Methods to Improve the Quality of CNC Turning Triangular Thread
Abstract: The triangular thread is widely used in parts, and its processing quality is an important link to ensure product quality.
In the turning process, according to the different materials of the workpiece need to use different materials of the tool, set different cutting parameters and select different cutting fluids, different pitch also need to use different programming methods.
This article describes the method to improve the quality of triangular-threaded CNC turning from the aspects of process factors, cutting methods, programming and operation.
Keywords: triangular thread; tool; cutting amount; cutting method; programming.
Threaded connections are often used in engineering applications. Thread turning is a common task for CNC lathes. CNC lathes can process a variety of threads and triangular threading is the most common. Using CNC turning lathes to turn threads is easier than turning lathes on ordinary lathes, and the machining efficiency is high. It is a commonly used method for machining threads. The quality of threading depends on factors such as process selection, tool selection, programming and operation.
This paper uses the GSK980TD CNC system, the processing material is 45 steel, the blank is Φ42mm bar, and the thread pitch is 1. 5mm. The workpiece is machined as shown in Fig. 1 and discussed on how to improve the turning quality of the triangular thread.
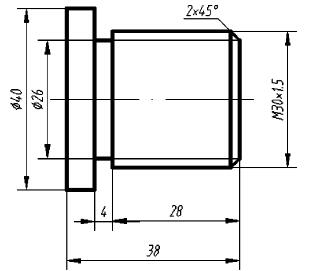
Figure 1. triangular thread parts
1. Effect of process factors on processing quality
Threading process factors are the basic factors on the quality of the threading,
It is very important to master the technological factors of thread processing to improve the quality of thread processing.
1. 1 Reasonable choice of tool material and tool geometry
In the cutting process, the cutter is subject to high pressure, high temperature and large friction. Therefore, the cutter must have high hardness, high heat resistance, good wear resistance, and sufficient strength and toughness. Good strength and toughness materials have poor hardness and wear resistance, and vice versa. CNC turning tools commonly used high-speed steel, carbide, ceramics and superhard materials. Depending on the material of the workpiece, choosing the right tool can improve the quality of parts, increase production efficiency and reduce costs.
For the thread cutting tool, in addition to selecting the appropriate material, the reasonable selection of the tool geometry angle and the shape of the tool tip transition edge is very important to improve the processing quality. The geometric angles of the turning tool include the main declination angle, the auxiliary declination angle, the tool nose angle, the blade inclination angle, the rake angle, the relief angle, and the auxiliary relief angle. The main angle of the thread turning tool is the angle of the tool nose. The size of the tool nose angle directly determines the thread profile, the general triangular thread turning tool, the blade angle is generally 10°, and the tool tip angle is 59°16′. The calculation of the radius formula of the tool tip r = 0. 144P (where P is the pitch).
The declination angle has the greatest influence on the surface roughness. The smaller the primary and secondary declination angles, the lower the surface quality of the thread produced by a thread turning tool with a larger tip radius. The larger the tool front and back angles are, the sharper the tool is, and the higher the thread surface quality is, the less the strength is.
1. 2 Reasonable selection of cutting amount
Choosing the cutting amount rationally is very important for improving the machining quality of CNC lathes. The cutting amount includes cutting depth, feed amount, and cutting speed. The choice of thread cutting amount should be based on the material of the workpiece, the size of the thread pitch, and the processing position of the thread. The cutting amount of the thread should be gradually reduced, and thread feed can sometimes be used as a zero feed amount depending on the material. After summarizing, a list of commonly used cutting amount for turning triangular threads of steel materials is listed, as shown in Table 1.
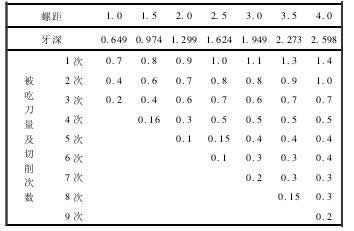
Table 1. The triangular thread common cutting amount table for steel materials
1. 3 reasonable choice of cutting fluid
The rational use of cutting fluid can reduce the machining error caused by the temperature increase, and the cutting fluid forms a lubricant film between the tool and the workpiece surface.Wash away iron scrap to reduce the friction between the tool and the workpiece, reduce tool wear, increase tool life, and prevent workpiece rust.
The cutting fluid that is commonly used in CNC turning is an emulsion with a concentration of 5% to 25%. Some threads can also use oil as the cutting fluid. When cutting brittle materials such as cast iron, no cutting fluid is used because the cutting chips are easily mixed with the cutting fluid to block the movement of the machine tool saddle. When turning the threads, a small amount of oil can be brushed. When cutting steel, aluminum and other plastic metals with high-speed steel cutters, use cutting fluid; When the flow of the cutting fluid can completely cool the carbide tool, the service life of the tool can be improved. Therefore, when turning steel and plastic materials, it is better to use cutting fluid.
1.4 Reasonable Selection of Workholding Methods
The clamping of the workpiece must be firm and have sufficient rigidity. Shaft parts are generally clamped directly with a three-jaw self-centering chuck. In the premise of ensuring the processing length, the shorter the workpiece extension length, the better, to ensure the processing rigidity of the workpiece, The center line of the rod can be coincided with the center line of the spindle as far as possible, so as to avoid hitting the knife. The mounting method of the workpiece must be reasonable, otherwise it will have a negative impact on the processing quality of the workpiece, and it can not play the superiority of high-precision machining of CNC lathes.
2, thread cutting feed method
The thread cutting method is mainly determined according to the size of the thread pitch. Affected by machine tool, workpiece material, insert geometry. Straight thread cutting feed methods include straight-in cutting, oblique-inclined cutting, and alternating side feeds on the left and right sides. As shown in Figure 2, the correct choice of threading feed method is also important for the quality of threading.
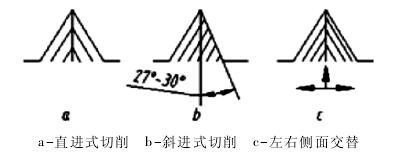
figure 2. The thread turning feed mode
Straight cutting means that the thread tool is radial direct feed, also called radial cutting. Both cutting edges of the thread cutter participate in the cutting, so the cutting force in the axial direction of the cutting tool will cancel each other out, and the tool wears evenly. Reduce the thread turning, due to the axial cutting force, resulting in turning tool skew phenomenon, processed thread shape is clear, good quality. However, due to the concentration of force, poor chip evacuation, and poor heat dissipation during straight thread cutting, especially when turning more than 3 mm pitch, the cutting depth is large and the blade wears quickly, which can easily cause errors in the thread diameter. Therefore, the straight-in cutting method is suitable for thread turning below 3mm. Inclined cutting means that the tool is turned at an angle of 27° to 30° from the radial direction.
In thread turning, because of its single-edge cutting, the tool is less stressed, the chip is fluent and the heat dissipation effect is good, so the surface roughness of the machined thread is slightly lower. However, the blade is relatively easy to damage and wear, resulting in the surface of the machined thread is not straight, the angle of the tool tip is easy to change due to wear, and the precision of the thread shape processed is poor. Therefore, oblique cutting is suitable for threads with a thread pitch of more than 3mm.
Alternating feeds to the left and right sides means that each time the tool feeds in a radial direction, the tool moves horizontally to the left or right a certain distance so that only one side edge of the turning tool can enter the cutting. Turn left and right alternately. Due to the complicated programming of this method, the operation is not as convenient as the above two, and it is generally used for general-purpose lathes and thread processing with a pitch of 3 mm or more.
3, the triangular thread CNC turning programming
Take GSK980TD as an example, the thread machining instruction of this system has the same pitch thread cutting instruction G32, Variable pitch thread cutting G34, The Z-axis tapping cycle command G33, thread cutting cycle command G92 and multiple screw thread cutting cycle command G76. The G32 and G92 instructions can process straight thread, taper thread, and end thread with constant pitch. The cutting methods are straight-in cutting and side-to-side alternate cutting. The G32 instruction belongs to a single program segment. When it is cut several times, the programming is longer and generally not used. The cutting method of the G92 command belongs to straight cutting and alternating left and right cutting. Because the instruction processing thread diameter error is large, but the teeth with high precision, Generally used for the processing of small pitch high precision thread.
G76 instruction can process straight thread and taper thread with thread stripping. It can realize single-side knife thread cutting. The amount of knife is gradually reduced, which is beneficial to protect the tool and improve the precision of the thread, but it cannot process the face thread. Because this instruction is more reasonable in terms of processability and programming efficiency, it is widely used.
based on the above analysis, Figure 1 shows the G92 command for thread machining and the thread path for G92 command is shown in Figure 3.
Point A is the thread starting point (end point).
Point B is the starting point of thread cutting.
L1 is the thread cutter's cutting amount (L1≥2P),
L0 is the effective cutting amount of thread,
L2 is the amount of thread cutter exit (L2≥0. 5P),
L3 is the thread withdrawal width (when the thread does not have an undercut, it is set according to the pitch, and when there is a undercut, it can be 0).
Point C is the cutting end point.
Point D is the radial direction of the thread and the end of the retraction.
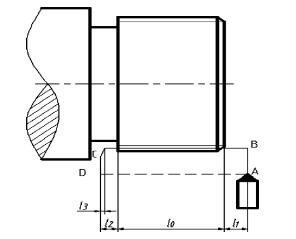
image 3. Tool path G92 instruction
In the turning process, according to the different materials of the workpiece need to use different materials of the tool, set different cutting parameters and select different cutting fluids, different pitch also need to use different programming methods.
This article describes the method to improve the quality of triangular-threaded CNC turning from the aspects of process factors, cutting methods, programming and operation.
Keywords: triangular thread; tool; cutting amount; cutting method; programming.
Threaded connections are often used in engineering applications. Thread turning is a common task for CNC lathes. CNC lathes can process a variety of threads and triangular threading is the most common. Using CNC turning lathes to turn threads is easier than turning lathes on ordinary lathes, and the machining efficiency is high. It is a commonly used method for machining threads. The quality of threading depends on factors such as process selection, tool selection, programming and operation.
This paper uses the GSK980TD CNC system, the processing material is 45 steel, the blank is Φ42mm bar, and the thread pitch is 1. 5mm. The workpiece is machined as shown in Fig. 1 and discussed on how to improve the turning quality of the triangular thread.
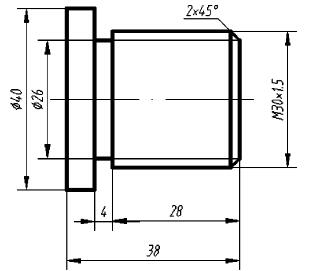
Figure 1. triangular thread parts
1. Effect of process factors on processing quality
Threading process factors are the basic factors on the quality of the threading,
It is very important to master the technological factors of thread processing to improve the quality of thread processing.
1. 1 Reasonable choice of tool material and tool geometry
In the cutting process, the cutter is subject to high pressure, high temperature and large friction. Therefore, the cutter must have high hardness, high heat resistance, good wear resistance, and sufficient strength and toughness. Good strength and toughness materials have poor hardness and wear resistance, and vice versa. CNC turning tools commonly used high-speed steel, carbide, ceramics and superhard materials. Depending on the material of the workpiece, choosing the right tool can improve the quality of parts, increase production efficiency and reduce costs.
For the thread cutting tool, in addition to selecting the appropriate material, the reasonable selection of the tool geometry angle and the shape of the tool tip transition edge is very important to improve the processing quality. The geometric angles of the turning tool include the main declination angle, the auxiliary declination angle, the tool nose angle, the blade inclination angle, the rake angle, the relief angle, and the auxiliary relief angle. The main angle of the thread turning tool is the angle of the tool nose. The size of the tool nose angle directly determines the thread profile, the general triangular thread turning tool, the blade angle is generally 10°, and the tool tip angle is 59°16′. The calculation of the radius formula of the tool tip r = 0. 144P (where P is the pitch).
The declination angle has the greatest influence on the surface roughness. The smaller the primary and secondary declination angles, the lower the surface quality of the thread produced by a thread turning tool with a larger tip radius. The larger the tool front and back angles are, the sharper the tool is, and the higher the thread surface quality is, the less the strength is.
1. 2 Reasonable selection of cutting amount
Choosing the cutting amount rationally is very important for improving the machining quality of CNC lathes. The cutting amount includes cutting depth, feed amount, and cutting speed. The choice of thread cutting amount should be based on the material of the workpiece, the size of the thread pitch, and the processing position of the thread. The cutting amount of the thread should be gradually reduced, and thread feed can sometimes be used as a zero feed amount depending on the material. After summarizing, a list of commonly used cutting amount for turning triangular threads of steel materials is listed, as shown in Table 1.
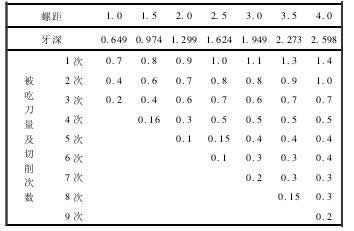
Table 1. The triangular thread common cutting amount table for steel materials
The thread cutting speed should be selected lower. The thread of the CNC lathe mainly depends on the spindle encoder. When the spindle speed is selected too high, the positioning pulse sent by the encoder may screw broken teeth due to "overshoot", most CNC lathe programming as shown below:
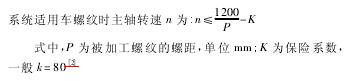
1. 3 reasonable choice of cutting fluid
The rational use of cutting fluid can reduce the machining error caused by the temperature increase, and the cutting fluid forms a lubricant film between the tool and the workpiece surface.Wash away iron scrap to reduce the friction between the tool and the workpiece, reduce tool wear, increase tool life, and prevent workpiece rust.
The cutting fluid that is commonly used in CNC turning is an emulsion with a concentration of 5% to 25%. Some threads can also use oil as the cutting fluid. When cutting brittle materials such as cast iron, no cutting fluid is used because the cutting chips are easily mixed with the cutting fluid to block the movement of the machine tool saddle. When turning the threads, a small amount of oil can be brushed. When cutting steel, aluminum and other plastic metals with high-speed steel cutters, use cutting fluid; When the flow of the cutting fluid can completely cool the carbide tool, the service life of the tool can be improved. Therefore, when turning steel and plastic materials, it is better to use cutting fluid.
1.4 Reasonable Selection of Workholding Methods
The clamping of the workpiece must be firm and have sufficient rigidity. Shaft parts are generally clamped directly with a three-jaw self-centering chuck. In the premise of ensuring the processing length, the shorter the workpiece extension length, the better, to ensure the processing rigidity of the workpiece, The center line of the rod can be coincided with the center line of the spindle as far as possible, so as to avoid hitting the knife. The mounting method of the workpiece must be reasonable, otherwise it will have a negative impact on the processing quality of the workpiece, and it can not play the superiority of high-precision machining of CNC lathes.
2, thread cutting feed method
The thread cutting method is mainly determined according to the size of the thread pitch. Affected by machine tool, workpiece material, insert geometry. Straight thread cutting feed methods include straight-in cutting, oblique-inclined cutting, and alternating side feeds on the left and right sides. As shown in Figure 2, the correct choice of threading feed method is also important for the quality of threading.
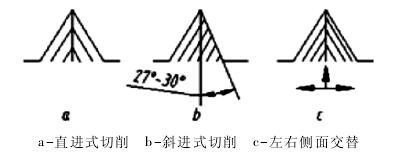
figure 2. The thread turning feed mode
Straight cutting means that the thread tool is radial direct feed, also called radial cutting. Both cutting edges of the thread cutter participate in the cutting, so the cutting force in the axial direction of the cutting tool will cancel each other out, and the tool wears evenly. Reduce the thread turning, due to the axial cutting force, resulting in turning tool skew phenomenon, processed thread shape is clear, good quality. However, due to the concentration of force, poor chip evacuation, and poor heat dissipation during straight thread cutting, especially when turning more than 3 mm pitch, the cutting depth is large and the blade wears quickly, which can easily cause errors in the thread diameter. Therefore, the straight-in cutting method is suitable for thread turning below 3mm. Inclined cutting means that the tool is turned at an angle of 27° to 30° from the radial direction.
In thread turning, because of its single-edge cutting, the tool is less stressed, the chip is fluent and the heat dissipation effect is good, so the surface roughness of the machined thread is slightly lower. However, the blade is relatively easy to damage and wear, resulting in the surface of the machined thread is not straight, the angle of the tool tip is easy to change due to wear, and the precision of the thread shape processed is poor. Therefore, oblique cutting is suitable for threads with a thread pitch of more than 3mm.
Alternating feeds to the left and right sides means that each time the tool feeds in a radial direction, the tool moves horizontally to the left or right a certain distance so that only one side edge of the turning tool can enter the cutting. Turn left and right alternately. Due to the complicated programming of this method, the operation is not as convenient as the above two, and it is generally used for general-purpose lathes and thread processing with a pitch of 3 mm or more.
3, the triangular thread CNC turning programming
Take GSK980TD as an example, the thread machining instruction of this system has the same pitch thread cutting instruction G32, Variable pitch thread cutting G34, The Z-axis tapping cycle command G33, thread cutting cycle command G92 and multiple screw thread cutting cycle command G76. The G32 and G92 instructions can process straight thread, taper thread, and end thread with constant pitch. The cutting methods are straight-in cutting and side-to-side alternate cutting. The G32 instruction belongs to a single program segment. When it is cut several times, the programming is longer and generally not used. The cutting method of the G92 command belongs to straight cutting and alternating left and right cutting. Because the instruction processing thread diameter error is large, but the teeth with high precision, Generally used for the processing of small pitch high precision thread.
G76 instruction can process straight thread and taper thread with thread stripping. It can realize single-side knife thread cutting. The amount of knife is gradually reduced, which is beneficial to protect the tool and improve the precision of the thread, but it cannot process the face thread. Because this instruction is more reasonable in terms of processability and programming efficiency, it is widely used.
based on the above analysis, Figure 1 shows the G92 command for thread machining and the thread path for G92 command is shown in Figure 3.
Point A is the thread starting point (end point).
Point B is the starting point of thread cutting.
L1 is the thread cutter's cutting amount (L1≥2P),
L0 is the effective cutting amount of thread,
L2 is the amount of thread cutter exit (L2≥0. 5P),
L3 is the thread withdrawal width (when the thread does not have an undercut, it is set according to the pitch, and when there is a undercut, it can be 0).
Point C is the cutting end point.
Point D is the radial direction of the thread and the end of the retraction.
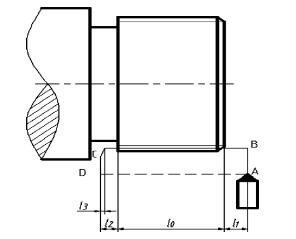
image 3. Tool path G92 instruction
4, thread processing operation skills
The knife setting technique of the thread knife, unlike the round turning tool, can accurately locate its position. Thread axial alignment is generally based on the operator's visual measurement of whether the tool tip coincides with the origin of the workpiece.
When the axial requirement of the thread is high, due to the visual error of the operator, the inaccuracy of the knife is easily caused, resulting in overcutting. To solve this problem, the operator can reserve the allowance in the axial and radial directions when setting the tool.( Thread long axis generally stays 0. 5mm - 1mm, and the minor axis of the thread generally stays 0. 2mm - 0. 5mm).
Through the first trial cut, the tool offset is adjusted after measurement (for ±W in the axial direction and ±U in the radial direction) to ensure that no over-cutting occurs. After the thread knife is used for many times, especially when processing high hardness materials such as stainless steel and nickel alloy, the tool wears quickly, so it is necessary to measure more, and the workpiece can be removed after passing the measurement. To master the tool wear law, it is possible to modify the tool compensation before the program is run to improve the thread processing quality and production efficiency.
5. Conclusion
In the actual processing and production, in addition to selecting suitable tools according to the workpiece material, pitch, etc., According to the thread pitch and processing characteristics to select the appropriate programming method, flexible use of thread processing instructions, Sometimes it is also possible to use a combination of two machining cycles, a cycle command (G76) and a single-segment command (G32), to give full play to the special features of each command and guarantee the quality of the thread. The reasonable use of the above knowledge can effectively improve the qualified rate of thread processing and ensure the processing quality of triangular threads.
The knife setting technique of the thread knife, unlike the round turning tool, can accurately locate its position. Thread axial alignment is generally based on the operator's visual measurement of whether the tool tip coincides with the origin of the workpiece.
When the axial requirement of the thread is high, due to the visual error of the operator, the inaccuracy of the knife is easily caused, resulting in overcutting. To solve this problem, the operator can reserve the allowance in the axial and radial directions when setting the tool.( Thread long axis generally stays 0. 5mm - 1mm, and the minor axis of the thread generally stays 0. 2mm - 0. 5mm).
Through the first trial cut, the tool offset is adjusted after measurement (for ±W in the axial direction and ±U in the radial direction) to ensure that no over-cutting occurs. After the thread knife is used for many times, especially when processing high hardness materials such as stainless steel and nickel alloy, the tool wears quickly, so it is necessary to measure more, and the workpiece can be removed after passing the measurement. To master the tool wear law, it is possible to modify the tool compensation before the program is run to improve the thread processing quality and production efficiency.
5. Conclusion
In the actual processing and production, in addition to selecting suitable tools according to the workpiece material, pitch, etc., According to the thread pitch and processing characteristics to select the appropriate programming method, flexible use of thread processing instructions, Sometimes it is also possible to use a combination of two machining cycles, a cycle command (G76) and a single-segment command (G32), to give full play to the special features of each command and guarantee the quality of the thread. The reasonable use of the above knowledge can effectively improve the qualified rate of thread processing and ensure the processing quality of triangular threads.