Misunderstanding and Analysis of High Accuracy in CNC Machine Tool Processing
I have been working on CNC machine tools for a while now. Found that many mechanical employees and even professional engineering and technical personnel, there are many misunderstandings of CNC machining accuracy. In production, it is often possible to hear workers say that this is a product processed, by a certain brand of CNC machine tools, how accurate it is, In fact, this is unscientific as a professional technician. Underneath, I feel that it is necessary to explain whether the accuracy of CNC is really as mysterious as it is in legend, or whether it is hidden.
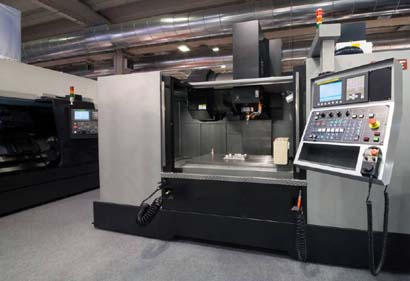
First of all, we have to figure out what the accuracy is.
Usually the precision in machining refers to four points:
1, dimensional tolerances
2, shape tolerance
3, position tolerance
4, the surface finish,
These concepts were mentioned in the teaching of tolerances, and he used the concepts of splines to apply these concepts; But you see the "Machine Design Course Design" and the "Mechanical Practical Design Manual." He did not use these concepts in the labeling of splines. It can be seen that he is actually a concept that can be used. Novice may feel strange, how could it be? In fact, there are many concepts in the machine that can be interchanged, such as the parallelism tolerance. It can also be said that two faces face each other at the same time with a handle tolerance. )
Returning to the accuracy problem, now that we are clear about the concept of accuracy, The following questions are whether CNC machine tools do this with good accuracy. First of all, we must clarify the characteristics of CNC machine tools. CNC machine tools, in fact, is the NC system installed on the machine, so it is called CNC. Many of China's good CNC machine tools have been refitted by installing ordinary CNC machines and feeding systems. (Of course, the point of exquisite research will increase the ball screw and increase the accuracy of the spindle bearing. However, based on my experience, in fact, the accuracy of the mechanical part is improved, which has little effect on the accuracy of the whole bed machining, because of the influence of the tool, which will be discussed later.) Then what precision is added to the numerical control device and the feeding service system? Improve position tolerances! ! ! Is it helpful to improve the other tolerance levels? The result of my research is not! ! ! !
This is the first point I want to elaborate. That is the core of the CNC machine (that is, people's most deified). The CNC machine and the feeding system increase the position tolerance of the machine tool processing. (In fact, the main improvement of the entire CNC machine tool compared to ordinary machine tools is also these, and will be mentioned later). Because you think about what digital control improves? Is the accuracy of the tool or the table in the feed position. Positioning accuracy, location tolerances also increased? But can he improve other tolerances? Impossible. Can you improve the surface finish by "going" the position? impossible, What is the guarantee of "clean finish"? First is the tool. Second is the rigidity of the machine. Can you improve the accuracy by installing the numerical control device and the feeding service system? ,impossible, No matter the CNC lathe or boring and milling machine, even the machining center is impossible to achieve the surface finish of the grinder.
And the tolerance of shape tolerance is the same. The so-called shape tolerance is the unevenness of his plane. Round circle is not round, rely on the position of the table to ensure degree tolerance? impossible, His bottom line is that you have a smooth surface, and you want to look on the surface. How can the plane be flat?
As far as dimensional tolerances are concerned, it is no problem to pull, and high-precision dimensional tolerances are actually guaranteed by the precision of the mechanical part of the machine tool. It has nothing to do with electrical control (in high-precision machining), So you look at the general introduction of CNC machining accuracy is 0.01mm, which is collectively referred to as a wire, To understand this tolerance you can do the instrument lathe, grinders easily reach this standard.
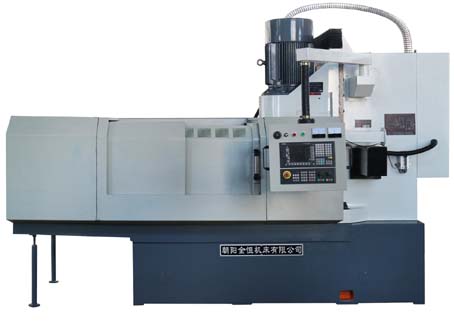
Some people may question that the spindle components and spindle bearings of CNC machine tools have high rotation accuracy and good rigidity. Ball screws are adopted for the feed drive, and the direction gap is eliminated by adding preload, so the precision of the mechanical part is high.
Then I can tell you, First, the improvement of the precision of the mechanical part has nothing to do with the electrical appliances. In other words, any machine tool can do this to improve the accuracy.
Second, in fact, these have little effect on the smoothness and shape tolerance of the machine tool, because the key to finish machining is metal cutting, and the last link of cutting is the tool.
The reason for the high precision of the grinder lies in the fact that there is a fundamental difference between the grinding wheel and the tool, and the difference in quality caused by this difference. It's not that you can improve the accuracy of the drive train. Is it like powerful elephants that can be eaten by strong tigers? Impossible, he is also a tiger, the most severe tiger, can not become like; In other words, your CNC lathes, boring machines and even machining centers are all impossible to make the quality of the grinder, such as finish, shape and so on.
Having said so much, I am afraid that some people would say that they are opposed to advanced production. No, I wrote this article in the hope that you will understand what is the most suitable part for CNC machine tools. In fact, the most typical is a hole-like component that has a number of holes, such as a gearbox case, in which each part has a positional tolerance relationship. The box, whether it is a hole or a mounting reference plane, in fact, its surface finish and roundness flatness tolerance requirements are not very high, the general precision milling can be done, In this way, it is possible to realize the high degree of tolerance in the machining position of the numerically-controlled machine tool, and since there is no need to change after programming, the machining efficiency is also high. Conversely, for some parts, the machining curve is very simple, the requirements for surface finish are high (0.8 for grinders), and there are no special requirements for position (for example, shafts for gearboxes). There is no need for a CNC lathe at all. That is why it is not worth the trouble.
Process is a complicated and serious matter, it is a scientific matter. However, many technologists now have little knowledge and are irresponsible. Moving the CNC machine tools and machining centers, yes, these advanced equipments make the current processing much easier. Many technologies in traditional machinery, such as prototypes, are not needed because of the emergence of these technologies; However, things have a two-way nature. If we insist on simple and rely on CNC, it will inevitably cause the high cost of parts production. We must know that the price of CNC equipment is very expensive, far more than ordinary equipment; The qualifications of CNC machining professionals are generally more than specialists, and the human cost is also high; The power and spindle speed of CNC machine tools is much higher than that of ordinary machine tools, and the cost of machine tool operation is also alarming.
Therefore, my opinion is that we must avoid increasing the cost of equipment use in our production process. Under the same conditions, we must choose a small-cost processing method. Because companies are motivated to make profits, those clamoring about costing are self-deceiving nerds and are unrealistic. Therefore, we must not use CNC as a Wanbao Book or moving a machining center. This is not good for the development of enterprises, the maturity of products, and the promotion of the market. CNC should actually become a sharp knife in the production process (a good steel is used on the blade), Instead of being a synonym for technology laziness or a business card that is worth raising, like many companies, it is the sorrow of the machinery industry practitioners.
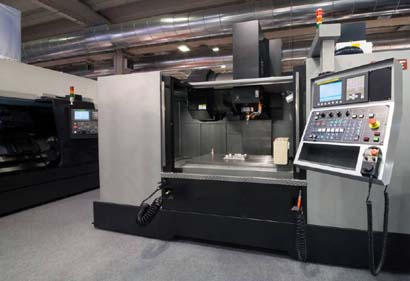
First of all, we have to figure out what the accuracy is.
Usually the precision in machining refers to four points:
1, dimensional tolerances
2, shape tolerance
3, position tolerance
4, the surface finish,
These concepts were mentioned in the teaching of tolerances, and he used the concepts of splines to apply these concepts; But you see the "Machine Design Course Design" and the "Mechanical Practical Design Manual." He did not use these concepts in the labeling of splines. It can be seen that he is actually a concept that can be used. Novice may feel strange, how could it be? In fact, there are many concepts in the machine that can be interchanged, such as the parallelism tolerance. It can also be said that two faces face each other at the same time with a handle tolerance. )
Returning to the accuracy problem, now that we are clear about the concept of accuracy, The following questions are whether CNC machine tools do this with good accuracy. First of all, we must clarify the characteristics of CNC machine tools. CNC machine tools, in fact, is the NC system installed on the machine, so it is called CNC. Many of China's good CNC machine tools have been refitted by installing ordinary CNC machines and feeding systems. (Of course, the point of exquisite research will increase the ball screw and increase the accuracy of the spindle bearing. However, based on my experience, in fact, the accuracy of the mechanical part is improved, which has little effect on the accuracy of the whole bed machining, because of the influence of the tool, which will be discussed later.) Then what precision is added to the numerical control device and the feeding service system? Improve position tolerances! ! ! Is it helpful to improve the other tolerance levels? The result of my research is not! ! ! !
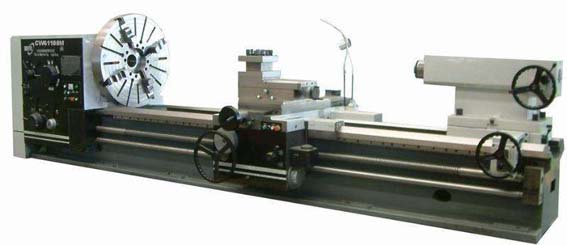
And the tolerance of shape tolerance is the same. The so-called shape tolerance is the unevenness of his plane. Round circle is not round, rely on the position of the table to ensure degree tolerance? impossible, His bottom line is that you have a smooth surface, and you want to look on the surface. How can the plane be flat?
As far as dimensional tolerances are concerned, it is no problem to pull, and high-precision dimensional tolerances are actually guaranteed by the precision of the mechanical part of the machine tool. It has nothing to do with electrical control (in high-precision machining), So you look at the general introduction of CNC machining accuracy is 0.01mm, which is collectively referred to as a wire, To understand this tolerance you can do the instrument lathe, grinders easily reach this standard.
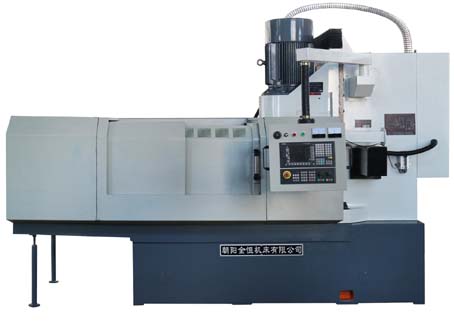
Some people may question that the spindle components and spindle bearings of CNC machine tools have high rotation accuracy and good rigidity. Ball screws are adopted for the feed drive, and the direction gap is eliminated by adding preload, so the precision of the mechanical part is high.
Then I can tell you, First, the improvement of the precision of the mechanical part has nothing to do with the electrical appliances. In other words, any machine tool can do this to improve the accuracy.
Second, in fact, these have little effect on the smoothness and shape tolerance of the machine tool, because the key to finish machining is metal cutting, and the last link of cutting is the tool.
The reason for the high precision of the grinder lies in the fact that there is a fundamental difference between the grinding wheel and the tool, and the difference in quality caused by this difference. It's not that you can improve the accuracy of the drive train. Is it like powerful elephants that can be eaten by strong tigers? Impossible, he is also a tiger, the most severe tiger, can not become like; In other words, your CNC lathes, boring machines and even machining centers are all impossible to make the quality of the grinder, such as finish, shape and so on.
Having said so much, I am afraid that some people would say that they are opposed to advanced production. No, I wrote this article in the hope that you will understand what is the most suitable part for CNC machine tools. In fact, the most typical is a hole-like component that has a number of holes, such as a gearbox case, in which each part has a positional tolerance relationship. The box, whether it is a hole or a mounting reference plane, in fact, its surface finish and roundness flatness tolerance requirements are not very high, the general precision milling can be done, In this way, it is possible to realize the high degree of tolerance in the machining position of the numerically-controlled machine tool, and since there is no need to change after programming, the machining efficiency is also high. Conversely, for some parts, the machining curve is very simple, the requirements for surface finish are high (0.8 for grinders), and there are no special requirements for position (for example, shafts for gearboxes). There is no need for a CNC lathe at all. That is why it is not worth the trouble.
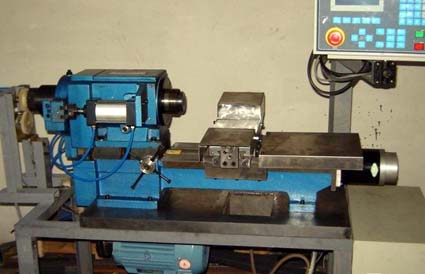
Therefore, my opinion is that we must avoid increasing the cost of equipment use in our production process. Under the same conditions, we must choose a small-cost processing method. Because companies are motivated to make profits, those clamoring about costing are self-deceiving nerds and are unrealistic. Therefore, we must not use CNC as a Wanbao Book or moving a machining center. This is not good for the development of enterprises, the maturity of products, and the promotion of the market. CNC should actually become a sharp knife in the production process (a good steel is used on the blade), Instead of being a synonym for technology laziness or a business card that is worth raising, like many companies, it is the sorrow of the machinery industry practitioners.
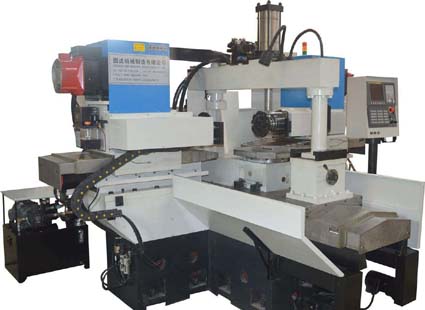
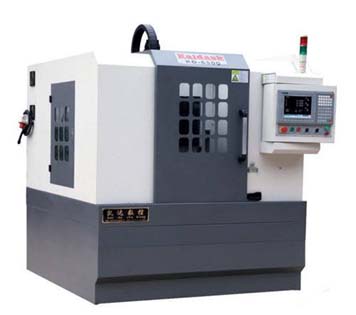
PREV:Metal Products Rust Causes And Solutions
NEXT:NONE
NEXT:NONE