Electroplating Method & Technology
Plating is divided into hanging plating, barrel plating, continuous plating, and brush plating, and is mainly related to the size and batch of parts to be plated.
Hanging plating is suitable for general-size products such as bumpers for cars, handlebars for bicycles, etc.
Barrel plating is suitable for small parts, fasteners, washers, pins, etc.
Continuous plating of wire and strip suitable for mass production.
Brush plating is suitable for partial plating or repair.
The plating solution has acidic, alkaline and acidic and neutral solutions with a chromium mixture.
No matter what kind of plating method is used, plating tanks and hanging fixtures that are in contact with the products to be plated and the plating solution should have a certain degree of versatility.
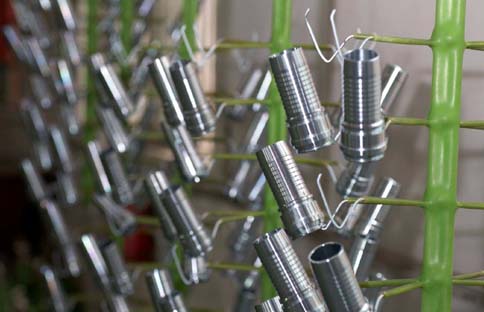
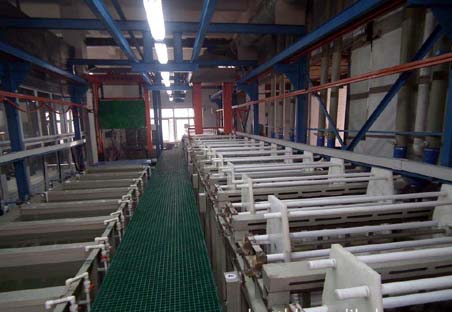
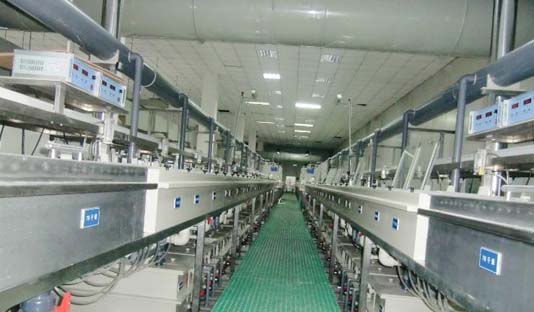
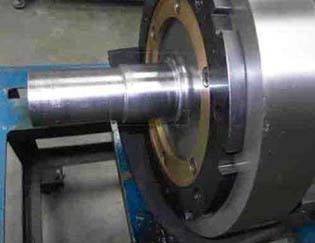
Plating technology
Cyanide-free alkaline bright copper
Pre-plating and thickening are performed on the copper alloy in one step, and the thickness of the plating layer can reach 10 μm or more. Acidic bright copper coating, if blackened to achieve dark effect, has been operating in a 10,000-liter tank for two years.
Can completely replace the traditional cyanide copper plating process and bright copper plating process, applicable to any metal substrate: Pure copper beryllium-copper alloy, iron-tantalum alloy, stainless-steel yttrium-zinc alloy die-casting, and aluminum, aluminum alloy workpieces can be rack-mounted or barrel-rolled.
Cyanide-free bright silver plating
The common type uses thiosulfate as the main complexing agent, and the advanced type uses sulfur-free organics as the main complexing agent. Full bright coating thickness up to 40μm, plating surface resistance ~ 41μΩ · cm, hardness ~ HV101.4, thermal shock 298K (25 °C) qualified, very close to the performance of cyanide silver plating.
Cyanide-free gold plating
The non-cyanide autocatalytic gold plating main salt uses Na3[Au(SO3)2] and the gold layer thickness can reach 1.5μm. It has been used for gold plating on high-density flexible circuit boards and electronic ceramics.
Non-formaldehyde copper plating
Non-formaldehyde autocatalytic copper plating, used for via plating and non-conductor surface metallization of circuit boards. The removal of toxic formaldehyde has been replaced by cheap and non-toxic hypophosphite, and there are no commercial products at home and abroad. The laboratory research has been basically completed, with a deposition rate of 3 to 4 μm/h, a life expectancy of more than 10 cycles (MTO), and a dense and bright coating. But it needs to be further improved and tested in the pilot test.
Pure palladium plating
Ni can cause dermatitis. The European Union has long refused to import Ni-containing accessories. Palladium is the best substitute for Ni metal.This project was completed in 1997 and includes two processes:
First, thin palladium plating, thickness 0.1 ~ 0.2μm, has been used as anti-corrosion decorative coating and anti-silver color-changing layer on the white copper tin;
The second is thick palladium plating, with a thickness of 3 μm without cracks (international level). Because palladium is expensive, it has not yet entered the domestic market.
Trivalent chromium zinc coating blue and white color passivation agent
The trivalent chromium salt replaces the carcinogenic hexavalent chromium salt.The blue and white passivation color, such as the chrome plating layer, passes the neutral salt spray test for more than 24 hours, and some special treatments can reach the neutral salt spray test for more than 96 hours, which has experienced a decade of market test. Color passivation than blue and white passivation, bright color, its salt spray test time is much higher than the blue and white passivation, can reach 48 to 120 hours.
Pure gold plating
The main salt is K[Au(CN)2], which is a microcyanide process. Gold plating purity 99.99%, gold wire (30μm) bonding strength> 5g, solder ball (25μm) shear strength> 1.2Kg. Knoop hardness H < 90, has been used for high-density flexible circuit board gold plating.
White steel plating
There are two kinds of Pd(60)Ni(40) and Pd(80)Ni(20), which have been used as gold-plating and anti-silver discoloration layers in electronic products.
Nano-nickel
The environmentally friendly products developed using nanotechnology can completely replace traditional cyanide copper plating pre-plating and traditional chemical nickel. Applicable to iron, stainless steel, copper, copper alloy, aluminum, aluminum alloy, zinc, zinc alloy, titanium, etc., can be plated or barrel plating.
High-speed chrome plating
Save cost, high plating speed, high wear resistance, high corrosion resistance. Not only can increase current efficiency, but also enhance wear and corrosion resistance. Suitable for any hard chrome plating process, including; micro-cracks chrome, opal chrome, and bright chrome. Good quality, stable technology, high production efficiency, energy conservation, and significant economic benefits.
Other technologies
Precious metal gold, silver, palladium recovery technology; diamond inlaid plating technology; Stainless steel electrochemical and chemical polishing techniques; Textile plating copper, nickel plating technology; hard gold (Au-Co, Au-Ni) plating; Palladium-cobalt alloy electroplating; gun black Sn-Ni electroplating; electroless gold plating; pure gold immersion plating; chemical silver immersion; chemical immersion tin.
Plating classification
If the composition of the coating can be divided into a single metal coating, alloy coating and composite coating three categories.
If classified by purpose, it can be divided into:
1. protective coating;
2. protective decorative plating;
3. decorative plating;
4 repair coating;
5. functional coating
Single metal plating
The single metal plating has more than 170 years of history. 33 kinds of metals on the periodic table have been electrodeposited from aqueous solutions. Commonly used more than 10 kinds of electroplating zinc, nickel, chromium, copper, tin, iron, cobalt, cadmium, lead, gold, silver and so on. The plating layer formed by depositing two or more elements simultaneously on the cathode is an alloy plating layer. The alloy coating has the organizational structure and properties not possessed by a single metal coating. Such as amorphous Ni-P alloy, Sn-alloys on the phase diagram, as well as special decorative appearance, particularly high corrosion resistance and excellent weldability, magnetic alloy coating and so on.
Composite plating
Composite plating is a process in which solid particles are added to the plating solution and co-deposited with the metal or alloy to form a metal-based surface composite material to meet specific application requirements.
According to the classification of the electrochemical properties between the plating and the base metal, the electroplating layer can be divided into two major categories, anode coating and cathode coating.
Where the potential of the plated metal with respect to the base metal is negative, the plated layer is an anode when the corrosion micro-cell is formed, so it is called an anode plated layer, such as a galvanized layer on a steel piece;
The plating metal has a positive potential with respect to the base metal, and when the corrosion micro cell is formed, the plating layer is a cathode, so it is called a cathode coating.Such as the nickel-plated steel layer and tin plating layer.
According to the purpose of use can be divided into:
1. Protective coatings: Such as Zn, Ni, Cd, Sn and Cd-Sn and other coatings, as a corrosion resistant coating against atmospheric and various corrosive environments;
2, protective - decorative coating: Such as Cu-Ni-Cr, Ni-Fe-Cr composite coating, both decorative and protective;
3, decorative coating: Such as Au, Ag and Cu. Imitation gold plating, black chrome, black nickel plating, etc.
4, repair coating: Such as electroplating Ni, Cr, Fe layer to repair some of the costly wear parts or processing super bad parts;
5, functional coating: Such as Ag, Au and other conductive coating; Ni-Fe, Fe-Co, Ni-Co and other magnetic coating; Cr, Pt-Ru and other high-temperature anti-oxidation coating; Ag, Cr and other reflective coating; Black chromium, black nickel and other anti-reflective coating; Hard chrome, Ni. SiC and other wear-resistant coatings; Ni. VIEE, Ni. C (graphite) anti-friction coating and so on; Solderable coatings such as Pb, Cu, Sn, and Ag; Anti-carburizing carbon plating etc.
Electroplating power supply
Power composition
The main circuit mainly includes a main transformer, a power rectifying device, and some detection and protection devices. The main transformer in the electroplating power supply is the voltage required to reduce the AC power supply voltage to the plating process. The thyristor rectifier uses an industrial frequency (50Hz) transformer, and a high-frequency (10 to 50kHz) transformer is used in the high-frequency switching power supply. Detection devices include voltmeters, current transformers, etc. The protection device is mainly used for overcurrent protection of power rectifier devices. The control circuit mainly includes a trigger control circuit such as a thyristor or an IGBT, a soft start circuit of a power supply, an over-current and over-voltage protection circuit, and a power supply phase loss protection circuit.
Power Features
1, energy-saving effect is good
Since the switching power supply adopts a high frequency transformer, the conversion efficiency is greatly improved. Under normal circumstances, more than 10% more efficiency than SCR equipment, the load rate of 70% or less, more efficient than SCR equipment, more than 30%.
2, high output stability
Due to the fast system response (microseconds), it is highly adaptable to network and load changes, and the output accuracy is better than 1%. The switching power supply has high working efficiency, so the control accuracy is high, which helps to improve product quality.
3, the output waveform is easy to modulate
Because the operating frequency is high, the output waveform adjustment is relatively low in relative processing cost, and the output waveform can be changed in accordance with user's process requirements more conveniently.
This has a stronger effect on improving work efficiency and improving the quality of processed products on the job site.
4, small size, light weight
The volume and weight are 1/5-1/10 of the thyristor electroplating power supply, facilitating planning, expansion, movement, maintenance and installation.
Material and Equipment Terminology
1. Anode bag: Made with cotton or polyester fabric jacket, on the anode, in order to prevent the anode sludge into the solution in the bag.
2. Brighteners: To obtain bright coating, additives in the electrolyte used.
3. Resistant: Substances that slow the rate of chemical reactions or electrochemical reactions.
4. Surfactant: Substances that can significantly reduce the interfacial tension even at very low levels of addition.
5. Emulsifier: Can reduce the interfacial tension between the immiscible liquid, so that the material forming the emulsion.
6. Complexing agent : Compounds that can combine with metal ions or metal ion-containing compounds to form complexes.
7. Insulation : Electrodes applied to a part or the rack, so that the parts of the surface layer of non-conductive material.
8. Hangers (fixtures) : A tool used to suspend parts for easy placement of parts in slots for plating or other processing.
9. Wetting agent : Can reduce the interfacial tension between the solution and the article, so that article surface is easily wetted material.
10. Additives : A small amount of additives contained in the solution that can improve the electrochemical performance of the solution or improve the quality of the coating.
11. Buff er: A substance that can maintain a substantially constant pH of the solution within a certain range.
12. Mobile cathode: With a mechanical device, the cathodes of the plated articles and the pole bars are periodically reciprocated.
Test and test Terminology
1. Discontinuous water film: It is generally used for non-uniform wettability caused by contamination of the surface, making the water film on the surface discontinuous.
2. Porosity: The number of pinholes per unit area.
3. Pinhole: From the surface of the coating to the tiny holes in the underlying coating or substrate metal, It is due to the fact that the electrodeposition process at certain points on the surface of the cathode is hindered, so that the coating cannot be deposited there and the surrounding plating is continuously thickened.
4. Discoloration: Changes in the color of the surface of the metal or plating due to corrosion (eg, darkening, discoloration, etc.).
5. Cohesion: The strength of the bond between the coating and the base material.
6. Skin: Coating into a sheet, the matrix material from the phenomenon.
7. Stripping: Some reasons (such as non-uniform thermal expansion or contraction) caused the surface coating to break or fall off.
8. Orange peel: Similar to orange peel corrugated surface treatment layer.
9. Sponge coating : A loose porous deposit that is formed during electroplating and that is not strongly bonded to the matrix material.
10. Scratch coating : The dark, rough, loose and other poor quality deposits formed at high currents often contain oxides or other impurities.
11. pitting: In electroplating or etching, pits or holes formed in metal surfaces.
12. Rough: In the electroplating process, the coating due to various causes rough not smooth phenomenon.
13. Plating solderability: The ability of the plating surface to be wetted by the molten solder.