetic properties of the product were greatly improved and stable. Started to produce 0.30mm thick products in 1959, and 0.27mm products in 1963. In the early 1940s, Armco Steel Company began to produce cold-rolled non-oriented silicon steel sheets. From 1963 to 1967, the United Kingdom, Japan and other countries stopped the production of hot-rolled silicon steel sheets one after another. Hot-rolled silicon steel sheets are gradually replaced by cold-rolled non-oriented electrical steel and cold-rolled oriented silicon steel sheets.
Etapa de desarrollo de acero al silicio orientado a alta inducción magnética (1961 ~ 1994)
En 1961, sobre la base de la introducción de las patentes de Armco, Nippon Steel produjo por primera vez acero al silicio orientado a alta inducción magnética de prueba con inhibidor integral de AlN + MnS. La producción de prueba comenzó en 1964 y se llamó Hi-B, pero sus propiedades magnéticas no eran estables. Después de 15 años de mejora continua, el proceso de fabricación de acero Hi-B se ha perfeccionado día a día y el grado Z8H se produjo oficialmente en 1968. A partir de 1979, Nippon Steel y Kawasaki han adoptado tecnologías para aumentar el contenido de silicio, reducir el grosor de las tiras de acero y refinar los dominios magnéticos. Se han producido sucesivamente nuevos grados de acero al silicio orientado por inducción magnética de 0,30, 0,27, 0,23 y 0,18 mm de alto.
Classification
Category |
Silicon content,,% |
Nominal thickness ,mm | ||
Hot rolled silicon steel sheet (No orientation) |
Hot rolled low silicon steel (hot rolled motor steel) | 1.0~2.5 | 0.50 | |
Hot rolled high silicon steel (hot rolled transformer steel) | 3.0~4.5 | 0.35 with 0.50 | ||
Cold rolled electrical steel sheet |
Non-oriented electrical steel (Cold rolled motor steel) |
Low carbon electrical steel | ≤0.5 | 0.50 with 0.65 |
Silicon steel | >0.5~3.2 | 0.35 with 0.50 | ||
Oriented silicon steel (Cold rolled transformer steel) |
Ordinary oriented silicon steel | 2.9~3.3 |
0.20,0.23,0.27 0.30 with 0.35 |
|
High magnetic induction oriented silicon steel | 2.9~3.3 |
In addition to the above-mentioned categories of electrical steel, there are also some special-purpose electrical steel plates: Such as 0.15 and 0.20mm thick 3%Si cold-rolled non-oriented silicon steel strips and 0.025, 0.05 and 0.1mm thick 3%Si cold-rolled oriented silicon steel strips, used as medium and high frequency motors and transformers, and pulse transformers; 0.7mm thick 3%Si high-strength cold-rolled non-oriented silicon steel sheet for relays and power switches;
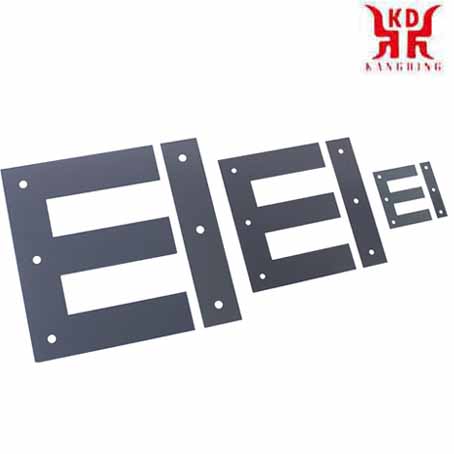
Performance requirements of iron core
Generally, motors, transformers and other electrical components are required to have high efficiency, low power consumption, small size and light weight. Electrical steel sheets usually take core loss and magnetic induction as the product's guaranteed magnetic value. The requirements for the performance of electrical steel plates are as follows:Low core loss (PT)
Iron core loss refers to the ineffective electric energy consumed when the iron core is magnetized under an alternating magnetic field of ≥50Hz, referred to as iron loss, also known as alternating loss, and its unit is W/kg. This kind of ineffective electric energy consumed by various obstacles due to the change of magnetic flux not only loses electric energy through the heating of the iron core, but also causes the temperature rise of the motor and the transformer. The iron loss (PT) of electrical steel includes three parts: hysteresis loss, eddy current loss (Pe) and abnormal loss (Pa). The electrical steel plate has low iron loss, which not only saves a lot of electric energy, but also prolongs the operation time of the motor and transformer, and simplifies the cooling device. Since the power loss caused by the iron loss of electrical steel plates accounts for 2.5% to 4.5% of the annual electricity generation in various countries, the production of electrical steel plates in various countries always tries every means to reduce the iron loss. And take the iron loss as the most important index to assess the magnetic properties of the product, and use the iron loss value of the product as the basis for dividing the product grades.
Magnetic induction intensity (B) is high
The magnetic induction intensity is the number of magnetic lines of force passing through a unit cross-sectional area of the iron core, also known as the magnetic flux density, which represents the magnetization capacity of the material, and the unit is T. The magnetic induction intensity of electrical steel plate is high, the excitation current of the iron core (also called no-load current) is reduced, and the copper loss and iron loss are reduced, which can save electric energy. When the power of the motor and the transformer is unchanged, the magnetic induction intensity is high, the design Bm can be increased, and the cross-sectional area of the iron core can be reduced. This reduces the volume and weight of the iron core, and saves electrical steel plates, wires, insulating materials and structural materials, which can reduce the total loss and manufacturing costs of motors and transformers. And it is conducive to the manufacture, installation and transportation of large transformers and large motors.The design Bm of oriented silicon steel is as high as 1.7~1.80T, which is close to the value of B8, so B8 is used as the guaranteed value of magnetic induction. The motor design Bm is about 1.5T, which is close to the B50 value of cold-rolled non-oriented electrical steel. Therefore, cold-rolled non-oriented silicon steel uses B50 as the guaranteed value of magnetic induction. The magnetic induction of hot-rolled silicon steel is lower, and B25 is usually used as a guaranteed value.
Requirements for magnetic anisotropy
The motor works in the running state, and the iron core is composed of a stator and a rotor laminated with a toothed circular punching sheet. Electrical steel sheets are required to be magnetically isotropic, so they are made of non-oriented cold-rolled electrical steel or hot-rolled silicon steel. Generally, it is required that the difference in longitudinal and longitudinal iron loss is less than 8%, and the difference in magnetic induction is less than 10%.The transformer works in a static state. The cores of large and medium-sized transformers are laminated with strips. Some distribution transformers, current and voltage transformers, and pulse transformers are made of wound iron cores. This can ensure the cutting and magnetization along the rolling direction of the electrical steel sheet, so they are all made of cold-rolled oriented silicon steel.
Good stamping properties
When users use electrical steel plates, the stamping workload is very large, so electrical steel plates are required to have good punching properties, which is particularly important for micro and small motors. Good stamping properties can increase the life of the die and the scissors, ensure the accuracy of the stamping plate size and reduce the burrs of the stamping plate.The main factors affecting the film development are:
1) Die or scissors material. For example, the punching flake property of cemented carbide die is more than doubled than that of tool steel die.
2) The distance between the punch and the die. The appropriate spacing is generally 5% to 6% of the thickness of the steel plate.
3) Type of lubricating oil for stamping sheet.
4) The shape of the stamping sheet.
5) The type and quality of the insulating film on the surface of the steel plate.
6) The hardness of the steel plate, etc. The latter two factors are related to the quality of electrical steel plates.
The surface of the steel plate is smooth, flat and uniform in thickness
The electrical steel sheet surface is required to be smooth, flat and uniform in thickness, mainly to improve the lamination coefficient of the iron core. The high lamination coefficient can increase the effective use of the iron core space, reduce the air gap, and reduce the excitation current. A 1% reduction in the lamination factor of electrical steel plates is equivalent to a 2% increase in iron loss and a 1% reduction in magnetic induction.
Good insulating film performance
In order to prevent short circuits between the core laminations and increase the eddy current loss. The surface of the cold-rolled electrical steel sheet is coated with a thin layer of inorganic salt or a semi-organic insulating film of inorganic salt + organic salt. The following requirements are imposed on the insulating film:1) Good heat resistance. It will not be damaged during stress relief annealing at 750~800℃.
2) The insulating film is thin and uniform.
3) High resistance between layers.
4) Good adhesion.
5) Good film development.
6) Good corrosion resistance and rust resistance.
7) Good weldability. Different uses have different requirements for insulating films.
Magnetic aging phenomenon is small
The phenomenon that the magnetic properties of ferromagnetic materials change over time is called magnetic aging. This phenomenon is mainly caused by impurity elements such as carbon and nitrogen in the material. When the carbon and nitrogen content of the electrical steel sheet is less than 0.0035%, the magnetic aging is significantly reduced.