Plating Technology & Precautions
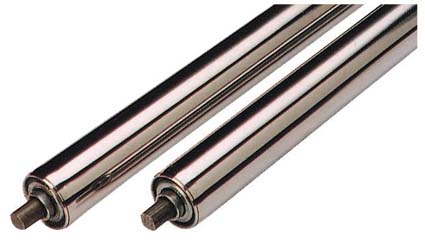
Electro-galvanized:
Is the use of electrolysis, the formation of a uniform, dense, well-integrated metal or alloy deposition layer on the surface of the workpiece. Compared with other metals, zinc is a relatively inexpensive and easily-plated metal and is a low-value corrosion-resistant plating.
It is widely used to protect steel parts, especially to prevent atmospheric corrosion, and for decoration. Plating techniques include slot plating (or rack plating), barrel plating (suitable for small parts), automatic plating and continuous plating (suitable for wire, strip).
Domestic classification by electroplating solution can be divided into four categories:
Cyanide galvanizing
Since (CN) is highly toxic, the environmental protection has imposed strict restrictions on the use of cyanide in electrogalvanizing, and has continuously reduced the development of cyanide electro-zinc plating bath systems, requiring the use of a low cyanide (microcyanide) electroplating bath. After electroplating with this process, the product quality is good, especially color plating, and the color remains good after passivation.
Zinc plate plating
This process evolved from cyanide galvanizing.
At present, there are two major factions in the country:
a) "DPE" series of Wuhan Material Protection Institute;
b) "DE" series of Radio and Television.
Both are zincate zincate alkaline additives; PH value of 12.5 ~ 13. With this process, the lattice structure of the coating is columnar, and it has good corrosion resistance and is suitable for color galvanization.
Chloride zinc plating
This process is widely used in the electroplating industry, accounting for up to 40%. After passivation (Lanbai) can be zinc chromium (equivalent to chrome plating), especially after the addition of water-soluble varnish, it is difficult for laymen to identify whether it is galvanized or chrome-plated. This process is suitable for white passivation (blue white, silver white).
Sulfate galvanizing
This process is suitable for continuous plating (wire, strip, simple, large parts, parts). low cost.
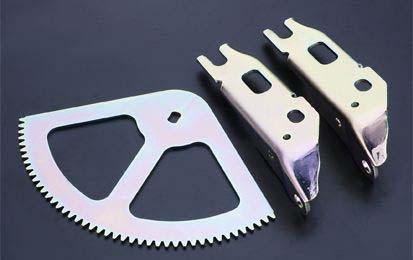
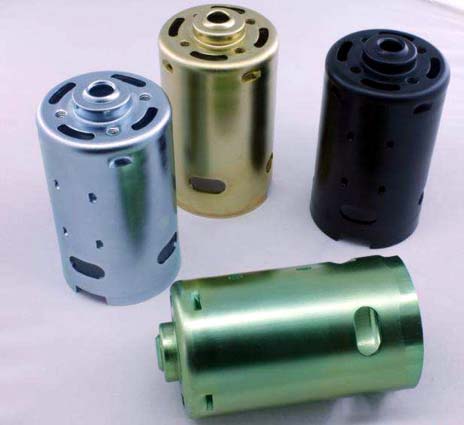
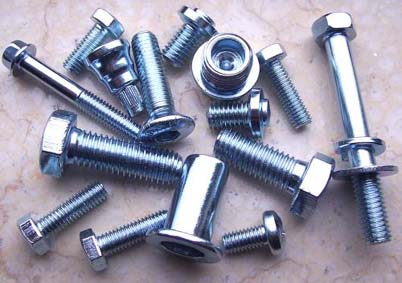
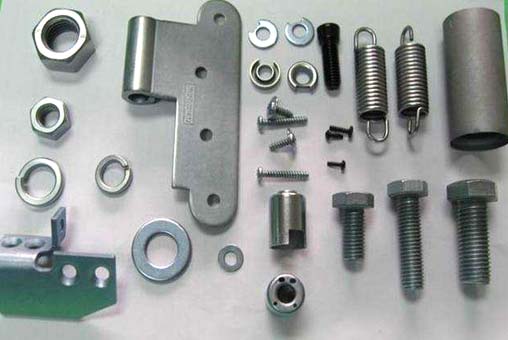
Partial plating
According to the plating area, plating can be divided into full plating and partial plating. Many parts that need to be partially plated are insulated by their non-plated surfaces. This requires the use of different partial insulation methods to meet the technical requirements of the construction to ensure that the non-plated parts of the parts will not be plated, especially parts with special requirements.
According to daily work experience, several local electroplating processes commonly used in electroplating are introduced.
Dressing method
In this method, the non-plated surface is insulated and protected by tape or plastic strips, tapes, and other materials, and the method of dressing is determined according to the shape of the part. The dressing method is suitable for simple parts, especially circular parts with regular shapes. Bandage insulation is the easiest method.
Special fixture method
Special fixture method, also known as profile fixture method. That is to say, for some parts with more complex shapes, special insulation fixtures can be designed in accordance with the shape of the parts, which can greatly improve the production efficiency. If the bearing inner or outer diameter is partially chrome-plated, a special bearing chrome-plating jig can be designed, and this jig can be used repeatedly.
Wax protection method
The characteristics of insulation with wax formulation is that it has good bonding performance with parts, wide range of use temperature, and the end edge of the insulation layer does not lift up. Therefore, it is suitable for parts with high dimensional tolerance of the insulation end and a relatively complicated shape. In addition, the wax formulation can also be reused with low loss, but its use method is more complicated and the cycle is longer. When applying a wax formulation, the parts should be preheated to 50-70°C, coated with a molten wax formulation, and coated with a thin layer to cover the entire surface to be insulated. At this time, the wax should not solidify in the middle, and then repeatedly coated to the desired thickness. After coating, the end of the insulation is trimmed with a knife after warming before cooling to room temperature, and the surface to be coated is repeatedly wiped with a cotton ball and dipping in gasoline. This operation is very careful. After plating, the wax preparation can be melted and recovered in hot water or a special wax bucket, and then the parts can be cleaned with a solvent such as gasoline or a water-soluble cleaning agent.
Coating insulation method
Paint insulation paint is often used for insulation protection during plating. This insulation protection method is easy to operate and can be applied to complex parts. Commonly used insulating coatings are vinyl chloride anti-corrosive varnish, polyvinyl chloride insulation coating, nitro glue and so on.
Bath leakage
Cause Analysis
(1) Prevent excessive heating of the plating solution. When the plating solution is heated too high, the plating solution accelerates evaporation and decomposition, and the aerosol contains a high concentration of solute components. At this time, it will seriously pollute the environment, especially the acid and alkali mists. Cyanide and chromium mist will have greater impact on the environment and human body.
(2) Strictly prevent the plating solution from being sucked away by the exhaust fan. When the exhaust fan is not properly equipped, the plating solution level is too high and the plating solution is easily sucked away. Before the slot cover is opened, it is particularly serious, causing both environmental pollution and the loss of the plating solution. When this happens, measures must be taken to solve it. If you lower the plating solution level and adjust the suction inlet width, set up a liquid trap below the outdoor exhaust fan to collect the ingested plating solution or condensate.
(3) Reducing the loss of large plating solution. If the plating solution does not pay attention in the process of large-scale processing, the amount of loss of the plating solution is quite large, and the typical loss is 2% to 3%. That is, 1000Lplating solution often needs to be supplemented with 20 to 30L of pure water, and the corresponding chemical materials, in order to restore to the original level and the original concentration, if careful to operate a little, Mechanical filtration is matched with manual filtration so that the plating solution is filtered out as much as possible from sediments at the bottom of the tank. The loss of the plating solution can be greatly reduced, thereby saving both the material loss and the pollution to the environment.
(4) Prevents contamination due to leakage from plating tanks and heating (cooling) pipes. Leakage of the electroplating tank or heating pipe often causes serious pollution, and the reason for the leakage is different depending on the manufacturing material and different plating species.
Take measures
1. Prevention methods: Near the anode groove, wall vertical block temperature resistant glass or plastic plate to partition the anode plate and the slot liner contact, reducing the chance of corrosion.
Remedy: In the iron shell groove below the liquid level drilled 3 ~ 5cm sound l ~ 1.5mm hole, when the lined lead slot is damaged, the chromium plating solution will thus shoot, Through this signal, you can know that the liner tank is damaged and can be repaired immediately, which can avoid the occurrence of a larger accident.
2. Leakage Causes and Preventive Measures of Lead Heating (Cooling) Tubes. Leakage of the lead heated (cooling) pipe is somewhat similar to leakage of the lead-lined tank, but it may also be damaged due to expansion caused by pressure. Lead pipe leakage is also very harmful to the environment. Once leakage, it is possible that the solution in the tank will be ejected out of the tank with steam or water, and the danger is greater, and it may cause damage to the boiler and a greater accident.
3. Plastic plating tank leakage causes and prevention methods. Plastic plating tank leakage is caused by poor welding quality, which does not exclude human factors.
Development
(1) DC generator stage This type of power source consumes large amounts of energy, is inefficient, and has high noise. Has been eliminated.
(2) The silicon rectification stage is a new generation of DC generators. The technology is very mature, but it is inefficient, bulky, and inconvenient to control. Many companies still use this kind of electroplating power supply.
(3) The silicon controlled rectifier stage is a mainstream power source that replaces the silicon-rectifier power supply, and is characterized by high efficiency, small size, and easy control. With the core device - the SCR technology matures and develops. The power technology has matured and it has been widely used.
(4) Transistor switching power supply, ie pulse power phase pulse electroplating power supply is the most advanced electroplating power supply. Its appearance is a revolution of electroplating power supply. This power supply has a small size, high efficiency, superior performance, stable ripple coefficient. And it is not easily influenced by the output current. Pulsed plating power is the direction of development and is now beginning to be used in enterprises.
Alloy Plating
3.1 High corrosion resistance zinc alloy plating process
Zinc alloy refers to an alloy containing zinc as a main component and containing a small amount of other metals. The binary zinc alloys that have been used for production are: Zn-Ni, Zn-Co, Zn-Fe, Sn-Zn. Zn-Ti, Zn-Cr, Zn-P, Zn-Mn, etc. Zinc alloys have good protective properties and are often referred to as high corrosion resistant alloy coatings. Among them, there are many researches, and the most widely used ones are the alloys formed by zinc and iron group metals, namely zinc-nickel, zinc-cobalt and zinc-iron. The atomic structures and properties of iron family metals are similar, and their co-deposition properties with zinc are similar. From the viewpoint of electrode potential, the iron group metal has more positive potentials than zinc, but when co-deposited, zinc is preferentially deposited and deposited preferentially than iron group metal. This kind of deposition is called anomalous co-deposition. The reason is that when zinc and iron group metals are co-deposited on the surface of the cathode, the pH of the surface increases with the precipitation of H2 on the surface of the cathode. A zinc hydroxide colloidal film is formed on the surface of the cathode, so that the iron group metal ions are inhibited on the surface of the cathode and are difficult to be deposited, so that zinc is preferentially precipitated on the surface of the cathode.
3.1.1 Electrogalvanizing - Ferroalloy process and passivation
There are two types of zinc-iron alloys that have been industrially used:
One is a high iron content alloy, the plating is not easy passivation, easy phosphating treatment, has a good bonding force on the paint, and more for the surface treatment of steel plates and strips, as the bottom layer of electrophoretic paint;
The other is a zinc-iron alloy containing trace amounts of iron.
The coating is easy to passivate and has excellent corrosion resistance. After black passivation, the corrosion resistance is greatly improved. The zinc-iron alloy process can also be divided into two types: acidic and alkaline. The iron content of the alloy coating is generally between 0.2% and 0.7%. The content of trivalent iron ions in the plating solution cannot be too high, otherwise the cathode current efficiency will be reduced and the crystals will be coarse.
The following only describes the low iron content plating process.
Jewelry Plating
Electroplating is a widely used surface optimization treatment technology in the jewelry production process, and is a method for electrochemically depositing metal and alloy plating on the surface of the jewelry. The so-called electroplating is that the metal ions in the plating solution are reduced to metal atoms through an electrode reaction under the action of an external electric field, and a metal precipitate is formed on the cathode so that a plating layer is formed on the surface of the jewelry. This effectively changed the texture, color, and texture of the jewelry to prevent alterations, and played a role in beautifying and prolonging the life of the jewelry.
According to the purpose of the use of electroplating to classify, electroplating can be divided into protective electroplating and decorative electroplating two.
Protective electroplating is mainly used to prevent metal corrosion, usually using galvanizing, rhodium plating, tin plating, and the like. It is commonly used on silver jewelry. We know that silver is very easy to oxidize and darken, which is bad for jewellery and is usually protected by electroplating. The 925 silver jewellery of Baodi Network has rhodium plating. Barium is an expensive precious metal, stable in nature, and white in color. Like platinum, it can effectively prevent 925 silver from becoming black and beautiful.
Decorative electroplating is mainly for decorative purposes, of course, there will be some protection. To beautify, most decorative electroplating is a combination of multiple layers of electroplating. It is usually on the jewellery that it is first coated with a base layer, then with the surface layer, and sometimes with an intermediate layer. This kind of electroplating is widely used in precious metal plating and artificial jewelry. This kind of electroplating jewelry, plating is often a very high-grade precious metal, Such as gold, 18k gold, colored metal, etc., and its basic material is often a hardware, or non-precious materials.
Plastic plating
The electroplating plating parts of plastics are easy to float, and are easily burned when they come in contact with the hangers. Because the specific gravity of the plastics is small, they float easily in the solution.
The shape of the lampshade is like a small plate.The inner surface is recessed and there are two small holes on the side. Only one copper wire is used to hold two small holes for plating.
Due to the release of gas during electroplating, the lampshade is easily detached from the copper wire, and the copper wire is also light enough to immerse the lampshade in the solution.
Later on the copper wire attached to heavy objects, to solve the floating problem. The contact point between the copper wire and the lampshade is scorched and the plastic is exposed, which is caused by poor conduction.
Solution: In order to solve the floating and conductive problems of the plastic plating workpiece, we designed a special fixture.The clip has a certain weight, and after the lampshade is no longer floated, two wider conductive pieces are stuck on the hole of the lampshade, so that the current is even in all places, and the contact point will not burn.