Stainless Steel Surface Treatment
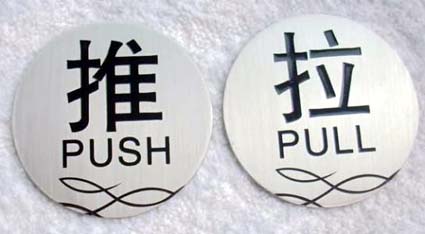
Product introduction
1.1.1 Main components of stainless steel: Generally contains high-quality metallic elements such as chromium (Cr), nickel (Ni), molybdenum (Mo), and titanium (Ti).
1.1.2 Common stainless steel: Chrome stainless steel, containing more than 12% Cr; nickel-chromium stainless steel, containing Cr ≥ 18%, with Ni ≥ 12%.
1.1.3 Classification from stainless steel metallurgical structure: Austenitic stainless steel, For example: 1Cr18Ni9Ti, 1Cr18Ni11Nb, Cr18Mn8Ni5. Martensitic stainless steel, such as: Cr17, Cr28 and so on. Commonly referred to as non-magnetic stainless steel and magnetic stainless steel.
Cause of corrosion
Chemical corrosion
2.1.1 Surface contamination: Oil, dust, acids, alkalis, and salts attached to the surface of the workpiece are converted into corrosive medium under certain conditions, chemical reactions occur with certain components in the stainless steel parts, and chemical corrosion and rust occur.
2.1.2 Surface scratches: All kinds of scratches damage the passivation film, so that the stainless steel protection ability is reduced, easy to react with chemical media, resulting in chemical corrosion and rust.
2.1.3 Cleaning: After pickling and passivation, the cleaning is not clean and the residual liquid remains, which directly corrodes stainless steel parts (chemical corrosion).
Electrochemical corrosion
2.2.1 Carbon Steel Pollution:
The scratched and corrosive medium caused by the contact with the carbon steel element forms a primary battery and generates electrochemical corrosion.
2.2.2 Cutting:
Cutting slag, spatter adhesion to the rust and other corrosive media material forming primary electrochemical cell and corrosion.
2.2.3 Roasting school:
The components of the flame heating zone and the metallurgical structure change unevenly, forming galvanic cells with the corrosive medium and causing electrochemical corrosion.
2.2.4 Welding:
Physical defects in the welding area (undercuts, pores, cracks, non-welding, incomplete penetration, etc.) and chemical defects (greater grain, chromium-depleted grain boundary, segregation, etc.) and the corrosive medium form primary cells. Generate electrochemical corrosion.
2.2.5 Material: Stainless steel chemical defects (inhomogeneous composition, S, P impurities, etc.) and surface physical defects (loose, trachoma, cracks, etc.) are conducive to the formation of primary batteries with corrosion medium and electrochemical corrosion.
2.2.6 Passivation: The poor pickling passivation results in non-uniform or thin passivation film on the surface of stainless steel, which is easy to form electrochemical corrosion.
2.2.7 Cleaning: Residual acid pickling and passivation residues and stainless steel chemical corrosion products and stainless steel parts form electrochemical corrosion.
Stress corrosion
In short, because of its special metallographic structure and surface passivation film, stainless steel makes it difficult to corrode with chemical reaction with the medium under normal circumstances, but it cannot be corroded under any conditions.
In the presence of corrosive media and causes (such as scratches, splashes, slags, etc.), stainless steel can also corrode with slow chemical and electrochemical reactions with corrosive media. Moreover, under certain conditions, the corrosion rate is quite rapid and causes corrosion, especially pitting and crevice corrosion. The corrosion mechanism of stainless steel parts is mainly electrochemical corrosion.
Preventive measures
Storage and lifting

4.1.1 Storage of stainless steel parts: There should be a special storage rack, which should be a carbon steel bracket or pad with a wood or painted surface to isolate it from other metal materials such as carbon steel. When storing, the storage location should be easy to lift, isolated from other material storage areas, and there should be protective measures to avoid contamination of stainless steel by dust, oil, and rust.4.1.2 Hoisting of stainless steel parts: When hoisting, special spreaders, such as lifting belts, special chucks, etc., shall be used. It is forbidden to use wire ropes to avoid scratching the surface; and when lifting and placing, collisions should be avoided to cause scratches.
4.1.3 Stainless Steel Parts Transport: When transporting, use transportation tools (such as trolleys, car batteries, etc.), and be clean and have isolation and protection measures to prevent dust, oil, and rust from contaminating the stainless steel. Do not drag, avoid bumps, scratches.
Processing
4.2.1 processing area: The machining area of stainless steel parts should be relatively fixed. The platform of the stainless steel processing area should take isolation measures, such as laying rubber pads. The setting management and civilized production of stainless steel processing areas should be strengthened to avoid damage and contamination of stainless steel parts.
4.2.2 Blanking: The blanking of stainless steel parts uses shear or plasma cutting, sawing, etc.
(1) Cut: When cutting, it should be isolated from the feeding bracket, and the falling hopper should be covered with a rubber pad to avoid scratching.
(2) Plasma cutting: After plasma cutting, the cuttings should be cleaned. When batch cutting, the field should be cleared in time for the completed parts to avoid the slag slag on the workpiece.
(3) Sawing blanking: When sawing the material, the clamp should be protected by rubber. After sawing, the oil and residue on the workpiece should be cleaned.
4.2.3 Mechanical processing: Stainless steel parts should also be guarded during turning, milling and other machining operations. After the operation is completed, clean the surface of the workpiece, such as oil, iron and other debris.
4.2.4 Molding processing: During plate rolling and bending, effective measures should be taken to avoid scratches and creases on the surface of the stainless steel parts.
4.2.5 Rivet welding: In the assembly of stainless steel parts, forced assembly should be avoided, in particular, flame baking and assembly should be avoided. If there is temporary plasma cutting during the process of pairing or production, isolation measures shall be taken to avoid contamination of other stainless steel parts by slag cutting. After cutting, the slag on the workpiece should be cleaned.
4.2.6 Welding: Stainless steel parts must be carefully cleaned of oil, rust, dust and other debris before welding. When welding, try to use argon arc welding. When using manual arc welding, use small current and fast welding to avoid swing. It is forbidden to start the arc in the non-welding area. The grounding position is appropriate and the connection is firm to avoid arcing scratches. Anti-splash measures should be taken when welding (such as brush white ash and other methods). After welding, stainless steel (not carbon steel) flat spades are used to thoroughly clean the slag and splash.
4.2.7 Multilayer welding: In multilayer welding, the inter-layer slag must be removed. When multi-layer welding, the temperature between layers should be controlled, and generally should not exceed 60 °C.
4.2.8 Welds: Weld joints shall be ground. The surface of the weld shall have no defects such as slag, air holes, undercuts, splashes, cracks, incomplete fusion, incomplete penetration, etc. The welds and parent metal shall be smoothly transitioned and shall not be lower than the base metal.
4.2.9 Orthopedic: In the orthopedics of stainless steel parts, flame heating methods should be avoided, in particular, repeated heating of the same area is not allowed. When correcting, use mechanical devices as far as possible, or hammer them with wooden hammers (rubber hammers) or pad rubber pads, and do not hammer them with hammers to avoid damage to the stainless steel parts.
Surface treatment
4.3.1 Clean and polish: If the damage should be polished, scratches and splashes caused by contact with carbon steel parts in particular, damage caused by cutting slag must be thoroughly cleaned and polished.
4.3.2 Mechanical polishing: The use of a suitable polishing tool for polishing requires uniform handling and avoids over-disposal and re-scratching.
4.3.3 Degreasing and dust removal: Before the stainless steel parts are pickled and passivated, impurities such as oil, oxide scale, and dust must be removed according to the process.
4.3.4 Water spray treatment: According to different processing requirements, choose different micro glass beads, different process parameters, and avoid overspray.
4.3.5 Pickling passivation: The pickling passivation of stainless steel parts must be passivated strictly in accordance with the process requirements.
4.3.6 Cleaning and Drying: After pickling and passivation, it should be strictly processed and neutralized, rinsed, and dried to completely remove the residual acid.
4.3.7 Protection: After the surface treatment of stainless steel parts is completed, protection shall be taken to prevent secondary pollution of personnel touching, oil, dust and other impurities.
4.3.8 Avoid reprocessing: After the surface treatment of stainless steel parts is completed, rework of the parts or products should be avoided.
Including: surface treatment of stainless steel/low-carbon steel products such as chemical vessels, storage tanks, and pipeline boilers, such as grinding/polishing, pickling/passivation, inspection/supervision, and technical consultation.
The main service targets are ships, petrochemicals and food equipment.
Existing problems
5.1 Weld Defects: Weld defects more serious, by hand to make a mechanical polishing treatment, The resulting grinding marks cause uneven surfaces and affect the appearance.
5.2 Inconsistent surface: Only pickling and passivation of the welds can also cause surface irregularities and affect the appearance.
5.3 scratches difficult to remove: The whole pickling passivation can not remove all the scratches produced during processing. In addition, it is not possible to remove carbon steel, spatter, and other impurities that adhere to the surface of stainless steel due to scratches and welding spatter. Cause chemical corrosion and rust or galvanic corrosion occurs in the presence of corrosive medium.
5.4 Polishing passivation uneven: After the hand-polishing process, pickling and passivation treatment is performed. For a workpiece with a large area, it is difficult to achieve a uniform and uniform treatment effect, and an ideal uniform surface cannot be obtained. And working hours, accessories costs are also high.
5.5 Pickling capacity is limited: Pickling passivation paste is not a panacea. It is harder to remove for plasma cutting and flame cutting.
5.6 The scratch caused by human factors is more serious: In the process of lifting, transportation and structural processing, scratches, dragging, hammering and other human factors cause serious scratches, which makes the surface treatment more difficult, and it is also the main cause of corrosion after processing.
5.7 Equipment Factors: In the course of bending, bending and bending of profiles, plates, scratches and creases are also the main causes of corrosion after processing.
5.8 Other factors: During the procurement and storage of stainless steel raw materials, bumps and scratches due to lifting and transportation are also serious and one of the causes of corrosion.
Basic processing
Commonly used stainless steel surface treatment technology has the following treatment methods:
1. Surface whitening treatment;
2. Surface mirror light treatment;
3. Surface coloring.
1.2.1 Surface whitening treatment:
During the processing of stainless steel, black oxide scales are produced after coiling, tying, welding or artificial surface heat baking and heating. This hard gray-black scale is mainly composed of NiCr2O4 and NiF EO4. Hydrofluoric acid and nitric acid are usually used to remove strong corrosion. However, this method is costly, pollutes the environment, is harmful to the human body, and is highly corrosive and is gradually being eliminated.
There are two main methods for treating oxide scales:
(1) Sand blasting (pill) method: The method of spraying micro glass beads is mainly used to remove the black oxide scale on the surface.
(2) Chemical method: A non pollution pickling and passivation paste and a cleaning solution with inorganic additives at normal temperature were used for washing. In order to achieve the purpose of the white color of stainless steel. After processing it basically looks like a matt color. This method is more suitable for large and complex products.
1.2.2 Light treatment of stainless steel surface mirror : According to the complexity of stainless steel products and different requirements of users can be used mechanical polishing, chemical polishing, electrochemical polishing and other methods to achieve the specular gloss.
1.2.3 Surface coloring: Stainless steel coloring not only imparts various colors to stainless steel products, but also increases the variety of colors of products, and improves the wear resistance and corrosion resistance of products.
Stainless steel coloring methods are as follows:
(1) chemical oxidation coloring;
(2) electrochemical oxidation coloring method;
(3) ion deposition oxide coloring method;
(4) High-temperature oxidation coloring method;
(5) Gas phase cracking coloring method.
The various methods are as follows:
1) Chemical oxidation coloring: In a particular solution, the color of the film formed by chemical oxidation includes the dichromate method, the mixed sodium salt method, the sulfurization method, the acid oxidation method, and the alkaline oxidation method. In general, INCO is used more often, but in order to ensure that the color of a batch of products is consistent, reference electrodes must be used for control.
(2) Electrochemical staining: It is the color of the film formed by electrochemical oxidation in a specific solution.
(3) Ion deposition oxide coloring chemical method: The stainless steel workpiece is placed in a vacuum coating machine for vacuum evaporation plating. For example: titanium-plated watch cases, watch bands, are generally golden yellow. This method is suitable for processing large quantities of products. Because of the large investment and high cost, small-volume products are uneconomical.
(4) High temperature oxidation coloring method: In a specific molten salt, the immersed workpiece is maintained at a certain process parameter, so that the workpiece is formed with a certain thickness of an oxide film, and exhibits a variety of different colors.
(5) Gas phase pyrolysis coloring method: It is more complicated and less applied in industry.