Aluminum Processing
Method of processing aluminum?
In aluminum processing, aluminum ingots are processed into materials by plastic processing methods. The main methods are rolling, extrusion, drawing, and forging. Aluminum processing began to be produced industrially in the early 20th century. Before the 1930s, copper processing equipment was basically used. The products were mainly used in aircraft manufacturing. After the 1960s, aluminum production grew rapidly, with an annual increase of about 4 to 8%. The products are widely used in aviation, construction, transportation, electrical, chemical, packaging and daily necessities industries. The output is second only to steel, ranking second in metal materials. In the mid-1950s, China established a large-scale aluminum processing plant and formed a production system. The products have been serialized and there are seven alloy systems. Can produce plate, strip, foil, pipe, bar, profiles, wire and forgings (free forgings, die forgings) eight types of products.
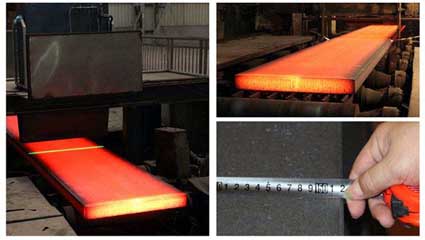
Development
From the macroscopic perspective of economic growth, the meso-perspective of the industry evolution, and the micro-behavior of corporate development, we all find that the aluminum industry is now becoming an inevitable trend from the smelting of primary electrolytic aluminum to deep processing. Aluminium processing products are generally priced at “aluminum price + processing fee”. When there is a rapid increase in total downstream demand and structure, companies with technological advantages, channel advantages, cost advantages, and locational advantages are required. The processing fee rate can not only be guaranteed, but also there is potential for improvement. If the factor of capacity expansion is superimposed, the growth of performance will be rapid and significant.
In recent years, the aluminum industry in China has grown rapidly and has fully developed into a highly competitive industry. As of the end of 2017, there were 1,824 aluminum profile enterprises above China's size. After a period of rapid development and fierce market competition, the basic pattern has taken shape. At present, there are many manufacturing enterprises in the aluminum foil industry in China and the industry concentration is low. No one company has a significant market share, and no one company can have a decisive influence on the development of the entire industry. In 2017, the output of aluminum foil in the country was about 12 million tons, and there were more than 1,250 companies engaged in aluminum foil production with an average output of about 0.8 million tons. The average size is small, there are many small businesses, and there is excessive competition in low-value-added products.
With the rapid development of China's metal doors and windows, building curtain wall, transportation industry, chemical industry, power equipment industry, national defense industry and other industries, Demand for aluminum profiles will continue to increase. At the same time, new products, new processes, and new uses of aluminum profiles will continue to emerge. In order to promote technological progress and the sustained and healthy development of the industry, the aluminum profile industry will still show a good development trend from 2018 to 2020.
With the rapid growth of the aluminum profile industry in China, the sales revenue of the aluminum profile industry will also increase year by year. According to statistics, from 2018 to 2020, the compound annual growth rate of sales revenue of the aluminum industry in China was 15.20%. According to the current economic situation at home and abroad, combined with sales data of China's aluminum industry in 2015-2017 and China's economic growth data, a rough estimation of the compound annual growth rate of sales revenue of China's aluminum industry from 2018 to 2020 is 8%. In 2017, China Aluminum The profile industry sales revenue will reach 1.5498 trillion yuan. With the rapid development of the aluminum foil downstream industry, its demand for aluminum foil will continue to increase. By 2018, aluminum foil consumption will reach 2.8 million tons. It will reach 3.1 million tons in 2019, The compound annual growth rate of 2018-2020 reached 7%.
Introduction
Plastic working of aluminum and aluminum alloys, the product should ensure stable, consistent dimensional accuracy, mechanical properties and good surface quality desired. Also pay attention to prevent mechanical damage and corrosion, control the grain size and organizational structure, these quality requirements are mainly guaranteed by the production process and equipment. Aluminum and its alloys generally have good plasticity and are easily plastically processed. The phase composition of hard aluminum is relatively complex, and there are brittle structures such as low-melting phases and intermetallic compounds.
Its plastic processing has some features:
Aluminum products processing plants, such as homogenization treatment to eliminate billet cooling when the internal stress and intragranular segregation; Billet surface by milling to remove surface segregation of the low melting phase produced. Some aluminum alloys to improve the corrosion resistance and workability have to be clad. Aluminum alloys are sensitive to overheating, and the heating temperature must be strictly controlled.
Melting and casting
Melting
Billet to provide plasticity processing.
Smelting furnaces use gas reverberatory or fuel reverberatory furnaces with a capacity of 20 to 40 tons or more; Electric resistance reverberatory furnace, capacity is generally about 10 tons. In order to shorten the charging time, increase the melting efficiency, and reduce the absorption of gas and entrainment into the oxide film, a rotary top-loading round furnace has been used in the industry. Best applied when melting the alloy composition rapid analysis instrumental analysis and timely adjustment. In order to ensure the purity of the melt, prevent the pollution of harmful gases and control the chemical composition, in addition to shorten the melting time as much as possible, It should be covered with powdered flux mainly consisting of potassium chloride and sodium chloride, The general dosage is 0.4 to 2% of the weight of the furnace. The smelting temperature is usually controlled at 700 to 750°C.
The molten metal needs to be refined and filtered to remove harmful hydrogen and non-metallic inclusions in the metal to improve the purity of the metal. Refining usually uses solid refining agents or gas refining agents. Solid refining agents are generally based on chloride salts and also use hexachloroethane instead of chlorine salt refining agents. Early use of highly active chlorine gas as a gas refining agent, although the purification effect is good, but the environmental pollution is serious, Therefore, nitrogen-chlorine mixed gas, inert gas and three-gas (N2, Cl2, CO) refining agent have been developed, and the effect is better. To ensure the effect of refining, refining gas of oxygen and moisture content should generally be less than 0.03% (by volume) and 0.3 g / m 3, respectively. Dynamic vacuum degassing also has better degassing and sodium removal effects.
Filtration is a filter made of molten metal through neutral or active materials, which removes suspended solids in the melt. Commonly used glass screens, microporous ceramic tubes and plates, and alumina pellets are used as filter beds for filtration, as well as flux refining and flux layer filtration.
casting
Casting generally uses vertical or horizontal water-cooled semi-continuous casting method. To improve the vertical cast billet structure and surface quality, electromagnetic crystallization tanks, dwarf crystallization tanks and hot top casting methods have also been developed. The water-cooled semi-continuous casting method introduces the liquid metal into a water-cooled crystallizer through a gutter, and the liquid metal is cooled to form a solidified shell. The crystallization is carried out by the traction of the casting machine base, or by the uniform drop of its own weight, to form a billet. The process parameters vary greatly depending on the composition of the alloy and the size of the billet. Generally, the casting speed and cooling rate should be increased as much as possible to reduce the height of the crystallization tank. The casting temperature is usually 50 to 110°C higher than the liquidus of the alloy. In addition, aluminum strip continuous casting and rolling processes have also been developed.
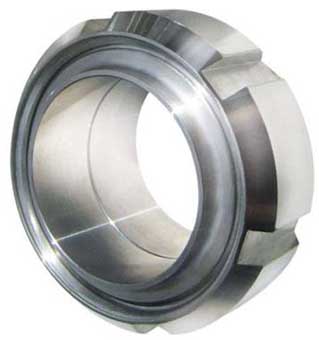
Plate and Strip Production Using flat roll rolling, the basic processes are hot rolling, cold rolling, heat treatment and finishing. Hard alloys such as LY12 and LC4 with complex chemical compositions should be homogenized before hot rolling. The treatment temperature is generally lower than the eutectic temperature of the low melting point phase of the alloy from 10 to 15 degrees, holding 12 ~ 24 hours. The aluminum cladding of the hard aluminum alloy is that the aluminum covering plate is placed on both sides of the milled ingot and welded by hot rolling. The thickness of the clad aluminum layer is generally 4% of the thickness of the plate. Hot rolling is generally performed above the recrystallization temperature. Hot rolling can be carried out on a single stand reversible rolling mill or on multiple stands. In order to improve the production rate and production efficiency, large ingots are rolled, and the weight of the ingots is 10-15 tons. The annual production capacity of 100,000 tons below the factory, generally with four-roll reversible hot rolling and the use of hot roll process, hot strip thickness of about 6 to 8 mm. A factory with a output of more than 100 thousand tons. After the four roll reversible hot rolling mill is open, single stand or two rack, three rack, five rack continuous rolling, hot finish rolling, the thickness of the tape can reach 2.5 ~ 3.5 mm. After hot rolled strips are rolled, they are used as cold rolled blanks. In order to ensure the best plasticity of the metal, hot rolling should be carried out in a single-phase state. The hot rolling starting temperature of LY11, LY12 and other alloys is 400-455°C. The first few pass deformation rates are generally within 10% and gradually increase thereafter. The pass deformation rate of pure aluminum and soft aluminum alloy can reach 50%, hard aluminum alloy is about 40%. Hot rolling total deformation rate of up to 90%.
Cold rolling is usually carried out at room temperature, and by means of cold rolling relatively thin sheets and strips with precise dimensions and smooth surfaces can be obtained, and work-hardened sheets and strips with specific mechanical properties can be obtained. Cold rolling mainly adopts the belt-type production process, and a four-high reversible rolling mill or a four-high irreversible rolling mill is used for cold rolling. Currently, an irreversible rolling mill is being developed for cold rolling. The rolling mill is equipped with a hydraulic pressure control system, a hydraulic bending roll, an automatic thickness control system or an automatic thickness control system for roll gaps, and a plate shape controller. Various parameters are controlled, recorded, and stored by the microcomputer to obtain precise, flat plate strips, such as 0.18 mm strip tolerances of ±5 microns. Small factories, but also block-type method, the production of the sheet. After annealing, the cold deformation rate of aluminum can reach more than 90%. The heterogeneous hard aluminum alloys are hardened by cold work and require intermediate annealing. The cold deformation after the intermediate annealing is 60 to 70%. Hot rolling emulsion lubrication, and cold-rolling has evolved from emulsion to full-oil lubrication. A multi-stage cooling system with separate nozzles is used to reduce the friction between the aluminum plate and the roll, cool the roll, control the roll type, wash off the aluminum powder and other impurities to obtain a good surface quality and plate shape.
After cold rolling and heat treatment, the coil is often fined on roller straightener or in stretch bending continuous straightener. The plate after leveling and quenching should be carried out in the incubation period. It is usually completed within 30~40 minutes after quenching. The total deformation of the quenched plate in the straight press should not exceed 2%. In 1955, successfully tested aluminum strips, continuous casting and rolling can produce thin and aluminum foil blanks. In the early 1970s, China started using this method to produce thin plates.
Foil production
Aluminum foil can be divided into industrial aluminum foil and packaging aluminum foil. Industrial aluminum foil has a relatively pure chemical composition and a thickness of 0.005 to 0.2 mm. It is mainly used as a capacitor, thermal insulation material, and moisture proof material in the electrical and electronic industries. Packaging aluminum foil thickness is generally 0.007 ~ 0.1 mm, there are flat foil, printed foil and crepe paper aluminum foil and other products, mainly used for food, tea, cigarettes and other packaging materials. The aluminum foil is produced in a strip production method with a minimum thickness of 0.0025 mm and a width of 1800 mm. Aluminum foil rolling, no roll gap rolling, the roll is always in an elastically flattened state. During rolling, the thickness of the foil is controlled by adjusting the rolling force, rolling speed and controlling the tension. In rough rolling, the rolling force is used to control the thickness of the foil; In finish rolling, the thickness of the foil decreases as the rolling speed increases; The greater the tension, the smaller the thickness; In order to prevent breakage, the tension is usually selected from 0.2 to 0.4 of the conditional yield strength σ0.2 of the foil. For low speed rolling, “thick oil” or “thin oil” is often added to the lubricating oil to adjust the rolling thickness of the aluminum foil. Lubricants and roll conditions have a very important influence on the foil quality. The aluminum foil blanks are from cold-rolled aluminum coils and are generally pre-annealed at 340-480°C and have a thickness of 0.4-0.7 mm. The duct deformation rate during rolling is about 50%, and the total deformation rate can reach 95% or more. he foil with finished product thickness less than 0.01 ~ 0.02 mm should be coiled and double folded.
Wire production
The main use of stretching process production. Products are rivets, electrodes and wires. Blank by extrusion, rolling or continuous casting and rolling production method. Extrusion method to produce billet, greater flexibility, better product performance. The rolling method and the continuous casting and rolling method are suitable for the production of billets of a single alloy type and have high production efficiency.
Forging production
Mainly used in aircraft and machine manufacturing. Forgings are divided into free forgings and die forgings. Its stock by casting and extrusion billets. The largest die forging hydraulic press is 70,000 tons, and the maximum size of the forging projected area is 4.5 meters 2. The critical deformation rate of aluminum alloy is about 5-15%. In order to avoid the formation of coarse crystals, the deformation rate of die forging should generally be greater than 15%. In order to reduce uneven deformation, multi-directional free forging is often used.
Other production
Production of pipes, rods and profiles The usual process is:
First, hot extrusion is used to make the billet, which is then finished by rolling (or stretching), finishing and heat treatment. It can also be directly made into finished products by hot extrusion. It has been developed from short spindles to long spindle extrusions. According to the extrusion force of the extruder with a uniform diameter ingot, Extruded various profiles and tubes by split-flow modular and tongue-shaped molds. The length of the product can reach more than 60 meters. After being straightened by stretching, it can be cut to the required length. The largest extruder for aluminum production is 20,000 tons. Can be extruded into a ribbed tube with a diameter of 800 mm. Building profiles are extruded products developed in the 1960s and account for more than 35% of the total extruded products, of which 80% are used as door and window frames. Almost all building profiles use aluminum-magnesium silicon alloys (LD30 and LD31). This product is anodized and colored, the surface of the formation of a variety of color oxide film, has a good corrosion resistance, made of beautiful doors and windows durable, good sealing. In addition to hot extrusion, cold extrusion, isothermal extrusion, residual extrusion and hydrostatic extrusion have also been developed (see the oxidation of aluminum).
Extrusion of aluminum and aluminum alloys uses forward extrusion and reverse extrusion. The appropriate extrusion speed should be selected according to different alloys. In order to obtain aluminum alloy extrusion products with good organization and performance, the extrusion coefficient (λ) of profiles and bars is greater than 8 to 12 when the finished products are extruded at one time, and the λ of the blanks used for forging is greater than 5. Extrusion die has a great influence on the quality of extruded products. Extruded bars and profiles are often used as flat dies, while pipes are often used as tapered dies. Extruding complex shaped hollow profiles and pipes is widely used for split combination die and tongue die. Some use liquid nitrogen cooling extrusion die to extend die life and ensure product accuracy. One die can squeeze 30 tons of aluminum. Some extruded products of aluminum alloys are prone to "coarse-grained rings", that is, after the products have been heat-treated, there is a layer of coarse grained areas around them. Extrusion at high temperatures can reduce this phenomenon. Some aluminum alloy extrusion products that can be strengthened by heat treatment undergo solid solution aging treatment, the strength increases and the plasticity decreases.
Pipe stretching uses a number of rapid and cylindrical stretching, swimming core tube coil stretching machine diameter up to 630 ~ 2900 mm, stretching tube diameter up to 40 ~ 50 mm. Pulling tube tensile force is 16 to 18 tons, tensile speed is 24 meters/minute, pass rate is generally 25 to 40%, and this kind of technology produces tube length up to 6000 meters.
Related process
The heat treatment to ensure the final performance of the product is called finished heat treatment, including finished annealing, solution treatment, quenching, natural aging and artificial aging treatment; In addition, graded aging and deformation heat treatment processes have also been developed. Aging treatment not only improves the mechanical properties of the product, but also improves the stress corrosion resistance and fracture toughness of the product. The transfer time from solid solution heating to quenching should generally be controlled within 30 seconds. Quenching the cooling rate, it is necessary to ensure that the supersaturated solid solution, but also not to produce excessive quenching stress and bending deformation of the product. The coils and plates are annealed in a powerfully ventilated box furnace, pit furnace, vertical plate continuous annealing furnace or air-cushion continuous annealing furnace. The new furnace adopts protective atmosphere. Quenching is generally heated in a salt bath and the new process is quenched with an air-cushion continuous quench furnace.
1.2 According to the force and deformation of the workpiece in the deformation process classification
According to the stress and deformation mode (stress and strain state) of the workpiece during the deformation process, Aluminum and aluminum alloy processing can be divided into rolling, extrusion, drawing, forging, spinning, forming processing (such as cold stamping, cold change, deep drawing, etc.) and deep processing.
Rolling
Rolling is a plastic deformation process in which the billet is pulled into the rotating roll by friction, and the cross-section is reduced by the pressure exerted by the roll, the shape is changed, and the thickness becomes thinner and the length increases. Rolling can be divided into vertical rolling, cross rolling and oblique rolling depending on the direction of rotation of the rolls. In longitudinal rolling, the working roller rotates in the opposite direction. The longitudinal axis of the rolling piece is perpendicular to the axis of the roller. It is the most commonly used method for aluminum alloy plate, belt, and foil flat roller rolling. When cross-rolling, the same direction of rotation of the work roll, with the longitudinal axis of the rolling roll axis parallel to each other, rarely used in the aluminum alloy plate and strip rolling; In oblique rolling, the working rolls rotate in the same direction. The longitudinal axis of the rolling stock is at a certain angle to the axis of the roll. In the production of aluminum alloy pipe and some special-shaped products commonly used double roll or multi-roller oblique rolling. According to different roll systems, aluminum alloy rolling can be divided into two-roll (one pair) rolling, multi-roll rolling and special rolling (such as planetary rolling, V-rolling, etc.) rolling: According to different roll shapes, aluminum alloy rolling can be divided into flat roll rolling and hole roll rolling. According to different product varieties, aluminum alloy rolling can be divided into plate, belt, foil rolling, bar, flat strip and special profile rolling, pipe and hollow profile rolling.
Extrusion
The extrusion billet is loaded into the extrusion cylinder, pressure is applied to the metal through the extrusion axis, so that a given die orifice shape and size from extruded to produce plastic deformation to obtain a desired extruded product processing method.
According to the extrusion when the metal flow direction is different.
The extrusion can be further divided into forward extrusion, reverse extrusion and combined extrusion.
In the forward extrusion, the direction of movement of the extrusion axis coincides with the direction of flow of the extruded metal.
In reverse extrusion, the direction of movement of the extrusion axis is opposite to that of the extruded metal.
According to the heating temperature of the billet, the extrusion can be divided into hot extrusion and cold extrusion.
Hot extrusion is performed by heating the ingot to a temperature above the recrystallization temperature. Cold extrusion is performed at room temperature.
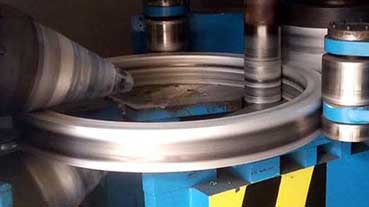
Drawing
Drawing is the drawing machine pulling the aluminum and aluminum alloy blank (billet or tube blank) through the clamps, from the given shape and size of the die L. It is plastically deformed to obtain the desired method of processing tubes, rods, shapes, and wires. According to the different types and shapes of products produced, stretching can be divided into wire stretching, pipe stretching, bar stretching and profile stretching. Pipe stretching can be divided into blank drawing, core drawing and floating core drawing. According to the variety and shape of the products, stretching can be divided into wire stretching, tube drawing, bar drawing and profile stretching. According to the stretching mode, stretching can be divided into single-mode stretching and multi-mode stretching.
Forging
Forging is a forging hammer or press (mechanical or hydraulic), using the hammer head or pressure head to exert pressure on aluminum and aluminum alloy ingot or forged billet to make a plastic deformation of the metal. Aluminum alloy forging has two methods, free forging and die forging. Free forging is to place workpiece on a flat anvil (or anvil) for forging. Die forging is to place the workpiece in a mold of a given size and shape, then apply pressure on the workpiece to forge deformation, and obtain the required die forging.
1.3 Other Plastic Forming Methods for Aluminum
People have also researched and developed a variety of new aluminum processing methods, which are mainly:
(1) Pressure casting forming methods such as low, medium and high pressure forming, extrusion molding, etc.
(2) Semi-solid forming methods such as semi-solid rolling, semi-solid extrusion, semi-solid drawing, and liquid forging.
(3) Continuous forming methods such as continuous casting and continuous extrusion, high speed continuous casting and rolling, and Conform continuous extrusion.
(4) Composite forming methods, such as laminating rolling method, multi-blank extrusion method, etc.
(5) deformation heat treatment method.
Aluminum and aluminum alloy processed materials are the most widely used and the largest in output, with rolled materials (plates, strips, strips, foils) and extruded materials (tubes, rods, wires, wires). According to statistics, the annual output of these two types of materials accounts for 58% and 39% of the total annual output of aluminum in the world (average). The remaining aluminum processing materials, such as forged products, account for only a few percent of the total output of aluminum materials. .
1.4 According to the temperature characteristics of the workpiece in the process of classification
Classification and Characteristics of Aluminum Processing Methods
Many aluminum and aluminum alloy plastic forming methods, It is usually classified according to the temperature characteristics of the workpiece during processing and the stress and deformation modes (stress-strain state) of the workpiece during the deformation process.
According to the temperature characteristics of the workpiece in the process of classification
According to the temperature characteristics of the workpiece in the process of processing, aluminum and aluminum alloy processing can be divided into thermal processing, cold processing and warm processing.
Thermal processing
Thermal processing refers to the plastic forming process of aluminum and aluminum alloy ingots at or above the recrystallization temperature. During hot working, the plasticity of the billet is higher and the deformation resistance is lower, so that a product with a larger amount of deformation can be produced with a smaller capacity equipment. In order to ensure the organization and performance of the product, the heating temperature, deformation temperature and deformation speed, deformation degree, temperature at the end of deformation and cooling rate after deformation should be strictly controlled. The common aluminum alloy hot processing methods include hot extrusion, hot rolling, hot forging, hot forging, liquid forging, semi-solid forming, continuous casting and rolling, continuous casting and continuous rolling, continuous casting and continuous extrusion.
Cold processing
Cold working refers to a plastic forming process that is completed below the temperature at which no recovery or recrystallization occurs.
The essence of cold working is the combination of cold working and intermediate annealing. Cold-worked to the final product with smooth surface, precise dimensions, good organization and performance, and can meet different performance requirements: The most common cold-working methods are cold extrusion, cold forging, cold-rolling of pipes, cold-drawing, cold-rolling with plate and foil, cold-stamping, cold bending, and spinning.
In aluminum processing, aluminum ingots are processed into materials by plastic processing methods. The main methods are rolling, extrusion, drawing, and forging. Aluminum processing began to be produced industrially in the early 20th century. Before the 1930s, copper processing equipment was basically used. The products were mainly used in aircraft manufacturing. After the 1960s, aluminum production grew rapidly, with an annual increase of about 4 to 8%. The products are widely used in aviation, construction, transportation, electrical, chemical, packaging and daily necessities industries. The output is second only to steel, ranking second in metal materials. In the mid-1950s, China established a large-scale aluminum processing plant and formed a production system. The products have been serialized and there are seven alloy systems. Can produce plate, strip, foil, pipe, bar, profiles, wire and forgings (free forgings, die forgings) eight types of products.
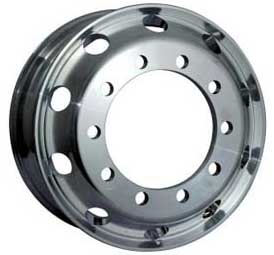
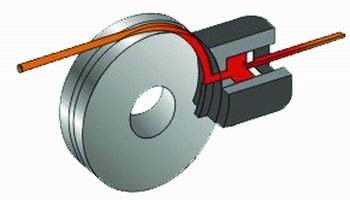
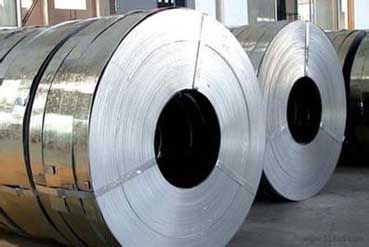
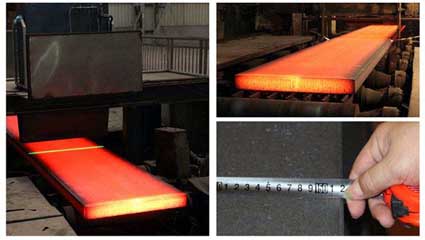
Development
From the macroscopic perspective of economic growth, the meso-perspective of the industry evolution, and the micro-behavior of corporate development, we all find that the aluminum industry is now becoming an inevitable trend from the smelting of primary electrolytic aluminum to deep processing. Aluminium processing products are generally priced at “aluminum price + processing fee”. When there is a rapid increase in total downstream demand and structure, companies with technological advantages, channel advantages, cost advantages, and locational advantages are required. The processing fee rate can not only be guaranteed, but also there is potential for improvement. If the factor of capacity expansion is superimposed, the growth of performance will be rapid and significant.
In recent years, the aluminum industry in China has grown rapidly and has fully developed into a highly competitive industry. As of the end of 2017, there were 1,824 aluminum profile enterprises above China's size. After a period of rapid development and fierce market competition, the basic pattern has taken shape. At present, there are many manufacturing enterprises in the aluminum foil industry in China and the industry concentration is low. No one company has a significant market share, and no one company can have a decisive influence on the development of the entire industry. In 2017, the output of aluminum foil in the country was about 12 million tons, and there were more than 1,250 companies engaged in aluminum foil production with an average output of about 0.8 million tons. The average size is small, there are many small businesses, and there is excessive competition in low-value-added products.
With the rapid development of China's metal doors and windows, building curtain wall, transportation industry, chemical industry, power equipment industry, national defense industry and other industries, Demand for aluminum profiles will continue to increase. At the same time, new products, new processes, and new uses of aluminum profiles will continue to emerge. In order to promote technological progress and the sustained and healthy development of the industry, the aluminum profile industry will still show a good development trend from 2018 to 2020.
With the rapid growth of the aluminum profile industry in China, the sales revenue of the aluminum profile industry will also increase year by year. According to statistics, from 2018 to 2020, the compound annual growth rate of sales revenue of the aluminum industry in China was 15.20%. According to the current economic situation at home and abroad, combined with sales data of China's aluminum industry in 2015-2017 and China's economic growth data, a rough estimation of the compound annual growth rate of sales revenue of China's aluminum industry from 2018 to 2020 is 8%. In 2017, China Aluminum The profile industry sales revenue will reach 1.5498 trillion yuan. With the rapid development of the aluminum foil downstream industry, its demand for aluminum foil will continue to increase. By 2018, aluminum foil consumption will reach 2.8 million tons. It will reach 3.1 million tons in 2019, The compound annual growth rate of 2018-2020 reached 7%.
Introduction
Plastic working of aluminum and aluminum alloys, the product should ensure stable, consistent dimensional accuracy, mechanical properties and good surface quality desired. Also pay attention to prevent mechanical damage and corrosion, control the grain size and organizational structure, these quality requirements are mainly guaranteed by the production process and equipment. Aluminum and its alloys generally have good plasticity and are easily plastically processed. The phase composition of hard aluminum is relatively complex, and there are brittle structures such as low-melting phases and intermetallic compounds.
Its plastic processing has some features:
Aluminum products processing plants, such as homogenization treatment to eliminate billet cooling when the internal stress and intragranular segregation; Billet surface by milling to remove surface segregation of the low melting phase produced. Some aluminum alloys to improve the corrosion resistance and workability have to be clad. Aluminum alloys are sensitive to overheating, and the heating temperature must be strictly controlled.
Melting and casting
Melting
Billet to provide plasticity processing.
Smelting furnaces use gas reverberatory or fuel reverberatory furnaces with a capacity of 20 to 40 tons or more; Electric resistance reverberatory furnace, capacity is generally about 10 tons. In order to shorten the charging time, increase the melting efficiency, and reduce the absorption of gas and entrainment into the oxide film, a rotary top-loading round furnace has been used in the industry. Best applied when melting the alloy composition rapid analysis instrumental analysis and timely adjustment. In order to ensure the purity of the melt, prevent the pollution of harmful gases and control the chemical composition, in addition to shorten the melting time as much as possible, It should be covered with powdered flux mainly consisting of potassium chloride and sodium chloride, The general dosage is 0.4 to 2% of the weight of the furnace. The smelting temperature is usually controlled at 700 to 750°C.
The molten metal needs to be refined and filtered to remove harmful hydrogen and non-metallic inclusions in the metal to improve the purity of the metal. Refining usually uses solid refining agents or gas refining agents. Solid refining agents are generally based on chloride salts and also use hexachloroethane instead of chlorine salt refining agents. Early use of highly active chlorine gas as a gas refining agent, although the purification effect is good, but the environmental pollution is serious, Therefore, nitrogen-chlorine mixed gas, inert gas and three-gas (N2, Cl2, CO) refining agent have been developed, and the effect is better. To ensure the effect of refining, refining gas of oxygen and moisture content should generally be less than 0.03% (by volume) and 0.3 g / m 3, respectively. Dynamic vacuum degassing also has better degassing and sodium removal effects.
Filtration is a filter made of molten metal through neutral or active materials, which removes suspended solids in the melt. Commonly used glass screens, microporous ceramic tubes and plates, and alumina pellets are used as filter beds for filtration, as well as flux refining and flux layer filtration.
casting
Casting generally uses vertical or horizontal water-cooled semi-continuous casting method. To improve the vertical cast billet structure and surface quality, electromagnetic crystallization tanks, dwarf crystallization tanks and hot top casting methods have also been developed. The water-cooled semi-continuous casting method introduces the liquid metal into a water-cooled crystallizer through a gutter, and the liquid metal is cooled to form a solidified shell. The crystallization is carried out by the traction of the casting machine base, or by the uniform drop of its own weight, to form a billet. The process parameters vary greatly depending on the composition of the alloy and the size of the billet. Generally, the casting speed and cooling rate should be increased as much as possible to reduce the height of the crystallization tank. The casting temperature is usually 50 to 110°C higher than the liquidus of the alloy. In addition, aluminum strip continuous casting and rolling processes have also been developed.
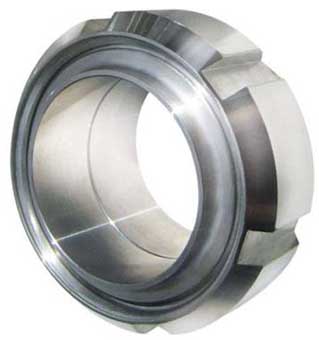
Plate and Strip Production Using flat roll rolling, the basic processes are hot rolling, cold rolling, heat treatment and finishing. Hard alloys such as LY12 and LC4 with complex chemical compositions should be homogenized before hot rolling. The treatment temperature is generally lower than the eutectic temperature of the low melting point phase of the alloy from 10 to 15 degrees, holding 12 ~ 24 hours. The aluminum cladding of the hard aluminum alloy is that the aluminum covering plate is placed on both sides of the milled ingot and welded by hot rolling. The thickness of the clad aluminum layer is generally 4% of the thickness of the plate. Hot rolling is generally performed above the recrystallization temperature. Hot rolling can be carried out on a single stand reversible rolling mill or on multiple stands. In order to improve the production rate and production efficiency, large ingots are rolled, and the weight of the ingots is 10-15 tons. The annual production capacity of 100,000 tons below the factory, generally with four-roll reversible hot rolling and the use of hot roll process, hot strip thickness of about 6 to 8 mm. A factory with a output of more than 100 thousand tons. After the four roll reversible hot rolling mill is open, single stand or two rack, three rack, five rack continuous rolling, hot finish rolling, the thickness of the tape can reach 2.5 ~ 3.5 mm. After hot rolled strips are rolled, they are used as cold rolled blanks. In order to ensure the best plasticity of the metal, hot rolling should be carried out in a single-phase state. The hot rolling starting temperature of LY11, LY12 and other alloys is 400-455°C. The first few pass deformation rates are generally within 10% and gradually increase thereafter. The pass deformation rate of pure aluminum and soft aluminum alloy can reach 50%, hard aluminum alloy is about 40%. Hot rolling total deformation rate of up to 90%.
Cold rolling is usually carried out at room temperature, and by means of cold rolling relatively thin sheets and strips with precise dimensions and smooth surfaces can be obtained, and work-hardened sheets and strips with specific mechanical properties can be obtained. Cold rolling mainly adopts the belt-type production process, and a four-high reversible rolling mill or a four-high irreversible rolling mill is used for cold rolling. Currently, an irreversible rolling mill is being developed for cold rolling. The rolling mill is equipped with a hydraulic pressure control system, a hydraulic bending roll, an automatic thickness control system or an automatic thickness control system for roll gaps, and a plate shape controller. Various parameters are controlled, recorded, and stored by the microcomputer to obtain precise, flat plate strips, such as 0.18 mm strip tolerances of ±5 microns. Small factories, but also block-type method, the production of the sheet. After annealing, the cold deformation rate of aluminum can reach more than 90%. The heterogeneous hard aluminum alloys are hardened by cold work and require intermediate annealing. The cold deformation after the intermediate annealing is 60 to 70%. Hot rolling emulsion lubrication, and cold-rolling has evolved from emulsion to full-oil lubrication. A multi-stage cooling system with separate nozzles is used to reduce the friction between the aluminum plate and the roll, cool the roll, control the roll type, wash off the aluminum powder and other impurities to obtain a good surface quality and plate shape.
After cold rolling and heat treatment, the coil is often fined on roller straightener or in stretch bending continuous straightener. The plate after leveling and quenching should be carried out in the incubation period. It is usually completed within 30~40 minutes after quenching. The total deformation of the quenched plate in the straight press should not exceed 2%. In 1955, successfully tested aluminum strips, continuous casting and rolling can produce thin and aluminum foil blanks. In the early 1970s, China started using this method to produce thin plates.
Foil production
Aluminum foil can be divided into industrial aluminum foil and packaging aluminum foil. Industrial aluminum foil has a relatively pure chemical composition and a thickness of 0.005 to 0.2 mm. It is mainly used as a capacitor, thermal insulation material, and moisture proof material in the electrical and electronic industries. Packaging aluminum foil thickness is generally 0.007 ~ 0.1 mm, there are flat foil, printed foil and crepe paper aluminum foil and other products, mainly used for food, tea, cigarettes and other packaging materials. The aluminum foil is produced in a strip production method with a minimum thickness of 0.0025 mm and a width of 1800 mm. Aluminum foil rolling, no roll gap rolling, the roll is always in an elastically flattened state. During rolling, the thickness of the foil is controlled by adjusting the rolling force, rolling speed and controlling the tension. In rough rolling, the rolling force is used to control the thickness of the foil; In finish rolling, the thickness of the foil decreases as the rolling speed increases; The greater the tension, the smaller the thickness; In order to prevent breakage, the tension is usually selected from 0.2 to 0.4 of the conditional yield strength σ0.2 of the foil. For low speed rolling, “thick oil” or “thin oil” is often added to the lubricating oil to adjust the rolling thickness of the aluminum foil. Lubricants and roll conditions have a very important influence on the foil quality. The aluminum foil blanks are from cold-rolled aluminum coils and are generally pre-annealed at 340-480°C and have a thickness of 0.4-0.7 mm. The duct deformation rate during rolling is about 50%, and the total deformation rate can reach 95% or more. he foil with finished product thickness less than 0.01 ~ 0.02 mm should be coiled and double folded.
Wire production
The main use of stretching process production. Products are rivets, electrodes and wires. Blank by extrusion, rolling or continuous casting and rolling production method. Extrusion method to produce billet, greater flexibility, better product performance. The rolling method and the continuous casting and rolling method are suitable for the production of billets of a single alloy type and have high production efficiency.
Forging production
Mainly used in aircraft and machine manufacturing. Forgings are divided into free forgings and die forgings. Its stock by casting and extrusion billets. The largest die forging hydraulic press is 70,000 tons, and the maximum size of the forging projected area is 4.5 meters 2. The critical deformation rate of aluminum alloy is about 5-15%. In order to avoid the formation of coarse crystals, the deformation rate of die forging should generally be greater than 15%. In order to reduce uneven deformation, multi-directional free forging is often used.
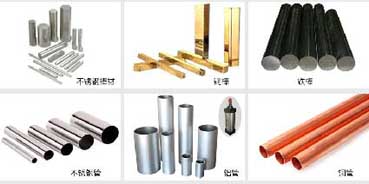
Production of pipes, rods and profiles The usual process is:
First, hot extrusion is used to make the billet, which is then finished by rolling (or stretching), finishing and heat treatment. It can also be directly made into finished products by hot extrusion. It has been developed from short spindles to long spindle extrusions. According to the extrusion force of the extruder with a uniform diameter ingot, Extruded various profiles and tubes by split-flow modular and tongue-shaped molds. The length of the product can reach more than 60 meters. After being straightened by stretching, it can be cut to the required length. The largest extruder for aluminum production is 20,000 tons. Can be extruded into a ribbed tube with a diameter of 800 mm. Building profiles are extruded products developed in the 1960s and account for more than 35% of the total extruded products, of which 80% are used as door and window frames. Almost all building profiles use aluminum-magnesium silicon alloys (LD30 and LD31). This product is anodized and colored, the surface of the formation of a variety of color oxide film, has a good corrosion resistance, made of beautiful doors and windows durable, good sealing. In addition to hot extrusion, cold extrusion, isothermal extrusion, residual extrusion and hydrostatic extrusion have also been developed (see the oxidation of aluminum).
Extrusion of aluminum and aluminum alloys uses forward extrusion and reverse extrusion. The appropriate extrusion speed should be selected according to different alloys. In order to obtain aluminum alloy extrusion products with good organization and performance, the extrusion coefficient (λ) of profiles and bars is greater than 8 to 12 when the finished products are extruded at one time, and the λ of the blanks used for forging is greater than 5. Extrusion die has a great influence on the quality of extruded products. Extruded bars and profiles are often used as flat dies, while pipes are often used as tapered dies. Extruding complex shaped hollow profiles and pipes is widely used for split combination die and tongue die. Some use liquid nitrogen cooling extrusion die to extend die life and ensure product accuracy. One die can squeeze 30 tons of aluminum. Some extruded products of aluminum alloys are prone to "coarse-grained rings", that is, after the products have been heat-treated, there is a layer of coarse grained areas around them. Extrusion at high temperatures can reduce this phenomenon. Some aluminum alloy extrusion products that can be strengthened by heat treatment undergo solid solution aging treatment, the strength increases and the plasticity decreases.
Pipe stretching uses a number of rapid and cylindrical stretching, swimming core tube coil stretching machine diameter up to 630 ~ 2900 mm, stretching tube diameter up to 40 ~ 50 mm. Pulling tube tensile force is 16 to 18 tons, tensile speed is 24 meters/minute, pass rate is generally 25 to 40%, and this kind of technology produces tube length up to 6000 meters.
Related process
The heat treatment to ensure the final performance of the product is called finished heat treatment, including finished annealing, solution treatment, quenching, natural aging and artificial aging treatment; In addition, graded aging and deformation heat treatment processes have also been developed. Aging treatment not only improves the mechanical properties of the product, but also improves the stress corrosion resistance and fracture toughness of the product. The transfer time from solid solution heating to quenching should generally be controlled within 30 seconds. Quenching the cooling rate, it is necessary to ensure that the supersaturated solid solution, but also not to produce excessive quenching stress and bending deformation of the product. The coils and plates are annealed in a powerfully ventilated box furnace, pit furnace, vertical plate continuous annealing furnace or air-cushion continuous annealing furnace. The new furnace adopts protective atmosphere. Quenching is generally heated in a salt bath and the new process is quenched with an air-cushion continuous quench furnace.
1.2 According to the force and deformation of the workpiece in the deformation process classification
According to the stress and deformation mode (stress and strain state) of the workpiece during the deformation process, Aluminum and aluminum alloy processing can be divided into rolling, extrusion, drawing, forging, spinning, forming processing (such as cold stamping, cold change, deep drawing, etc.) and deep processing.
Rolling
Rolling is a plastic deformation process in which the billet is pulled into the rotating roll by friction, and the cross-section is reduced by the pressure exerted by the roll, the shape is changed, and the thickness becomes thinner and the length increases. Rolling can be divided into vertical rolling, cross rolling and oblique rolling depending on the direction of rotation of the rolls. In longitudinal rolling, the working roller rotates in the opposite direction. The longitudinal axis of the rolling piece is perpendicular to the axis of the roller. It is the most commonly used method for aluminum alloy plate, belt, and foil flat roller rolling. When cross-rolling, the same direction of rotation of the work roll, with the longitudinal axis of the rolling roll axis parallel to each other, rarely used in the aluminum alloy plate and strip rolling; In oblique rolling, the working rolls rotate in the same direction. The longitudinal axis of the rolling stock is at a certain angle to the axis of the roll. In the production of aluminum alloy pipe and some special-shaped products commonly used double roll or multi-roller oblique rolling. According to different roll systems, aluminum alloy rolling can be divided into two-roll (one pair) rolling, multi-roll rolling and special rolling (such as planetary rolling, V-rolling, etc.) rolling: According to different roll shapes, aluminum alloy rolling can be divided into flat roll rolling and hole roll rolling. According to different product varieties, aluminum alloy rolling can be divided into plate, belt, foil rolling, bar, flat strip and special profile rolling, pipe and hollow profile rolling.
Extrusion
The extrusion billet is loaded into the extrusion cylinder, pressure is applied to the metal through the extrusion axis, so that a given die orifice shape and size from extruded to produce plastic deformation to obtain a desired extruded product processing method.
According to the extrusion when the metal flow direction is different.
The extrusion can be further divided into forward extrusion, reverse extrusion and combined extrusion.
In the forward extrusion, the direction of movement of the extrusion axis coincides with the direction of flow of the extruded metal.
In reverse extrusion, the direction of movement of the extrusion axis is opposite to that of the extruded metal.
According to the heating temperature of the billet, the extrusion can be divided into hot extrusion and cold extrusion.
Hot extrusion is performed by heating the ingot to a temperature above the recrystallization temperature. Cold extrusion is performed at room temperature.
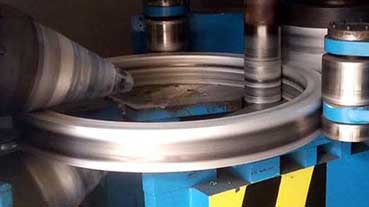
Drawing
Drawing is the drawing machine pulling the aluminum and aluminum alloy blank (billet or tube blank) through the clamps, from the given shape and size of the die L. It is plastically deformed to obtain the desired method of processing tubes, rods, shapes, and wires. According to the different types and shapes of products produced, stretching can be divided into wire stretching, pipe stretching, bar stretching and profile stretching. Pipe stretching can be divided into blank drawing, core drawing and floating core drawing. According to the variety and shape of the products, stretching can be divided into wire stretching, tube drawing, bar drawing and profile stretching. According to the stretching mode, stretching can be divided into single-mode stretching and multi-mode stretching.
Forging
Forging is a forging hammer or press (mechanical or hydraulic), using the hammer head or pressure head to exert pressure on aluminum and aluminum alloy ingot or forged billet to make a plastic deformation of the metal. Aluminum alloy forging has two methods, free forging and die forging. Free forging is to place workpiece on a flat anvil (or anvil) for forging. Die forging is to place the workpiece in a mold of a given size and shape, then apply pressure on the workpiece to forge deformation, and obtain the required die forging.
1.3 Other Plastic Forming Methods for Aluminum
People have also researched and developed a variety of new aluminum processing methods, which are mainly:
(1) Pressure casting forming methods such as low, medium and high pressure forming, extrusion molding, etc.
(2) Semi-solid forming methods such as semi-solid rolling, semi-solid extrusion, semi-solid drawing, and liquid forging.
(3) Continuous forming methods such as continuous casting and continuous extrusion, high speed continuous casting and rolling, and Conform continuous extrusion.
(4) Composite forming methods, such as laminating rolling method, multi-blank extrusion method, etc.
(5) deformation heat treatment method.
Aluminum and aluminum alloy processed materials are the most widely used and the largest in output, with rolled materials (plates, strips, strips, foils) and extruded materials (tubes, rods, wires, wires). According to statistics, the annual output of these two types of materials accounts for 58% and 39% of the total annual output of aluminum in the world (average). The remaining aluminum processing materials, such as forged products, account for only a few percent of the total output of aluminum materials. .
1.4 According to the temperature characteristics of the workpiece in the process of classification
Classification and Characteristics of Aluminum Processing Methods
Many aluminum and aluminum alloy plastic forming methods, It is usually classified according to the temperature characteristics of the workpiece during processing and the stress and deformation modes (stress-strain state) of the workpiece during the deformation process.
According to the temperature characteristics of the workpiece in the process of classification
According to the temperature characteristics of the workpiece in the process of processing, aluminum and aluminum alloy processing can be divided into thermal processing, cold processing and warm processing.
Thermal processing
Thermal processing refers to the plastic forming process of aluminum and aluminum alloy ingots at or above the recrystallization temperature. During hot working, the plasticity of the billet is higher and the deformation resistance is lower, so that a product with a larger amount of deformation can be produced with a smaller capacity equipment. In order to ensure the organization and performance of the product, the heating temperature, deformation temperature and deformation speed, deformation degree, temperature at the end of deformation and cooling rate after deformation should be strictly controlled. The common aluminum alloy hot processing methods include hot extrusion, hot rolling, hot forging, hot forging, liquid forging, semi-solid forming, continuous casting and rolling, continuous casting and continuous rolling, continuous casting and continuous extrusion.
Cold processing
Cold working refers to a plastic forming process that is completed below the temperature at which no recovery or recrystallization occurs.
The essence of cold working is the combination of cold working and intermediate annealing. Cold-worked to the final product with smooth surface, precise dimensions, good organization and performance, and can meet different performance requirements: The most common cold-working methods are cold extrusion, cold forging, cold-rolling of pipes, cold-drawing, cold-rolling with plate and foil, cold-stamping, cold bending, and spinning.
