5-axis high-speed milling of aircraft fuselage parts
The structural features of typical aircraft parts are thin-walled structures with complex shapes. The shape has a large change in the bevel angle, and the shape is mostly a hyperboloid, which requires precise forming. In order to reduce the weight of the aircraft, increase the maneuverability of the aircraft and increase the payload and range, lightweight design is adopted, and new lightweight materials are widely used. In order to improve part strength and work reliability, the overall blank and the overall thin wall structure are mainly used. A large number of aluminum alloys, titanium alloys, high temperature resistant alloys, high strength steels, composite materials, and the like are now used. The thin-walled parts and honeycomb parts with complicated structure are not only complicated in shape, but also have many holes, grooves, ribs, etc., and the process rigidity is poor.
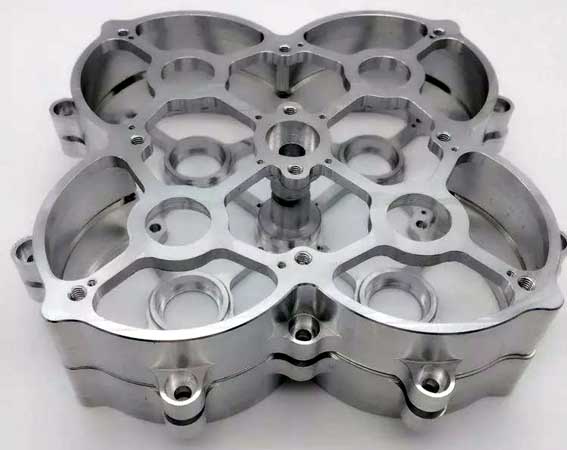
I. Typical parts of the fuselage structure
Typical parts of the aircraft fuselage structure are beams, ribs, ribs, frames, siding, joints, slides and other parts. It is mainly composed of flat parts, elongated parts, multi-chamber parts and ultra-thin wall frame structure. The blanks are sheets, forgings and extruded aluminum profiles. The material utilization rate is only about 5%-10%, and the amount of raw materials removed is large. At present, more than 90% of domestic aircraft parts are aluminum alloy parts, a small amount is stainless steel and titanium alloy, and the overall structural parts are more and more. The application of composite materials is the future development direction.
II. Structural features of typical parts of fuselage structural parts
1, The outline size of the part is getting larger and larger. If any beam parts have a length of 13m.
2, The angle of the bevel of the part changes greatly, and the thin wall and the like. The thinnest part is only about 0.76mm, so the processing rigidity is poor.
3. The structure of the parts is more and more complicated, and many parts adopt the overall structure.
4. The dimensional accuracy and surface quality requirements of parts are getting higher and higher. If some parts are defective after machining, such as burrs, manual removal is not allowed.
III. Machining center machine tool for milling typical parts of the fuselage
1. Three-coordinate machining center, such as large gantry vertical machining center;
2, five-axis linkage machining center, such as large gantry vertical machining center, should be equipped with A / B swing angle milling head or A / C swing angle milling head;
3. From the perspective of development, a large gantry-type dual-spindle five-axis machining center is required, and the working table size is 5m×20m, which is used for processing beam parts;
4, processing aluminum alloy parts requires high-power high-speed machining center, power ≥ 40kW, spindle speed 20000r / min or more, with two-axis swing angle milling head;
5, due to the large amount of aluminum alloy parts cutting processing removal. In order to facilitate chip evacuation, it is best to have a horizontal machining center where the table can be turned over 90°;
The aircraft fuselage structure has many varieties, different shapes, and poor process rigidity, requiring a large number of fixtures. In order to reduce costs and shorten the production preparation cycle, various flexible fixtures are required.
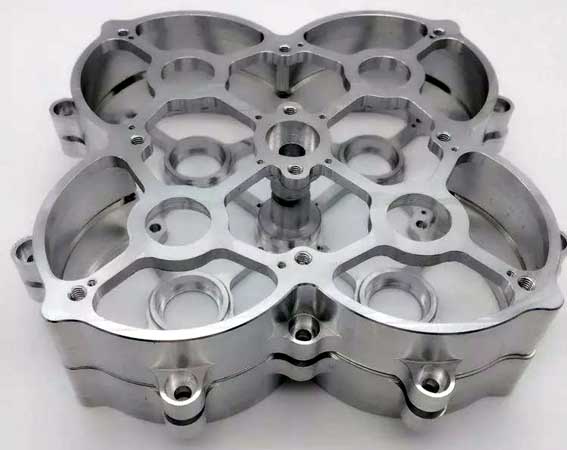
I. Typical parts of the fuselage structure
Typical parts of the aircraft fuselage structure are beams, ribs, ribs, frames, siding, joints, slides and other parts. It is mainly composed of flat parts, elongated parts, multi-chamber parts and ultra-thin wall frame structure. The blanks are sheets, forgings and extruded aluminum profiles. The material utilization rate is only about 5%-10%, and the amount of raw materials removed is large. At present, more than 90% of domestic aircraft parts are aluminum alloy parts, a small amount is stainless steel and titanium alloy, and the overall structural parts are more and more. The application of composite materials is the future development direction.
II. Structural features of typical parts of fuselage structural parts
1, The outline size of the part is getting larger and larger. If any beam parts have a length of 13m.
2, The angle of the bevel of the part changes greatly, and the thin wall and the like. The thinnest part is only about 0.76mm, so the processing rigidity is poor.
3. The structure of the parts is more and more complicated, and many parts adopt the overall structure.
4. The dimensional accuracy and surface quality requirements of parts are getting higher and higher. If some parts are defective after machining, such as burrs, manual removal is not allowed.
III. Machining center machine tool for milling typical parts of the fuselage
1. Three-coordinate machining center, such as large gantry vertical machining center;
2, five-axis linkage machining center, such as large gantry vertical machining center, should be equipped with A / B swing angle milling head or A / C swing angle milling head;
3. From the perspective of development, a large gantry-type dual-spindle five-axis machining center is required, and the working table size is 5m×20m, which is used for processing beam parts;
4, processing aluminum alloy parts requires high-power high-speed machining center, power ≥ 40kW, spindle speed 20000r / min or more, with two-axis swing angle milling head;
5, due to the large amount of aluminum alloy parts cutting processing removal. In order to facilitate chip evacuation, it is best to have a horizontal machining center where the table can be turned over 90°;
The aircraft fuselage structure has many varieties, different shapes, and poor process rigidity, requiring a large number of fixtures. In order to reduce costs and shorten the production preparation cycle, various flexible fixtures are required.