Efficient processing of aluminum engine cylinder bore rough boring, finish boring
Since the cast iron cylinder liner is pre-cast in the blank. The rough and fine boring of cylinder bore is concentrated in the same process with some hole series processing, which makes it the bottleneck of the processing of all aluminum engine cylinder block production line. To this end, the use of new cutting theory to rationally optimize the tool not only reduces production costs, but also achieves efficient processing with low power consumption.
The engine (see Figure 1) is made of all-aluminum, which has the advantages of light weight, good heat dissipation and low energy consumption. In the processing, the main oil passage casting molding, the breaking link, etc., a number of new processes are adopted; The production line adopts a highly flexible design concept, and the machining equipment is mainly based on the machining center.
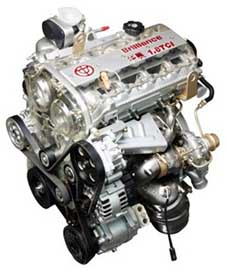
Figure 1 Brilliance 1.8T series turbocharged engine
The 1.8T cylinder production line is a fully flexible production line, and all processing equipment except the honing machine is a machining center (see Figure 2). The engine block (see Figure 3) is made of all-aluminum, and the cast iron cylinder liner is pre-cast in the blank. The rough hole and partial hole machining are concentrated in the same process. Since aluminum alloy is an easy-to-process material, it is easy to achieve high-efficiency processing, and cast iron is a general material with general processing properties, and the workability of the two materials varies greatly. Therefore, the rough machining of the cylinder bore becomes the processing bottleneck of the cylinder production line, which restricts the production capacity of the cylinder production line.
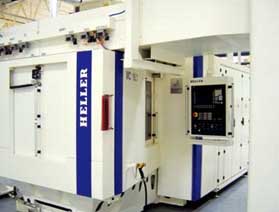
Figure 2 Machining center on the cylinder production line
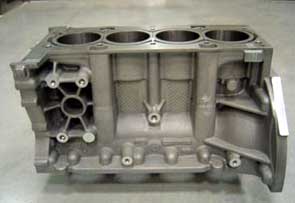
Figure 3 The engine block is made of aluminum
In-depth analysis of the specific conditions of the rough machining of the cylinder bore, in order to obtain a better machining plan and improve the roughing efficiency of the cylinder bore.
The actual machining situation of the rough cylinder bore is: The machining uses a three-blade file (see Figure 4), 75° lead angle, 0° front angle, and the blade is made of CBN material.
Specific cutting parameters: Cutting speed = 400m / min, feed per tooth = 0.18mm, depth of cut = 2.5mm; processing time 42.5s.
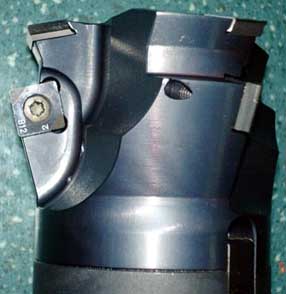
Figure 4 The traditional tool used for the rough hole of the cylinder bore - three-blade file
Several different processing schemes were designed for trial cutting. After analyzing the test results, it is believed that there are two main reasons for restricting the efficiency of cylinder bore machining:
1, boring vibration
The cutting vibration generated when the cylinder bore is rough increases as the cutting speed increases, which limits the increase in cutting speed. Moreover, the cutting vibration causes the blade to be easily damaged, and the tool change is frequent, resulting in a decrease in the starting rate of the device.
2, the spindle load is too high
The 1.8T series engine is an all-aluminum engine, and the machining is mainly aluminum processing. In order to save energy and reduce equipment capacity, the production line does not use a high-power machining center. Therefore, the machine is operated at full load while machining the cast iron cylinder bore. Due to machine power limitations, material removal rates cannot be increased by increasing the feed rate or increasing the number of cutting inserts.
To reduce cutting force, eliminate cutting vibration and improve machining efficiency. We worked with a tool manufacturer to design a new cylinder hole roughing boring tool (see Figure 5). Compared with traditional boring tools, the new boring tool has the following advantages:
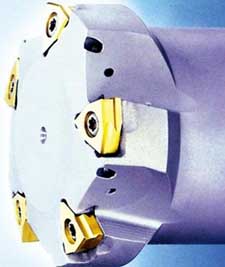
Figure 5 New roughing boring tool for machining cylinder bore
The engine (see Figure 1) is made of all-aluminum, which has the advantages of light weight, good heat dissipation and low energy consumption. In the processing, the main oil passage casting molding, the breaking link, etc., a number of new processes are adopted; The production line adopts a highly flexible design concept, and the machining equipment is mainly based on the machining center.
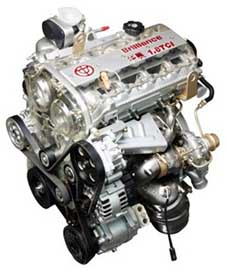
Figure 1 Brilliance 1.8T series turbocharged engine
The 1.8T cylinder production line is a fully flexible production line, and all processing equipment except the honing machine is a machining center (see Figure 2). The engine block (see Figure 3) is made of all-aluminum, and the cast iron cylinder liner is pre-cast in the blank. The rough hole and partial hole machining are concentrated in the same process. Since aluminum alloy is an easy-to-process material, it is easy to achieve high-efficiency processing, and cast iron is a general material with general processing properties, and the workability of the two materials varies greatly. Therefore, the rough machining of the cylinder bore becomes the processing bottleneck of the cylinder production line, which restricts the production capacity of the cylinder production line.
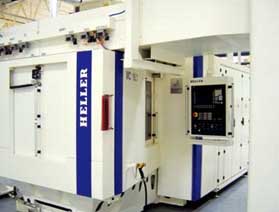
Figure 2 Machining center on the cylinder production line
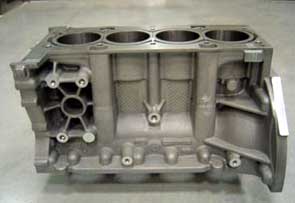
Figure 3 The engine block is made of aluminum
The actual machining situation of the rough cylinder bore is: The machining uses a three-blade file (see Figure 4), 75° lead angle, 0° front angle, and the blade is made of CBN material.
Specific cutting parameters: Cutting speed = 400m / min, feed per tooth = 0.18mm, depth of cut = 2.5mm; processing time 42.5s.
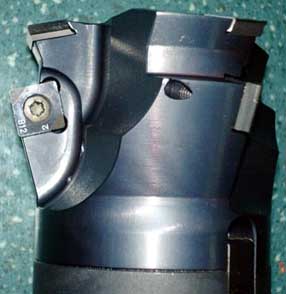
Figure 4 The traditional tool used for the rough hole of the cylinder bore - three-blade file
Several different processing schemes were designed for trial cutting. After analyzing the test results, it is believed that there are two main reasons for restricting the efficiency of cylinder bore machining:
1, boring vibration
The cutting vibration generated when the cylinder bore is rough increases as the cutting speed increases, which limits the increase in cutting speed. Moreover, the cutting vibration causes the blade to be easily damaged, and the tool change is frequent, resulting in a decrease in the starting rate of the device.
2, the spindle load is too high
The 1.8T series engine is an all-aluminum engine, and the machining is mainly aluminum processing. In order to save energy and reduce equipment capacity, the production line does not use a high-power machining center. Therefore, the machine is operated at full load while machining the cast iron cylinder bore. Due to machine power limitations, material removal rates cannot be increased by increasing the feed rate or increasing the number of cutting inserts.
To reduce cutting force, eliminate cutting vibration and improve machining efficiency. We worked with a tool manufacturer to design a new cylinder hole roughing boring tool (see Figure 5). Compared with traditional boring tools, the new boring tool has the following advantages:
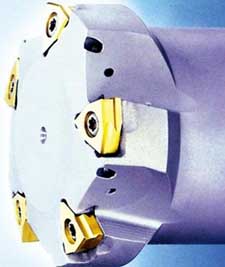
Figure 5 New roughing boring tool for machining cylinder bore
First, the cutting angle
1, positive rake cutting
It is generally considered that tools that process brittle materials such as cast iron should use a negative rake angle to increase tool strength and prevent tool chipping from being damaged. However, among the various geometric parameters of the tool, the rake angle has the greatest influence on the cutting force. The other the conditions are the same, the larger the rake angle of the tool, the smaller the cutting force.
With the improvement of machine tool stability and the emergence of various new tool materials, it has become possible to process brittle materials with large rake angle tools, so the new file uses a positive 10° rake angle. Compared to conventional boring tools with a 0° rake angle or a negative rake angle, the rake angle of the positive rake angle produces less cutting force. The cutting force can be effectively reduced without reducing the cutting parameters, which not only makes the cutting lighter, but also effectively reduces the occurrence of cutting vibration.
1, positive rake cutting
It is generally considered that tools that process brittle materials such as cast iron should use a negative rake angle to increase tool strength and prevent tool chipping from being damaged. However, among the various geometric parameters of the tool, the rake angle has the greatest influence on the cutting force. The other the conditions are the same, the larger the rake angle of the tool, the smaller the cutting force.
With the improvement of machine tool stability and the emergence of various new tool materials, it has become possible to process brittle materials with large rake angle tools, so the new file uses a positive 10° rake angle. Compared to conventional boring tools with a 0° rake angle or a negative rake angle, the rake angle of the positive rake angle produces less cutting force. The cutting force can be effectively reduced without reducing the cutting parameters, which not only makes the cutting lighter, but also effectively reduces the occurrence of cutting vibration.
2, 90 ° lead angle
Radial cutting component is the main cause of cutting vibration, and the larger the radial component, the more likely it is to cause vibration. The new boring tool uses a 90° lead angle and does not produce a radial cutting component on the main cutting edge. Compared with tools with small angle lead angles, the radial cutting component is greatly reduced, which makes the cutting process more stable.
two, Blade clamping method
Using a super-hardened blade such as CBN or cermet in the ordinary clamping method, it is impossible to make a positive rake angle on the blade, and making a positive rake angle on the tool increases the difficulty in installing and adjusting the blade.
Compared to conventional clamping blades, vertical blades can easily produce blades with large rake angles, and the blades can withstand greater cutting forces and improve tool reliability.
The rake face of the vertical insert does not come into contact with other parts or parts of the tool. The design of the chip flute is limited and the optimization is easier.
Compared with the ordinary clamping type of the blade, in most cases, the vertical blade has better chip breaking effect, more reasonable chip space, smoother chip removal, and easier to obtain a stable processing process. Thus, the new boring tool blade mounted by vertical clamping manner.
III. Blade material and structure
Ceramic tools are a new type of material tool in modern metal cutting. It is characterized by high hardness, high strength, high red hardness, high wear resistance, excellent chemical stability and low friction coefficient. In recent years, with the use of various additives and the application of fine particles, the fracture toughness and impact resistance of ceramic inserts have been greatly improved. Ceramic types that can be used for roughing under impact loads have emerged. The boring process is continuous cutting, and no impact is generated during the cutting process, so a ceramic blade can also be used for rough machining. Compared to CBN tools, ceramic tools have a lower coefficient of friction and produce less cutting forces under the same conditions. Therefore, the new boring tool does not use a CBN insert, and a ceramic insert that is more conducive to stable cutting is selected.
In order to make the ceramic blade have sufficient strength. After several comparison tests, it was determined that the blade adopts a W-shaped blade with a blade angle of 80°, and the tool nose radius is 0.8 mm, and the cutting edge and the tool tip are passivated. The passivated blade eliminates microscopic defects in the cutting edge, which not only effectively extends the tool life, but also enhances the strength of the cutting edge and improves the stability of the cutting process.
According to the characteristics of the new boring tool, different processing parameters were used to carry out the comparative experiment, and finally the processing parameters were determined as follows:
Cutting speed = 500m/min, Feed per tooth = 0.12 mm; The depth of cut is uncontrollable and unadjusted. As the new boring tool increases the number of cutting edges and the cutting speed, the processing time is reduced to 30.5 s and the machining efficiency is increased by 39%. Due to the anti-vibration measures adopted by the new tool in various aspects, the stability of the machining process is improved, and the abnormal damage of the blade is basically eliminated, thereby reducing the number of tool changes and increasing the starting rate of the device. Based on the above two factors, the production efficiency of the OP20 process in which the cylinder bore is rough is increased by about 6%.
Through the analysis of the use effect of the new boring tool, the good performance of the new tool material is fully utilized. Proper optimization of the tool with the new cutting theory not only reduces production costs, but also enables efficient machining with low power consumption.
Radial cutting component is the main cause of cutting vibration, and the larger the radial component, the more likely it is to cause vibration. The new boring tool uses a 90° lead angle and does not produce a radial cutting component on the main cutting edge. Compared with tools with small angle lead angles, the radial cutting component is greatly reduced, which makes the cutting process more stable.
two, Blade clamping method
Using a super-hardened blade such as CBN or cermet in the ordinary clamping method, it is impossible to make a positive rake angle on the blade, and making a positive rake angle on the tool increases the difficulty in installing and adjusting the blade.
Compared to conventional clamping blades, vertical blades can easily produce blades with large rake angles, and the blades can withstand greater cutting forces and improve tool reliability.
The rake face of the vertical insert does not come into contact with other parts or parts of the tool. The design of the chip flute is limited and the optimization is easier.
Compared with the ordinary clamping type of the blade, in most cases, the vertical blade has better chip breaking effect, more reasonable chip space, smoother chip removal, and easier to obtain a stable processing process. Thus, the new boring tool blade mounted by vertical clamping manner.
III. Blade material and structure
Ceramic tools are a new type of material tool in modern metal cutting. It is characterized by high hardness, high strength, high red hardness, high wear resistance, excellent chemical stability and low friction coefficient. In recent years, with the use of various additives and the application of fine particles, the fracture toughness and impact resistance of ceramic inserts have been greatly improved. Ceramic types that can be used for roughing under impact loads have emerged. The boring process is continuous cutting, and no impact is generated during the cutting process, so a ceramic blade can also be used for rough machining. Compared to CBN tools, ceramic tools have a lower coefficient of friction and produce less cutting forces under the same conditions. Therefore, the new boring tool does not use a CBN insert, and a ceramic insert that is more conducive to stable cutting is selected.
In order to make the ceramic blade have sufficient strength. After several comparison tests, it was determined that the blade adopts a W-shaped blade with a blade angle of 80°, and the tool nose radius is 0.8 mm, and the cutting edge and the tool tip are passivated. The passivated blade eliminates microscopic defects in the cutting edge, which not only effectively extends the tool life, but also enhances the strength of the cutting edge and improves the stability of the cutting process.
According to the characteristics of the new boring tool, different processing parameters were used to carry out the comparative experiment, and finally the processing parameters were determined as follows:
Cutting speed = 500m/min, Feed per tooth = 0.12 mm; The depth of cut is uncontrollable and unadjusted. As the new boring tool increases the number of cutting edges and the cutting speed, the processing time is reduced to 30.5 s and the machining efficiency is increased by 39%. Due to the anti-vibration measures adopted by the new tool in various aspects, the stability of the machining process is improved, and the abnormal damage of the blade is basically eliminated, thereby reducing the number of tool changes and increasing the starting rate of the device. Based on the above two factors, the production efficiency of the OP20 process in which the cylinder bore is rough is increased by about 6%.
Through the analysis of the use effect of the new boring tool, the good performance of the new tool material is fully utilized. Proper optimization of the tool with the new cutting theory not only reduces production costs, but also enables efficient machining with low power consumption.