Application of Threaded Fastener Assembly Grading Technology
Assembly grading
At present, domestic and foreign automobile manufacturers classify the assembly of threaded fasteners. The domestic automotive industry standard Q/T 518 divides the tightening accuracy of fasteners into three grades, which are different; Volkswagen's assembly below the yield point is divided into 4 levels; DEUTZ divides the assembly into 3 levels according to the fluctuation range of the clamping force after tightening; For the torque method assembly, Mercedes-Benz is divided into 3 levels, and Toyota is divided into 5 levels. FAW Group divides the torque method assembly into 4 levels.
When the bolt assembly level is increased, the fluctuation range of the tightening torque is reduced, the axial preload force is increased, and the reliability of the threaded connection is improved; When the clamping force requirement is constant, the size of the bolt can be reduced, the weight can be reduced, and the coupling structure can be made compact.
4.1 Torque-turn angle method
A passenger car sub-frame and body connection position. Bolt size M14 × 1.5 × 85,10.9 stage, the friction coefficient μ = 0.18-0.14, using the method of assembling the torque, the tightening torque (110 ± 20) Nm, minimum axial preload force 34kN.
When assembling by the torque-angle method, the bolt of M12 can be used, the tightening process is 70Nm+180°, and the yield is tightened to the yield. The minimum axial pre-tightening force is 44kN, which meets the requirements for use. The comparison results of the screw parameters under different assembly methods are shown in Table 1.
Table 1 Comparison of bolt parameters under different assembly methods
After tightening by the torque-angle method, the usage rate of the bolt is improved, the stability of the assembly quality is also improved, and the bolt specifications (M14→M12) can be reduced accordingly, the weight reduction (36g) can be realized, and the cost can be reduced accordingly. .
4.2 Assembly grading
Take a joint structure of a commercial vehicle as an example. Currently used is a 10.9 grade, friction coefficient μ = 0.18-0.14, M14 × 1.5 × 70 hex flange bolts. When using FN4 assembly, the axial preload is (31-77) kN, and the pre-tightening force is large. When the assembly level is increased to FN1, the axial preload is (73-87) kN, the dispersion is significantly reduced, and the minimum axial preload is 73kN, which is 2.35 times that of FN4 assembly (Fig. 4a). It can greatly improve bolt utilization and greatly improve the stability of assembly quality. The comparison results of bolt parameters under different assembly fans are shown in Table 2.
Figure 4 Tightening torque and axial preload force at different assembly levels
Table 2 Comparison of bolt parameters under different assembly levels
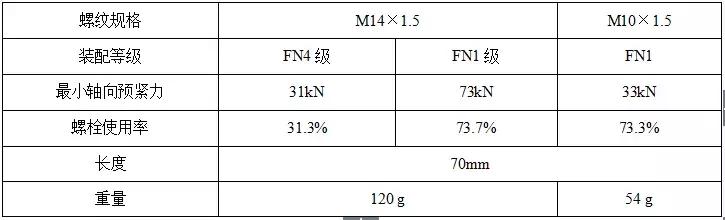
If the minimum axial pre-tightening force (31kN) of FN4 assembly meets the requirements of the connection structure, the bolt size can be reduced to M10 and the minimum axial pre-tightening force 33 kN by FN1 assembly, as shown in Fig. 4b.
In this case, due to the reduced bolt size, a single bolt can achieve a weight reduction of 66g. The coupling structure is equipped with a total of 10 bolts, and the bicycle can achieve a weight reduction of 660g, and the cost can be reduced.
in conclusion
This paper introduces the common assembly methods for automotive threaded fasteners and introduces the technique of assembly grading. In the actual tightening, the requirements of the actual joint structure, the most suitable method and process can be selected.
Torque-turn angle method and assembly grading technology are adopted to improve assembly reliability and increase bolt utilization rate. Under the condition that the pre-tightening force requirements are the same, the bolt specifications are reduced, and the joint structure is compact, and the weight reduction and cost reduction are realized, which is of great significance in the light weight of the automobile.
At present, domestic and foreign automobile manufacturers classify the assembly of threaded fasteners. The domestic automotive industry standard Q/T 518 divides the tightening accuracy of fasteners into three grades, which are different; Volkswagen's assembly below the yield point is divided into 4 levels; DEUTZ divides the assembly into 3 levels according to the fluctuation range of the clamping force after tightening; For the torque method assembly, Mercedes-Benz is divided into 3 levels, and Toyota is divided into 5 levels. FAW Group divides the torque method assembly into 4 levels.
When the bolt assembly level is increased, the fluctuation range of the tightening torque is reduced, the axial preload force is increased, and the reliability of the threaded connection is improved; When the clamping force requirement is constant, the size of the bolt can be reduced, the weight can be reduced, and the coupling structure can be made compact.
Application examples in car lightweighting
4.1 Torque-turn angle method
A passenger car sub-frame and body connection position. Bolt size M14 × 1.5 × 85,10.9 stage, the friction coefficient μ = 0.18-0.14, using the method of assembling the torque, the tightening torque (110 ± 20) Nm, minimum axial preload force 34kN.
When assembling by the torque-angle method, the bolt of M12 can be used, the tightening process is 70Nm+180°, and the yield is tightened to the yield. The minimum axial pre-tightening force is 44kN, which meets the requirements for use. The comparison results of the screw parameters under different assembly methods are shown in Table 1.
Table 1 Comparison of bolt parameters under different assembly methods
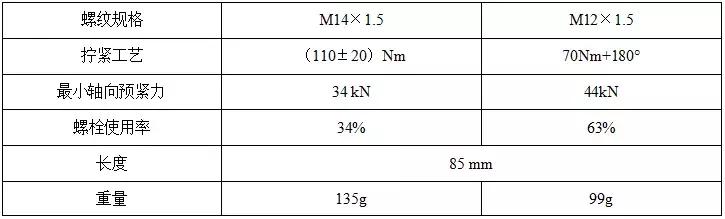
After tightening by the torque-angle method, the usage rate of the bolt is improved, the stability of the assembly quality is also improved, and the bolt specifications (M14→M12) can be reduced accordingly, the weight reduction (36g) can be realized, and the cost can be reduced accordingly. .
4.2 Assembly grading
Take a joint structure of a commercial vehicle as an example. Currently used is a 10.9 grade, friction coefficient μ = 0.18-0.14, M14 × 1.5 × 70 hex flange bolts. When using FN4 assembly, the axial preload is (31-77) kN, and the pre-tightening force is large. When the assembly level is increased to FN1, the axial preload is (73-87) kN, the dispersion is significantly reduced, and the minimum axial preload is 73kN, which is 2.35 times that of FN4 assembly (Fig. 4a). It can greatly improve bolt utilization and greatly improve the stability of assembly quality. The comparison results of bolt parameters under different assembly fans are shown in Table 2.
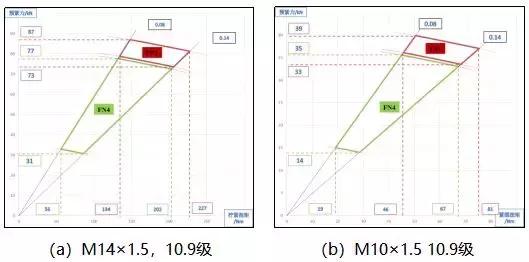
Figure 4 Tightening torque and axial preload force at different assembly levels
Table 2 Comparison of bolt parameters under different assembly levels
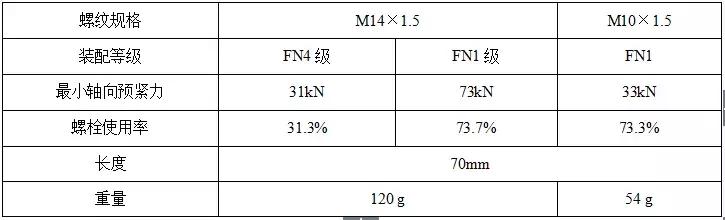
If the minimum axial pre-tightening force (31kN) of FN4 assembly meets the requirements of the connection structure, the bolt size can be reduced to M10 and the minimum axial pre-tightening force 33 kN by FN1 assembly, as shown in Fig. 4b.
In this case, due to the reduced bolt size, a single bolt can achieve a weight reduction of 66g. The coupling structure is equipped with a total of 10 bolts, and the bicycle can achieve a weight reduction of 660g, and the cost can be reduced.
in conclusion
This paper introduces the common assembly methods for automotive threaded fasteners and introduces the technique of assembly grading. In the actual tightening, the requirements of the actual joint structure, the most suitable method and process can be selected.
Torque-turn angle method and assembly grading technology are adopted to improve assembly reliability and increase bolt utilization rate. Under the condition that the pre-tightening force requirements are the same, the bolt specifications are reduced, and the joint structure is compact, and the weight reduction and cost reduction are realized, which is of great significance in the light weight of the automobile.