Drill Bit and Drilling Technology Research
The history of human understanding and use of drill bits can be traced back to prehistoric times. The stone drill used by the ancients to "fire for wood" can be regarded as the most primitive drill. The twist drill (commonly known as the drill bit) widely used in modern industrial processing is a complex workpiece machining tool with a complex shape, which was born more than 100 years ago. Today, hundreds of millions of drill bits are consumed every year in the world. According to statistics, in the US automobile manufacturing industry, the proportion of drilling processes in mechanical processing accounts for about 50%; In the aircraft industry, the drilling process accounts for a higher proportion. Despite the widespread use of drill bits, drilling is well known as one of the most complex machining methods. Because of this, people have been working on the improvement of the drill bit and the research of the drilling process. Based on the available English literature, this paper reviews the technical issues of two-groove twist drills and the history, current status and development trends of drilling research.
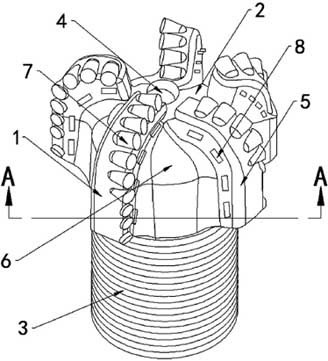
1. Main areas of research and technical issues
In recent decades, research on drill bits and drilling has focused on the following five aspects in addition to improvements in drill bit making materials:
①, drill bit mathematical model and geometric design research:
The mathematical models including spiral grooves, flank face, main blade and transverse blade are established. Transverse truncation and optimization of the parameters of the drill tip structure, calculation and control of the cutting angle (distribution), Static and dynamic analysis of the bit structure, study of the relationship between the geometry of the drill tip and the cutting and chip removal performance.
②, research on the manufacturing method of the drill bit:
It includes the establishment and optimization of the relationship between the geometric parameters of the drill bit and the sharpening parameters of the flank. Evaluation of manufacturing precision and sharpening quality of drill bits and measurement and control of manufacturing errors, The design and calculation of the cutting shape of the spiral groove machining tool, the development of the drill processing equipment, especially the CNC grinding machine and processing software.
③, Drilling process and drilling quality research:
Includes analysis of various factors affecting the drilling process and the analysis, modeling and monitoring of various physical phenomena (such as drilling forces, measurement of cutting edge stress and temperature distribution, modeling and forecasting); Research on bit wear, damage mechanism and bit life; The deformation and deflection of drill bit, slippage during drilling and the swing of drill point are studied. Drilling processes (such as vibration drilling, high speed drilling, deep hole drilling, stability of drilling processes, etc.); Drilling quality (pore position accuracy, straightness, surface roughness, cylindricity, diameter, orifice burrs, etc.).
④, Drilling mechanism and research on various high performance drill bits:
(such as group drills, gun drills, dry cutting drills, micro-holes, deep-hole drills, long drill bits, indexable drill bits, drills for synthetic material processing, woodworking drills, multi-slot drill bits, etc.)
⑤, The drilling process model verification and the automation of the drill bit performance evaluation process, the cutting conditions and the establishment of the knowledge base of the drill bit shape selection. At present, the most dynamic research areas are mathematical models of drill bits, geometric design and manufacturing methods (equipment), drilling process modeling and drilling quality research.
2. Research on mathematical model and geometric design of drill bit
2.1 Mathematical model of the drill bit
Establishing a mathematical model of the drill bit is the basis for geometric design, manufacturing, cutting performance analysis and modeling of the drilling process. The first mathematical model of the drill bit was proposed by Galloway D F in 1957. He derived the parametric equation of the rake face of the straight edge drill bit, and gave the definition, calculation formula and measurement method of the front edge, the back angle and the heel angle of the main edge. The viewpoint of "the flank of the drill bit is used as a part of the grinding cone formed by the interaction of the drill bit with the grinding wheel during the sharpening process" is proposed.
In the early 1970s, Fujii S et al. conducted further research on the model proposed by Galloway D F. It is proposed to use the cutting plane method to analyze the three-dimensional surface flank into a two-dimensional plane curve, and develop a computer aided design program for twist drill.
In 1972, Armarego E J A and Rotenbery A discovered: The flank face sharpening method has 4 independent sharpening parameters, and the general given drill tip geometry parameters are only 3, so the shape and sharpening parameters of the flank face of the drill tip cannot be uniquely determined. To this end, they proposed using the flank clearance angle as a supplementary geometric parameter to obtain the only solution to the sharpening parameters.
In 1979, Tsai W D and Wu S M proved: The flank faces of tapered drills, Racon drills, auger drills and Bickford drill bits can all be represented by quadrics and a comprehensive mathematical model representing the geometry of the drill bit is proposed, which can be used to control the sharpening process. In 1983, Radhakrishnan L et al. proposed a mathematical model of the flank of a cross drill bit.
They divide the flank into a first flank and a second flank: For the first flank, based on the Tsai model, an improved cone model was established; A planar model is created for the second flank. Fugelso M A proposes a mathematical model of the cylindrical tip. In 1985, Fuh K H et al. established a mathematical model of the flank face of a drill with a quadric surface to design it into an ellipsoid, a hyperboloid, a cone, a cylinder, or any combination thereof.
2.2 Structural optimization of the drill bit
Due to the poor cutting performance of the widely used tapered twist drills, people have been working on improving their structure (parameters) and sharpening methods. More than 200 different drill bit shapes have been proposed to improve the cutting performance.
Among them, Shi H M et al. proposed a method to control the distribution of the front edge of the main edge by changing the direction of the main edge. In 1990, a curved-blade twist drill was developed that maximized the rake angle of each point on the main edge of the drill.
In 1987, Lee S J proposed a method to optimize the design of the drill bit under the condition of considering the deviation of the drill bit to eliminate the swinging phenomenon of the drill tip during the drilling process.
In 1995, Selvamhe S V and Sujatha C used the finite element method to optimize the bit geometry when studying the deformation of the twist drill.
The optimized structural parameters (bit diameter 25mm) obtained to minimize the deformation of the drill bit are: The helix angle is 39.776°, the chisel edge angle Ψ = 54° to 80°, and the front angle is 120°.
In 1997, Chen W C proposed a special truncated thick core twist drill with sufficient torsional stiffness and reasonable distribution of the main and chisel rake angles.
In 2005, Paul A et al. ensured the processability of the drill bit. A new drill tip model based on sharpening parameters was proposed, which was used to optimize the taper drill tip, the Racon drill tip and the helicoid drill tip to minimize the cutting force.
2.3 Calculation of spiral groove truncation and machining tool truncation
In 1975, Dibner L G proposed a method to simplify the calculation of the grinding of the spiral grooved grinding wheel, improve the accuracy of the groove machining and completely eliminate the influence of the diameter change of the grinding wheel.
In 1990, Ehmann K F proposed a method for cutting the helical groove machining tool based on differential geometry and kinematics.
1998-2003, Kang D C and Armarego E J A studied the "positive problems" and "anti-problems" of spiral groove machining ("tool truncation by groove truncation" and "groove truncation by tool truncation"). A computer-aided geometric analysis method for the design and manufacture of helical groove spiral groove drilling is proposed.
2.4 Research on Group Drills and Micro Drills
In 1982, Shen J et al established the first mathematical model of group drilling. Using this model, people can drill group drill several times.
In 1984, Chen L and Wu S M studied nine typical group drills and improved the mathematical model of group drills, which provided the possibility of computer-aided design of group drills.
In 1985, Hsiao C and Wu S M proposed a specific method for assisting the optimization design of group drills by computer.
In 1987, Fuh K H proposed a method for designing and analyzing group drills using a comprehensive quadric surface model and a finite element method. Liang E J proposed a group-drilling CAD/CAM integrated system based on knowledge base technology.
In 1991, Liu T I designed and optimized a group drill for machining machine shaft oiling holes using a two-stage strategy.
In 1994, Huang H T et al. derived the formulas of the working method back angle and the pre-angle of the group cutting edge, and proposed an accurate geometric model of the group drill considering the transition between the inner edge and the circular edge.
In 2001, Wang G C et al. applied a tilted solid block method to establish a new mathematical model for group drilling. The problem that the geometry of the chisel edge existing in the existing model is uncertain is solved, and the machinability of the designed group drill is guaranteed.
3. Research on drilling force modeling
3.1 History of drilling force modeling
In the past few decades, many methods for predicting drilling forces have been reported, most of which are used for standard twist drills. Due to the lack of advanced computers and measuring equipment, early research focused on building simple empirical torque and axial force models. The model parameters are the geometric parameters of the drill bit (such as the diameter of the drill bit) and the amount of cutting. The modeling method is to use a large number of cutting experiments to fit the empirical formula of the drilling force by statistical methods.
3.2 Development of drilling force modeling
In addition to the basic geometry of the drill bit, many factors in the drilling process can affect the drilling force. In 1996, Chandrasekharan V et al. considered the manufacture of the drill bit and the sharpening error such as the contour of the two main edges, the radius error, the axial deflection and so on. A complete 3D cutting force model of the tapered drill bit was established, which was subsequently extended to predict the cutting force of any shape drill bit (eg group drill). Sriram R established a model for predicting the radial force of drilling while considering the influence of drill sharpening and installation error on the drilling force.
In 2001, Gong Y P and Ehmann K established a comprehensive consideration of bit geometry, sharpening and installation errors. And the axial force, torque and radial force models of the micro-hole drill bit affected by the deviation of the bit from the dynamic cutting thickness and cutting area of the main and chisel edges.
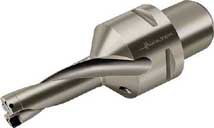
4. Research trends
(1) Drilling process modeling has become a research hotspot
Various factors affecting the drilling process:
Including bit geometry, manufacturing and installation errors, physical properties (static and dynamic), cutting conditions, ambient temperature, workpiece size and materials will be gradually incorporated into the scope of modeling studies. Drilling forces, drilling temperatures, bit wear and life associated with various drill types, cutting conditions and drilling processes, Chip deformation and discharge, drilling quality, drilling efficiency and drilling costs will all be the object of modeling the drilling process. The modeling method will be more diversified, the accuracy of model prediction will be further improved, and the drilling model will be used not only for simulation and forecasting. It will be used more to guide the optimization and monitoring of the bit design, manufacturing and drilling processes.
(2) The geometric design and manufacturing method of the drill bit will remain the focus of research.
New types of drills suitable for processing a wide range of materials and processing conditions will continue to emerge, and research into micro-drills for micro-machinery and printed circuit board manufacturing will go deeper. Research on the manufacturing method of the drill bit will be developed in the direction of integrated manufacturing systems. The problem of automatic sharpening of drill bits, especially group drills, will be addressed, with special emphasis on integration, automation and intelligence in design and manufacturing.
(3) Research on drilling mechanism will gradually receive attention
The research on drill bit and drilling process is more and more in need of the support of drilling mechanism research. The research on drilling mechanism is the bottleneck restricting the research of drill bit and drilling technology; Drilling is one of the most complex cutting processes, and basic research on cutting principles is bound to shift from relatively simple turning machining research to more complex drilling machining research.
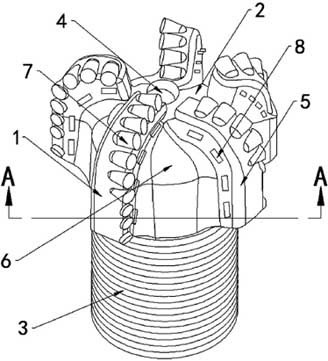
1. Main areas of research and technical issues
In recent decades, research on drill bits and drilling has focused on the following five aspects in addition to improvements in drill bit making materials:
①, drill bit mathematical model and geometric design research:
The mathematical models including spiral grooves, flank face, main blade and transverse blade are established. Transverse truncation and optimization of the parameters of the drill tip structure, calculation and control of the cutting angle (distribution), Static and dynamic analysis of the bit structure, study of the relationship between the geometry of the drill tip and the cutting and chip removal performance.
②, research on the manufacturing method of the drill bit:
It includes the establishment and optimization of the relationship between the geometric parameters of the drill bit and the sharpening parameters of the flank. Evaluation of manufacturing precision and sharpening quality of drill bits and measurement and control of manufacturing errors, The design and calculation of the cutting shape of the spiral groove machining tool, the development of the drill processing equipment, especially the CNC grinding machine and processing software.
③, Drilling process and drilling quality research:
Includes analysis of various factors affecting the drilling process and the analysis, modeling and monitoring of various physical phenomena (such as drilling forces, measurement of cutting edge stress and temperature distribution, modeling and forecasting); Research on bit wear, damage mechanism and bit life; The deformation and deflection of drill bit, slippage during drilling and the swing of drill point are studied. Drilling processes (such as vibration drilling, high speed drilling, deep hole drilling, stability of drilling processes, etc.); Drilling quality (pore position accuracy, straightness, surface roughness, cylindricity, diameter, orifice burrs, etc.).
④, Drilling mechanism and research on various high performance drill bits:
(such as group drills, gun drills, dry cutting drills, micro-holes, deep-hole drills, long drill bits, indexable drill bits, drills for synthetic material processing, woodworking drills, multi-slot drill bits, etc.)
⑤, The drilling process model verification and the automation of the drill bit performance evaluation process, the cutting conditions and the establishment of the knowledge base of the drill bit shape selection. At present, the most dynamic research areas are mathematical models of drill bits, geometric design and manufacturing methods (equipment), drilling process modeling and drilling quality research.
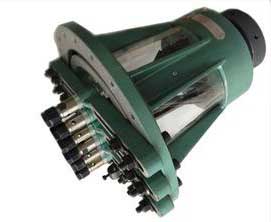
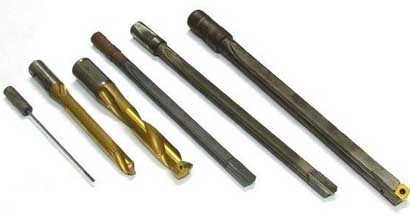
2. Research on mathematical model and geometric design of drill bit
2.1 Mathematical model of the drill bit
Establishing a mathematical model of the drill bit is the basis for geometric design, manufacturing, cutting performance analysis and modeling of the drilling process. The first mathematical model of the drill bit was proposed by Galloway D F in 1957. He derived the parametric equation of the rake face of the straight edge drill bit, and gave the definition, calculation formula and measurement method of the front edge, the back angle and the heel angle of the main edge. The viewpoint of "the flank of the drill bit is used as a part of the grinding cone formed by the interaction of the drill bit with the grinding wheel during the sharpening process" is proposed.
In the early 1970s, Fujii S et al. conducted further research on the model proposed by Galloway D F. It is proposed to use the cutting plane method to analyze the three-dimensional surface flank into a two-dimensional plane curve, and develop a computer aided design program for twist drill.
In 1972, Armarego E J A and Rotenbery A discovered: The flank face sharpening method has 4 independent sharpening parameters, and the general given drill tip geometry parameters are only 3, so the shape and sharpening parameters of the flank face of the drill tip cannot be uniquely determined. To this end, they proposed using the flank clearance angle as a supplementary geometric parameter to obtain the only solution to the sharpening parameters.
In 1979, Tsai W D and Wu S M proved: The flank faces of tapered drills, Racon drills, auger drills and Bickford drill bits can all be represented by quadrics and a comprehensive mathematical model representing the geometry of the drill bit is proposed, which can be used to control the sharpening process. In 1983, Radhakrishnan L et al. proposed a mathematical model of the flank of a cross drill bit.
They divide the flank into a first flank and a second flank: For the first flank, based on the Tsai model, an improved cone model was established; A planar model is created for the second flank. Fugelso M A proposes a mathematical model of the cylindrical tip. In 1985, Fuh K H et al. established a mathematical model of the flank face of a drill with a quadric surface to design it into an ellipsoid, a hyperboloid, a cone, a cylinder, or any combination thereof.
2.2 Structural optimization of the drill bit
Due to the poor cutting performance of the widely used tapered twist drills, people have been working on improving their structure (parameters) and sharpening methods. More than 200 different drill bit shapes have been proposed to improve the cutting performance.
Among them, Shi H M et al. proposed a method to control the distribution of the front edge of the main edge by changing the direction of the main edge. In 1990, a curved-blade twist drill was developed that maximized the rake angle of each point on the main edge of the drill.
In 1987, Lee S J proposed a method to optimize the design of the drill bit under the condition of considering the deviation of the drill bit to eliminate the swinging phenomenon of the drill tip during the drilling process.
In 1995, Selvamhe S V and Sujatha C used the finite element method to optimize the bit geometry when studying the deformation of the twist drill.
The optimized structural parameters (bit diameter 25mm) obtained to minimize the deformation of the drill bit are: The helix angle is 39.776°, the chisel edge angle Ψ = 54° to 80°, and the front angle is 120°.
In 1997, Chen W C proposed a special truncated thick core twist drill with sufficient torsional stiffness and reasonable distribution of the main and chisel rake angles.
In 2005, Paul A et al. ensured the processability of the drill bit. A new drill tip model based on sharpening parameters was proposed, which was used to optimize the taper drill tip, the Racon drill tip and the helicoid drill tip to minimize the cutting force.
2.3 Calculation of spiral groove truncation and machining tool truncation
In 1975, Dibner L G proposed a method to simplify the calculation of the grinding of the spiral grooved grinding wheel, improve the accuracy of the groove machining and completely eliminate the influence of the diameter change of the grinding wheel.
In 1990, Ehmann K F proposed a method for cutting the helical groove machining tool based on differential geometry and kinematics.
1998-2003, Kang D C and Armarego E J A studied the "positive problems" and "anti-problems" of spiral groove machining ("tool truncation by groove truncation" and "groove truncation by tool truncation"). A computer-aided geometric analysis method for the design and manufacture of helical groove spiral groove drilling is proposed.
2.4 Research on Group Drills and Micro Drills
In 1982, Shen J et al established the first mathematical model of group drilling. Using this model, people can drill group drill several times.
In 1984, Chen L and Wu S M studied nine typical group drills and improved the mathematical model of group drills, which provided the possibility of computer-aided design of group drills.
In 1985, Hsiao C and Wu S M proposed a specific method for assisting the optimization design of group drills by computer.
In 1987, Fuh K H proposed a method for designing and analyzing group drills using a comprehensive quadric surface model and a finite element method. Liang E J proposed a group-drilling CAD/CAM integrated system based on knowledge base technology.
In 1991, Liu T I designed and optimized a group drill for machining machine shaft oiling holes using a two-stage strategy.
In 1994, Huang H T et al. derived the formulas of the working method back angle and the pre-angle of the group cutting edge, and proposed an accurate geometric model of the group drill considering the transition between the inner edge and the circular edge.
In 2001, Wang G C et al. applied a tilted solid block method to establish a new mathematical model for group drilling. The problem that the geometry of the chisel edge existing in the existing model is uncertain is solved, and the machinability of the designed group drill is guaranteed.
3. Research on drilling force modeling
3.1 History of drilling force modeling
In the past few decades, many methods for predicting drilling forces have been reported, most of which are used for standard twist drills. Due to the lack of advanced computers and measuring equipment, early research focused on building simple empirical torque and axial force models. The model parameters are the geometric parameters of the drill bit (such as the diameter of the drill bit) and the amount of cutting. The modeling method is to use a large number of cutting experiments to fit the empirical formula of the drilling force by statistical methods.
3.2 Development of drilling force modeling
In addition to the basic geometry of the drill bit, many factors in the drilling process can affect the drilling force. In 1996, Chandrasekharan V et al. considered the manufacture of the drill bit and the sharpening error such as the contour of the two main edges, the radius error, the axial deflection and so on. A complete 3D cutting force model of the tapered drill bit was established, which was subsequently extended to predict the cutting force of any shape drill bit (eg group drill). Sriram R established a model for predicting the radial force of drilling while considering the influence of drill sharpening and installation error on the drilling force.
In 2001, Gong Y P and Ehmann K established a comprehensive consideration of bit geometry, sharpening and installation errors. And the axial force, torque and radial force models of the micro-hole drill bit affected by the deviation of the bit from the dynamic cutting thickness and cutting area of the main and chisel edges.
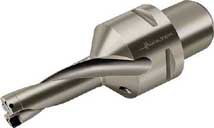
4. Research trends
(1) Drilling process modeling has become a research hotspot
Various factors affecting the drilling process:
Including bit geometry, manufacturing and installation errors, physical properties (static and dynamic), cutting conditions, ambient temperature, workpiece size and materials will be gradually incorporated into the scope of modeling studies. Drilling forces, drilling temperatures, bit wear and life associated with various drill types, cutting conditions and drilling processes, Chip deformation and discharge, drilling quality, drilling efficiency and drilling costs will all be the object of modeling the drilling process. The modeling method will be more diversified, the accuracy of model prediction will be further improved, and the drilling model will be used not only for simulation and forecasting. It will be used more to guide the optimization and monitoring of the bit design, manufacturing and drilling processes.
(2) The geometric design and manufacturing method of the drill bit will remain the focus of research.
New types of drills suitable for processing a wide range of materials and processing conditions will continue to emerge, and research into micro-drills for micro-machinery and printed circuit board manufacturing will go deeper. Research on the manufacturing method of the drill bit will be developed in the direction of integrated manufacturing systems. The problem of automatic sharpening of drill bits, especially group drills, will be addressed, with special emphasis on integration, automation and intelligence in design and manufacturing.
(3) Research on drilling mechanism will gradually receive attention
The research on drill bit and drilling process is more and more in need of the support of drilling mechanism research. The research on drilling mechanism is the bottleneck restricting the research of drill bit and drilling technology; Drilling is one of the most complex cutting processes, and basic research on cutting principles is bound to shift from relatively simple turning machining research to more complex drilling machining research.